Abstract
This paper describes an Artificial Neural Network (ANN) based fault diagnosis methodology for Induction Motors (IM) operating under the same conditions for various speeds and loads. In this study, ten different IM fault conditions are considered. We considered five mechanical faults (bearing fault, unbalanced rotor, misaligned rotor, bowed rotor, rotor with broken bar), four electrical faults (phase unbalance fault with two levels of severity, stator winding fault with two levels of severity), and one healthy motor condition. The current and vibration signals were considered in this work as these signals are generally considered to be the most efficient for the detection of mechanical and electrical faults in IM when used simultaneously. A machine fault simulator was used for the generation of vibration and current signals from different fault conditions. An ANN model was developed in which raw time domain vibration (in three directions) as well as current (in three phases) data are used simultaneously as input and then the fault diagnosis (training and testing) is performed. In this work, the fault diagnosis was attempted when testing was done for the same operating conditions as training. The developed fault diagnosis methods were found to be robust for various operating conditions (speeds and loads) of the IM.
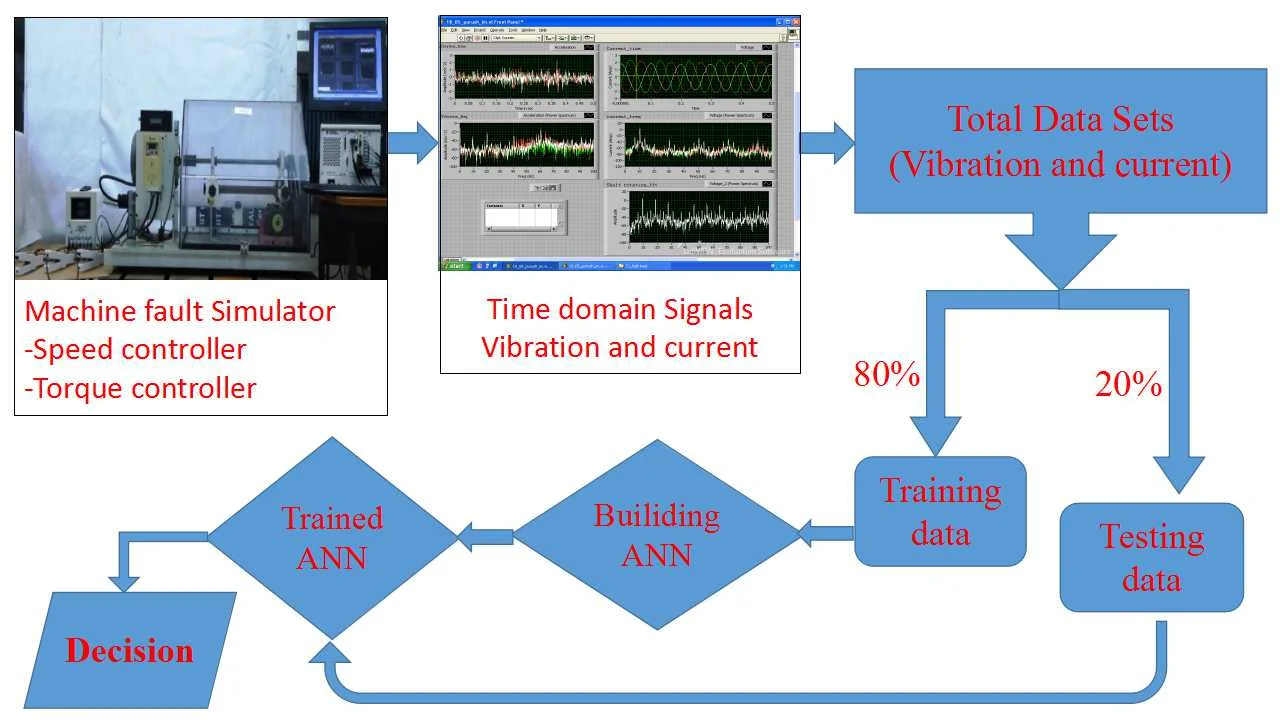
Highlights
- Diagnosis of simultaneous ten different induction motor (IM) fault conditions (mechanical and electrical faults with different severity levels)
- Vibration and Current based multiclass induction motor fault diagnosis
- Artificial neural network based IM fault diagnosis
- Robustness of the Artificial intelligence based fault diagnosis for various operating condition (Speed and Load)
1. Introduction
Induction motors (IMs) are most often utilized in different types of commercial applications such as machine tools, petrochemicals facilities, textile mills, power plants, and farming. As they are simple in mechanical design, robust, low cost and adaptable for a wide variety of applications they are most common. In modern manufacturing and transportation applications, induction machines play a significant role. Failure can result in large losses. Hence, the system of failure detection is important for proper prevention of operation downtime and repair [1, 2].
Many research results on the identification of mechanical defects in induction motor have been published. Nonetheless, the probability of IM failure is nearly 50 % because of mechanical failure such as faults in bearings, rotor unbalance faults, bowed and misaligned rotor. Many non-invasive condition monitoring techniques which depend on voltage, current, acoustic, angular velocity and vibration have been used for failure detection. Thomson and Orpin [3] demonstrate the advantages of using an integrated monitoring strategy via vibration and current analysis to diagnose faults and establish the root cause of problems. In electrical drive systems it is better to simultaneously analyse electrical and mechanical signals such as vibration and current, and in high-voltage motors (4.16 kV and above) partial discharges should also be monitored to ascertain the health of the stator winding. Many articles have been presented on diagnosis of induction motor faults using vibration and current signals but only deal with one fault at a time.
Alsaedi [4] showed that the use of condition monitoring of electrical machines is increasing due to its potential to reduce operating costs, enhance the reliability of operation and improve service to customers. Different alternatives to detect and diagnose faults in induction machines have been proposed and implemented in recent years. In a study, Bhavsar et al., [5] worked on stator fault detection in IM using ANN. They stated that when there is a fault in a motor the stator current becomes unbalanced. To train the neural network sixteen different parameters are used. According to them ANN provides the best results with ten hidden layers. Hamdani et al., [6] proposed a multilayer feed forward neural network to detect rotor defects such as bar breakage and dynamic eccentricity on a 3-phase induction motor. The accuracy depended on ANN structure. However, increasing the neurons performance did not improve the overall performance. Noor Al-Deen et al., [7] investigated two important types of mechanical faults and their diagnostic procedure, namely unbalance and misalignment. Various factors like load condition, unbalanced power supply and saturation effects will affect the speed and accuracy of failure detection.
In the continuation of the AI based research work on IM fault diagnosis, Gangsar and Tiwari [8-10] have successfully attempted the diagnosis based on Support Vector Machine. They have considered time, frequency as well as wavelet analysis for the diagnosis of mechanical and electrical faults of IM. In paper [10], they have shown the importance of diagnosis for limited operating conditions. In a study, Hsu and Lin [11] discussed the multiclass methods of SVM methods like one-against all (OAA), one-against-one (OAO) and direct-acyclical (DAG) and showed that the OAO and DAG are better for practical applications like fault diagnosis. Zhongming and Bin [12] suggested an ANN based approach for induction motor bearing fault diagnosis based on time, frequency and time-frequency domain analysis. Jigyasu et al., [13] presented a comparison of current and vibration based diagnosis using artificial neural networks for different types of motor failures such as bearings, stators, rotors and eccentricity. Nejjari and Benbouzid [14] proposed an IM fault diagnosis method based on the Park Vector Approach. In this work, the current Park Stator Vector patterns are first identified using ANN, and then successfully used to distinguish between “sound” and “wrong” induction machines. In another study, Li and Mechefske [15] presented the comparison of induction motor fault detection using stator current, vibration, and acoustic methods. They concluded that the stator current method is sensitive to the broken rotor bar fault while the vibration method is sensitive to bearing faults. The acoustic method is attractive in that it contains less noise and interference within the analyzing frequency band. With the proper selection of monitoring and analysis methods, induction motor faults can be detected accurately under both stationary and non-stationary states.
After reviewing a number of papers on AI based fault diagnostics of IM, it was found that most of the researchers considered a maximum of two to three IM faults simultaneously for the detection. However, it is important to build a diagnostic scheme that can detect all the possible electrical and mechanical defects simultaneously. In addition, the reliability of AI based fault detection of the IM remains a challenging task. The AI based diagnosis may or may not be effective at all the operating conditions of the motors because it is totally dependent on the data available for testing/classification. Therefore, it is crucial to check the robustness of the fault diagnosis for various motor operating conditions. In this work, the ANN based IM fault diagnosis is developed for diagnosing mechanical and electrical faults as well as their severity simultaneously for similar operating conditions. In addition, the robustness of the developed methodology has also been checked for various operating conditions (i.e. speed and load) of the IM which is one of the critical things in any AI based fault diagnosis.
2. Introduction to artificial neural network
One of the main tools used in machine learning is the artificial neural network. These are brain inspired systems, as the “neural” part of their name suggests, which aims to simulate the way people learn. Neural networks consist of input and output layers and (in most cases) a hidden layer of units that convert the inputs into something that the output layer can use. These are excellent tools for identifying complex patterns.
In the past few decades, ANN has become an important part of artificial intelligence. This is due to the arrival of a technique called “posterior diffusion”, which allows networks to adjust their hidden layers of neurons in cases where the result is not what the creator hoped for.
Fig. 1 shows various layers used in ANN. The figure above includes three yellow circles. Which represent the layer of input and are generally referred to as vector X. The hidden layers are represented by four blue and four green circles. These circles represent activity nodes. The purple circle is either the output layer or expected value (or values for multiple classes/output types). Each node is attached to the next layer node and each connection (black arrow) has a specific weight. The weight can be considered as the effect of this node on the next layer node. From Fig. 1, it is observed that all nodes from the previous (yellow) layer are associated with the blue color nodes. All of these links represent weights (effect). When all the values of the yellow nodes are multiplied by their weight and everything is summarized, this gives a certain value to the higher blue node. The blue node has a predefined “activation” function that determines whether a “node” will be activated or how it will be “active”, depending on the summarized value. The additional knot of value 1 is called the “bias” node.
Fig. 1Artificial neural network
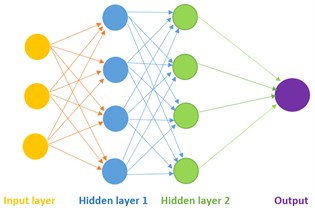
Fig. 2MFS experimental setup
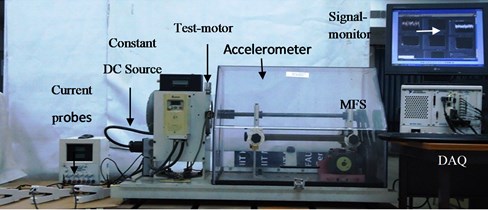
3. Experimental setup and data processing
Experiments have been performed on a MFS (machine fault simulator). Fig. 2 shows a three-phase induction motor (0.5 HP) mounted on the shaft by means of a flexible coupling in the MFS experimental configuration. This configuration enables the study of IM errors by installing defective motors on the MFS, then generates its current and vibration signature. In a total of ten different IM states considered here, i.e., No defect (ND), bearing fault (BF), unbalanced rotor (URF), Bowed Rotor (BRF), Misaligned Rotor (RMF), broken rotor fault (BRBF), two severities of stator winding faults (SWF and MSWF) and two severities of phase unbalance (PUF and MPUF).
For all faulty IM conditions, vibrations (in three directions) and current data (in three stages) are recorded. The data are generated at seven different speeds (10 Hz, 15 Hz, 20 Hz, 25 Hz, 30 Hz, 35 Hz, and 40 Hz) and two torque levels ( no load-0 N-m, i.e. 0 % of rated torque (T1); the high load- 0.565 N-m, i.e. 0.55 % of rated torque (T2)) of IMs. The experiment was performed with the sampling rate of 1000 S/s and 10000 sample points in order to maintain the higher resolution of data, i.e. 0.1 Hz and capture lower frequencies with more accuracy. In total 25 raw data sets (10000 sample points per data set) were generated in the time domain in 250 seconds.
4. ANN based fault diagnosis
The multi-class induction motor fault diagnosis is performed after obtaining the necessary data sets from raw time domain data with the help of the ANN classifier. The flow chart of the methodology is shown in Fig. 3. For performing the fault diagnosis, the total number of standard data sets is split into two classes of training and test data i.e., in respective proportions of 80 % and 20 %. An ANN model is created and then trained using 80 % of the data extracted from the experiments. Using the test data sets (remaining 20 % data), this model was used to predict the faults. Fault diagnosis is obtained from test data for frequencies ranging from 10 Hz to 40 Hz at 5 Hz intervals and for all the two load conditions. It also shows the individual accuracy of the fault classification of all the ten faults with their class labels.
In this study, the fault diagnosis is considered when training and testing are done at the same speed and at the same load. To analyse the robustness of the diagnosis, fourteen distinct operating conditions of IM are considered in this work (shown below in the Table 2). For the diagnosis of IM faults (mechanical and electrical faults), an ANN model is developed where training and tests are performed with 80 % data and 20 % data, respectively. The results are shown in Fig. 4, and Table 2. The training and testing accuracy are plotted with the IM speeds for T1 and T2 load in Fig. 4(a) and 4(b), respectively. From these figure it can be observed that the training and testing accuracy are found to be nearby at each operating condition of the IM. Therefore, it can be noted that there is no case of over fitting and under fitting in the developed ANN model. Or in other words, the developed ANN model is accurate with the current raw time domain data (vibration and current) as input features. The flow chart of fault diagnosis is shown below:
Fig. 3Flow chart of multiclass fault diagnosis based on ANN
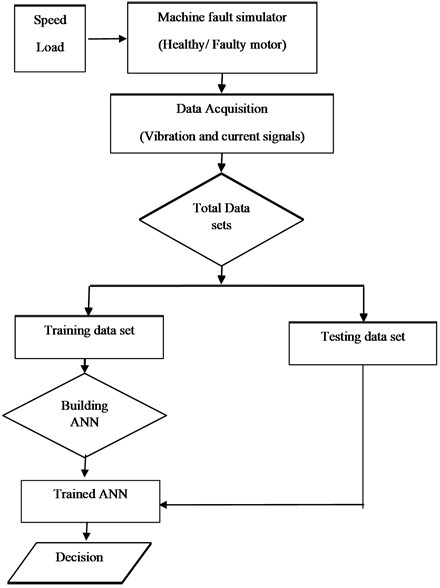
Fig. 4a) Training and testing accuracy with speeds at T1 load, b) training and testing accuracy with speeds at T2 load
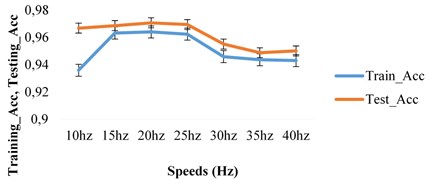
a)
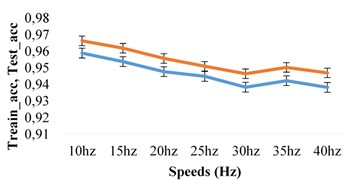
b)
The results of the diagnosis are tabulated in the Table 1 which shows the individual and overall accuracy for all fourteen operating conditions. It can be observed that, for no load condition or load T1, the overall prediction accuracy is approximately 96 % for all Speeds except 35 Hz for which it is 94 % and at load T2 it is 95 % for all speeds except for 40 Hz for which it is 94 %.
It can be seen that from the table for load T1 that URF has the maximum Individual prediction accuracy and RMF has minimum Individual prediction accuracy. For load T2 overall prediction accuracy is approximately 95 % for all speeds. The overall accuracies are found to be the same as for the T1 load case. From here it can be concluded that the ANN based fault diagnosis of induction motors do not depend on the motor speeds nor loads. Hence, the fault diagnosis of induction motors can be performed at any operating conditions of the motor.
Table 1Fault diagnosis in same speed and load situation
Train speed (Hz) | Test speed (Hz) | Individual accuracy, % | Acc. % | |||||||||
ND | BF | BRB | BRF | URF | RMF | SWF-1 | SWF-2 | PUF-1 | PUF-2 | |||
For load T1 | ||||||||||||
10 | 10 | 82 | 94 | 88 | 88 | 99 | 65 | 83 | 98 | 92 | 89 | 96 |
15 | 15 | 68 | 92 | 76 | 85 | 99 | 61 | 94 | 92 | 91 | 83 | 96 |
20 | 20 | 82 | 99 | 72 | 86 | 97 | 58 | 90 | 92 | 89 | 90 | 96 |
25 | 25 | 66 | 92 | 73 | 83 | 97 | 72 | 87 | 94 | 86 | 83 | 96 |
30 | 30 | 69 | 81 | 59 | 72 | 97 | 54 | 92 | 88 | 91 | 69 | 96 |
35 | 35 | 53 | 90 | 72 | 73 | 96 | 52 | 67 | 86 | 89 | 68 | 94 |
40 | 40 | 65 | 95 | 65 | 69 | 97 | 55 | 74 | 80 | 86 | 64 | 96 |
For load T2 | ||||||||||||
10 | 10 | 81 | 81 | 81 | 77 | 96 | 66 | 82 | 92 | 86 | 92 | 95 |
15 | 15 | 79 | 93 | 70 | 71 | 85 | 67 | 86 | 91 | 88 | 81 | 95 |
20 | 20 | 67 | 95 | 84 | 63 | 87 | 59 | 71 | 88 | 87 | 84 | 95 |
25 | 25 | 70 | 92 | 71 | 61 | 76 | 67 | 82 | 67 | 88 | 75 | 95 |
30 | 30 | 58 | 88 | 61 | 62 | 77 | 58 | 68 | 80 | 91 | 83 | 95 |
35 | 35 | 62 | 90 | 76 | 65 | 93 | 69 | 61 | 73 | 80 | 75 | 95 |
40 | 40 | 66 | 90 | 66 | 67 | 94 | 65 | 54 | 64 | 81 | 72 | 94 |
5. Conclusions
ANN-based fault diagnosis is developed for IM for various operating conditions (seven speeds and two loads). Raw vibration data in the time domain (three directions) and current (three phases) are used as characteristics. Based on the raw time domain vibrations and current data, the ANN-based diagnosis of mechanical and electrical failures of IM is effective. The fault detection developed for the same speed and the same load cases is effective (the accuracy for the same speed and the same condition of load is close to about 96 %). In addition, the developed model is capable of effectively detecting different levels of severity of the same defect, namely MSWF and SWF, MPUF and PUF. The diagnosis based on the feed forward-ANN proves effective for all the operating conditions considered of the IM. This means that the diagnosis developed is reliable regardless of the IM operating conditions. In future, the fault diagnosis will be attempted based on deep learning and compared the results with the present study. In addition, the ANN fault diagnosis will be attempted for limited operating conditions cases, where data are not available for each speed and load of interest.
References
-
Henao H., Capolino G. A., Fernandez Cabanas M., Filippetti F., Bruzzese C., Strangas E., Hedayati Kia S. Trends in fault diagnosis for electrical machines: a review of diagnostic techniques. Industrial Electronics Magazine, Vol. 8, Issue 2, 2014, p. 31-42.
-
Bazzi A. M., Krein P. T. Review of methods for real-time loss minimization in induction machines. IEEE Transactions on Industry Applications, Vol. 46, Issue 6, 2010, p. 2319-2328.
-
Thomson W. T., Orpin P. Current and vibration monitoring for fault diagnosis and root cause analysis of induction motor drives. Proceedings of the 31st Turbomachinery Symposium, 2002.
-
Alsaedi M. A. Fault diagnosis of three-phase induction motor: a review. Optics, Special Issue: Applied Optics and Signal Processing, Vol. 4, Issue 1, 2015, p. 1-8.
-
Bhavsar R. C., Patel R. A., Bhalja B. R. Condition monitoring of induction motor using artificial neural network. Annual International Conference on Emerging Research Areas: Magnetics, Machines and Drives, 2014.
-
Hamdani S., Touhami O., Ibtiouen R., Fadel M. Neural network technique for induction motor rotor faults classification-dynamic eccentricity and broken bar faults. 8th IEEE Symposium on Diagnostics for Electrical Machines, Power Electronics and Drives, 2011.
-
Al Deen K.-N., Hummes D., Fruth B., Caironi C., Ghaffar A. A., Karas M. Signature analysis as a medium for faults detection in induction motors. International Conference on Computing Sciences and Engineering, 2018.
-
Gangsar P., Tiwari R. Comparative investigation of vibration and current monitoring for prediction of mechanical and electrical faults in induction motor based on multiclass-support vector machine algorithms. Mechanical Systems and Signal Processing, Vol. 94, 2017, p. 464-481.
-
Gangsar P., Tiwari R. Taxonomy of induction-motor mechanical-fault based on time-domain vibration signals by multiclass SVM classifiers. Intelligent Industrial Systems, Vol. 2, Issue 3, 2016, p. 269-281.
-
Gangsar P., Tiwari R. Multifault diagnosis of induction motor at intermediate operating conditions using wavelet packet transform and support vector machine. Journal of Dynamic Systems, Measurement, and Control, Vol. 140, Issue 8, 2018, p. 081014.
-
Hsu C. W., Chang C. C., Lin C. J. A Practical Guide to Support Vector Classification, 2003.
-
Zhongming Y., Bin W. A review on induction motor online fault diagnosis. Proceedings IPEMC, 3rd International Power Electronics and Motion Control Conference, Vol. 3, 2000, p. 1353-1358.
-
Jigyasu R., Mathew L., Sharma A. Multiple faults diagnosis of induction motor using artificial neural network. International Conference on Advanced Informatics for Computing Research, 2018.
-
Nejjari H., Benbouzid M. E. H. Monitoring and diagnosis of induction motors electrical faults using a current Park’s vector pattern learning approach. IEEE Transactions on Industry Applications, Vol. 36, Issue 3, 2000, p. 730-735.
-
Li W., Mechefske C. K. Detection of induction motor faults: a comparison of stator current, vibration and acoustic methods. Journal of Vibration and Control, Vol. 12, Issue 2, 2006, p. 165-188.
Cited by
About this article
The experimental data have been acquired at Noise and Vibration laboratory in IIT Guwahati, India. We are very thankful to IIT Guwahati, India.