Abstract
The damage to propellant is unavoidable during the production, storage, transportation, and application, resulting in huge safety risks. It is greatly significant to endow the matrix (polyurethane) of the propellant with self-repairing properties. Herein, the copolymerization and double dynamic bonds cross-linking strategies were applied to the polyurethane design, and an intelligent polyurethane material that can self-repair at sub-zero temperatures was successfully prepared. The self-repairing efficiency of the polyurethane is 70.1 % and the elongation at break is ~1424 % at –40 ℃ for 12h.While at –20 ℃ for 12 h, the self-repairing efficiency is 77.9 % and the elongation at break is as high as ~1649 %, which is rare in the existing literature. The intelligent polyurethane material synthesized in this paper possesses an excellent application prospect in the field of composite solid propellant and has important military significance.
1. Introduction
Composite solid propellants are widely used in rockets, missiles, and other weapons [1-3]. The mechanical performances of the composite propellant are the key elements that decide the structural security of the weapon system, and it depends upon the mechanical properties of its matrix adhesive to a great extent [4, 5]. However, the occurrence of cracks and damage to adhesive is always inevitable, which will trigger the structure security problems of composite solid propellant and cause great waste and security risks [6].
In the past few decades, self-repairing technology has developed rapidly, and self-repairing materials have been widely used in daily life, which will provide a feasible solution to address the above problems. At present, in accordance with the repairing mechanism, self-repairing materials can be classified as external and internal types [7-9]. External self-repairing materials have the shortcoming of one-time repair, so the mainstream self-healing materials are internal. Internal self-repairing materials contain reversible bonds, including non-covalent and covalent bonds. When damaged, these reversible bonds can repair themselves under certain conditions.
Research on low-temperature self-healing polyurethane materials can make it applicable in more fields. However, mechanical properties and low-temperature self-healing ability have always been a pair of contradictions, and there is little existing research on low-temperature self-healing materials. Therefore, it is greatly significant to accept a low-temperature self-healing polyurethane with excellent mechanical properties.
Herein, a sub-zero self-repairing intelligent polyurethane material with excellent mechanical properties was successfully prepared by copolymerization of hydroxyl-terminated polyethylene glycol-tetrahydrofuran co-polyether (HTPE) and hydroxyl-terminated polybutadiene (HTPB) and introducing quadruple hydrogen bonds and disulfide bonds. Some novel characterization methods were used to analyze its self-repairing performances.
2. Materials and characterization methods
2.1. Reagents
HTPB (liquid, -OH: 0.75 mmol/g, 99 %) and HTPE (liquid, -OH: 0.68 mmol/g, 99.95 %) was obtained from Liming Research & Design Institute of Chemical Industry Co., Ltd., Luoyang. N, N-dimethylformamide (DMF, liquid, ≥ 99.8 %) and dibutyl phthalate (DBP, liquid, 99.5 %) were obtained from Damao Chemical Reagent Factory, Tianjin. Isophorone diisocyanate (IPDI, liquid, 99 %) and triphenylbismuthine (TPB, powder) were obtained from Macklin Biochemical Technology Co., Ltd, Shanghai. 1,4-Butanedio (BDO, liquid, ≥ 99 %) was purchased by Jining Huakai Resin Co., Ltd. 2-amino-4-hydroxyl-6-methyl pyrimidine (UPy, 98 %) and b is (2-hydroxyethyl) disulfide (HEDS, liquid, 90 %) were obtained from Aladdin Co., Shanghai.
2.2. Samples preparation
First, 2.4 g of HTPB was added into a 150 ml three-necked flask and dried at 60 °C overnight. Next, 0.49 g of IPDI, 0.39 g of DBP, and 1.8 mg of TPB in 3 ml of DMF were placed in the flask. The mixture was mixed for 2 h at 60 °C to acquire prepolymer, then copolymerized with 0.6 g of HTPE. After that, 0.32 g of HEDS was dropped gradually and fully reacted with the copolymer at 60 °C for 2 h. Thereafter, 0.12 g of UPy dissolved in 2 ml of DMF was added and was mixed for another 2 h. Ultimately, the mixture was poured into a Teflon mold and cured for 24 h at 60 ℃ in a vacuum oven and coded as HUEPU. For comparison, three control groups were established, namely PU (p-HTPB, the chain extender is BDO), EPU (without HEDS and UPy, the chain extender is BDO), and HUPU (without HTPE).
2.3. Characterization
Temperature sweeps, frequency sweeps, and stress relaxation experiments were performed on the prepared polyurethanes using a dynamic thermomechanical analyzer. In the temperature sweep, the frequency was set to 1 Hz, the heating rate was 3 °Cmin-1, and the temperature range was –90-60 °C. For the frequency sweep and stress relaxation experiments, the temperatures were set to 25 °C, –20 °C, and –40 °C, the frequency range of the frequency sweep was 0.1-100 Hz, and the strain in the stress relaxation experiment was set to 50 %. Fourier transform infrared spectroscopy (FTIR) is measured by NicoletiS10 with a wave number range of 600-4000 cm-1and a resolution of 4 cm-1. According to GB/T 528-92, tensile experiments were characterized on the Instron 5982 at a rate of 100 mmmin-1. The results were averaged by three measured data at least. The test section sizes of the samples are 12×2×2 mm. In the self-repairing test, the polyurethanes were cut into two halves and kept at a certain temperature for 12h after contact. After that, the tensile test was conducted via the Instron 5982 universal testing machine at 100 mmmin-1 to record elongation at break (εb). The self-repairing efficiency was defined as Eq. (1):
3. Results and discussion
3.1. Design and characterizations of materials
The innovation of this design lies in the combination of copolymerization and dynamic bonding into the polyurethane to prepare polyurethane materials with excellent mechanical performances which can be self-repaired at sub-zero temperatures. In this study, polyurethane was prepared by a four-step method. First, HTPB reacted with IPDI to generate -NCO-terminated prepolymers. Then, it is copolymerized with HTPE, and then HEDS is reacted with the mixture to introduce disulfide bonds. Finally, the addition of UPy consumes excess -NCO groups and introduces quadruple hydrogen bonds. The chemical structure of polyurethane was characterized by FTIR. Fig.1 showed FTIR spectra of prepolymer and HUEPU. The spectrum of the prepolymer has obvious characteristic peaks at 1714 cm-1, 3312 cm-1, 1322 cm-1, and 1525 cm-1, which corresponds to the N-H and C = O stretching vibrations of the urethane bond, the C-N stretching vibration and the N-H bending vibration, respectively [10-12]. The prepolymer possessed an evident absorption peak at 2256 cm-1, which is due to the terminal -NCO group, and the peak disappeared after reacting with UPy, which means the successful synthesis of HUEPU.
Fig. 1FTIR spectra of HEPU and HUEPU
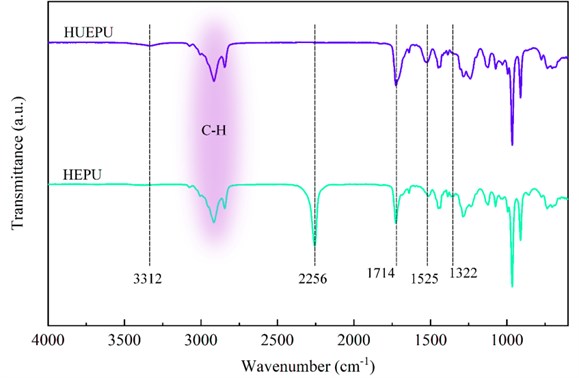
3.2. Dynamic thermomechanical analysis
From the temperature sweep curves (Fig. 2(a, b)), it can be seen that the glass transition temperature (Tg) of HUEPU was in the range of –77.8~–63.8 °C, while that of PU was in the range of –82.1~–66.8 °C. The Tg of the two were not much different, and both were at ultra-low temperatures. Fig. 3(b) is the stress relaxation curves of HUEPU polyurethanes. It can be seen that the relaxation time (2.3 min) at –20 °C was close to that at 25 °C (1.0 min), which indicates that the molecular chain mobility of the polyurethane is still good at –20 °C. However, the relaxation time at –40 °C was 30.7 min, which indicates that the molecular chain movement is greatly hindered at this time. This is due to the introduction of the HTPE long chain, which improves the fluidity of the polyurethane molecular chain. In addition, the rapid exchange reaction of disulfide bonds and coordination bonds also has an important contribution.
Fig. 2Temperature scan curves of a) PU and b) HUEPU
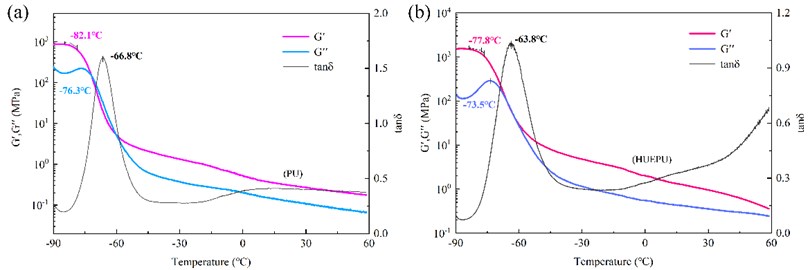
Fig. 3a) Frequency scan curves and b) stress relaxation curves of HUEPU
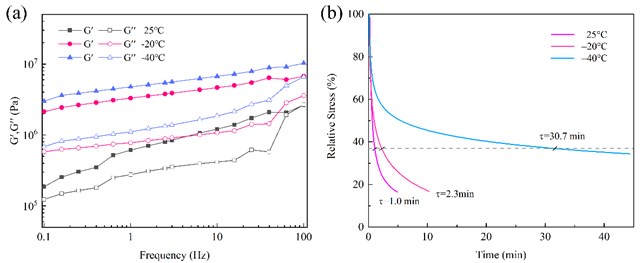
3.3. Mechanical and self-healing properties
Fig. 4(a-c) showed the stress-strain curves of four polyurethanes at 25 ℃, –20 ℃, and –40 ℃, respectively. Fig. 4(d) showed the elongation at break and tensile strength of HUEPU polyurethane. It can be concluded from Fig. 4 that at three temperatures, the tensile strength of PU was the highest, while the elongation at break was the lowest because its cross-linking network is irreversible. While HUEPU showed the highest elongation at break, followed by HUPU and EPU, which can be attributed to HEDS and UPy providing a large number of dynamic reversible disulfide bonds and quadruple hydrogen bonds for the polyurethane network [13]. At the same time, copolymerization can further reduce the cross-linking density of the polyurethane network, improve the flexibility of the molecular chain, and thus improve the mechanical properties [14].
Fig. 4Mechanical properties images of four polyurethanes
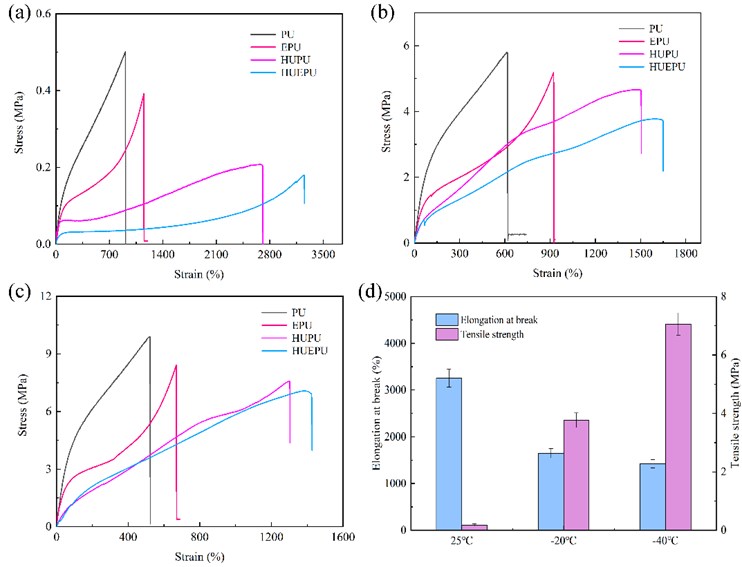
To test the self-repairing performance of specimens, all the polyurethane specimens were cut into two halves by a knife, and after being contacted without external force, they were placed in a temperature box for repairing for a certain time, and then their mechanical properties were tested (Fig. 5). The PU and EPU had almost no self-healing ability because of their irreversible crosslinking as shown in Fig. 5(a). With the addition of HEDS and UPy, the self-repair ability of HUPU was significantly improved. This can be due to the rapid exchange reactions of the quadruple hydrogen bonds and disulfide bonds, which enabled the polyurethane network to be re-crosslinked. The introduction of HTPE improves the fluidity of the molecular chain of polyurethane and further promotes the exchange reaction of dynamic bonds. Therefore, HUEPU shows the highest self-repairing performance. More importantly, the elongation at break of the repaired HUEPU at –40 ℃ and –20 ℃ reaches 998 % and 1285 %, which is 70.1 % and 77.9 % of that of the original sample, which is quite meaningful [15].
Fig. 5a) Self-repairing performance curves of four polyurethanes, b) c) self-repairing performance curves of HUPU and HUEPU, d) self-repair efficiencies of HUEPU at different temperatures
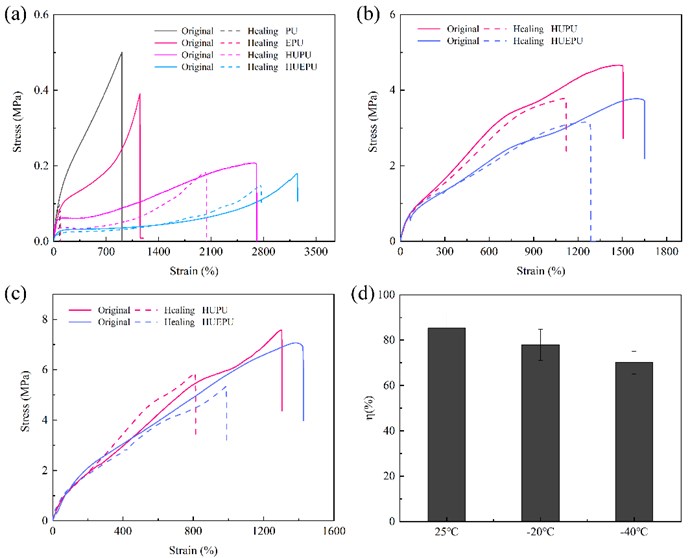
4. Conclusions
To sum up, through the reasonable design of the polyurethane network, an intelligent polyurethane material with excellent mechanical properties and self-repairing performances at sub-zero temperatures was successfully prepared. The self-repairing efficiency of the polyurethane is 70.1 % and the elongation at break is 1424 % at –40 ℃ for 12 h. While at –20 ℃ for 12 h, the self-repairing efficiency is 77.9 % and the elongation at break is as high as 1649 %. In addition, the Tg of polyurethane samples was extremely low (< –63 ℃), which was much lower than the normal temperature, thus ensuring the great mechanical performance of PU. This will make the polyurethane have a better prospect in the field of composite solid propellants.
References
-
J. Ren, H. Shi, H. Du, J. Li, and R. Yang, “Effect of polyhedral oligomeric silsesquioxane on combustion performance of HTPB propellants,” Combustion and Flame, Vol. 238, p. 111856, Apr. 2022, https://doi.org/10.1016/j.combustflame.2021.111856
-
T. Wang, J. Xu, H. Li, W. Ding, J. Liu, and X. Chen, “Crack propagation velocity and fracture toughness of hydroxyl-terminated polybutadiene propellants: Experiments and simulations,” Engineering Fracture Mechanics, Vol. 257, p. 108034, Nov. 2021, https://doi.org/10.1016/j.engfracmech.2021.108034
-
K.-J. Meng, H. Zhang, S.-Z. Wang, Y. Wang, Q. Zhang, and Q.-L. Yan, “Unique thermal and combustion behaviors of composite propellants containing a high-energy insensitive nitropyrimidine derivative,” Combustion and Flame, Vol. 237, p. 111855, Mar. 2022, https://doi.org/10.1016/j.combustflame.2021.111855
-
M. Ji, S. Zhu, Z. Ma, and H. Li, “Effects of adhesive modulus and curing conditions on curing behavior of silicate based ceramic coatings on carbon fiber reinforced resin matrix composites,” Ceramics International, Vol. 47, No. 8, pp. 11089–11096, Apr. 2021, https://doi.org/10.1016/j.ceramint.2020.12.232
-
V. K. Srivastava, T. Gries, T. Quadflieg, B. Mohr, M. Kolloch, and P. Kumar, “Fracture behavior of adhesively bonded carbon fabric composite plates with nano materials filled polymer matrix under DCB, ENF and SLS tests,” Engineering Fracture Mechanics, Vol. 202, pp. 275–287, Oct. 2018, https://doi.org/10.1016/j.engfracmech.2018.09.030
-
S. Yuan, S. Jiang, and Y. Luo, “Cross-linking network structures and mechanical properties of novel HTPE/PCL binder for solid propellant,” Polymer Bulletin, Vol. 78, No. 1, pp. 313–334, Jan. 2021, https://doi.org/10.1007/s00289-020-03110-w
-
J. Du, X. Li, H. Song, X. Cao, and J. Yao, “Self-healing coating preparation and anti-corrosion performance on 3D-printed stainless steel surface,” Journal of Materials Engineering and Performance, Vol. 30, No. 12, pp. 8715–8723, Dec. 2021, https://doi.org/10.1007/s11665-021-06025-3
-
J. Huang, L. Guo, and L. Zhong, “Synergistic healing mechanism of self-healing ceramics coating,” Ceramics International, Vol. 48, No. 5, pp. 6520–6527, Mar. 2022, https://doi.org/10.1016/j.ceramint.2021.11.198
-
X. Wang, Y. Li, C. Zhang, and X. Zhang, “Visualization and quantification of self-healing behaviors of microcracks in cement-based materials incorporating fluorescence-labeled self-healing microcapsules,” Construction and Building Materials, Vol. 315, p. 125668, Jan. 2022, https://doi.org/10.1016/j.conbuildmat.2021.125668
-
N. Sun et al., “Preparation and characterization of lignin-containing self-healing polyurethane elastomers with hydrogen and disulfide bonds,” Industrial Crops and Products, Vol. 174, p. 114178, Dec. 2021, https://doi.org/10.1016/j.indcrop.2021.114178
-
Y. Sun et al., “Bio-based vitrimer-like polyurethane based on dynamic imine bond with high-strength, reprocessability, rapid-degradability and antibacterial ability,” Polymer, Vol. 233, p. 124208, Oct. 2021, https://doi.org/10.1016/j.polymer.2021.124208
-
X. Li, X. Chen, S. Zhang, Y. Yin, and C. Wang, “UV-resistant transparent lignin-based polyurethane elastomer with repeatable processing performance,” European Polymer Journal, Vol. 159, p. 110763, Oct. 2021, https://doi.org/10.1016/j.eurpolymj.2021.110763
-
Y. Zhang et al., “Dual dynamic bonds self-healing polyurethane with superior mechanical properties over a wide temperature range,” European Polymer Journal, Vol. 163, p. 110934, Jan. 2022, https://doi.org/10.1016/j.eurpolymj.2021.110934
-
Y. Zhang et al., “Effect of chemical copolymerization and mixed chain extenders on mechanical properties of HTPB polyurethane,” IOP Conference Series: Materials Science and Engineering, Vol. 1167, No. 1, p. 012012, Jul. 2021, https://doi.org/10.1088/1757-899x/1167/1/012012
-
J. Ko, Y.-J. Kim, and Y. S. Kim, “Self-healing polymer dielectric for a high capacitance gate insulator,” ACS Applied Materials and Interfaces, Vol. 8, No. 36, pp. 23854–23861, Sep. 2016, https://doi.org/10.1021/acsami.6b08220