Abstract
In order to greatly improve the length of shaped charge jet and optimize the jet forming performance, the forming process of a tandem shaped charge structure with reverse detonation mode was numerically simulated. The effects of the rear and front stage liner thickness on the jet length, jet head velocity, jet kinetic energy and energy conversion rate were analyzed respectively using LS-DYNA finite element analysis software. Then the optimal thickness of the front and rear stage liner of the tandem shaped charge structure was optimized, and the jet length was measured. Under the condition of charge diameter of 200 mm, when the liner thickness was 0.02CD (charge diameter) for K-charge and liner thickness was 0.25CD for the front stage warhead, the jet forming was stable and the length is the longest. After the two-stage warhead was detonated in reverse order (the initiation delay time was 220 μs), a tandem jet can be formed, and the effective jet length (excluding the pestle body) is 65 % higher than that of the later stage charge.
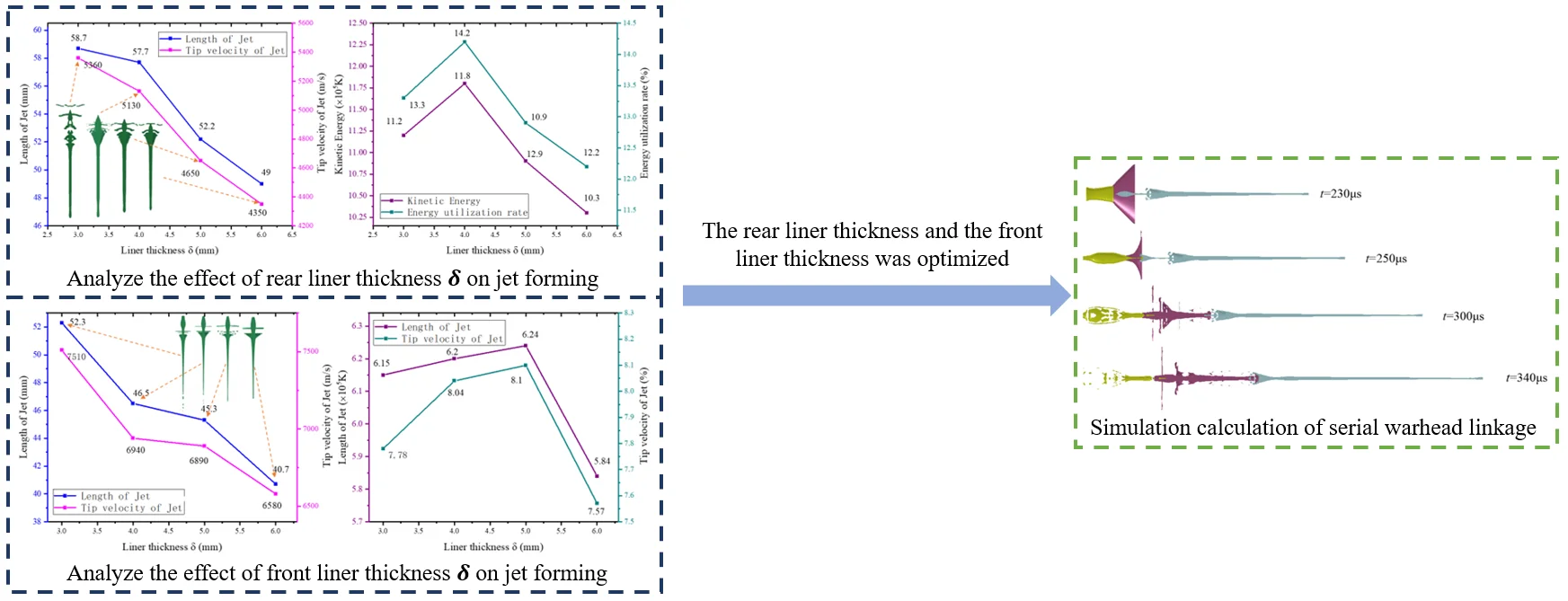
Highlights
- The forming process of a tandem shaped charge structure with reverse detonation mode was numerically simulated.
- The effects of the rear and front stage liner thickness on the jet length, jet head velocity, jet kinetic energy and energy conversion rate were analyzed respectively.
- The optimal thickness of the front and rear stage liner of the tandem shaped charge structure was optimized.
1. Introduction
The effective length of shaped charge jet is the key factor to determine the penetration ability of jet. Adjusting the structure of shaped charge warhead to improve the effective length of jet is a feasible method to enhance the penetration ability. Due to the structural limitation of the single-stage shaped charge warhead, the optimal jet length is restricted by the diameter of the warhead. The tandem shaped charge warhead can significantly improve the jet length without increasing the diameter of the liner by means of sequential connection of jets, which has become an effective way to increase the jet length.
Tandem shaped charge technology is a hot research direction at present. C Chen et al. analyzed the variation law of the tip velocity drop of post JPC under the optimal delayed initiation time [1]. Malygin et al. analyzed the action sequence of the tandem shaped charge warhead detonated in reverse order in the penetration process, and studied the jet forming process by using X-ray technology [2]. Chen Chuang analyzed the influence of the structural parameters of the liner on the velocity difference between the head and tail, and optimized the structure of K-charge [3]. N. D. Gerami et al. studied the jet forming and penetration process of different metal liner [4]. At present, the research on the forming mechanism and process of tandem jet has been more in-depth, but the correlation analysis between liner thickness and jet length and energy needs to be further studied.
This paper aimed at a tandem shaped charge structure in reverse order initiation mode, which can greatly improve the jet length without increasing the caliber of the warhead. The metal jet forming process of tandem shaped charge was numerically calculated by LS-DYNA finite element analysis software. The thickness of the liner plays an important role in the forming process of the jet. Therefore, this paper mainly analyzed the influence of the thickness of the front and rear liner on the jet performance, then optimized the structure according to the simulation results, and finally carried out the linkage simulation calculation of the tandem warhead, so as to verify that the optimized structure was feasible and effective in improving the jet length and jet performance.
2. Structural scheme of tandem shaped charge warhead
The structural scheme of the tandem shaped charge warhead in this paper is shown in Fig. 1. The rear stage warhead adopted the K-charge structure. The diaphragm material of this structure can improve the detonation wave waveform and maintain the same power level as the conventional shaped charge of the same caliber while reducing the size and quality of the warhead [5]. The front stage warhead was composed of a conical shaped charge cover with a hole in the center, a liner, explosives and flame-proof devices. The rear stage charge detonated first, and the formed jet would pass through the central liner hole of the former stage charge. After appropriate delay, the former stage charge detonated, and the front stage jet would catch up with the rear stage jet, so as to form a tandem long jet connected in space.
Fig. 1Tandem shaped charge warhead structure
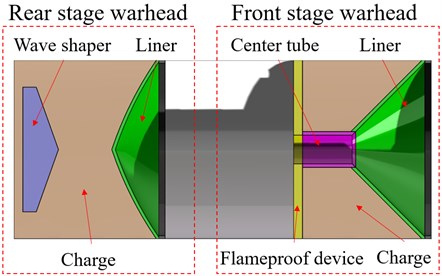
The caliber of the warhead was 200 mm, the rear warhead was detonated at the top center point, and the front warhead was detonated by 8 points. The specific parameters of the rear warhead, the front warhead and the linkage simulation calculation of the tandem warhead were as follows. For the standard rear warhead: the height of the charge H= 53 mm, the diameter of the charge was the same as the liner diameter, the charge length was L= 160 mm, radius of curvature of liner R= 400 mm, liner thickness δ= 4 mm; For standard front stage warhead: cone angle of shaped charge cover α= 45 °, liner height H= 53 mm, liner thickness δ= 5 mm. The wall thickness of the central liner was 2 mm, the ratio of liner channel to charge diameter was 0.1, and the charge length L= 160 mm; Linkage simulation model of tandem warhead: the thickness δ of the rear and front liner was the simulation optimization value, and other geometric parameters were consistent with the benchmark models of the front and rear warheads. According to the debugging and verification of the simulation calculation results, the setting of explosion-proof spacing and initiation delay time of the front and rear warheads of the linkage structure were finally determined.
3. Calculation model and material model
3.1. Calculation model
The separate simulation of the rear or front stage warhead and the linkage simulation of the tandem warhead was established by 1/4 model considering symmetry. The explosive, liner and air were Euler algorithm and Solid164 eight node hexahedron element. Outflow boundary constraints were set around the air domain, and symmetrical boundary constraints were set at the two symmetrical planes.
Fig. 2Discrete model of numerical calculation
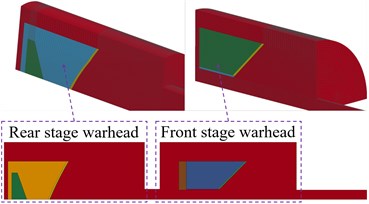
3.2. Material model
8701 explosive was used for the two-stage charge of the warhead, which was used MAT_HIGH_EXPLOSIVE_BURN burn high explosive combustion model and JWL equation of state, see in reference [7] for specific parameters. The front and rear stage liner and center tube was made of copper, which was described by Johnson-Cook model see in reference [8] for specific parameters. The wave shaper of the rear warhead and the flameproof device of the front warhead used phenolic resin and described by MAT_PLASTIC_KINEMATIC material model, see in reference [8] for specific parameters. The air was simulated using NULL material model.
4. Simulation calculation of jet forming
4.1. The effect of rear liner thickness δ on jet forming
The curvature radius of the rear stage liner was set to 400 mm, and the other geometric parameters and initiation mode were consistent with the standard model of the rear stage warhead. The charge structures with the thickness of the liner of 3 mm, 4 mm, 5 mm and 6 mm were numerically simulated.
As shown in Fig. 3, The slug was broken when the thickness is δ= 3 mm. It can be seen that the thickness of the liner was too small to form a stable jet. With the increase of thickness, the fluidic formability tended to be good. In terms of jet length, with the increase of liner thickness, the jet length decreased, and the formed jet gradually becomes “short and thick”.
Fig. 3Performance curve of rear stage jet under different liner wall thickness
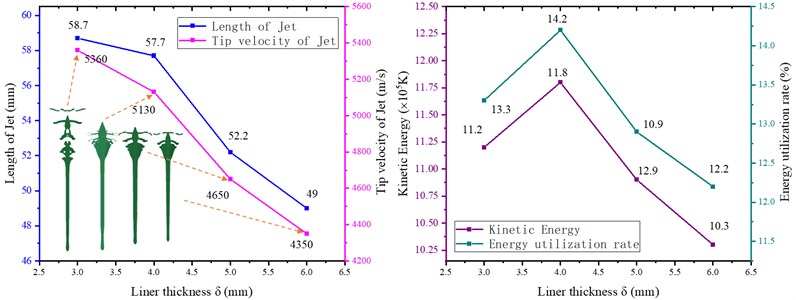
Drew the liner thickness δ influence law curve of jet velocity, length, kinetic energy and utilization of energy. It can be seen from the curve that with the increase of liner thickness, the jet length decreased as well as the head velocity. This was because the initial total energy of the explosive remained unchanged, and the mass increased with the increase of the thickness of the liner. According to the kinetic energy theorem, the velocity and energy conversion rate of the jet generally showed a downward trend. Because the unstable jet would be formed when the liner thickness was 3 mm, which would affect the energy conversion, therefore, in the law curve of jet kinetic energy and energy conversion rate δ inflected at point of 4 mm. By comprehensively comparing, the thickness of the rear liner was optimized to be 4 mm.
4.2. The effect of front liner thickness δ on jet forming
Half cone angle of the front liner was set to 45°, the other geometric parameters and initiation mode were consistent with the reference model of the front warhead. The charge structures with the thickness of the liner of 3 mm, 4 mm, 5 mm and 6 mm were numerically simulated.
There was also a positive correlation between jet stability and wall thickness in the front stage liner. The thin-walled liner (3 mm, 4 mm) would break due to the high velocity of the jet head driven by explosives.
Similarly, drew the liner thickness δ influence law curve of jet velocity, length, kinetic energy and utilization of energy. It can be seen from the curve that, consistent with the law of the former liner, the jet velocity, length, kinetic energy and energy conversion rate generally decreased with the increase of liner thickness, and the inflection point of jet kinetic energy and energy utilization rate curve appeared when the thickness was 5 mm. By comprehensively comparing the jet performance parameters, the thickness of the front stage liner was optimized to be 5 mm.
Fig. 4Performance curve of front stage jet under different wall thickness
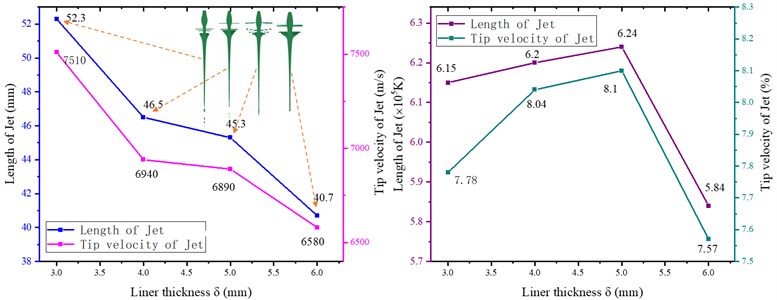
4.3. Simulation calculation of serial warhead linkage
The above research only considered the forming of shaped charge jet when the each warhead acted alone. In order to verify the feasibility of tandem shaped charge warhead in increasing jet length, the linkage simulation calculation of tandem shaped charge was carried out. In order to make the front and rear jets form a tandem jet with good connection shape, the initiation delay time was determined as 220 μs.
From the simulation process, it can be seen that the rear charge detonates and collapses the liner to form a jet. After the rear jet passes through the central tube bushing of the front stage, the front charge detonated and collapsed the central liner to form a tandem jet connected in sequence.
Due to the influence of the detonation products formed by the front charge, there were some differences between the formation form of the front stage jet and the separate calculation of the front stage warhead. The velocity of the rear stage slug was about 2000 m·s-1, while the head velocity of the front stage jet was higher than that of the rear stage slug, so the front stage jet must be able to catch up with the rear stage jet; After 300 μs, the front stage jet and the rear stage jet were connected in sequence to form a long jet in tandem. Measured, the length of the whole tandem jet was 108.5 cm at the time of 340 μs, while the effective jet length (excluding the slug) was 95.7 cm, which was 65 % higher than the jet length of the rear stage charge, and the performance of the tandem jet was significantly improved.
Fig. 5Tandem jet forming process
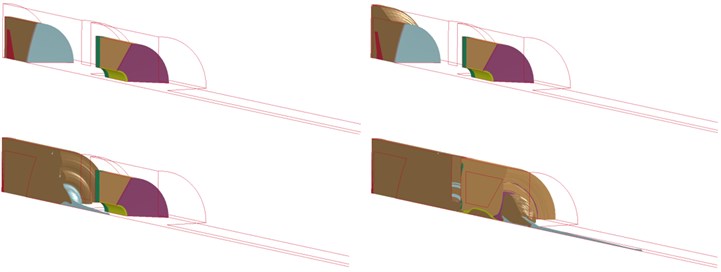
Fig. 6Profile of tandem jet forming process
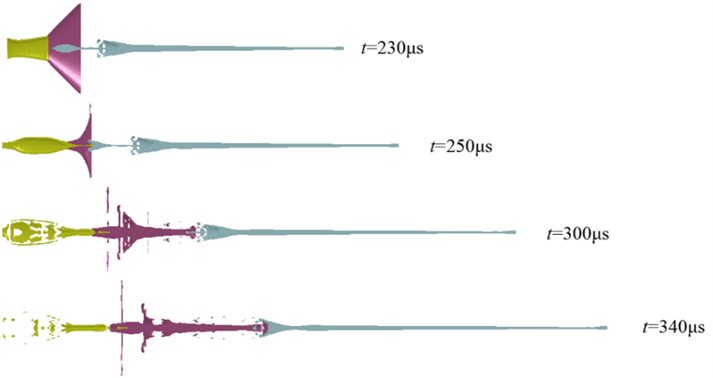
5. Conclusions
1) In order to greatly increase the jet length, a tandem shaped charge structure with reverse order initiation mode was numerically simulated and analyzed.
2) The detonation wave propagation and jet shape in the process of front and rear stage jet forming were analyzed. The performance of metal jet under the change of thickness δ of front and rear liner was calculated respectively. The jet length, energy and stability were comprehensively analyzed. The best structural parameter was determined as: rear liner δ=4 mm, front stage liner δ= 5 mm.
3) The linkage simulation of the front and rear stage warhead was carried out for the optimized structure. The calculation results showed that after the collapse of the two-stage liner, the front and rear continuous long jet was formed, which was significantly higher than the length of the single-stage jet. The research results had a certain reference significance for the design and application of the tandem shaped charge warhead.
References
-
C. Chen, X. M. Wang, and L. I. Wen-Bin, “Research on matching relationship between tandem shaped charge delay initiation time and charge interval,” Beijing Ligong Daxue Xuebao/Transaction of Beijing Institute of Technology, Vol. 12, No. 34, pp. 1217–1222, 2014.
-
A. V. Malygin, E. V. Proskuryakov, and M. V. Sorokin, “Matching of operation of “base-head” composite shaped-charge stages,” Journal of Applied Mechanics and Technical Physics, Vol. 53, No. 1, pp. 136–139, Jan. 2012, https://doi.org/10.1134/s0021894412010178
-
C. Chuang, L. I. Wei-Bing, and W. Xiao-Ming, “Optimization design of precursor k-charge structure of tandem warhead,” Chinese Journal of High Pressure Physics, 2014, https://doi.org/10.11858/gywlxb.2014.01.012
-
N. D. Gerami, G. H. Liaghat, G. H. R. S. Moghadas, and N. Khazraiyan, “Analysis of liner effect on shaped charge penetration into thick concrete targets,” Journal of the Brazilian Society of Mechanical Sciences and Engineering, Vol. 39, No. 8, pp. 3189–3201, Aug. 2017, https://doi.org/10.1007/s40430-017-0797-6
-
Z. H. Yao, “Study of airport unexploded ordnance clearance warhead technology,” North University of China.
-
J.-Q. Liu, W.-B. Gu, M. Lu, H.-M. Xu, and S.-Z. Wu, “Formation of explosively formed penetrator with fins and its flight characteristics,” Defence Technology, Vol. 10, No. 2, pp. 119–123, Jun. 2014, https://doi.org/10.1016/j.dt.2014.05.002
-
“LS-DYNAR Keyword User’s Manual V971,” Livermore Software Technology Corporation (LSTC), Livermore, 2012.