Abstract
In order to analyze the impact acceleration of the projectile impacting the aluminum foam material, a dynamic non-linear finite element model of the projectile impacting the closed-cell aluminum foam experiment device was established and verified by the experiment. It is found that the numerical simulation results of projectile impact closed-cell aluminum foam are consistent with the change of experimental results. When the projectile impacts the homogeneous closed-cell aluminum foam, the impact acceleration is trapezoidal and the impact peak and pulse width are related to the density of the aluminum foam material. With the increase of the porosity of the aluminum foam, the peak value of the acceleration rises and the pulse width of acceleration decreases.
1. Introduction
In recent years, with the rapid development of aviation, aerospace, and weapons industries, there are some higher requirements on new materials and certain key components. There is an increasing need for impact experiment. Such experiments require that equipment be capable of providing a strong shock, wide pulse impact environment. At present, domestic research on the design of impact experiment mainly focuses on experimental simulation under low-velocity impact environment. However, there are few experimental studies on strong impact and wide pulse impact environment. There is no complete set of strong impact experiment methods and experiment methods. The wide-pulse and strong-impact parameter calibration technology of foreign gunfire missile-borne flight recorder experiment equipment is relatively advanced. The configuration of calibration equipment at all levels is complete. The United States and the United Kingdom have 6.5 ms and 34000 m/s2 strong impact experiment equipment and the corresponding calibration device mainly used for the strong impact experiment of the flight data recorder in this field.
In the impact experiment, the performance of the buffer material directly affects the impact performance (peak value of impact acceleration and pulse width). Foam metal materials have good energy absorption and cushioning properties, and their excellent mechanical properties have been widely used in engineering. Jilin Yu et al. [1] carefully analyzed the impact mechanical behavior of foamed metal materials and structures through three-dimensional Voronoi grid technology. Zhigeng Fan et al. [2] established a three-dimensional random spherical cell model for aluminum foam and studied the influence of porosity and strain rate on the dynamic impact process of aluminum foam by finite element method; Jun Tang et al. [3] and others simulated the projectile numerically. Penetrating the closed-cell aluminum foam, the shape of the warhead was found to have a great influence on the waveform of the acceleration time history curve of the impact of the projectile on the closed-cell aluminum foam.
Based on the good cushioning properties of aluminum foam materials, this paper uses aluminum foam as the acceleration generating medium. By a combination of numerical simulations and experiments, the impact acceleration of high-velocity projectiles impacting homogeneous porosity aluminum foams with different porosity are studied. The formation of the acceleration of the projectile provides a reference for further study of the high-peak and wide pulse acceleration.
2. Simulation and analysis of high-speed projectile impact aluminum foam
2.1. Model assumptions
To simplify the calculation model, make the following assumptions:
(1) Regardless of the projectile flight process, the model starts when the projectile touches the aluminum foam plate.
(2) The strain rate effect of aluminum foam materials is not considered, there is no strain rate-related quantity in the material constitutive model.
(3) Regardless of temperature stress field: Assuming that the projectile and aluminum foam plate are deformed in an adiabatic process during impact without considering the impact generated by friction.
2.2. Finite element mesh
The projectile is a ball-headed projectile with a radius of 55 mm. The body of the projectile is a cylinder and the hollow structure of the projectile. This article takes the closed-layer aluminum foam plate stacked in ten layers as the research object. The specification of each plate is 200 mm×200 mm×20 mm. It is fixed in front of a rigid baffle and the four corners of the aluminum foam plate are supported by the baffle’s support. The eight node hexahedron element is used to mesh the projectile and aluminum foam, and the aluminum foam mesh penetrated by the projectile should be refined. The grid model is set up as shown in Fig. 1. There are about 196,000 units in total.
The established finite element model is explicitly solved by the Lagrange algorithm of LS-DYNA software. The single-point integration and viscosity-based hourglass control are both conducive to stable and reliable large deformation calculation [4], and save computer resources.
Fig. 1Mesh model
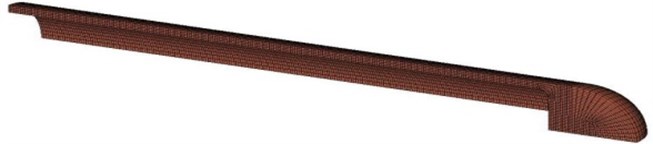
a) Projectile mesh model
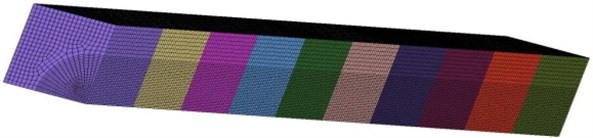
b) Aluminum foam grid model
2.3. Material model and constraint load
The projectile material is hard aluminum alloy grade 2A11 and the aluminum foam plate material is closed cell aluminum foam.
Table 1Projectile material
Material brand | Density | Elastic modulus | Poisson’s ratio | Yield stress | Shear modulus |
2A11 | 2.79 g/cm3 | 68 GPa | 0.33 | 215 MPa | 26 GPa |
Table 2Closed cell aluminum foam material
Porosity | Density (g/cm3) | Elastic modulus (MPa) | Poisson’s ratio | Platform stress (MPa) |
81.5 % | 0.4995 | 410.0 | 0.25 | 7.71 |
85.0 % | 0.4028 | 320.2 | 0.24 | 5.22 |
88.5 % | 0.3105 | 216.0 | 0.24 | 3.53 |
During the process of penetrating the aluminum foam plate, the projectile may be damaged in view of high-speed impact, and an ideal elastic-plastic constitutive model with damage is used. The aluminum foam plate uses the MAT_CRUSHABLE_FOAM material constitutive model according to the literature [5]. This model describes the mechanical properties of the compressible material through the stress-strain curve of the material. The projectile material and aluminum foam material parameters are shown in Table 1 and Table 2.
2.4. Definition of contact and constraint load
The contact algorithm between the projectile and aluminum foam plate is the erosion contact algorithm based on penalty function method in LS-DYNA. When the projectile began to impact the aluminum foam, the projectile was given an initial speed of 140 m/s. The aluminum foam plate is fixed in front of the rigid baffle. Due to the symmetry of the model, in order to reduce the calculation time, this paper uses 1/4 of the total model to calculate, and it needs to add symmetry constraint of displacement and rotation angle on the symmetry plane.
2.5. Simulated results and analysis of impact homogeneous aluminum foam
The finite element model of the projectile impact foam was numerically calculated by LS-DYNA software. The aluminum foam plates with the porosity of 81.5 %, 85.0 %, and 88.5 % were respectively impacted with the same shot and speed (140 m/s). Fig. 2 is the von Mises deformation cloud diagram at various times during the impact of the projectile on the 81.5 % porosity aluminum foam. Fig. 3 is the acceleration time curve, and the peak acceleration and pulse width are shown in Table 3.
Fig. 2Aluminum foam at different times von mises stress
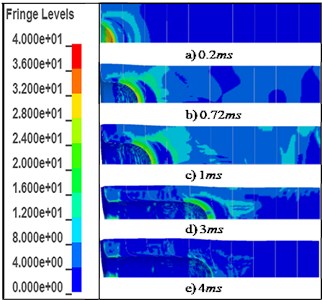
Fig. 3Projectile acceleration-displacement curve
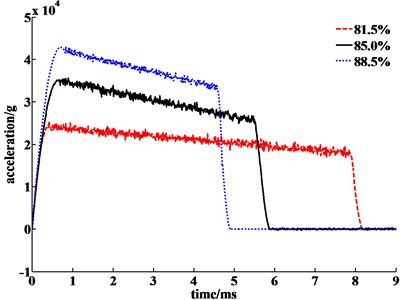
It can be seen from Fig. 2 that during the impact process, the aluminum foam is pressed by the projectile and pushed to both sides, and the deformation of the material in contact with the spherical surface of the projectile warhead is the largest, and there is almost no deformation at the end of the aluminum foam plate.
As can be seen from Fig. 3 the impact acceleration of three different porosity aluminum foam plates have a similar trend, and the whole is a trapezoidal wave, which is mainly divided into three stages. 1) the beginning of the impact, when the ball warhead touched the target plate and completely submerged into the target plate, the impact acceleration rapidly increases and reaches a peak with time. The upward trend coincides with the contact area between the warhead and the target plate, and no sudden change or fluctuation occurs; 2) the mid-impact stage, there is a fluctuating downward trend. During this process, due to the platform characteristics of aluminum foam, the resistance of the projectile is not changed very much. As the projectile speed decreases, the acceleration also decreases linearly; 3) the end stage, the acceleration rapidly drops and completes projectile penetration. The acceleration peaks and pulse widths (acceleration durations) of the three accelerations are shown in Table 3.
Table 3Impact acceleration peak and pulse width
Porosity | Acceleration peak (g) | Pulse width (ms) |
81.5 % | 2482.42 | 7.80 |
85.0 % | 3535.91 | 5.49 |
88.5 % | 4567.21 | 4.58 |
The simulation results show that the peak value of the acceleration rises, the pulse width of acceleration decreases, and the absorption energy per unit volume of aluminum foam increases with the increase of porosity of aluminum foam.
3. Experiment of high speed projectile impacting aluminum foam
Through the impact experiment, the displacement of the projectile was measured, and the change law of the impact acceleration of the projectile was studied to verify the correctness of the simulation modeling method when the aluminum foam with different material parameters was impacted.
3.1. The design and principle of impact experiment
The air gun was used as the generating device of the acceleration form. The experiment system is composed as shown in Fig. 4.
Fig. 4The experiment system
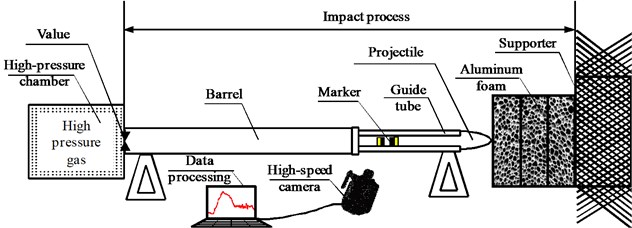
The waveform-producing experiment piece is mounted inside the body tube and is in close contact with the high-pressure chamber. During launch, the release mechanism opens quickly and the gas pressure is applied to the bottom of the waveform-producing specimen. The waveform-producing specimen is accelerated until it exits the muzzle. During the process of penetrating into the buffer material, the experiment piece of the waveform causes the buffer material to locally break and compress, and finally the plug phenomenon occurs. The waveform of the sample generates the required acceleration waveform, and the waveform is measured by a high-speed camera and motion analysis software. The impact movement displacement of the part, after the data preprocessing, obtains the complete waveform of the impact acceleration by the secondary differential operation.
3.2. Experiment results and analysis
The aluminum foam plates with the porosity of 81.5 %, 85.0 %, and 88.5 % is respectively impacted with the same speed (140 m/s). Fig. 5 shows the acceleration curve, and the acceleration peaks and pulse widths are shown in Table 4.
Fig. 5Different porosity aluminum foam acceleration curves
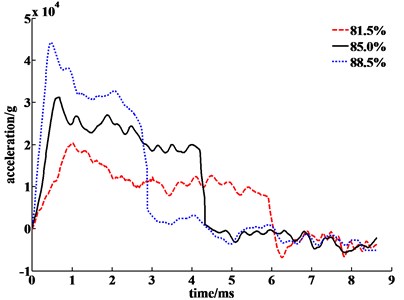
As can be seen from Fig. 7, three different porosity aluminum foam materials have similar acceleration and are roughly divided into three phases: 1) the beginning of the impact, the aluminum foam material only undergoes elastic deformation, and the smaller deformation of the material causes larger increases of the stress, leading to acceleration in a short time to increase to the peak; 2) the middle stage of impact, the acceleration slightly decreases with the plastic yield of the aluminum foam, with closed-cell aluminum foam part or the whole densification, the mechanical properties of the closed-cell aluminum foamed material increase, the resistance to the projectile increases, and the acceleration begins to increase; 3) the end stage of impact, the acceleration at this stage decreases rapidly and completes the projectile penetration.
The experimental results show that with the increase of the porosity of aluminum foam, the relative density of aluminum foam decreases, the proportion of matrix material on the closed-cell aluminum foam material per unit area decreases, the peak value of the acceleration increases, and the pulse width of the acceleration decreases. The volume of absorbed energy increases.
Table 4Impact acceleration peak and pulse width
Porosity | Acceleration peak (g) | Pulse width (ms) |
81.5 % | 2029.51 | 6.23 |
85.0 % | 3113.62 | 4.35 |
88.5 % | 4320.45 | 2.89 |
Comparing the experiment and simulation results shown in Fig. 4, Fig. 6, Table 3, and Table 4, we can see that the calculation result of the acceleration peak of a simulation is large and the deviation is about 22 %, 12 %, and 5 %, respectively. and the change laws of acceleration in the experiment and simulation are consistent and both decrease in proportion to time.
4. Conclusions
By the method of experiment and numerical simulation, it is analyzed that the acceleration of the projectile when the closed-cell aluminum foam material with different porosity is impacted by the projectile. The following conclusions have been drawn:
1) The results of the projectile impacting the closed hole aluminum foam have a large error between the experiment and the experiment, but the numerical simulation calculation is consistent with the acceleration variation rule of the experiment.
2) When the projectile impacts the homogeneous closed-cell aluminum foam, the acceleration form is trapezoidal and the impact peak and pulse width are related to the density of the aluminum foam material. With the increase of the porosity of the aluminum foam, the peak value of the acceleration rises and the pulse width of the acceleration decreases.
References
-
Yu Ji Lin, Wanger Heng, Lijian Rong Structure and impact mechanics behavior of foamed metal materials. The Report of Applied Mechanics, 2004.
-
Fanzhi Geng, Chen Chang Qing, Wan Qiang Finite element simulation of aluminum - related properties of aluminum foam. Explosion and Acceleration, Vol. 34, Issue 6, 2014, p. 742-747.
-
Tang Jun, Ge Jian Li, Yan Bin Numerical simulation of the acceleration form of projective penetration. Journal of Nanjing University of Science and Technology, Vol. 3, 2016, p. 328-333.
-
South J., Powers B., Minnicino M. Evaluations of computational techniques for the engraving of projectiles. Wit Transactions on Modelling and Simulation, Vol. 45, 2007, p. 193-202.
-
Hanssen A. G., Hopperstad O. S., Langseth M., et al. Validation of constitutive models applicable to aluminiumfoams. International Journal of Mechanical Sciences, Vol. 44, Issue 2, 2002, p. 359-406.