Abstract
This paper aims to study the temperature control of mass concrete, and to understand concrete pouring of hydration heat temperature field and temperature stress distribution. The influence of relevant parameters on reducing the temperature difference between inside and outside and the concrete temperature control and crack resistance measures are put forward. Taking Fuma Yangtze River Bridge as the engineering background, the combining of engineering measurement, theoretical calculation, and ANSYS numerical simulation is adopted. Results show that the use of ANSYS simulation for the mass concrete casting process is feasible. Furthermore, it is concluded that the cracks of mass concrete are prone to appear at the corner of the surface, and the influences of t input temperature, mixing ratio on reducing the internal and external temperature difference are also studied.
1. Introduction
Mass concrete has the characteristics of large size and a large amount of cement [1]. When the temperature stress generated in the concrete structure is greater than the ultimate tensile strength of the concrete, cracks will occur, which will seriously affect the safety and durability of the concrete structure [2, 3].
Sharma [4] has tested the temperature effect on a square plate. Zhu [5] proposed a complete theory of temperature control based on this and solved a series of problems during the construction and operation of mass concrete structures. Later, Chen [6] improved the high-speed solution method for the mass concrete temperature field. Lin [7] revealed the evolution law of the real temperature field of mass concrete through water cooling through field tests. Wang [8] used ANSYS to study the temperature field of mass concrete with circulating cooling water pipes. Tahersima and Tikalsky [9] used the finite element program to analyze the temperature stress of mass concrete in a concrete slab-on-grade floor. Recently, Cha and Jin [10] proposed a method to predict thermal stresses in mass concrete structures by the, which was based on experimental and analytical results. However, at present, the research results on the temperature stress field and temperature control measures of mass concrete are mainly concentrated in hydraulic structures or dam bodies, and the results related to bridge structures are relatively limited.
2. Project overview
The Fuma Yangtze River Bridge is an important controlling project for the Chongqing Wanzhou to Hubei Lichuan Expressway. The bridge site is located in Wanzhou District, Chongqing City. The main bridge layout is 300+1050+300 meters and the total length is 2030 meters, which is the largest span suspension bridge in the Three Gorges Reservoir area. The plane size of the gravity anchorage on the north side is 79×48 m in length by width and 52 m in height. It is mainly composed of a splay saddle buttress and foundation, anchor block, and front anchor room. The anchor block and splay saddle buttress are large volume impermeable concrete structures.
3. Simulation analysis of mass concrete pouring process
In this paper, the ANSYS indirect coupling method is used to model and analyze the foundation of the splay cable saddle of the Fuma Yangtze River Bridge. The size of the foundation in the model is 50 m×4 m×41 m, and the size of the first layer of the buttress foundation is 34 m×4 m×23 m. According to construction requirements and initial and boundary conditions, the thermal element is proposed. Using mapped meshing, the model after meshing is shown in Fig. 1.
Fig. 1Finite element meshing of buttress foundation
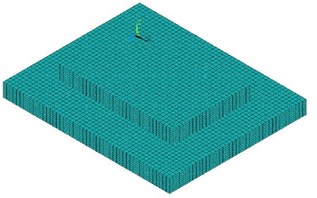
3.1. Simulation analysis of temperature field
According to the actual pouring situation of concrete, combined with external conditions such as temperature and soil, ANSYS was used to simulate the temperature field of the buttress foundation from the beginning of pouring to the end of the hydration heat release, and the temperature change results obtained by numerical simulation are compared with the measured and calculated values, and the results are shown in Fig. 2.
Fig. 2Temperature comparison
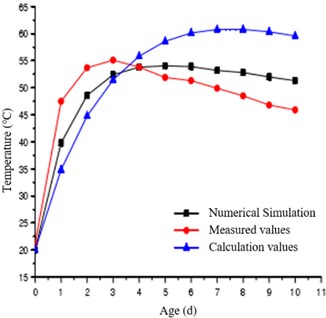
a) Comparison of Middle layer temperature
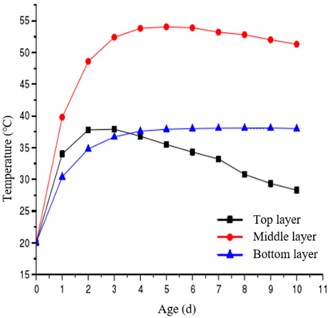
b) Comparison of numerical simulation results
In general, the numerical results, measured values, and calculation values have relatively consistent trends with age. It is feasible to simulate the pouring process of mass concrete by ANSYS finite element software, especially the results of numerical simulation of the middle layer, which are very close to the measured values. In practice, the cooling water pipe is used to cool down the concrete and the external concrete is properly insulated and maintained, which can further reduce the temperature difference between the inside and outside of the mass concrete. The heat transfer between the bottom of the buttress and the foundation is more complicated, and the simulation accuracy needs to be further improved.
3.2. Simulation analysis of stress field
Based on ANSYS temperature field analysis, re-enter the pre-processor, convert the temperature field analysis element SOLID70 to the stress field analysis element SOLID45, and the result of the temperature field analysis is applied as a load to the structural analysis model to obtain the stress field analysis. The results are shown in Fig. 3.
It can be found from Fig. 3 that the tensile stress at the corner points is relatively large. This shows that mass concrete cracks are most likely to occur at the corners of the surface, mainly because the surface of the concrete is in direct contact with the external atmosphere, dissipating heat faster, and forming a larger temperature gradient with the higher internal temperature, so tensile stress zone appears on the surface, cracks are generated on the surface. In addition, the corners of the surface are less constrained by the bedrock, so cracks are most likely to appear at the corners of the surface.
Fig. 3Stress cloud diagram of buttress foundation
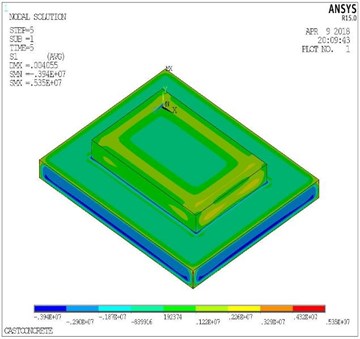
a) Stress nephogram on the 5th day
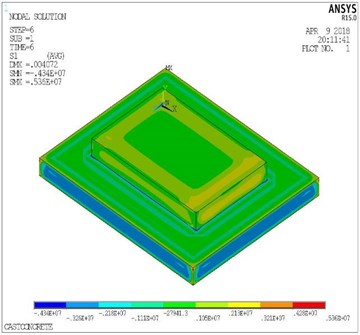
b) Stress nephogram on the 6th day
3.3. Simulation analysis of pouring process under different working conditions
3.3.1. Simulation analysis of different entry temperatures
Setting the different mold entry temperatures to 15 °C and 25 °C, and other parameters remain unchanged. Compare with the actual mold entry temperature of 20 °C. The temperature change is shown in Fig. 4.
Fig. 4Comparison of the temperature difference between the inside and outside of the middle layer and the top layer
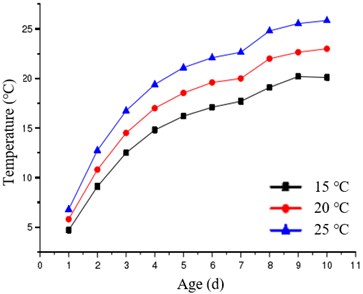
It can be seen from Fig. 4 that with the increase of the mold entry temperature, the temperature of the middle layer, the top layer, and the bottom layer of the mass concrete also increase correspondingly, and the temperature difference between the inside and outside of the middle layer and the top layer also increases. When the molding temperature is 25 °C, the temperature difference between inside and outside is greater than 25 °C on the 8th day. In addition, when the mold entry temperature is 25 °C, the top layer temperature of the buttress foundation drops by 2.2 °C, exceeding 2 °C/d after the mold is removed on the 7th day. Therefore, it is an efficient method to control the temperature of mass anchorage concrete by controlling the mold-in temperature reasonably.
3.3.2. Simulation analysis of different mix ratios
The adiabatic temperature rise mainly depends on the heat release of cement hydration. Therefore, the different cement content of each cubic concrete is 310 kg (78 kg of fly ash, of which the cement content is 80 %) and 388 kg (without fly ash), and the actual use (233 kg of cement, 155 kg of fly ash, of which the cement content is 60 %) The temperature changes of each layer of the buttress foundation are compared to obtain a reasonable cement content, as shown in Fig. 5.
Fig. 5Comparison of the temperature difference between the inside and outside of the middle layer and the top layer
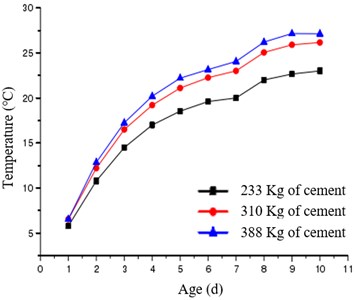
It can be seen from Fig. 5 that when the cement content per cubic meter of concrete increases from 233 kg to 310 kg, the maximum temperature of the middle layer of the buttress foundation in the first 10 days has increased by 5.3 ℃, and the maximum temperature difference between the middle layer and the top layer also increases by 3.2 ℃; when the cement content per cubic meter of concrete increases from 310 kg to 388 kg, the maximum temperature of the middle layer of the buttress foundation in the first 10 days increases by 2.1 ℃, the maximum temperature difference between the inside and outside of the middle layer and the top layer has increased by 1 ℃; this indicates that the fly ash in the cementing material in the mass concrete should be added in an appropriate amount, and the addition should not be too small, otherwise the effect of reducing the heat of hydration will not be obvious.
4. Conclusions
At present, most of the researches on the temperature control of mass concrete were concentrated in hydraulic structures or dam bodies, while those related to bridge structures are relatively limited. Based on the Fuma Yangtze River Bridge, this paper compares the numerical simulation values, the measured values, and the theoretical calculation values for the foundation of the anchor buttress piers, and simulated the working conditions of different parameters. The main conclusions are as follow:
1) Through the simulation analysis of the stress field, it is found that the tensile stress at the corners of the concrete of the early buttress foundation is relatively large, while the ultimate tensile strength of the concrete is small, as a result, the cracks are easier to appear at the corners of the surface.
2) With the increase of the molding temperature, the increase of the cement content in the concrete mix, the higher the internal and external temperature of the mass concrete, the greater the temperature difference between the internal and external, therefore the more unfavorable for temperature control and cracking resistance.
References
-
Dainora Jankauskiene, Viktoras Dorosevas, Vitalijus Volkovas The crack analysis in monitoring procedures of Seaport pier concrete constructions. Journal of Measurements in Engineering, Vol. 6, Issue 1, 2018, p. 74-80.
-
Wu Bo, Yang, Yang, Zhang Liangliang, Wang, Yuancha, Li Haohong Meso-scale numerical study on the non-uniform corrosion-induced cracking of confined concrete. Construction and Building Materials, Vol. 260, 2020, p. 120463.
-
Mohammad Shooshtari, Hamid Mortezaie Effect of using linear multiple tuned mass dampers on concrete structures with hysteresis behavior. Journal of Vibroengineering, Vol. 19, Issue 2, 2017, p. 1158-1172.
-
Amit Sharma Free vibration of square plate with temperature effect. Journal of Measurements in Engineering, Vol. 5, Issue 4, 2017, p. 222-228.
-
Zhu Bofang Temperature Stress and Temperature Control of Hydraulic Concrete Structure. Water Resources and Electric Power Press, 1976.
-
Chen Guorong, Li Huangsheng, Li Hongjian Improvement of fast solution method for mass concrete temperature fields. Journal of Hohai University (Natural Sciences), Vol. 37, Issue 4, 2009, p. 396-399.
-
Lin Peng, Hu Hang, Zheng Dong, Li Qingbin Field tests on the evolution of a real thermal field in concrete. Journal of Tsinghua University (Science and Technology), Vol. 55, Issue 1, 2015, p. 27-32.
-
Wang Jiejun, Li Hui, Lu Erxia Numerical analysis of hydrated heat temperature field of massive volume concrete pier. Journal of Central South University of Forestry and Technology (Natural Science), Vol. 27, Issue 1, 2007, p. 124-128.
-
Mohammad Tahersim, Paul Tikalsky Finite element modeling of hydration heat in a concrete slab-on-grade floor with limestone blended cement. Construction and Building Materials, Vol. 154, 2017, p. 44-50.
-
Cha Sang-Lyu, Jin Seung-Seop Prediction of thermal stresses in mass concrete structures with experimental and analytical results. Construction and Building Materials, Vol 258, 2020, p. 120367.
Cited by
About this article
This research was funded by the Science and Technology Research Program of Chongqing Municipal Education Commission (Grant No. KJZD-K201905201).