Abstract
In order to analysis the sulfate diffusion process in polypropylene fiber concrete, the influence of the introduction of polypropylene fiber on the porosity was calculated at first based on the spatial distribution features of polypropylene fiber in concrete, which was classified into three types, penetration type, half through type and embedded type. On the basis of Fick’s second law and reaction kinetics equation, the diffusion model of sulfate ions in polypropylene concrete was established. The numerical solution was achieved with the adoption of finite difference method and the concentration of sulfate ions at any position can be calculated. At last, the numerical solution was verified using the results of polypropylene fiber reinforced concrete sulfate attack test. The results show that the relative error between numerical calculation and the actual test results is less than 17.65 %, the accuracy of the model is relatively high.
1. Introduction
Most of the existing researches are the experimental research on the mechanical properties of polypropylene fiber concrete based on the difference of its own materials (such as fiber content, fiber type, water-cement ratio, etc.), or the analysis of the sulfate diffusion process in plain concrete. There is little research on the diffusion law of sulfate in polypropylene fiber concrete and its meso numerical simulation [1-4]. Therefore, this paper studies the diffusion process of sulfate in polypropylene fiber concrete, establishes the diffusion model of sulfate in polypropylene fiber concrete, and uses sulfate erosion test to verify the numerical simulation results.
2. Diffusion model of sulfate ions in polypropylene fiber concrete
2.1. Change of concrete porosity
Assuming that fibers are randomly distributed in concrete, they can be divided into three types according to their spatial positions, as shown in Fig. 1.
2.1.1. Through type polypropylene fiber
The through type polypropylene fiber penetrates the whole concrete model element up and down. Its length is equal to the thickness of the model element, and it introduced open pores, the interface is in direct contact with the external erosive liquid through the openings at both ends. The expression of porosity (φPFg) of through type polypropylene fiber is:
where, VPFg represents the volume of through polypropylene fiber; V represents the volume of polypropylene fiber concrete model element; N represents the number of through polypropylene fibers in the polypropylene fiber concrete model element, which can be converted according to the volume content of polypropylene fibers; dPF represents the diameter of polypropylene fiber; H represents the thickness of the model element, which is also the length of the through polypropylene fiber; X represents the length of the model primitive; L represents the width of the model primitive.
Fig. 1Distribution diagram of fiber in concrete
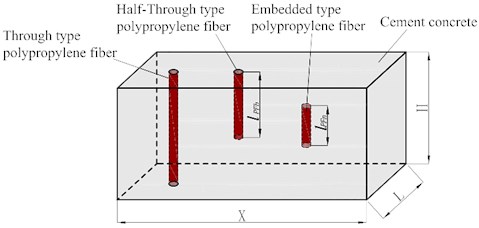
2.1.2. Half-Through type polypropylene fiber
The upper or lower end of the half-through type polypropylene fiber reaches the surface of the concrete model. The length of the polypropylene fiber is randomly distributed in the range of [0, H]. The pores introduced by it are open pores, and the interface is directly in contact with the external erosive liquid through the openings at the upper or lower end. The expression of porosity (φPFb) of half-through type polypropylene fiber is:
where, VPFb represents the volume of half-through type polypropylene fiber; V represents the volume of polypropylene fiber concrete model element; dPF represents the diameter of polypropylene fiber; lPFbi represents the length of the ith half-through type polypropylene fiber, lPFbi∈[0,H], i=0,1,2…n; X represents the length of the model primitive; L represents the width of the model primitive; H represents the thickness of the model primitive.
2.1.3. Embedded type polypropylene fiber
The embedded type polypropylene fiber is completely suspended in the concrete model element. The length of polypropylene fiber is randomly distributed in the range of (0, H), and the introduced pores are closed pores. The expression of porosity (φPFn) of Embedded type polypropylene fiber is:
where, cCA represents the concentration of hydrated calcium aluminate in concrete; cCA0 represents the initial concentration of calcium aluminate in concrete; VPFn represents the volume of embedded polypropylene fiber; V represents the volume of polypropylene fiber concrete model element; dPF represents the diameter of polypropylene fiber; lPFni represents the length of the i-th embedded polypropylene fiber, lPFni∈(0,H), i=0,1,2…n; X represents the length of the model primitive; L represents the width of the model primitive; H represents the thickness of the model primitive.
In the initial stage, because there are closed pores around the embedded polypropylene fiber, the interface will not contact with the external corrosive liquid. Sulfate reacts with cement hydration products to produce erosion products, which will gradually fill the pores in the concrete. As sulfate corrosion products continue to fill the pores in the concrete, microcracks will eventually occur. When the microcracks are located around the embedded polypropylene fiber, connecting pores will be formed. At this time, the cement mortar around the embedded polypropylene fiber will contact the erosion solution through the connecting pores.
2.1.4. Initial porosity of polypropylene fiber reinforced concrete
Regardless of the filling effect of erosion products on the pores, the initial porosity in the concrete can be expressed as:
where, fVc represents the volume fraction of cement; hα represents the hydration degree of cement; wc represents the water cement ratio; φ0PF represents the initial porosity introduced by polypropylene fiber.
The degree of hydration h can be expressed as hα=1-0.5[(1+1.67t)-0.6+(1+0.29t)-0.48], where t represents the time of cement hydration.
The initial porosity introduced by polypropylene fiber can be expressed as:
where, φPFg represents the porosity of the penetrating polypropylene fiber; φPFb represents the porosity of the semi-penetrating polypropylene fiber.
2.1.5. Polypropylene fiber concrete filled porosity
The filling of ettringite will affect the porosity of concrete. The porosity of concrete filled with ettringite can be expressed as:
where, Min is the minimum function; VcA1, VcA2, VcA3 respectively represent the volume consumption of C4AH13, C4AˉSH12 and C3A in the chemical reaction process in the concrete; mv-CH represents the molar volume of calcium hydroxide; γi represents the reaction coefficient of ettringite by reaction of tricalcium aluminate with gypsum; f represents the volume fraction of the initial porosity after the ettringite is filled with capillary pores; φPFn represents the porosity of the embedded polypropylene fiber.
Under sulfate attack, the porosity of the concrete is reduced due to the filling of erosion products. Then: φ=Max[(φ0-φprod),0].
2.2. Concentration distribution of sulfate ions
It is assumed that polypropylene fiber concrete meets the following conditions: saturation; isotropy; porous material, the diffusion coefficient of sulfate ions in concrete is a function of time. When polypropylene fiber concrete is exposed to a sulfate environment for a long time, SO2-4 will gradually diffuse from both sides to the inside. The erosion model of concrete is assumed to be one-dimensional symmetric model, then the erosion model is shown in Fig. 2.
Fig. 2Sulfate erosion model
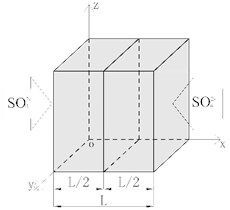
Fig. 3Sulfate erosion plane sketch
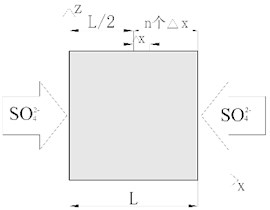
2.2.1. Diffusion reaction equation
The diffusion reaction equation of SO2-4 can be deduced by using Fick’s second law and chemical reaction kinetic equation as [5]:
where, C represents the concentration of SO2-4; x represents the position coordinates; t represents the diffusion time of SO2-4 in concrete; DC represents the diffusion coefficient of sulfate ions; Cd represents the concentration consumed by SO2-4 due to chemical reactions; C0 represents SO2-4 The boundary concentration; Π represents the cross-sectional area; L represents the thickness of the concrete specimen.
2.2.2. Diffusion coefficient
There is electrolyte solution containing Na+, K+, OH-, Ca2+, SO2-4and other ions in the internal pores of the concrete. According to Davis model [6] and the Mode Coupling Theory Method of Electrolyte Friction Electrolyte [7] and other electrolyte solution theory, the diffusion coefficient of SO2-4in concrete can be expressed as [8]:
∙[Λ0-(CZ2+Dz3ωΛ0)√c],
where, φ represents the saturated porosity after the erosion product fills the capillary pores, which is given by Eq. (10); R represents the gas constant; T represents the ambient temperature; τc represents the tortuosity of the transmission path in the concrete before the erosion product fills the capillary pores, It is given by Eq. (11); z represents the valence of SO2-4; F represents Faraday’s constant; I represents ionic strength, which is given by Eq. (10); α represents SO2-4 radius; Λ0 represents SO2-4 conductivity; ω represents ionic Activity coefficient; c represents the concentration of sulfur SO2-4; A, B, C and D are parameters related to temperature, which can be expressed by Eq. (9):
where, e represents the elementary charge; ε0 represents the vacuum dielectric constant; εr represents the relative dielectric constant; η represents the viscosity of water.
The ion concentration in polypropylene fiber concrete can be calculated according to the theory of electrolyte solution:
where, N represents the number of types of ions; zi represents the valence of the i-th ion in the solution; ci represents the initial concentration of the ion in the solution.
2.2.3. Tortuosity of erosion path
According to the material composition, distribution state and geometric characteristics of polypropylene fiber concrete, the geometric model of the tortuosity of the erosion path can be express:
where, ηst and fst represent the shape factor and volume rate of the sand, respectively; ηsa and fsa represent the shape factor and volume rate of the crushed stone, respectively; τcp represents the tortuosity of the sulfate transmission path in the cement paste, which can be expressed by Eq. (12) express:
where, ωwc represents the adjustment coefficient; ηr represents the shape factor of the cement particles.
2.2.4. Concentration distribution
Assuming that the external sulfate ion concentration on both sides of polypropylene fiber concrete is C0, the diffusion reaction equation of SO2-4 can be solved according to a one-dimensional symmetry problem. By analyzing the distribution of SO2-4 in the concrete range of L/2, we can get the erosion of SO2-4 on the whole concrete, as shown in Fig. 3. According to the above analysis, the diffusion reaction equation of SO2-4 erosion polypropylene fiber concrete model can be established as follows:
By iterative solution of catch-up method, the concentration distribution of SO2-4 in concrete at any time can be obtained.
2.3. Method of specimen
In this experiment, P·O42.5 ordinary Portland cement and grade Ⅰ fly ash were used as cementing materials, and the replacement of fly ash was 20 %. Fine aggregate was made of continuously graded fine sand with particle size of 0-4.75 mm, fineness modulus of 2.68, apparent density of 2.64 g/cm3. Gravel is limestone gravel with continuous gradation of 5-20 mm in diameter. The water was ordinary drinking tap water with a water-cement ratio of 0.32. The fiber is polypropylene fiber (PF), and its physical and mechanical properties are shown in Table 1. Forming 100 mm×100 mm×400 mm concrete specimen.
Table 1Physical and mechanical properties of polypropylene fiber
Fiber type | Density (g/cm3) | Equivalent diameter (μm) | Tensile strength (MPa) | Elastic modulus (MPa) | Elongation at break (%) |
Fascicular monofilament | 0.91 | 21 | ≥ 400 | ≥ 3500 | 8-30 |
Erosion method: Put the polypropylene fiber concrete specimens (100 mm×l00 mm×400 mm) cured to the specified age into a 5 % Na2SO4 solution for long-term soaking. The long-term immersion test takes 30 d as a cycle, that is, take out the test block after soaking in Na2SO4 solution for 30 d, 60 d, 90 d, 120 d... And wipe the surface moisture of the test block with a rag. After natural air drying, drill core sampling, and the distribution of sampling drilling points is shown in Fig. 4.
Fig. 4Specimen sampling drilling point distribution diagram
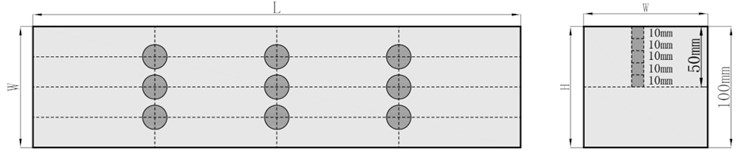
2.4. Comparison between experimental results and numerical simulation results
Fig. 5 shows the changes of theoretical and experimental values of SO2-4 concentration at different depths (0 mm, 10 mm, 20 mm, 30 mm, 40 mm and 50 mm) in concrete specimens soaked with 5 % sodium sulfate solution for 0 d, 30 d, 60 d, 90 d, 120 d and 150 d respectively.
Fig. 5Relative error statistics of simulation results and the test results (%)
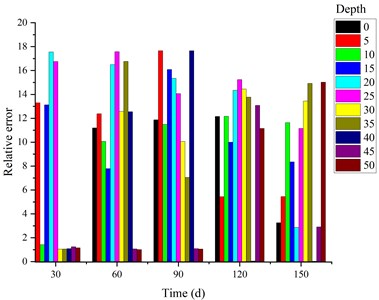
It can be seen from Fig. 5 that the maximum relative difference between the theoretical calculation results and the test results shall not exceed 17.65 %. However, in the period of 0 d-90 d, the theoretical calculation value increases more significantly than the measured value. The error between the two groups of data is concentrated between 12.38 %-17.65 %, and the error is relatively large, indicating that the diffusion speed of erosion ions is relatively fast in the theoretical model calculation; In the period of 90 d ~ 150 d, the theoretical calculated values tend to be consistent with the measured values. The relative error between the two groups of data is concentrated between 10.00 %-15.24 %, and the error gradually decreases, indicating that the erosion ions diffusion reaction reaches a relatively stable state during this period, and the actual test is less affected by the external test conditions.
3. Conclusions
1) Based on the spatial distribution characteristics of polypropylene fiber in concrete, the spatial distribution of polypropylene fiber is divided into through type, half-through type and embedded type. The porosity of three types of polypropylene fiber is calculated respectively, and the initial porosity and filling porosity of polypropylene fiber concrete are calculated respectively according to the process of sulfate eroding concrete structures.
2) Based on Fick’s second law and reaction kinetics theory, the diffusion model of SO2-4 in polypropylene fiber concrete is established. The finite difference method is used to realize the numerical solution, the sulfate erosion migration law in polypropylene fiber concrete is studied, and the numerical solution of SO2-4 concentration at any position (Xi,Tj) is realized.
3) In this paper, the sulfate erosion test of polypropylene fiber reinforced concrete is designed, and the sulfate ion concentration of the specimen at different time and depth under the erosion condition of 5 % sodium sulfate solution is quantitatively measured, which is compared with the theoretical calculation value of the established sulfate erosion model of polypropylene fiber reinforced concrete. The results show that the relative error between the model calculation results and the actual test results is less than 17.65 %, and the accuracy is high.
References
-
Q. Song, J. Nie, D. Wu, Y. Hu, and Y. Chen, “Effect of SO42−, Cl− and Mg2+ on the system of C-S-H and Ca(OH)2,” Construction and Building Materials, Vol. 285, p. 122955, May 2021, https://doi.org/10.1016/j.conbuildmat.2021.122955
-
X. Qiao and J. Chen, “Correlation of propagation rate of corrosive crack in concrete under sulfate attack and growth rate of delayed ettringite,” Engineering Fracture Mechanics, Vol. 209, pp. 333–343, Mar. 2019, https://doi.org/10.1016/j.engfracmech.2019.01.036
-
B. Ali, S. S. Raza, I. Hussain, and M. Iqbal, “Influence of different fibers on mechanical and durability performance of concrete with silica fume,” Structural Concrete, Vol. 22, No. 1, pp. 318–333, Feb. 2021, https://doi.org/10.1002/suco.201900422
-
M. R. Latifi, Biricik, and A. Mardani Aghabaglou, “Effect of the addition of polypropylene fiber on concrete properties,” Journal of Adhesion Science and Technology, Vol. 36, No. 4, pp. 345–369, Feb. 2022, https://doi.org/10.1080/01694243.2021.1922221
-
X. B. Zuo, “Modeling ion diffusion-reaction behavior in concrete associated with durability deterioration subjected to couplings of environmental and mechanical loadings,” Nanjing, School of Materials Science and Engineering, Southeast University, 2011.
-
E. Samson, J. Marchand, J. L. Robert, and J. P. Bournazel, “Modelling ion diffusion mechanisms in porous media,” International Journal of Numerical Methods in Engineering, Vol. 46, No. 12, pp. 2043–2060, 1999, https://doi.org/10.1002/(sici)1097-0207(19991230)46:12
-
A. Chandra and B. Bagchi, “Ion conductance in electrolyte solutions,” The Journal of Chemical Physics, Vol. 110, No. 20, pp. 10024–10034, May 1999, https://doi.org/10.1063/1.478876
-
W. Sun and C. Yu, “Modeling of ion diffusion coefficient in saturated concrete,” Computers and Concrete, Vol. 7, No. 5, pp. 421–435, Oct. 2010, https://doi.org/10.12989/cac.2010.7.5.421
About this article
The research was supported by the Transportation Science and Technology Project in Shaanxi Province (Nos. 20-16 K), the Key R&D Program in Shaanxi Province (No. 2019GY-422).