Abstract
In order to determine the radius of borehole gas drainage, using five kinds of gas content under different conditions corresponding to the extraction rate were compared according to different drainage objectives, determine the need for gas drainage amount, according to a certain period of time the average single hole gas drainage quantity, calculate the number of drilling in the region need to be arranged, and then get the borehole gas drainage radius. Based on the actual investigation and comparison analysis, the effective radius of borehole gas drainage in certain extraction time is obtained. The results show that the method of gas content determination of drilling drainage radius is feasible.
1. Introduction
With the gradual depletion of shallow coal resources, the mine gradually into the deep mining, gas disaster is becoming more and more serious. The regional gas control measures mainly include two kinds of protective seam mining and pre extracting coal seam gas. Because some protective layer into the outburst danger, or not be recoverable, which has prominent protective layer mining conditions mine more and less, at the same time, the mine outburst risk is becoming more and more serious, therefore, will take more and more prominent coal mine gas pre drainage measures.
The precondition of coal seam gas extraction is the rationality of the design of the drainage hole, and the effective radius of gas drainage can solve the rationality of the design of the drainage hole. Standard Provisional Regulations of coal mine gas pumping Mining: mining should adhere to the “should exhaust smoke, Duocuobingju, pumping and digging the balance” the principle of gas pumping. The effective drainage radius can guide the rational design of the drainage hole, not only can eliminate the outburst danger to meet the premise of pre drainage time of the use of this method, but also can save a lot of manpower, financial and material resources.
2. Method for determination of drainage radius
2.1. Determination method
The effective radius of borehole gas drainage is the minimum range of the single borehole in the radius of a certain extraction time. At present, the effective method of determining the effective drainage radius is to reduce the gas pressure in coal seam [1-5]. This method refers to the original coal seam within certain distance arrangement pressure drilling, determination of the original coal gas pressure, gas pressure stable, in pressure around the borehole at a certain distance from the construction of several specific diameter boreholes, in drainage period, measuring pressure and gas pressure decrease to a certain extent the pressure, drilling and drainage hole distance between the specific borehole drainage time in the effective drainage radius. The method for field determination of coal seam gas pressure, the determination of long cycle, high cost, and the consequent drainage radius of investigation, due to the effect of the drainage structure and gas, often gas pressure hole suddenly unloading, resulting in investigation of failure, the success rate is low.
The influence radius of borehole extraction is mainly related to the factors such as gas content of coal seam, permeability coefficient, diameter of drainage hole, negative pressure of extraction, target and time of extraction. In this paper, the influence radius of borehole gas drainage is determined by the known gas content and target gas content.
According to the current “coal mine safety regulations”, “prevention and control of coal and gas outburst regulations” and other laws and regulations to determine the extraction target. As follows:
(1) The gas extraction rate by reducing the residual gas content to 8 m3/t, η1 please refer to Eq. (1):
(2) According to the gas drainage rate when the residual gas content is reduced to the coal seam gas content, η2 please refer to Eq. (2):
(3) According to the gas drainage rate when the residual gas pressure is reduced to 0.74 MPa, η3 please refer to Eq. (3):
(4) According to the gas pressure when the residual gas pressure is reduced to the initial depth, η4 please refer to Eq. (4):
(5) According to the “coal mine gas extraction basic indicators” of the gas extraction rate, η5.
Determined gas extraction rate, please refer to Eq. (5):
The total amount of gas extraction can be calculated by pressing, please refer to Eq. (6):
where: L1, L2 – the length and width of the control area of the drainage borehole, m; h – the thickness of coal seam in control area, m; γ – the density of coal in the control area, m3/t; W – the original gas content of coal seam in the control area of the drainage borehole, m3/t; η – determined extraction rate.
The calculation of the number of drilling holes, please refer to Eq. 7:
where: Q2 – single hole extraction quantity in the extraction time, m3; Q2 – statistical calculation: first, according to the test data obtained directly cumulative, and the other is based on the test data to fit the attenuation index curve, in order to calculate the total amount of time to get the total amount of extraction.
Finally, the N drilling holes are distributed in the control area of the borehole, and the radius of borehole extraction can be calculated. The radius of borehole drainage can be calculated by the following equation, please refer to Eq. (8):
where r: drainage radius.
2.2. Investigation procedure
(1) The original gas content of the coal seam in the test area is directly determined by the DGC gas content measurement device or W method;
(2) The construction of a set of (10) drilling holes, spacing 8 m;
(3) Calculate the amount of gas needed to be extracted according to the extraction target;
(4) According to the different time of extraction, calculate the gas drainage radius.
3. Engineering geological condition
2101 mining area of a total of two layers of coal, respectively, on the top of the coal and 1 coal, are recoverable coal seam. 1 the thickness of coal seam is 3.9m on average, the thickness of coal seam is stable, the overall structure of coal seam is simple, the coal seam angle is from 4 to 12 degrees, with an average of 9 degrees. 1 the thickness of the upper coal seam is from 0 to 4.44 M, with an average of 3.5 m, the overall structure of the coal seam is relatively simple, and the coal seam inclination angle is from 4 to 12 degrees, with an average of 9 degrees. Between 1 and 1 on the development of a coal seam layer 0– 1.7 m black mudstone partings.
The test area is located on the 210108 faces, the working face to 1485.3m long; long 145.5 m; 216110 m2 mining area; to 1338.3 m long; coal seam angle: 5 degrees to 12 degrees (average 8), the recoverable slope area: 96638 m2, underground elevation of –608.3-–647.1 m. The gas content of coal seam is 6.65 m3/t, which has not occurred the phenomenon of outburst. Coal mining method for working face adopting long wall retreating type comprehensive mechanized mining full height, all caving and forced caving management roof.
4. Drainage borehole layout
According to the field investigation, the 1 groups of the same layer of 3# drilling field along the coal seam in the construction of the formation of the 210108 sets of bedding drilling. The drilling parameters of the horizontal borehole are as follows: the diameter of the borehole is 94 mm, the distance between the holes is 8 m, the sector is arranged. Along the roadway heading direction control 35 m, along the coal seam inclination control 100 m. This kind of arrangement can solve the problem that the condition of the site cannot be used to investigate the problem of parallel bedding. The layout of the design drawing of the drawing hole is shown in Fig. 1. The drilling parameters are shown in Table 1.
Fig. 1Layout design of borehole layout
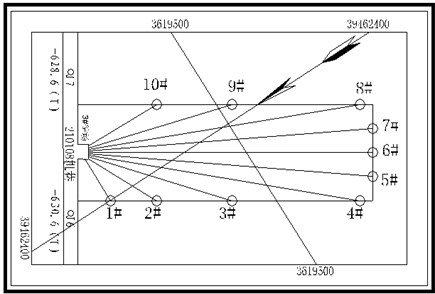
Table 1Parameters of borehole construction
Number | Position ° | Dip angle ° | Depth (m) | Number | Position ° | Dip angle ° | Depth (m) |
1 | 271 | 5 | 16 | 6 | 213 | 9 | 98 |
2 | 244 | 7 | 27 | 7 | 208 | 8 | 98 |
3 | 229 | 7 | 51 | 8 | 203 | 8 | 94 |
4 | 222 | 8 | 94 | 9 | 196 | 7 | 51 |
5 | 217 | 8 | 98 | 10 | 182 | 7 | 27 |
5. Results and analysis
5.1. Analysis of statistical data
5.1.1. Calculation of pumping radius by statistical flow
According to the basic index of coal mine gas extraction, according to the prediction of gas emission in 1 coal seam face, the gas extraction rate of mining face is greater than or equal to 30 %.
210108 the extraction radius of the 3# drilling field in the working face, the amount of gas needed to be taken into account in the drilling control area, please refer to Eq. (9):
In order to reduce the influence of borehole length difference, the 10 field drilling unified measurement in 210108 working face of 3# drilling, drilling in the area controlled by the average calculation of single hole gas drainage quantity, statistical results are shown in Table 2.
Table 2Statistics of average single hole pumping gas production
Date | Cumulative days | Average daily gas production by single hole(m3/d) |
March 20th | 1 | 56.44 |
March 26th | 7 | 50.45 |
April 3rd | 15 | 47.79 |
April 18th | 30 | 36.5 |
May 18th | 60 | 14.19 |
The actual average daily amount of pure single hole drainage is not equal, according to the daily average extraction of pure cumulative amount calculated 15 days, 30 days, 60 days of drainage, drainage radius of scalar results in Table 3 pumping drilling, the pumping pressure at 13 kPa, drainage hole diameter 94 mm.
Table 3Calculation results of borehole drainage radius
Extraction time (d) | Cumulative total extraction of single hole (m3) | Drillings required | Drainage radius (m) |
15 | 810.94 | 40 | 0.90 |
30 | 1385.12 | 24 | 1.6 |
60 | 2199.91 | 15 | 2.5 |
5.1.2. fitting radius of discharge curve
210108 working face of 3# drilling field average single hole pumping on statistical results of gas drainage amount fitting ring burden index curve, as shown in Fig. 2, the data correlation coefficient R2= 0.9616, the correlation of data, the attenuation of negative exponential curve can effectively represent the 210108 working face of single hole drilling, Caiwa law.
On the basis of the equation for calculating the value of the 210108 indexes of the working face, the integral radius of the working face is calculated, please refer to Eq. 10, and the results are shown in Table 4:
Table 4Calculation results of borehole drainage radius
Extraction time (days) | Single hole extraction (m3) | Drillings | Drainage radius (m) | Remarks |
30 | 1363.28 | 24 | 1.6 | |
60 | 2047.06 | 15 | 2.5 | |
∞ | 2735.17 | 12 | 3.1 | Limit radius |
To sum up, the two methods are basically consistent with the calculated radius of borehole drainage. The calculation results show that the radius of the 1 coal seam drilling is about 2.5 m for the first 2 months, and the ultimate drainage radius is 3.1 m.
Fig. 2Fitting chart of gas volume per day
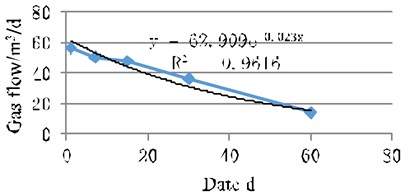
6. Conclusions
1) The method of determining the influence radius of borehole gas drainage by using the original gas content and the target gas content is put forward.
2) Mining radius 2.5 m pumping two Xinji Mine 1 coal seam 2 months for 3.1 m borehole gas drainage radius, pumping limit.
3) The method can be used as a reference for the traditional method of determining the radius of pumping and is used to guide the treatment of mine gas disaster.
References
-
Yu Tao Measurement of effective drainage radius based on gas flow and pressure of boreholes. Journal of Mining and Safety Engineering, Vol. 29, Issue 4, 2012, p. 596-600, (in Chinese).
-
Lu Yi Gas drainage radius and borehole distance along seam. Journal of Mining and Safety Engineering, Vol. 32, Issue 1, 2015, p. 156-162, (in Chinese).
-
Ji Huai-jun Drainage radius measurement based on gas flow field. Journal of Mining and Safety Engineering, Vol. 30, Issue 6, 2013, p. 917-921, (in Chinese).
-
Liang Bing Grouped pressure test to determine effective gas drainage radius. Journal of Mining and Safety Engineering, Vol. 30, Issue 1, 2013, p. 132-142, (in Chinese).
-
Zhao Feng Numerical calculation method of effective drainage radius for gas drainage borehole. Coal Engineering, Vol. 392, Issue 6, 2011, p. 82-84, (in Chinese).
About this article
This work was financially supported by the National Natural Science Foundation of China (51604298), the Science and Technology Innovation Foundation Program of China Coal Research Institute (2016ZYMS016), and the Key Laboratory Open Foundation of Anhui Province (KLDCMERDPC14101).