Abstract
Time-varying length axially moving string subjected to control force and transverse excitation force is analyzed. The string’s transverse vibration attenuation law is achieved. Suitable lateral displacement solution is proposed to meet the conditions of vibration based on the accurate control. The relationship among the transverse displacement, the angular velocity and the time is obtained and discussed. The effect of string’s speed, damping, tension variable on the transverse displacement of string are also taken into consideration.
1. Introduction
Axially travelling string systems are widely used in mechanical engineering, which is a one-dimensional continuum without considering the bending stiffness, such as elevator cables, satellite tethers, high-speed magnetic, etc. Transverse vibrations of axially travelling string systems have been studied extensively for many years and are still of interesting nowadays. Sack [1] studied transverse standing wave characteristics of a constant speed and uniform tensioned axially moving string in two smooth support. Swope and Ames [2] study the instability of the fibers in the textile industry under the axially moving string of mechanical model.
Mote studied the constraints in chainsaw movement between two end points [3] and the nonlinear vibration of axially moving strings [4]. Thurman and Mote [5] studied the problem of the nonlinear free vibration of the axial movement string, considering the longitudinal and transverse vibrations. Ulsoy [6] established a band saw vibration equation and analyze the incentives, instability standards and vibration control. Kotera [7] applied a new variable substitution method to deal with time-varying length string problem. Wickert and Mote [8] set up the equations of motion of the axially moving string, solving the response of axially moving strings of arbitrary initial conditions. Lee and Mote [9] studied an additional inertial stiffness and viscous damping in the axially moving string model between two fixed fulcrums and analyzes the energy transmission and reflection in nodes. Foda [10] study the lateral vibration of the axially moving string fixed at both ends using Hamilton's principle combined with the Green's function with the damping and excitation force acting on it. Butikov [11] studied potential and kinetic energy of strained string from horizontal and vertical direction by the microscopic view.
2. Principle
This paper analyzes the axially moving time-varying length string through two support holes, in Fig. 1. In order to analyze, make some necessary vision as following: The deflection of the transverse vibration is small, the slope of the string is very small, the effect of gravity on the string can be ignored, string density does not change with different lateral displacement of the string, strain remains constant during movement, ignoring axial vibration.
A point worth noting is that this paper is for the analysis of transverse vibration energy of the string, the following calculation is also based on this. Although the analyzed axial string length (i.e. mass) increases with the time, but the lateral kinetic and potential energy of the increase part are zero. Therefore, it can be considered that the increased part had taken into account at the initial time, but the contribution of this part to transverse energy is zero only.
Fig. 1Model of moving string with variable length
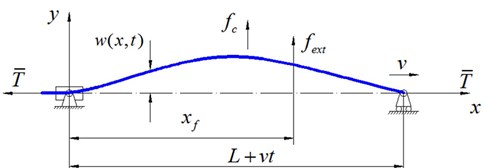
The kinetic energy of two vertical support ends system can be written as:
where ρ is the density, A is the cross-sectional area, L is the length when t= 0, v is speed, w(x,t) is the displacement at the location x and time t. Potential energy in the vertical direction is:
Note: Because of the existence the lateral displacement w(x,t), the components in the vertical direction of the tension ˉT do work on the system. The lateral displacement at both ends of the string is zero, so the components do not work. Using the Hamilton’s principle:
Work done by the non-conservative forces in the vertical direction of the string is defined as:
where fext(t) is the vertical exciting force acting on the string, fc(t) is the vertical control force acting on the string, xf is the location of the exciting force, b is the damping coefficient.
Substitute Eqs. (1), (2), (4) into Eq. (3), and the formula was set up by an arbitrary time, obtain:
+2[fextδ(x-xf)+fc(t)-b(∂w(x,t)∂t+v∂w(x,t)∂x)]∂w(x,t)∂xdx=0.
To change influence of the location on time, the substitutions of variables are as follow [7]:
Using ξ instead of x, τ instead of t, the displacement variables are no long subject to time variable constraints. Where υ=v/L, ξ∈[0,L]. From Eq. (6), one can obtain:
For convenience, define ∂w(x,t)/∂x=wx(x,t), ∂w(x,t)/∂t=wt(x,t). Under the assumption:
Substituting Eqs. (6), (7), (8) into Eq. (5), one can obtain:
Here Eq. (9) has been set up for any time interval [τ1, τ2], so the function of the integral is zero. To facilitate the simplification of Eq. (9), w(ξ,τ), F'0 and F'c, the following forms are taken:
where W(ξ) is a polynomial including ξ only. The boundary conditions can be written as:
The boundary condition of the string can be written in the following way:
where ak is a factor. When n= 3, one has:
Among them:
The relationship between coefficients can be drawn from the boundary conditions Eq. (11):
Substituting Eqs. (13), (14) into Eq. (10) and simplifying the result, one can obtain:
Substituting Eqs. (10), (13), (14) into Eq. (9) and after simplification, one has:
where W'(ξf) is the derivative of W(ξf). Eq. (15) indicates that, A4 reflects the magnitude of the lateral displacement to some extent. The damping coefficient b in Eq. (16) locating on the denominator of A4 becomes larger when A4 is smaller, which accords with the actual circumstance. From Eqs. (13) and (14), one has
Substituting Eq. (17) into Eq. (16), we obtain the expression of A4. Then substituting the expression of A4 into Eq. (15), the transverse displacement of the string can be obtained.
3. Simulation
In this section, the effect of various parameters on the string transverse displacement attenuation is analyzed, which will give some guidance to the control the axial movement of the string. In the following, Assume ρ= 900 kg/m3, A= 0.0002, L= 1, ξf.= 0.4, F0= 1, v= 0.3.
When b=0 and Fc=0.05(1+0.3t)1/3+0.096, the relationship among the displacement w(x,t) of the midpoint of the string, time t and angular ω is shown in Fig. 2.
Fig. 2The relationship between wx,t and ω
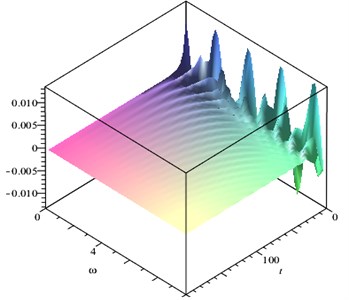
Fig. 3The relationship between wx,t and t
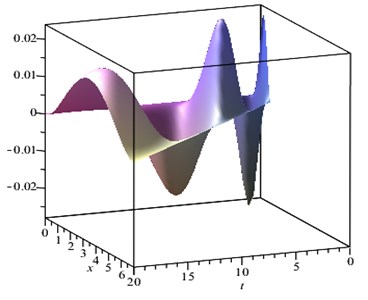
Fig. 2 shows the midpoint displacement w(x,t) is different as angular ω changes, while the general trend is getting small with the time. We can choose appropriate angular ω to make the midpoint displacement w(x,t) small. So, taking the appropriate angular value ω can avoid peak shock. When ω= 2, we have the result shown in Fig. 3. Fig. 3 shows the transverse displacement w(x,t) is tend to smaller as its length getting longer. The curve of midpoint displacement is shown in Fig. 4. To compare with the result when b= 1, two curves are given in Fig. 5. Where, the color of curves is red when b= 0 and blue when b= 1.
From the Fig. 5, the red curve is always above the blue curve. Under the circumstance of existing damping, transverse displacement at the midpoint of string is always smaller than the no damping, which accords with the actual circumstance.
When the control force Fc= 0.05(1+0.3t)1/3+0.096 (represented by the red curve), and no control force, i.e. Fc= 0 (represented by the blue curve), the results are shown as below:
The Fig. 6 above shows the red curve applied control force is always below the blue curve, which achieves the desired effect. Adding time-varying control force may change the attenuation trend. Selecting the appropriate control force can achieve the desired control effect of transverse displacement of the string.
Fig. 4The relationship between wx,t and time t
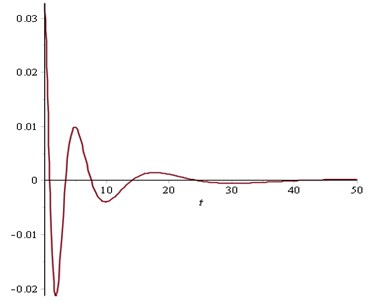
Fig. 5The displacement with or without damping
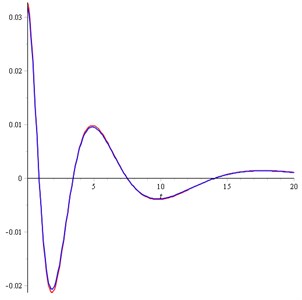
Fig. 6The midpoint displacement wx,t with or without control force Fc
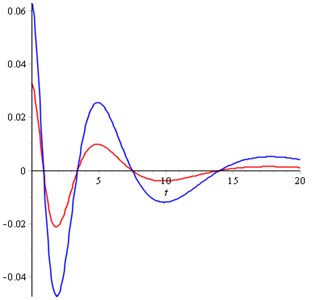
4. Conclusions
In this article, the transverse energy of the time-varying length axially moving string is analyzed based on the expanded Hamilton principle. The non-conservative forces acting on the analyzed strained string are also taken into consideration, such as damp control force and excitation force. The relationship between control force and transverse displacement is obtained. Selecting the appropriate natural frequency could effectively reduce the transverse displacement of the string when other conditions remain unchanged. Transverse displacement in the case of with damping is smaller than that of without damping, which accords with the actual circumstance. Selecting the appropriate control force can achieve the desired control effect of transverse displacement of the string by the relationship between control force and transverse displacement, which will give guidance in real application.
References
-
Sack R. A. Transverse oscillations in travelling strings. British Journal of Applied Physics, Vol. 5, Issue 6, 1954, p. 224.
-
Swope R. D., Ames W. F. Vibrations of a moving threadline. Journal of the Franklin Institute, Vol. 275, Issue 1, 1963, p. 36-55.
-
Mote Jr C. D. A study of band saw vibrations. Journal of the Franklin Institute, Vol. 279, Issue 6, 1965, p. 430-444.
-
Mote C. D. On the nonlinear oscillation of an axially moving string. Journal of Applied Mechanics, Vol. 33, Issue 2, 1966, p. 463-464.
-
Thurman A. L., Mote C. D. Free, periodic, nonlinear oscillation of an axially moving strip. Journal of Applied Mechanics, Vol. 36, Issue 1, 1969, p. 83-91.
-
Ulsoy A. G., Mote Jr C. D., Szymni R. Principal developments in band saw vibration and stability research. Holz als Roh-und Werkstoff, Vol. 36, Issue 7, 1978, p. 273-280.
-
Kotera Tadashi Vibrations of string with time-varying length. The Japan Society of mechanical Engineer, Vol. 160, Issue 5, 1978, p. 1469-1474.
-
Wickert J. A., Mote C. D. Classical vibration analysis of axially moving continua. Journal of Applied Mechanics, Vol. 57, Issue 3, 1990, p. 738-744.
-
Lee S. Y., Mote C. D. Traveling wave dynamics in a translating string coupled to stationary constraints: energy transfer and mode localization. Journal of Sound and Vibration, Vol. 212, Issue 1, 1998, p. 1-22.
-
Foda M. A. Vibration control and suppression of an axially moving string. Journal of Vibration and Control, Vol. 18, Issue 1, 2012, p. 58-75.
-
Butikov E. I. Peculiarities in the energy transfer by waves on strained strings. Physica Scripta, Vol. 88, 2013, p. 065402.
About this article
The authors are greatly indebted to the National Natural Science Foundation of China (Grant No. 51305115, and Grant No. 51675150) for the support of this research.