Abstract
Compression garbage trucks mainly work on fresh municipal solid waste (MSW), while fresh MSW has complex composition, high compressibility, high water content. Less research has been done about fresh MSW. Its uncertain mechanical property limits the simulation of garbage compression process, thereby limits the compressor structure analysis and optimization for compression garbage trucks. In order to obtain the mechanical properties of fresh MSW, a special test device combining the direct shear test with the confined compression test was designed, manufactured and assembled. A total fifteen tests from four batches fresh MSW were conducted with the special test devices. And the Duncan-Chang constitutive model parameters by summarizing and organizing test data. Finally, the confined compression test was simulated with the constitutive model, and the constitutive model parameters was verified. The research provides a basis for the simulation of garbage compression process of the compression garbage truck.
1. Introduction
China’s urban waste production was increasing at an annual rate of 8 % to 10 % in recent years. Finding a proper way to dispose of municipal solid waste has become an urgent problem for urban development [1]. Driven by national policy and rigid demand, total amount of the sanitation market will maintain a rapid growth of more than 20 % in the next five years. And with the improvement of people's awareness of energy conservation and environmental protection, compression garbage trucks with hermetic, self-compression and large loading capacity are more and more accepted by the public, and their occupation rate in garbage trucks will increase gradually.
Fresh MSW consists of many different components, including waste paper, vegetables, peels, wood, grass, leaves, textiles, bones, plastics, rubber, metal, brick, stone, earth, ceramics, glass, and so on. In addition, the water content is also very large. These ingredients are usually porous and unsaturated, which have a significant impact on the engineering properties of domestic waste [2, 3]. Zhang et al. [4] conducted a combined compression and direct shear test on fresh domestic waste, and studied its strength characteristics under different compressive strains systematically. Zhang [5] used the unidirectional compression test and the direct shear test results to propose a simplified calculation method for the Duncan-Chang model parameter of the garbage, and obtained the Duncan-Chang model parameter of the garbage.
The main working object of compression garbage trucks is fresh MSW. Peng Xuan et al. [6] used Zhang’s Duncan-Chang model parameters of landfill waste [5] to analyze the structure of garbage compression vehicles. In order to improve the performance and optimize structure of compression garbage trucks, it’s indispensable to simulate the compression device [7]. However, it is very difficult to implemented due to the uncertainty of the mechanical properties of the garbage.
Therefore, it is urgent to carry out experimental research to obtain actual mechanical properties of fresh MSW, and provide a basis for the design technology of compression garbage trucks and other waste processing equipment. Duncan-Chang model was chosen as constitutive model of fresh MSW, and a special test device was designed, manufactured and assembled to conduct tests of fresh MSW. The parameters of Duncan-Chang constitutive model were achieved by data processing. Last, garbage compression process was simulated with the Duncan-Chang constitutive model.
2. Duncan-Chang model and test devices
2.1. Duncan-Chang E-μ constitutive model
Until now, domestic and international scholars proposed countless soil constitutive models, and the Duncan-Chang model is one of them. In the conventional triaxial test, the axial stress σ1 is applied when the σ3 is unchanged. At this time, the stress increment is applied in only one direction, and the stress increments of the other directions are unchanged. The Duncan-Chang model starts from this point [8]. The model is a nonlinear elastic model based on the incremental generalized Hooke’s law. It can reflect the nonlinearity of the stress-strain relationship with only 8 parameters, and every parameter has clear physical meaning, so it’s easy to grasp. It can be determined by static triaxial test, and is easy to be used in numerical calculation, therefore, it has been used widely [9, 10].
Fig. 1The relation between σ1-σ3 and ε1
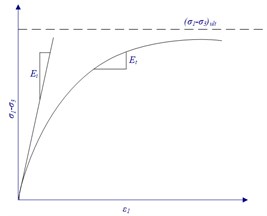
Fig. 2The relation of ε1 and ε3
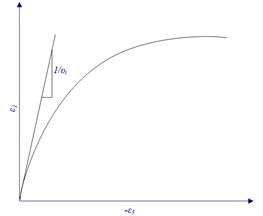
The relationship between σ1-σ3 and axial strain ε1 can be represented with a hyperbola, as shown in Fig. 1. The relationship between axial strain ε1 and the confined strain ε3 can also be represented with a hyperbola, as shown in Fig. 2.
The tangent elastic modulus Et at any stress (σ1,σ3) is shown in Eq. (1) [8]:
where, initial tangent elastic modulus Ei=Kpa(σ3/pa)n; K is coefficient of elastic modulus; n is exponent of elastic modulus; pa is atmospheric pressure; σ3 is minor principal stress or confining pressure; c is cohesion; φ is internal friction angle; Rf is damage ratio.
The tangent Poisson’s ratio μt at any stress (σ1, σ3) is shown in Eq. (2):
where, initial Poisson’s ratio μi=G-Flg(σ3/pa), G, F and D are the undetermined parameters of the initial Poisson’s ratio.
To summarize, the eight parameters of Duncan-Chang constitutive model are cohesion c, internal friction angle φ, damage ratio Rf, elastic modulus coefficient K, elastic modulus exponent n, undetermined parameter of the tangent Poisson’s ratio G, F and D. The Duncan-Chang constitutive model parameters are generally obtained through triaxial tests. But maintaining confining pressure σ3 in triaxial test device is very difficult and needs lot of auxiliary devices. Meanwhile, almost all scales of triaxial test devices are small, and they are not suitable to conduct garbage compression test due to uneven composition. It’s difficult and costly to develop large scale triaxial test devices. Zhang [5] proposed a simplified calculation method, in which Duncan-Chang model can be put out by the results of direct shearing test and the axial direction compression test.
2.2. Direct shear test
The direct shear test is a common method for determining the shear strength in soil mechanics. The shear stress at the horizontal plane failure can be obtained from horizontal shear force to the samples under different vertical pressures. And cohesion c, internal friction angle φ can be calculated further according to the Coulomb strength theory. According to Zhang’s suggestion [5], we used the slow shear test of the direct shear test, and cohesion c, internal friction angle φ were taken as the parameters of the Duncan-Chang model when the shear strain reached 10 %. The relation between normal stressσ and shear stress τf is shown in Coulomb equation Eq. (3):
Taking the shear stress τf as ordinate and the normal stressσ as abscissa, the relationship between the shear stress and the normal stress is plotted in Fig. 3. The intercept of the line on the ordinate is cohesion c and the inclination of the line is the internal friction angle φ, as shown in Fig. 3.
Fig. 3Principle of direct shear test
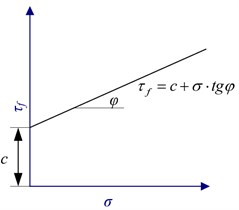
Fig. 4Direct shear test device: a – upper bucket; b – middle bucket; c – lower bucket; d – upper bucket support; e – lower bucket support; f – horizontal slide; g – horizontal slide support; h – horizontal actuator; i – vertical actuator; j – vertical cylinder fixed frame; k – sewage tank
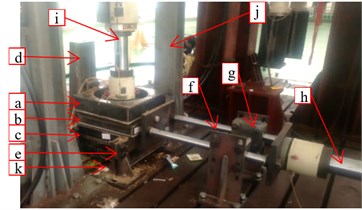
A large-scale test device was needed, so inner diameter of the test device was set to 500 mm. The container of traditional direct shear device is generally composed of two parts, one shear surface, which needs to overcome the friction of the sample and the weight of the counterweight. In order to improve the accuracy of the shear test, the container we designed was divided into three parts: upper, middle and lower parts. The shear force is applied to the middle part to achieve the shear of the sample. The upper and lower buckets were fixed completely, while the middle bucket was connected to the horizontal hydraulic actuator through the horizontal slides. Vertical pressure was provided by the vertical hydraulic actuator and horizontal shear is provided by the horizontal actuator. The fresh MSW has a large water content, and a large amount of sewage was continuously discharged during the compression process. So some holes with diameter of 5 mm were arranged at the bottom of the lower bucket for the sewage discharge to sewage tank. The special direct shear device is shown in Fig. 4.
2.3. Confined compression test device
Take the logarithm of initial elastic modulus Ei on both sides:
Taking lg(Ei/pa) as ordinate and lg(σ3/pa) as abscissa, the line is plotted as Fig. 5(a). Then the intercept is lgK and the slope is the elastic modulus exponent n. This is the method to determine Duncan-Chang model parameters K and n with the triaxial test. According to the initial Poisson’s ratio μi, taking μi as ordinate and lg(σ3/pa) as abscissa, the line is plotted as shown in Fig. 5(b). Then the intercept is G and the slope is F. This is the method to determine Duncan-Chang model parameters G and F with the triaxial test.
Fig. 5Principle of confined compression test
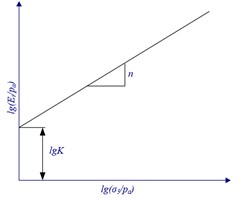
a) The relation betweenlg(Ei/pa) and lg(σ3/pa)
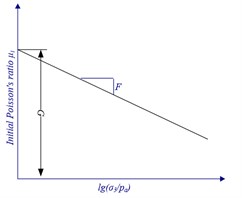
b) the relation betweenμi and lg(σ3/pa)
Fig. 6Confined compression test device
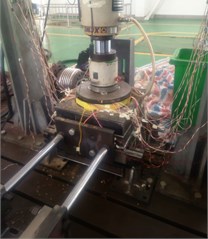
a) Overall view of the confined test device
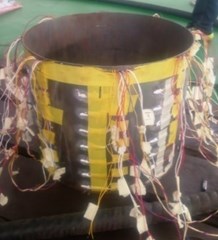
b) Strain gauges on outer surface of thin-walled bucket
Confined compression test device was reformed on the basis of the direct shear test device. The upper bucket, middle bucket and lower bucket were kept aligned vertically, and the horizontal actuator was locked. Another thin wall bucket with inner diameter of 476 mm, height of 500 mm and thickness of 2 mm was laid in bucket to conduct the confined compression test, as shown in Fig. 6(a). Seven rows and eight columns of strain gauges were arranged on outer surface of thin wall bucket, and their direction is the circumferential tangential direction, as shown in Fig. 6(b). In the compression process, V402EX wireless dynamic strain test system was used to monitor the microstrain value εφ of each strain gauge, so that the circumferential tangential stress σφ can be obtained as shown in Eq. (5):
where, E is the elastic modulus of the thin-walled bucket.
Since the wall thickness is much smaller than the radius, the relationship between the circumferential stress σφ and the internal pressure σ3 of the thin-walled bucket can be obtained according to the elastic mechanics equation Eq. (6):
where, R and t are inner diameter and wall thickness of the thin-walled bucket.
Therefore, the confining pressure σ3 can be derived as Eq. (7):
In this way, the confining pressure σ3 of the garbage can be derived by the microstrain values εφ of these strain gauges.
3. Test data and final Duncan-Chang constitutive model
3.1. Direct shear test data and confined compression test data
The direct shear test data was processed according to Eq. (3), and the points of normal compression stressσ and shear stress τf are plotted shown in Fig. 3. The straight line was fitted to obtain the internal friction angle φ and the cohesion c.
The confined test data were processed according to Eq. 4, and the elastic modulus coefficient K and exponentn were obtained by linear fitting as shown in Fig. 5(a). According to Eq. (4), the data of confined compression test were processed and the coefficient G and F were obtained by linear fitting, as shown in Fig. 5(b).
3.2. The final Duncan-Chang constitutive model parameters
According to Feng’s research [11], the damage ratio Rf of garbage increases with the axial strain. Meanwhile, it is recommended to take ε= 10 % as damage standard of the garbage, and take the damage ratio Rf= 0.55 without triaxial test data. The final Duncan-Chang constitutive model parameters of the fresh MSW were taken the average, as shown in Table 1.
Table 1The final Duncan-Chang model parameters of the fresh MSW
Constitutive model parameters | Value | Obtaining method |
Cohesionc | 8 kPa | Direct shear test |
Internal friction angle φ | 12° | Direct shear test |
Damage ratioRf | 0.55 | Reference [11] |
Modulus of elasticity K | 6 | Confined compression test |
Elastic modulus exponent n | 1.15 | Confined compression test |
G | 0.39 | Confined compression test |
F | 0.0166 | Confined compression test |
D | 1 | Reference [5] |
4. Simulation of garbage compression process
4.1. Model of confined compression test
Based on the Duncan-Chang constitutive model of fresh MSW obtained in the previous article, simulation of garbage compression test was conducted with ANSYS. But all FEA software lacks Duncan-Chang constitutive model, so further development is achieved with the APDL language on ANSYS platform. The material properties of every element are constantly changing in Duncan-Chang constitutive model. According to Duncan-Chang model, the material properties used in the next step need to be calculated with the current stress state.
Simulation of the confined compression test was conducted based on the Duncan-Chang constitutive model in Section 3.2. The inner diameter and height of the thin wall bucket are 476 mm and 500 mm respectively. Axisymmetric model was adopted, and a forced displacement was applied on upper boundary of model, as shown in Fig. 7. Because the stress of garbage is uniform everywhere in the whole model, the garbage can simply be set as one material instead of extracting stress from each element, recalculating its elastic modulus, Poisson's ratio and updating material properties. Therefore, simulation of the confined compression test becomes very simple at this time.
4.2. Analysis results
Analysis terminated due to element excessive distortion, and the final result is shown in Fig. 8, in which the maximum deformation only reached 181 mm. The average pressure curve with the forced displacement of the garbage is shown in Fig. 9. Meanwhile, the average pressure curve with the forced displacement of five tests of the fourth batch is shown in Fig. 9. As shown in the figure, the resistance of the garbage was weak at the early compression stage, and after that, the resistance has sharply increased. The elastic modulus of the garbage changed with average pressure, as shown in Fig. 10.
Fig. 7Test model of waste compression
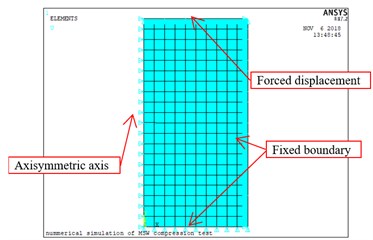
Fig. 8Deformation of last step
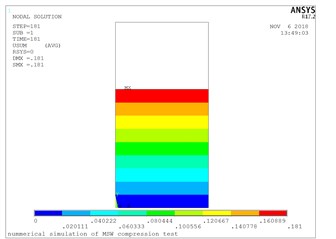
Fig. 9The average pressure along the displacement curve of five tests of the fourth batch and simulation
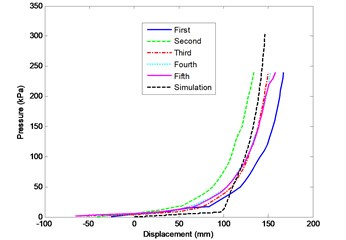
Fig. 10The elastic modulus of the garbage changes with pressure
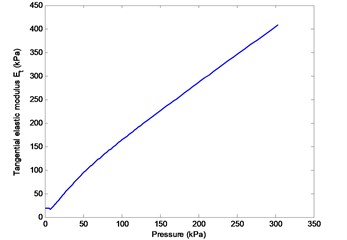
Firstly, geometric nonlinearity and contact nonlinearity were involved. Secondly, it is necessary to extract the principal stress of each element after each loadstep and recalculate and update the elastic modulus and Poisson's ratio according to the Duncan-Chang model. Thirdly, the garbage itself has a large deformation, and it may lead to element malformation and even negative volume, which results in the termination of the calculation. Generally, it is difficult to simulate the whole garbage compression process according to the Duncan-Chang model.
5. Conclusions
In this paper, as the working objects of compression garbage trucks, the mechanical properties of fresh MSW were studied. A special test device combining the direct shear test with the confined compression test was designed, manufactured and assembled to conduct test about the fresh MSW. Detailed test data was obtained with direct shear test and confined compression test. And the Duncan-Chang constitutive model parameters by summarizing and organizing test data. Then the Duncan-Chang constitutive model parameters were used to simulate the confined compression test. The correctness of the parameters of the Duncan-Chang constitutive model of fresh MSW was verified, which provided a basis for the simulation and structure optimization of the garbage compression process of the compression garbage trucks.
References
-
Zhang Bingyin, Jie Yuxin Strength and deformation characteristics of waste soil. Engineering Mechanics, Vol. 23, Issue 2, 2006, p. 14-22, (in Chinese).
-
Qian Xue De, Guo Zhi-Ping Engineering properties of municipal solid waste. Chinese Journal of Geotechnical Engineering, Vol. 20, Issue 5, 1998, p. 4-9, (in Chinese).
-
Sun Xiuli, Kong Xianjing, Zou Degao, et al. Stress-strain model of municipal solid waste. Chinese Journal of Geotechnical Engineering, Vol. 30, Issue 5, 2008, p. 726-731, (in Chinese).
-
Zhen-Ying Z., Li-Jun Y., Da-Zhi Wu Experimental study of compression and direct shear combined test of fresh municipal solid waste. Rock and Soil Mechanics, Vol. 35, Issue 11, 2014, p. 3049-3055, (in Chinese).
-
Zhen-Ying Z. Study on Compressibility and Settlement of Landfill for Municipal Solid Waste. Zhejiang University, 2005, (in Chinese).
-
Xuan P., Hua-Ping T. Finite element analysis of rear-loaded garbage compressing cart based on Duncan-Chang constitutive model. Mechanical Research and Application, Vol. 3, 2015, p. 14-16, (in Chinese).
-
Zhong M. Q., Xiao H. B., Huang Q., et al. The optimization analysis of the lifting structure of the buried garbage compression station. Applied Mechanics and Materials, Vol. 364, 2013, p. 76-80.
-
Qian Jiahuan, Yin Zongze Geotechnical Principles and Calculations. China Water Resources and Hydropower Press, Beijing, 2000, (in Chinese).
-
Wang X., Liu Z., Cui W. Implementation of Duncan-Chang model in ANSYS and the inversion of its parameters. Proceedings of the 2nd International Conference on Modelling and Simulation, Vol. 7, 2009, p. 65-71.
-
Guo P., Li W. C. Development and implementation of Duncan-Chang constitutive model in GeoStudio2007. Procedia Engineering, Vol. 2, Issue 1, 2011, p. 395-402.
-
Feng Shijin Static and Dynamic Strength Characteristics of Municipal Solid Waste and Stability Analysis of Landfill. Zhejiang University, 2005, (in Chinese).