Abstract
The results of the study of acoustic characteristics of aircraft radial piston engines ASH-62IR and M-14P are presented. The tests were carried out during the race of the power plants of the AN-2 and Yak-18T light propeller-driven aircrafts under static conditions at the local aerodrome. It is shown that the method of organizing the exhaust of a multi-cylinder engine determines the main tone frequency. The influence of the engine power condition on the directivity of the tonal noise components is considered. The dependences of the sound power on the engine speed are obtained.
1. Introduction
Currently, internal combustion engines (ICE) are used as a propeller drive for light aircraft, helicopters and unmanned aerial vehicles (UAVs), while providing low specific fuel consumption and long flight time [1, 2].
The aircraft noise with piston engines is a superposition of fields formed by the radiation of a power plant [3-7] (propeller [8], piston engine [9]) and an airframe [10, 11], taking into account aeroacoustics effects in real power plant configurations, such as the scattering of power plant noise on airframe elements [12, 13], the noise of the “blade-turbulent wake” interaction noise for pushing layouts [14], the “wing (pylon)-blade” interaction for pulling layouts.
In general, the role of a piston engine in the overall noise level of an aircraft will be determined by many factors, among which we note: the power condition of the power plant, the direction of sound radiation, the configuration of the power plant on the aircraft, the number of stroke and displacement of the engine, the ignition method, the type of mixing, load, the presence of mufflers in the intake and exhaust paths and bonnets, the unit of noise assessment, etc.
Modern light propeller-driven aircraft (LPDA) are certified for community noise during the take-off power condition of the power plant, and the main methods used to reduce noise are increasing the number of blades and installing exhaust noise mufflers [15].
For small-sized UAVs, it is important to ensure low noise levels in cruising flight mode, and approaches to reducing LPDA noise may not be applicable due to the following circumstances:
– With an increase in the number of blades of a small-sized propeller operating at low Reynolds numbers, one can expect deterioration in the aerodynamic characteristics of the UAV [16].
– The inability to install exhaust noise mufflers due to the mass and dimensional limitations of the UAV.
Therefore, the study of the patterns of noise generation by aircraft internal combustion engines in order to develop reliable methods for assessing the community noise of propeller-driven UAVs [17] is an urgent and important task.
The purpose of this work is to study the spectral, directivity and energy characteristics of the sound field of radial piston engines used in small aircraft as part of the power plants of light propeller-driven aircrafts.
2. Object of study and test procedure
The objects of the tests are radial 4-stroke gasoline engines with external mixing and air-cooling ASH-62IR and M-14P, installed on light propeller-driven aircrafts AN-2 and YAK-18T, respectively. The aircraft have automatic variable pitch propellers operating in a straight line. The engines under study are low-altitude, but to improve the quality of the fuel-air mixture and operational characteristics, drive centrifugal superchargers are installed on the engines. Exhaust noise mufflers are not installed on engines.
The main parameters [18, 19] and engine power conditions during aircraft tests are presented in Tables 1 and 2, respectively. It can be seen that the engines are similar in the main parameters, which are compression ratio, power-to-volume ratio and specific power. Additionally, Table 1 provides information on the gear ratio and the number of blades of the power plants in question. This information determines the frequencies of the tonal components of the propeller in the noise spectrum of the power plant.
Table 1The main parameters of the studied power plants of light propeller-driven aircrafts
Aircraft | AN-2 | YAK-18T |
Engine | ASH-62IR | M-14P |
Available power, kW | 735.43 | 265 |
Displacement, l | 29.86 | 10.161 |
Compression ratio | 6.4 | 6.3 |
Power-to-volume ratio, kW/l | 24.62 | 26.06 |
Specific power, kW/kg | 1.31 | 1.24 |
Gear ratio | 0.6875 | 0.658 |
Propeller | AV-2 | MTV-9 |
Number of blades | 4 | 3 |
Table 2Engine power conditions during tests
Aircraft | AN-2 | YAK-18T |
Engine | ASH-62IR | M-14P |
Power condition No. | , rpm | |
1 | 1100 | 1160 |
2 | 1300 | 1450 |
3 | 1500 | 1740 |
4 | 1700 | 2030 |
5 | 1900 | 2320 |
6 (nominal) | 2100 | 2610 |
7 (take-off) | – | 2900 |
The reduced power conditions of power plants in the paper are understood to be modes with a rotation speed less than when the engine is running in cruising mode. The ASH-62IR engine could not be brought to the take-off power condition, which corresponds to the engine speed of 2200 rpm when the propeller run under static condition and the maximum power condition is the nominal (2100 rpm). For the M-14P engine, all power conditions from idle to take-off were considered. The actual engine speeds were determined based on the analysis of narrowband spectrum of sound pressure levels.
The tests were carried out at the local aerodrome of the Moscow Aviation Institute (National Research University) with an underlying surface in the form of mown grass. The sound pressure during the tests of the AN-2 aircraft was measured at 12 points of the acoustic field located on an arc of a circle with a radius of 30 meters and in increments of 15° (Fig. 1(a)). The center of the arc of the circle coincided with the projection of the propeller sleeve on the earth's surface. The direction () 0° corresponded to the radiation into the front hemisphere in the plane passing through the crankshaft, and the direction 90° corresponded to the direction of radiation in the plane of the propeller disc. When testing the power plant of the YAK-18T aircraft, measurements were carried out in the following directions 0, 20, 40, 60, 80, 90, 100, 120, 140 and 160° (Fig. 1(b)). Measuring microphones in both cases were located at the level of the earth's surface.
Fig. 1Scheme of the noise measurement points on the arc of a circle with a radius of 30 m,
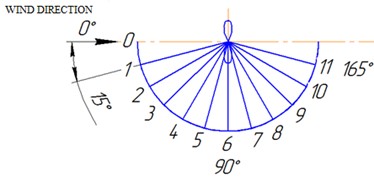
a) AN-2
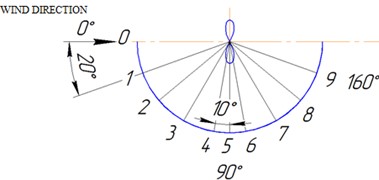
b) YAK-18T
when testing light propeller-driven aircraft
The “PORTABLE” measuring system was used for recording acoustic measurements and subsequent data processing. Acoustic signal measurements were performed in parallel from 12 measuring channels with a sampling frequency of 51200 Hz for 30 seconds. Post-processing of the signal within the framework of the purposes of this work included obtaining narrowband spectrum of sound pressure levels (SPL) with a bandwidth of 1.56 Hz in the frequency range of 0.1-10000 Hz. The Hanning window with 50 % overlap was used as the Fourier transform window for obtaining narrowband spectrum.
During the tests, atmospheric parameters (temperature, pressure and relative humidity), as well as wind speed and direction were measured. To minimize measurement uncertainty, the aircraft was installed in such a way that the wind direction corresponded to direction 0°. Measurements were performed at wind speeds of less than 2 m/s. The ambient noise levels during the tests were lower than the noise levels of the power plant in the entire studied frequency range by at least 1 0-15 dB [20].
3. Test results
3.1. Spectral characteristics of the sound field of propeller-driven power plants
The noise spectrum of the propeller power plant includes the tonal components of the noise of the propeller at frequencies multiple of the frequency of the blades and the piston engine at frequencies multiple of the frequency of the flashes in the cylinders. The frequencies of cylinder () and engine () tones in the engine noise spectrum are determined by the ratios:
where – tone number, – engine speed (rpm), – number of cylinders, – number of strokes in the engine (2 or 4).
Fig. 1 shows the narrowband spectrum of sound pressure levels measured during the run of the AN-2 power plant in reduced (Fig. 2(a)) and nominal (Fig. 2(b)) power conditions. On the graphs, the figures with the indices “p” and “c” indicate the first two tones of the propeller noise and tones (from the 2nd to the 10th) at frequencies multiple of the frequency of flashes in the engine cylinders, respectively. It can be seen that the first cylinder tones in the noise spectrum are masked by the broadband component, the lower the engine speed, the fewer cylinder tones stand out against the broadband noise. When operating at nominal mode, the power plant noise spectrum contains tonal components between the 2nd and 3rd, 8th and 9th and 9th and 10th cylinder tones, which are most likely due to the run of the power plant units, but it was not possible to identify the sources of this tonal radiation.
In accordance with Eq. (2), the 1st engine tone is the 9th cylinder tone. But the tones of the engine noise of the highest intensity when operating in reduced power condition correspond to the 5th and 7th cylinder tones. When running in nominal power condition, the sound pressure level of the 2nd cylinder tone is even slightly higher (by ~1 dB) than the sound pressure levels of the 5th and 7th tones.
Fig. 2Narrowband spectrums of sound pressure levels measured in direction 105° for two different power conditions of AN-2 power plant
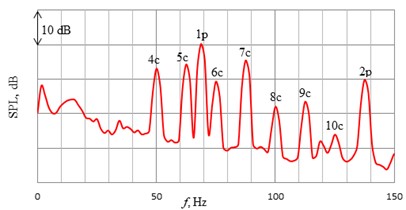
a)1500 rpm
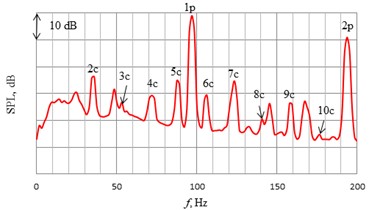
b)2100 rpm
In the ASH-62IR engine, the exhaust is organized in such a way that exhaust gases from the cylinders fall into the circular flame tube and then into the exhaust manifold (Fig. 3). The ends of the circular flame tube are open, and it turns out that 7 cylinders work together for one exhaust, and the two lower cylinders work separately and their exhaust gases go down without falling into the common exhaust manifold.
And yet, the main tone in the noise spectrum of the ASH-62IR engine will be the 7th cylinder tone due to the design features of the exhaust system of this engine. And the 5th cylinder tone is most likely the main tone for two cylinders operating on separate exhausts, which is consistent with the experimental data obtained by the author earlier when studying the noise of a UAV with a single-cylinder 4-stroke gasoline engine [21]. The 2nd cylinder tone is most likely the main tone for the two lower cylinders (two imaginary single-cylinder engines) running on separate exhausts.
Thus, the multi-cylinder radial engine ASH-62IR can be considered as a complex noise source, consisting in fact of three separate imaginary engines: 7-cylinder and two single-cylinder.
Fig. 3General view of the exhaust system of the ASH-62IR engine on the AN-2 aircraft
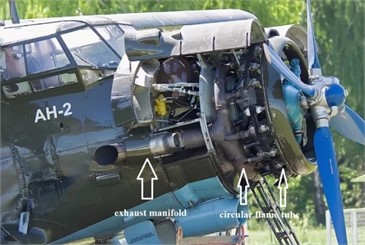
Fig. 3 shows narrowband spectrum of sound pressure levels measured during running of the power plant of the YAK-18T aircraft in reduced (Fig. 4(a)) and take-off (Fig. 4(b)) power conditions. The graphs, similar to the data presented in Fig. 1, indicate tones at frequencies multiple of the frequency of the propeller blades, and tones at frequencies multiple of the frequency of the flashes in the engine cylinders, respectively. Just as when the ASH-62IR engine is running, the 1st cylinder tones in the noise spectrum when running at reduced modes are masked by a broadband component.
Fig. 4Narrowband spectrums of sound pressure levels measured in direction 100° for two different power conditions of YAK-18T power plant
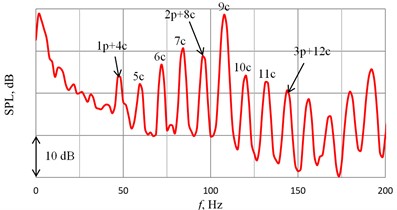
a)1450 rpm
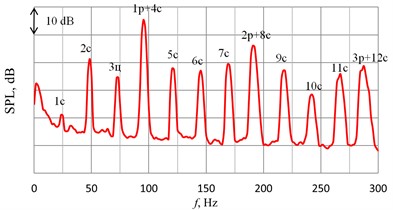
b)2900 rpm
It can be seen that the frequencies of the 1st tone of propeller noise and the 4th cylinder tone of engine noise, the 2nd tone of propeller noise and the 8th cylinder tone, as well as the 3rd tone of propeller noise and the 12th cylinder tone in the spectrum are close and in spectral analysis with a given bandwidth (1.56 Hz) actually coincide. Most likely, at the frequency of the 1st tone of the noise of the propeller and the 4th cylinder tone, the radiation of the propeller dominates when the power plant is running in take-off power condition, but at the frequency of the 2nd tone of the propeller noise and the 8th cylinder tone, etc., given the monotonous nature of the decrease in the intensity of the propeller noise with the frequency, it is impossible to speak unequivocally about the dominance of the propeller noise. At reduced power conditions (Fig. 3(a)), most likely the contribution of the tones of the propeller noise is insignificant against the background of the ICE noise.
The main tone of the engine when running in reduced mode is the 9th cylinder tone (1st engine tone in accordance with Eq. (2)), and when running in take-off power condition, the level of the 2nd cylinder tone is slightly higher than that of the other cylinder tones in the spectrum.
In the M-14P engine, the exhaust is organized in such a way that exhaust gases from the cylinders fall into two annular exhaust manifolds (Fig. 5). One collector connects four cylinders, and the other connects five.
Fig. 5General view of the exhaust system of the M-14P engine on the YAK-18T aircraft
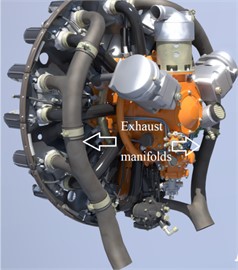
Thus, in fact, the M-1P engine is a complex noise source consisting of actually four separate dummy engines: a 5-cylinder, a 4-cylinder and two single-cylinder.
Note the general characteristic features of the spectral characteristics of the studied 9-cylinder radial engines:
– at reduced engine power conditions in the noise spectra, the first cylinder tones do not stand out against the broadband noise;
– at the nominal and take-off power conditions of the power plants under study, the 2nd cylinder tone is slightly higher in level than other tonal components in the radiation spectrum;
– the method of organizing the exhaust of multi-cylinder internal combustion engines significantly affects the intensity of the tonal components in the spectrum.
As part of the tests of propeller-driven power plants, it is not possible to separate the vortex component of the propeller noise [22] and the broadband component of the ICE noise, therefore, further analysis of the directivity and energy characteristics of engine noise is performed for the tonal components.
3.2. Directivity pattern of ICE noise
Fig. 6 shows the directivity patterns of the tonal components of the noise and the overall tonal radiation of the ASH-62IR ICE for the noise tones shown in the graphs allocated in the radiation spectrum of the power plant. It can be seen that for reduced (Fig. 6(a)) and nominal (Fig. 6(b)) engine power conditions, the maximum overall tonal radiation occurs in the front hemisphere along the crankshaft axis (0°) and in the rear hemisphere in the direction of 135°. The maximum in the front hemisphere is most likely due to structural-borne noise, and in the rear – the noise of the exhaust of the ICE.
For a reduced power condition, the 7th cylinder tone determines the direction of the overall radiation of the internal combustion engine, except for the angles of 105 and 165°, where the contribution of the 5th cylinder tone is also significant. When running at the nominal power condition, the directivity of the overall noise of the internal combustion engine is determined in the range of azimuth angles 0-45° and 165° by radiation on the 7th cylinder tone, in the range of angles 60–75° by radiation at the frequency of the 5th cylinder tone, in the range of angles 90-120° by radiation on the 5th and 7th tones, and in the directions 135-150° by radiation on the 4th cylinder tone.
Fig. 6Directivity patterns of the tonal components of the ASH-62IR engine noise
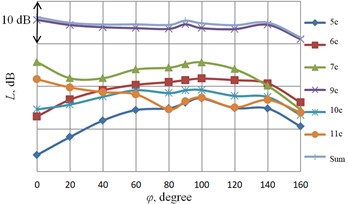
a)1450 rpm
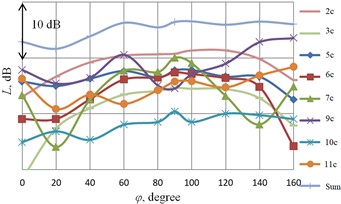
b)2900 rpm
When running in the take-off power condition (Fig. 6(a)), the direction of the overall radiation of the internal combustion engine in the directions of 20-120° is determined by radiation at the frequency of the 2nd cylinder tone. The 9th cylinder tone dominates in the directions 0, 140 and 160°, and also makes a significant contribution to the overall radiation in the direction of 60°.
To assess the effect of the power condition on the directivity patterns of the overall tonal noise of the internal combustion engine, the measurement results were brought to a normalized form according to the expression:
where – sound pressure level measured in the direction , – sound pressure level measured in the direction 0°.
The normalized directivity patterns of the overall tonal radiation of the ASH-62IR and M-14P engines are shown in Fig. 7(a) and (b), respectively.
For the ASH-62IR engine, there is no significant change in the directivity patterns during the transition from reduced power conditions to nominal. As previously noted, the maximum in the front hemisphere (0°) is most likely due to structural-borne engine noise, the maximum in the rear hemisphere (135°) is exhaust noise. At the same time, the minimum noise levels are observed in the direction of 90°. When assessing the community noise of an aircraft with this engine, it is possible to use the radiation directivity factor obtained from the radiation directivity characteristic averaged over all power conditions.
For the M-14P engine, one can see a significant influence of the engine speed on the directivity pattern. The radiation maximum corresponds to azimuthal angles of 60 and 90 degrees. When assessing the community noise of an aircraft with this engine, it is necessary to use radiation directivity factors obtained for each characteristic (cruising, nominal or take-off) engine power condition. At reduced power conditions, the maximum in the direction of 0° are most likely due to structural-borne engine noise. And the maximum in the direction of 140° are most likely caused by exhaust noise and shift to an angle of 90° with an increase in the power condition.
A significant difference in the directivity patterns of the ASH-62IR and M-14P engines is due to:
– the difference in the methods of exhaust organization;
– the presence of the M-14P engine, in addition to the bonnet, additional controlled shutters installed to improve the cooling of the engine cylinders in flight, which also affect the energy and directivity characteristics of structural-borne noise.
Fig. 7Normalized directivity patterns of the overall tonal noise of piston engines
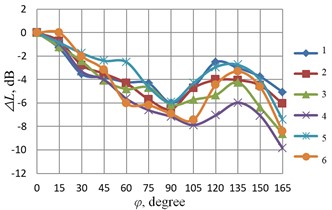
a) ASH-62IR
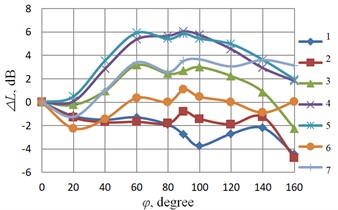
b) M-14P
3.3. Energy characteristics of ICE noise
Based on the measured sound pressure levels on the arc of the circle, the overall sound power level of the tonal component of the internal combustion engine noise for different power conditions is estimated in accordance with the ratio:
where – distance from the source to the microphone, – function of the dependence of the overall sound pressure level on the azimuth angle.
It should be noted that when calculating sound power levels, the acoustic field of the engine was assumed to be axisymmetric with respect to the crankshaft axis, and sound radiation is carried out into the hemisphere.
The dependences of the overall sound power levels of the ASH-62IR and M-14P engines depending on the engine speed are shown in Fig. 8. At engine speeds over ~1500 rpm, the ASH-62IR engine is ~2 dB noisier. This is due to almost 3 times the displacement and more available power at the same engine speeds.
Based on the presented data, indicators of the degree of dependence of the overall sound power on the engine speed were obtained. For the ASH-62IR engine, the indicator of the degree of dependence is 3.9, and for the M-14P engine is 1.8. A significant difference in the degree indicators indicates a different ratio of sources in the overall noise of engines in different power conditions.
If the first two reduced modes are not taken into account for the ASH-62IR engine when evaluating the degree indicator, then the degree indicator will be 1.6, which is close to the degree indicator for the M-14P engine.
Fig. 8Dependences of sound power levels on the engine speed of the ASH-62IR and M-14P engines
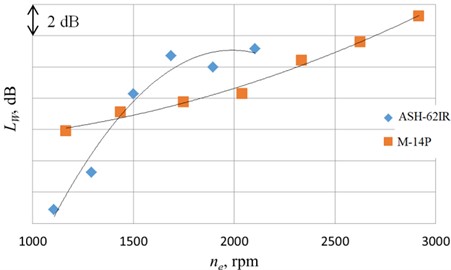
4. Conclusions
The results of the study of acoustic characteristics of aviation radial piston engines with similar specific characteristics without exhaust mufflers are presented. Spectral, energy and directivity characteristics of sound fields are considered. The significant influence of the exhaust organization method (the number of cylinders in the engine working on one exhaust) on the spectrum and directivity pattern of the internal combustion engine noise is shown. The obtained directivity factors and energy dependences can be used to verify methods for accessing community noise.
References
-
P. Moshkov, V. Samokhin, and A. Yakovlev, “About the community noise problem of the light propeller aircraft,” Akustika, Vol. 34, pp. 66–71, Nov. 2019, https://doi.org/10.36336/akustika20193466
-
P. Moshkov, V. Samokhin, A. Yakovlev, and C. Bolun, “The problems of selecting the power plant for light propeller-driven aircraft and unmanned aerial vehicle taking into account the requirements for community noise,” Akustika, Vol. 39, pp. 164–169, 2021, https://doi.org/10.36336/akustika202139162
-
R. K. Rathgeber and D. E. Sipes, “The influence of design parameters on light propeller aircraft noise,” in National Business Aircraft Meeting and Engineering Display, Feb. 1977, https://doi.org/10.4271/770444
-
K. E. Jones, “Acoustic flight test of the Piper Lance,” United States. Federal Aviation Administration. Office of Environment and Energy, Dec. 1986.
-
D. Jones, J. D. Lewis, and M. Hedrick, “Noise levels during recreational flight of a Cessna 172 Skyhawk,” The Journal of the Acoustical Society of America, Vol. 142, No. 4, pp. 2541–2542, Oct. 2017, https://doi.org/10.1121/1.5014288
-
C. Dahan, L. Avezard, G. Guillien, C. Malarmey, and J. Chombard, “Propeller light aircraft noise at discrete frequencies,” Journal of Aircraft, Vol. 18, No. 6, pp. 480–486, Jun. 1981, https://doi.org/10.2514/3.57515
-
J. J. Berton and D. M. Nark, “Low-noise operating mode for propeller-driven electric airplanes,” Journal of Aircraft, Vol. 56, No. 4, pp. 1708–1714, Jul. 2019, https://doi.org/10.2514/1.c035242
-
S. Timushev, A. Yakovlev, and P. Moshkov, “Numerical simulation of the light aircraft propeller noise under static condition,” Akustika, Vol. 41, pp. 100–106, 2021, https://doi.org/10.36336/akustika202141100
-
W. Dobrzynski, B. Gehlhar, W. Dobrzynski, and B. Gehlhar, “The noise from piston engine driven propellers on general aviation airplanes,” in 3rd AIAA/CEAS Aeroacoustics Conference, May 1997, https://doi.org/10.2514/6.1997-1708
-
P. Moshkov, “Study of the influence of in-flight conditions on the light propeller-driven aircraft noise,” Aerospace Systems, Vol. 5, No. 1, pp. 131–140, Mar. 2022, https://doi.org/10.1007/s42401-021-00127-5
-
K. Yamamoto, K. Hayama, T. Kumada, and K. Hayashi, “A flight demonstration for airframe noise reduction technology,” CEAS Aeronautical Journal, Vol. 10, No. 1, pp. 77–92, Mar. 2019, https://doi.org/10.1007/s13272-019-00376-3
-
A. Vieira, M. Snellen, A. M. N. Malgoezar, R. Merino-Martinez, and D. G. Simons, “Analysis of shielding of propeller noise using beamforming and predictions,” The Journal of the Acoustical Society of America, Vol. 146, No. 2, pp. 1085–1098, Aug. 2019, https://doi.org/10.1121/1.5121398
-
A. E. Alves Vieira, A. M. N. Malgoezar, M. Snellen, and D. G. Simons, “Experimental study of shielding of propeller noise by a wing and comparison with model predictions,” in Euronoise, pp. 237–244, 2018.
-
V. A. Titarev, G. A. Faranosov, S. A. Chernyshev, and A. S. Batrakov, “Numerical modeling of the influence of the relative positions of a propeller and pylon on turboprop aircraft noise,” Acoustical Physics, Vol. 64, No. 6, pp. 760–773, Nov. 2018, https://doi.org/10.1134/s1063771018060118
-
M. P. A., S. V. F., and Y. A. A., “Engine-propeller power plant aircraft community noise reduction key methods,” International Conference on Electrical, Electronics, Materials and Applied Science, Vol. 1952, No. 1, p. 020059, 2018, https://doi.org/10.1063/1.5032021
-
S. P. Ostroukhov, Aerodynamic of Propeller and Ducted Propeller. Fizmatlit: Moscow, 2014.
-
P. A. Moshkov and V. F. Samokhin, “Integral model of noise of an engine-propeller power plant,” Journal of Engineering Physics and Thermophysics, Vol. 91, No. 2, pp. 332–338, Mar. 2018, https://doi.org/10.1007/s10891-018-1753-8
-
P. S. Labazin, ASh-62IR Aviation Engine. (in Russian), Moscow: Transport, 1972.
-
A. I. Lapshin and P. I. Anokhin, M-14P Aviation Engine. (in Russian), Moscow: Transport, 1976.
-
P. Moshkov, “Ambient noise: problem and study in the framework of UAV aeroacoustics,” Akustika, Vol. 41, pp. 16–21, 2021, https://doi.org/10.36336/akustika/20214116
-
P. Moshkov, N. Ostrikov, V. Samokhin, and A. Valiev, “Study of Ptero-G0 UAV Noise with Level Flight Conditions,” in 25th AIAA/CEAS Aeroacoustics Conference, May 2019, https://doi.org/10.2514/6.2019-2514
-
P. A. Moshkov, “Study of vortex noise of rotating blades,” Herald of the Bauman Moscow State Technical University. Series Natural Sciences, Vol. 2, No. 2 (89), pp. 85–98, Apr. 2020, https://doi.org/10.18698/1812-3368-2020-2-85-98
About this article
The authors thank Kozhevnikov Yevgeniy, head of the Moscow Aviation Institute (National Research University) local aerodrome for assistance in organization of acoustics tests.