Abstract
The research on improving production efficiency and reducing labor cost by reducing production CWS is the focus of notebook computer manufacturing enterprises. This research breaks the traditional method of reducing CWS at the production end and chooses to find breakthroughs from the whole life cycle of products. Finally, innovatively based on product lean design, and from the product design side, explore the optimization opportunity to reduce the CWS value of product production, so as to achieve the purpose of reducing CWS. Firstly, laptop model S is selected as the research object, and its structure disassembly and analysis, assembly action research and station sequencing were carried out to preliminarily determine the product production process. According to the production bottleneck process time, the current CT of the production line was determined to be 13S, and the initial CWS value of the production line was calculated to be 0.2167. Then, based on the principles of lean product design, the CONN of FAN, Battery, Speaker and RCT are optimized to make their assembly easier. The SSD fixation method, I/O BKT and I/O modular design are optimized to eliminate the need for auxiliary BKT assembly. In addition, Center Hook and WLAN were integrated on MB, and their assembly was cancelled, so that the design of the optimized parts was more integrated and modular. Then, the optimized product was rearranged for production. The CWS value of the optimized product was 0.1589, which decreased by 27 % compared with that before optimization.
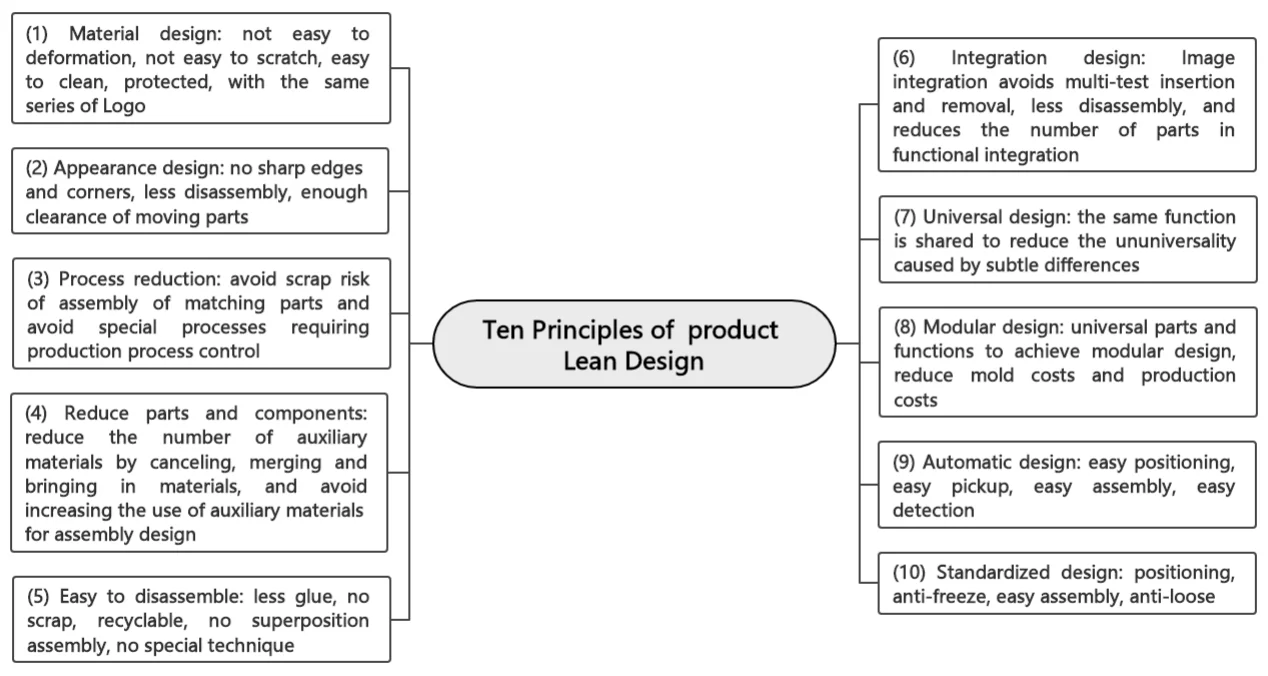
Highlights
- Ten Principles of Product Lean design
- Improve production efficiency and reduce labor costs
- Laptop parts integration and modular design
1. Introduction
Since its establishment in 2012, L company has been focusing on notebook computers as its main production business. In the early stage of COVID-19, home office and study stimulated the growth of demand for notebook computers. Faced with the surging demand for orders, L Company also exposed the extensive and defects of production control and management while pursuing UPH. In the post-epidemic period, lean production with CWS (current work standard) reduction as the breakthrough point has become the main theme of current production control. With the research and application of lean production by more and more experts, scholars and well-known enterprises, its theory and method have been gradually improved [2]-[4]. Xiao Qianqiao et al. considered the dynamic effect of employee learning curve on the production process, studied the dynamic change relationship between man-machine resources and employee learning ability, and obtained an effective dual resource allocation method for manufacturing system based on lean indicators [5]. Wang Yanjun pointed out that the production and management links of enterprises should be standardized, including the work sequence, technical specifications and safety production, there should be corresponding standards. Standardized operation and lean production complement each other. The former is the basis, while the latter can also promote the continuous improvement of the former [6]. Irina analyzed the role of employees in the implementation of lean production in six Russian enterprises, and pointed out that enterprises should consider human factors in the process of implementing lean production, starting from changing the attitude of employees, so that enterprises can obtain more benefits from the implementation of lean production [7]. As the theory and method of lean production become more and more perfect, lean optimization has gradually changed from focusing only on the production site to employee quality cultivation, standardized operation, human resource management and many other aspects. The re-optimization of product production from the production side becomes more and more limited, and the space for optimization becomes smaller and smaller. Therefore, exploring new optimizable directions has become the current difficulty and focus of L Company.
2. CWS value of industrial production and optimization method to reduce CWS
In the production of laptop computers, CWS value, as an important parameter to evaluate industrial production efficiency and production cost, has a high reference value in cost budget evaluation. The establishment of CWS model is to balance and control the production efficiency and production labor cost. For the assembly and production of a certain laptop, the number of assembly actions required is determined, so the total assembly time is also determined. In order to arrange the production on the assembly line with high efficiency and low cost, it is necessary to balance and set the running speed of the conveyor belt and the number of workers in the production line, that is, the balance and setting of CT (operation cycle time of a single process) and HC. The smaller CT is, the faster the assembly line speed is and the higher the production efficiency is. However, there are few actions that can be completed in a single process, which requires more manpower to complete, that is, HC needs to be increased, in other words, the labor cost needs to be increased. Therefore, the production efficiency is positively correlated with the production labor cost. Therefore, we only need to comprehensively optimize and reduce CWS to comprehensively control production efficiency and production labor cost. The core goal of CWS optimization is how to reduce costs, ensure product quality in the production process, and improve the production efficiency of the system, so as to obtain a variety of benefits. It can be seen from Formula (1) that CWS value is related to CT and HC. In actual production, IE engineers mainly rely on ECRS principle and 5W1H technology to reduce CWS. By eliminating, merging, rearranging and simplifying process stations, HC and CWS can be reduced [8]-[11]. Zhao Chaowen [12] used ECRS to merge, rearrange, simplify and eliminate processes. He also analyzed the gating workstation of toy car assembly line to reduce unnecessary actions, which improved UPH and indirectly reduced CWS value. Wang Xia [13] and others in the production system and process analysis of DS company, using the method of model row when on work hours for approval, at the same time, using the method of action rearrangement optimization, process to improve the production mode, make CT is reduced by 4.04 seconds, line balance up to 92.30 %, ultimately achieve the goal of reducing island operation, improve productivity:
Among them, CWS is the current work standard; CT is the cycle time of conveyor belt running in each process of production line; HC is the number of manual workers in the production process.
The core of CWS optimization mentioned above focuses on the production side, which is also the method commonly used by IE engineers to reduce CWS value at present. In fact, at the product design stage, the structure and assembly of parts, and the selection and placement of connectors all have a certain impact on production operations, but few people optimize CWS from the upstream product design side:
Among them, LB is the balance rate of the production line [14]; PT is the actual total manual operation time of each process of the product; HC is the number of manual workers in the production process; CT is the cycle time of conveyor belt running in each process of production line; CTi is the actual manual operation time of each process.
It can be deduced from Eqs. (1) and (2):
According to Eq. (3), the influencing factors of CWS are not only related to CT and HC at the production end, but also related to product PT. In other words, the improvement of production efficiency and the reduction of production cost can not only look for improvement points from production management, but also related to the actual total production time of the product itself, that is, the optimization and improvement of the product itself is also very important. Therefore, the lean optimization from the product design side provides a new way to reduce the CWS value.
3. Optimized the design of notebook computer parts based on lean design
3.1. Connotation and criterion of product lean design
“Lean” means less and better, and all design elements are beneficial, efficient, and economical. Lean means to achieve higher efficiency with less resource consumption, and also to eliminate unnecessary waste [15]-[17].
Fig. 1Ten principles of lean product design
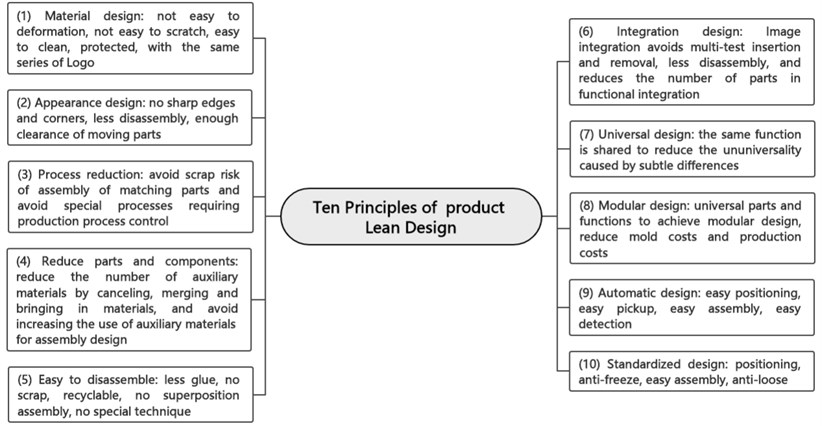
Product lean design adheres to the core idea of Lean, emphasizes the elimination of unnecessary waste from the product design stage, improves the ease of manufacturing, and tries to better meet the production demand with fewer parts, lower material cost and lower manufacturing complexity. The key difference between lean design and traditional design lies in the fact that there is little waste in manufacturing under lean design concept [18]-[20]. Therefore, the connotation of product lean design mainly includes:
1) To eliminate waste as the starting point. Lean design emphasizes eliminating waste from the source of product design, striving for perfection in every link of design, effectively controlling cost and achieving higher utility with lower cost.
2) To make the overall optimal product as the end point. Lean design not only emphasizes the elimination of waste and cost reduction, but also tries to achieve the overall optimization of the whole product through reasonable design, which is a multi-objective balanced optimization idea.
3) Take continuous improvement as the guide. The product lean design scheme is not invariable, but takes future changes as an important factor in the preliminary design stage, selects materials reasonably, optimizes layout, and finally achieves the overall optimization of the product.
In line with the concept of lean design, strive to make the product design to achieve the overall optimal, therefore, summed up ten principles of product lean design is shown in Fig. 1.
3.2. Structure analysis of notebook computer
Laptop computer in the structure can be divided into Upper module and Lower module, which, the Upper module is mainly composed of A Cover, Camera, Bezel, Hinge, Hinge cap, LCD. The Lower module consists of C Cover, Keyboard (KB), Keyboard bracket (KB BKT), SPK, THM, FAN, I/O Board, MB, WLAN, SSD, FP, TP, Battery, and D Cover. In this paper, model S is selected as the research object to disassemble and analyze all parts of the machine. Fig. 2 shows the structural explosion diagram of model S.
From the structure disassembly, it can be seen that there are a large number of parts in the notebook computer, and the parts and MB are connected by wire harnesses, which will lead to a long time of wire trimming action for manual assembly. Moreover, the complex wiring harnesses arrangement and assembly and connector connection make it difficult to automate the parts assembly. Therefore, from the perspective of lean product design, hope that through design optimization to achieve the purpose of the components of modularization, integration and automation, as much as possible to reduce the number of parts, reduce parts of complex wire connection. Thus, the internal structure of the product tends to be simple, the assembly action tends to be simple, and ultimately improve the manufacturability of the product.
Fig. 2Structural explosion diagram of model S
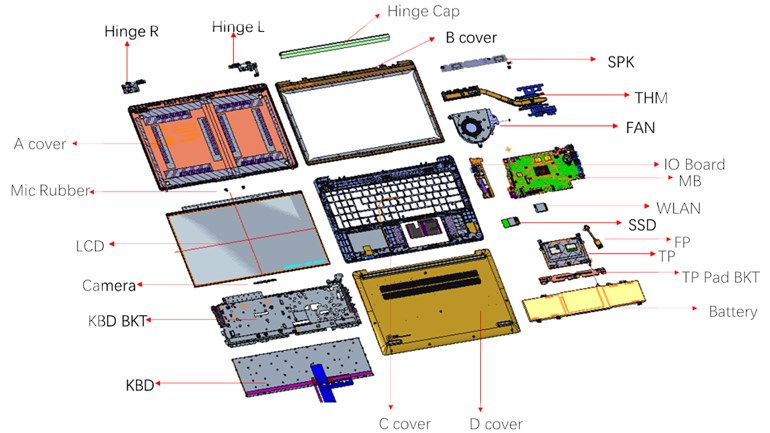
3.3. Parts design optimization based on product lean design
Based on the ten principles of lean design and product PT reduction, the design optimization of product components was carried out, as shown in Table 1, which shows the comparison and assembly impact of each component before and after optimization. Through lean design optimization, the wiring harnesses of FAN, Battery, SPK and RTC are omitted, so as to cancel wiring harnesses finishing and assembly. WLAN and Center Hook are integrated into MB to cancel their additional assembly actions. In addition, the I/O interface and BKT are designed to be integrated by optimization, so that two separate parts are optimized into one part. In this optimization, the design of SSD screw column and metal NUT are added to the corresponding positions, thus eliminating the assembly process of SSD BKT and making SSD meet the automatic assembly conditions of the existing SSD card insertion machine.
Table 1Parts optimization comparison and optimization benefits
Parts | Current design | Lean design | Improvements and Benefits |
FAN | ![]() | ![]() | 1. Design FAN and THM into one body to realize modular one-action assembly 2. Optimize the FAN wire harness and CONN to spring CONN without cable trimming and connector insertion |
Battery | ![]() | ![]() | 1. Optimize the Battery harness and CONN to a knife-type CONN, eliminating the wire trimming and CONN insertion actions 2. The optimized structure is simple, no complex line, and meets the conditions of automatic assembly |
Speaker | ![]() | ![]() | Two SPK-one CONN are optimized to two SPK-two CONN, and the long complex cable in the middle is omitted |
RTC | ![]() | ![]() | The traditional RTC is optimized into button RTC, eliminating the wiring and CONN insertion action, realizing one-action assembly and meeting the requirements of automatic assembly |
SSD | ![]() | ![]() ![]() | A screw column and a metal NUT are added to the C cover at the end of the short SSD so that the short SSD does not share the same screw column with the long SSD, thus canceling the short SSD BKT |
WLAN | ![]() | ![]() | Optimize the traditional WLAN card to the on board format and cancel the original WLAN assembly action |
I/O BKT | ![]() | ![]() | Optimize the design of I/O BKT, which is designed to be integrated with I/O interface, so as to cancel the assembly action of the original BKT |
Center Hook | ![]() | ![]() | The traditional Center hook is optimized into the form of on board and welded to MB, saving the original Center hook assembly and fixing screw action |
4. Optimization reduction of CWS value in notebook computer production
4.1. Production process and CWS value evaluation of model S
According to the actual layout of the current production line, the existing design and parts assembly production of model S are analyzed, and the assembly process of each part is arranged for production. The Table A1 shows the parts assembly process of model S and the corresponding CWS value of each process. Among them, the first 10 stations Kitting is the feeding section of the production line, and ASSY is the assembly section of the production line. The whole production process has 64 stations, and a total of 64 workers are required for pure manual operation. As can be seen from the table A1, the bottleneck station is KB&BKT hot melt fixation, and the production process time is 11.82 s. Considering that the release rate of the actual production is 10 %, the actual production time of the bottleneck station is 13s, so the CT of the production line is 13 s. Combined with equations 1-2, it can be calculated that the production CWS is 0.2167.
4.2. CWS value evaluation after lean design optimization of model S
As can be seen from the above analysis, the assembly and production of a production line of laptop computers requires 64 people. Under the increasingly high labor cost, pure manual work will face huge recruitment pressure, especially in the epidemic environment, manual work will make the actual production situation more uncontrollable. Therefore, it is important to reduce production PT and thus production line HC based on lean product design. After the integration, modularization and automatic optimization of the component design, the number of production and assembly actions of the product is reduced compared with that before the optimization, and the automatic assembly of some components is realized, and the final PT is reduced. It can be seen from the attached table that a total of 44 HC are required for the production process after product optimization, and the CWS after optimization is 0.1589.
5. Conclusions
In this paper, model S is selected as the research object. After its production CWS drops to 0.2167, it will be limited if the traditional ECRS method is used to optimize it, and it will become very difficult to reduce CWS. Therefore, this research innovatively seeks breakthroughs from the perspective of product design optimization, summarizes the methodology of product lean design, namely the ten principles of lean design, and based on this principle components of S model is optimized, the design of components is more integrated and modular, so that the parts assembly movement is simplified, and can improve degree of automation. After optimization, the HC decreased by 20, and the CWS decreased from 0.2167 to 0.1589, optimizing decreased by 27 %. To some extent, the recruitment pressure of the factory has been alleviated, and the production cost has been reduced. This research from the aspects of the lean product design to production and manufacturing of CWS optimization made contributions, let the manufacture and design are no longer two independent unit, The higher manufacturability and lower complexity of the designed product, the more helpful it is to the production cost and production efficiency of the manufacturing unit. In turn, the production experience and operation techniques of the manufacturing can guide the optimization of product design. Therefore, the establishment of design and manufacturing collaboration will become very important. The successful reduces the production of CWS are optimized by the lean product design value for the future design and manufacture of the collaborative optimization laid a good foundation, the future will continue to be from the perspective of the lean product design, to build a complete evaluation system of the lean, So as to guide the direction of product design, make the designed products more manufacturable, make the production of products with higher efficiency and lower cost, and finally make the product more competitive in the market. In addition, the lean of the parts were optimized design, make the production assembly human reduces 20 people, It lays a foundation for building a less humanized and automated factory in the future. After all, whether a product has automatic assembly is related to the level of automation on the one hand, and is closely related to the assembly complexity of the product itself and whether it has automatic conditions on the other hand. In the future, it will continue to dig deeply from the perspective of DFA (design for automation), so that product production will gradually move from traditional manual assembly to less or even unmanned assembly, so as to make the production capacity of the factory more competitive in the market.
References
-
James P. Womack and Daniel T. Jones., Lean Thinking. (in Chinese), Beijing: China Machine Press, 2011.
-
Y. Jiang, “Construction and application of lean production factor system – taking a company as an example,” (in Chinese), China University of Mining and Technology, Jiangsu, 2019.
-
H. Qu, “Research on lean production in workshop of a military enterprise based on MES,” (in Chinese), Shipping Materials and Markets, Vol. 11, No. 3, 2020, https://doi.org/10.19727/j.cnki.cbwzysc.2020.11.034
-
Y. Wang, “Analysis of cost management strategy under lean production mode of production enterprises,” (in Chinese), Chief Financial Officer, Vol. 17, No. 17, 2021, https://doi.org/10.12317/j.issn.1673-3169.2021.17.1269
-
Q. Xiao et al., “Dual resource allocation method for lean manufacturing system considering learning curve,” (in Chinese), Computer Integrated Manufacturing Systems, Vol. 12, pp. 2800–2808, 2016, https://doi.org/10.13196/j.cims.2016.12.008
-
Y. J. Wang, “Application and analysis of operation standardization in Lean production management of enterprises,” (in Chinese), Management and Technology of Small and Medium Enterprises, Vol. 23, pp. 46–47, 2017, https://doi.org/10.3969/j.issn.1673-1069.2017.23.023
-
S. Irina, F. Oleg, and Y. Alla, “Improving enterprise production management system on the basis of lean production,” International Journal of Economics, Finance and Management Sciences, Vol. 7, No. 6, p. 210, 2019, https://doi.org/10.11648/j.ijefm.20190706.15
-
C. Yang, “Research on improving production efficiency of MP products in S company,” (in Chinese), South China University of Technology, 2015.
-
Chen Liang, “Research on balance improvement of a product surface production line based on IE Theory,” (in Chinese), Xihua University, 2017.
-
Boszentana, “Research on lean design theory and method for spatial organization of discrete manufacturing system,” (in Chinese), Tianjin University, 2017.
-
G. Cao, “Research on efficiency improvement of notebook computer production line of A company,” (in Chinese), Jilin University, 2018.
-
C. Zhao, “Research on assembly line design and UPH promotion of type ⅱ toy car based on LOB Technology,” (in Chinese), Software, Vol. 40, No. 5, 2019, https://doi.org/10.3969/j.issn.1003-6970.2019.05.047
-
X. Wang, W. Huang, and R. Li, “Improvement of MT workshop assembly line based on IE,” (in Chinese), in Machine Design and Manufacturing Engineering, Vol. 48, No. 12, 2019, https://doi.org/10.3969/j.issn.2095-509x.2019.12.020
-
A. Jin, “Lean automation production improvement based on production line balance,” (in Chinese), Science and Technology Wind, Vol. 14, 2018, https://doi.org/10.19392/j.cnki.1671-7341.201814139
-
J. Sun, “The definition of total lean management concept,” (in Chinese), Industrial Engineering and Management, Vol. 14, No. 2, 2009, https://doi.org/10.19495/j.cnki.1007-5429.2009.02.026
-
C. Ji and H. Wang, “Research on lean production process of multi-variety small batch electronic product unit,” (in Chinese), Electronic World, Vol. 1, 2020, https://doi.org/10.19353/j.cnki.dzsj.2020.01.003
-
Q. Liu, “Research on manufacturing enterprise management innovation model based on lean production,” (in Chinese), Enterprise Reform and Management, Vol. 8, 2020, https://doi.org/10.13768/j.cnki.cn11-3793/f.2020.0738
-
L. Wang, “Lean field management improvement and product lean R&D design,” (in Chinese), Standards Press of China, China Quality Inspection Press, 2012.
-
Y. Fang, “Research on product design and manufacturing process optimization of Y company based on lean thinking,” (in Chinese), China University of Mining and Technology, 2019.
-
L. Fang, “Research on product development process optimization of B company based on lean thinking,” (in Chinese), East China University of Science and Technology, 2016.
About this article
The authors have not disclosed any funding.
The datasets generated during and/or analyzed during the current study are available from the corresponding author on reasonable request.
Qu Songtao main contribution is conceptualization, supervision and project administration. Dai Qilong main contribution is conceptualization, supervision and project administration. Zhou Qing main contribution is data curation and writing – original draft preparation. Yang Zhifeng main contribution is project administration and resources. Xu Xiangdong main contribution is investigation. Chen Yangyang main contribution is investigation.
The authors declare that they have no conflict of interest.