Abstract
The concealment capability of submarine is seriously restricted by the vibration of pipe penetration piece which is an important obstacle to the development of ‘quiet submarine’. In this paper, the characteristics and structures of pipe penetration piece are analyzed. Combining with domestic and foreign achievements, the active and passive methods of piping vibration reduction were introduced, and the measures of piping vibration isolation were elaborated. It provides reference for the vibration control of pipe penetration piece.
1. Introduction
Vibration of submarine structure has been an important factor restricting the development of concealment capability of submarine. In the marine environment, the vibration of the hull usually spread to the surrounding by waves, and it can easily be detected by the enemy's sonar system. Especially in recent years, it has been difficult to achieve the requirements of concealment that relying solely on the traditional measures to control the hull vibration, because of the rapid development of sonar detection technology. So, improve submarine vibration reduction measures constantly, developing ‘quiet submarine’ quickly, has gradually become major means to improve military power for great power.
In recent years, due to the continuous development of submarine vibration damping technology, the vibration transmission between the pipeline and the bulkhead has gradually become prominent, which is an important source of hull vibration. Some studies have found that the vast majority of vibration which occurs in interior of the submarine come from mechanical equipment and pipeline fluid. Pipe penetration piece is gradually becoming an important ‘tools’ that transmit these vibration [1]. Usually, during the vibration transmission of the pipeline, the vibration of the pump or valve and the pulsation of the high temperature and pressure fluid can transmit to the hull directly through the pipeline welded on the bulkhead, which pose a threat to the survival of submarine. Therefore, it is of great significance to reduce the vibration level of the pipeline and isolate the vibration transmission of the pipeline for submarine concealment capability’s development. In this paper, the vibration characteristics and sources of the pipeline are analyzed, and the vibration reduction and isolation of the pipeline are discussed, which provide a reference for the vibration control of the pipe fitting.
2. Analysis of vibration characteristics of pipe penetration piece
Interior of the submarine is a structure with multi-chamber confined space. The internal of submarine usually has a very complex pipeline layout, and the pipeline is an important part of submarine power, cooling, water transport and drainage systems. Pipe penetration piece is the pipeline which completes the transport task through the compartments. Generally speaking, there are two sources of vibration for the pipeline. One is the pulsation excitation of the fluid in the pipe, and the other is the vibration of the pump, the valve and the auxiliary machinery [2].
In general, the pipe penetration piece is responsible for the transport of energy and momentum, and the temperature and pressure of fluid in it is usually high. In order to complete the transport task in an even better fashion, there must be some mechanical devices in the system which provide power and control, such as pumps and valves. Therefore, the flow state of the high-temperature fluid usually changes frequently due to the influence of the mechanical equipment in the whole pipeline, which produce strong pulsation excitation and cause the flow-induced vibration [3]. When the vibration parameter is accord with intrinsic parameter of pipeline, strong resonance will occur. Resonance is not only a great threat to the submarine’s concealment, it could be damage to the pipeline seriously and even cause submarine accidents. Because such vibrations are ultimately caused by the fluid in the pipe, we attribute it to the vibration of the fluid pulsation. This kind of vibration usually has two characteristics. One is greatly affected by the fluid movement state, and the other is that the frequency of it is usually higher than others [4]. As for the influence of the fluid state, because the flow in the pipeline is mostly high-temperature and high-pressure fluid, the molecular motion of the fluid is active, and the thermal shock energy is high, which make the vibration of the pipeline be more severe. Yang Yuan-long conducted research which was related to the shipping steam pipe in the literature [5] and found that the impact of such fluid on the pipeline vibration is very intense. On the other hand, in order to achieve accurate control to fluid parameters, pumps, valves and other auxiliary machinery are often active. Coupled with the structure such as elbow and joint pipe whose action area can change in a short time, the high-frequency characteristics of the vibration are more obvious and influence of it is very broad.
When the system of the pipeline work properly, the motor, pump, fluid valves and various auxiliary equipment could cause varying degrees’ vibration. Because these components connected with the pipe penetration piece directly, the vibration energy of the components can be transmitted directly to the pipeline and cause vibration. We usually refer to such vibration as pipeline mechanical vibration. Obviously, pipeline mechanical vibration is affected greatly by the vibration level of various equipment. At the same time, the damping property of the pipeline itself and the distance to the equipment can affect pipeline vibration. In the study, Li Wei-gang, Wang Jian-chun found that the mechanical vibration spectrum of the pipeline is the same as the mechanical equipment. The vibration energy mainly gathered in the middle and low frequency Range. In the process of long-distance transmission, the vibration energy is dissipated due to the impact of damp of the pipe itself [6].
Through the analysis of the vibration characteristics of the pipeline, it can be found that the main cause of pipeline vibration is flow-induced vibration, and the mechanical vibration of pipelines also can affect the pipeline.
3. Research on the method of vibration reduction of pipe penetration piece
The damping of submarine piping is similar to that of most naval vessels. It is mainly to control the vibration of piping itself, so as to reduce the vibration to a reasonable range and reduce the vibration output to the bulkhead. At present, the general pipe vibration control can be divided into active control and passive control according to the power source [7], and both of two methods have their own advantages and disadvantages. Their applications in practice are very extensive, and domestic and there are lots of research at home and abroad.
3.1. Study on the active vibration control of pipeline
Active control of pipeline vibration means that the vibration of pipelines is balanced by actuators which drove by certain control strategies based on the vibration signals, and achieve the purpose of vibration absorption finally.
In general, there are two structures of active control for pipeline vibration, one of which is a non-submerged structure. This kind of structure directly installs the device on the outer wall of the pipeline, and controls the movement of the actuator through the collected vibration signal from external environment. This method does not distinguish flow-induced vibration and mechanical vibration. Because this kind of structure does not count the fluid pulsation separately, the installation is not influenced by the small size pipeline, and it provides a convenient condition for analysis and design of the structure. Foreign scholars carry on the research in an early time because of the development advantages of materials science, testing technology and control technology. In the 1990s, Swedish scholar Maillard, et al. designed a non-submerged device whose actuators was installed on the pipe for piping, and the shape of actuators are usually annular. Coupling with radial motion of the pipe, the actuators promote fluid to fluctuate to balance the pulsation of the fluid. However, the fluctuating pressure generated by the actuator is much less than that of the pipeline fluid, so the vibration reduction effect of the device is not very obvious [8, 9], and Fig. 1 is the physical diagram of the device. After that, many foreign scholars have carried out research on them. By adjusting the design parameters and changing the method of vibration isolation, they have gradually improved the damping performance of this kind of structure, and provided reference for the design and application of immersion structure [10, 11]. Domestic scholars carry on the research later than foreigners, and mainly concentrated in the field of theoretical analysis, and the practical application is less. For example, after a detailed analysis of the acoustic field characteristics of a semi-infinite pipe acting on an active noise control system, Wu Bin, Fei Ren-yuan, etc. designed an adaptive active muffler experiment system [12]. They used the system to carry out the experiment of single-frequency silencer experiment in the low frequency range, and verify the effect of it [13]. Combining with frequency adaptive algorithm based on comb filter, Li Wan-you, Zhang Hong-tian et al. proposed an electromagnetic active vibration absorber and a new active vibration control technology. The experimental results show that the method can suppress vibrations in multiple frequency range, including fundamental frequency and harmonic frequency, and the damping effect is good [14, 15]. Taiwanese scholars Y. K. Tsai and Y. H. Lin have also designed a vibration suppression device based on the variation of the pipe shape which fluid velocity cause. The device can control the movement of two semi-arc piezoelectric actuators by capturing the deformative information of the pipeline, and finally achieve the purpose of vibration reduction [16].
Another type of submerged structure is mainly directed against the flow-induced vibration of the pipeline vibration. Immersion devices are usually installed inside the pipeline, and it operates or not decided by parameters of the fluid. The control unit will send signals to actuators if it is necessary to reduce the vibration. Ouyang Ping-chao, Liu Hong-mei and others have conducted research on the structure. They have proposed a distributed fluid pulsation method of active control to solve the problems that it is difficult to arrange the location of piping single point vibration sensor and deal with the standing wave in pipeline fluid. They control the vibration using several pressure sensors and active valves in the method, in order to achieve the effect of micro-control. The experiment shows that the vibration attenuation can reach more than 10 dB [17]. In allusion to cyclical characteristics of fluid pulsation, they have also proposed an adaptive feedforward control method for on-line frequency estimation. It gets information of frequency according to the pulsation signal of sensors. Based on the information, the control of the fluid pulsation is realized, and experimental shows that the result is good [18]. The structure usually needs to work in the pipeline, so it is difficult to be put into use because of the restriction of the pipe size.
3.2. Passive control technology of pipeline vibration
Passive control of pipe vibration means that controlling vibration by changing the material impedance or dissipation characteristics, and measures which are commonly used are that adds vibration absorption materials, increase flexible joints, install dampers and connect attenuator [19].
The simplest and the most effective method of passive control of pipeline vibration is that put a layer of damping materials on the outer wall of the pipe directly, and it is also called pipe surface damping treatment [20]. 90s of last century, foreign scholars Fang and Lyons have found that there was axial vibration in the fluid-filled pipe all the time in the research of damping effect of materials. That makes the method of putting a layer of damping materials on the outer wall is effective to reduce the vibration of Pipeline system [21]. Du Dong-ju and Liu Ai-hua have also carried out a theoretical analysis of pipeline surface damping detailed in literature [22], and they deduced the calculation formula of the structural loss factor of the pipeline after damping treatment. At the same time, they also used the formula to analyze the damping effect of material SA-3. It is found that the characteristics of the material are adapt to the submarine in the high-temperature damping zone greatly. At present, increasing flexible joints is also an effective measure to control the pipeline vibration. It can not only isolate and attenuate the vibration and noise of the pipeline structure, but also can compensate the vibration and shock caused by the equipment and pipeline system [23]. Is the common method of reducing pipeline vibration for the ship and other military equipment. In the study of flexible joints, the Institute of Vibration and Noise of Naval University of Engineering has been at the forefront of the country. The shipboard flexible joints that belongs to JYXR series has successfully broken the technical blockade of developed countries in Europe, America and Russia. It overcomes the difficulties such as balanced design, utilization of aramid fiber and homogeneous winding technology. It provides a technical support for the ship piping system vibration and shock design [24-28]. As a general vibration damping device, the damper also has a good effect in the vibration control of the pipeline, and it is also paid close attention to by scholars in China. Aiming at the requirement of impact resistance, Ja Jiu-hong and Zhang Zhen-hua designed a new type damper. They used the single degree-of-freedom system consisting of a numerical simulation drop table and a damper do the experiment, and found that nonlinearity of it is obvious, and the buffered characteristic is good [29]. Zeng Sheng and Ren Yie conduct research on vibration attenuation of the existing pipe system, and designed a ring-shaped damper. The experimental result showed that the device can greatly reduce the steady vibration of piping system. It is confirmed that the way of vibration reduction is effective and practical [30]. Xie Po-an, Wang Qiang established an acoustics model of accumulator by transfer matrix method. The insertion loss formula of accumulator was deduced, and the effect of accumulator on the attenuation of fluid fluctuation was validated by experiments too [31]. Li Lang and Wang Hai-tao studied on the factors of damping of the bladder-type accumulator pipeline. Basing on the mathematic model of the bladder-type accumulator with the influence parameters, they found that the pre-charge pressure of the accumulator, the length, diameter and other parameters of pipeline impacted on the performance of the accumulator significantly [32]. Cao Shu-ping and Luo Xiao-hui proposed a model of an adaptive accumulator loop which can be used to adjust the flow area of the accumulator pipeline by the pressure sensor that acquires the steady-state pressure information of the system. The model can also change the natural frequency of the accumulator to achieve the effect of absorption of pressure pulsation, and found that the adaptability of loop model is reasonable by tests and simulation analysis [33].
4. Study on the isolation method of pipe penetration piece
Although the method of vibration damping can effectively control the vibration of the pipeline, the effect of the vibration control of the hull is not as obvious as that of the pipe vibration isolation method. In contrast, the isolation of the piping vibration can reduce the vibrations that are actually transmitted to the bulkhead through the piping, and not only acts on the vibrations of the piping. At the same time, the isolated vibration requires neither an external power source nor the structure whose function is that counteract vibration. In general, the two methods are used together in the submarine, and the anti-vibration measures of the piping in the pipeline are the final link of the vibration control in most cases [34].
The most common method of isolation is to change the way of connection, which is that replace the rigid connection with an elastic connection. In present, the main form of it is the type of sleeve and isolator. Pipe Penetration Piece of sleeve mainly composes with elastic damping materials and structural sleeve. Damping materials are clamped in the middle by the sleeve and pipe, and so that it has a certain pre-tightening pressure, while pipe can get some support. When the pipe vibrates, pipe, materials and the sleeve can form a vibration isolation system. Basing on the system, it can complete the vibration of the elastic isolation and continue to dissipate the vibration energy, so that vibration cannot be transmitted to the bulkhead. Because this kind of structure is simple, the effect is obvious and attract the domestic scholars’ attention. Shen Zheng-fan and Wu Sheng-min once have studied the vibration isolation effect of sleeve pipe penetration piece, and through the finite element simulation analysis of the structure of the ship’s hydraulic system, it was found that the level of vibration acceleration respectively was 106 m/s2and 104 m/s2 for the same point on the bulkhead [35]. From the perspective of design, Peng Yun-fei and He Hai-yang stated the principle of the damping parameters by analyzing the mechanism of vibration absorption and simulation design of the sleeve pipe penetration piece. It provided a reference for the development of a new type of pipe penetration piece with excellent damping performance [36]. In addition, Hu De-fang and Jin Xiang conduct research on structural design of pipe penetration and analyzed the impact of vibration materials’ location [37]. LI Guang-lei conduct research on the pipe penetration piece used in high-temperature environment, and designed a fitting structure of pipe with water circulation cooling system. Three-dimensional model of the pipe penetration piece is shown in Fig. 2 [38]. Qiu Da-lu is the flexible graphite as a vibration damping material used in the cabin wear pipe structure, and achieved good damping effect [39]. It is different from sleeve-style pipe penetration piece that materials of vibration isolation are made to be an isolator in the sleeve-style pipe penetration piece. The size of it is relatively flexible, and it is suitable for large-scale pipeline.
Fig. 1Real figure non-submerged device
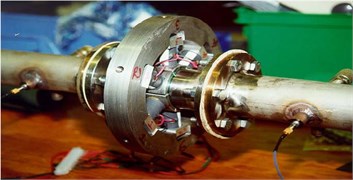
Fig. 2Three-dimensional model of pipe penetration piece
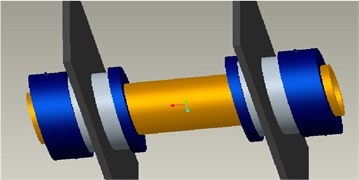
5. Summary and Prospect
In this paper, the vibration characteristics of the pipeline are analyzed firstly, and then combining with the research of domestic and foreign scholars and the characteristics of the pipeline’s vibration, the method of vibration reduction and isolation are introduced. It provides reference for the development and analysis of pipe penetration piece.
Through the research of this paper, it can be found that as an important measure of “quiet type” submarine damping, the vibration analysis and control of the pipeline will be a spotlight in related fields in the future. In the meantime, along with the development of material science and control technology, the active control of micro vibration and the design of high temperature damping materials will be the main direction of pipeline vibration control.
References
-
Shang G. Q., Guo Y. S. Study on theory and application of ship vibration isolation technology. Ship Science and Technology, Vol. 28, Issue 1, 2006, p. 15-18.
-
Dai A. D., Chen G., Zhu S. J. Review on control measures of ship pipeline vibration and noise. Ship and Ocean Engineering, 2001, p. 75-77.
-
Guo T. Study on Flow-Induced Vibration and Noise of Pipeline. Huazhong University of Science and Technology, Wuhan, 2012.
-
Liang X. D. Analysis and control strategy of high frequency vibration in ship piping. Noise and Vibration Control, Vol. 29, Issue 3, 2009, p. 101-103.
-
Yang Y. L. Prediction of thermal shock characteristics of steam release pipes in ship steam regenerator. Journal of Chemical Industry and Engineering, Vol. 66, Issue 11, 2015, p. 4432-4434.
-
Li W. G., Wang C. J., Li S. B. Analysis and control of vibration and noise of submarine hydraulic system. Machine Tool and Hydraulics, Vol. 39, Issue 14, 2011, p. 70-105.
-
Ling X. D. The significance of pipeline vibration and noise control to ship noise control. 12th Symposium on Underwater Noise of Ships, 2009, p. 14-15.
-
Maillard J., Lago T. L., Winberg M., et al. Fluid wave actuator for the active control of hydraulic pulsations in piping systems. IMAC-XVII, International Modal Analysis Conference, 1999.
-
Maillard J. Active Control of Pressure Pulsation in Piping Systems. University of Karlskrona/Ronneby, Ronneby, 1998.
-
Kartha S. C. Active, Passive and Active/Passive Control Techniques for Reduction of Vibrational Power Flow in Fluid Filled Pipes. Virginia Polytechnic Institute and State University, 2000.
-
Lenz J. Three dimensional vibration absorber for pipeline vibrations. International Compressor Engineering Conference, 2008, p. 1-8.
-
Wu B., Fei R. Y., Zhou D. S., et al. Study on acoustic characteristics of active control of pipeline noise Ⅰ theoretical section. Journal of Beijing University of Technology, Vol. 29, Issue 4, 2003, p. 411-413.
-
Wu B., Fei R. Y., Zhou D. S., et al. Study on acoustic characteristics of active control of pipeline noise Ⅱ experimental section. Journal of Beijing University of Technology, Vol. 30, Issue 1, 2004, p. 31-34.
-
Li W. Y., Zhang H. T., Liu Z. G. experimental study on active vibration absorbing technique of ship pipeline vibration. Noise and Vibration Control, Vol. 6, 1998, p. 10-13.
-
Li W. Y., Zhang H. T., Yang T. J. Experimental study on semi - active control of ship pipeline vibration. Journal of Harbin Engineering University, Vol. 20, Issue 5, 1999, p. 11-15.
-
Tsai Y. K., Lin Y. H. Adaptive modal vibration control of a fluid-conveying cantilever pipe. Journal of Fluids and Structures, Vol. 11, Issue 5, 1997, p. 535-547.
-
Ouyang P. C., Jiao Z. X., Liu H. M. An active control method of distributed hydraulic fluctuation. Journal of Beijing University of Aeronautics and Astronautics, Vol. 33, Issue 9, 2007, p. 1060-1063.
-
Ouyang P. C., Jiao Z. X., Liu H. M. Active control of fluid pulsation based on bypass flooding. Acta Aeronautica ET Astronautica Sinica, Vol. 28, Issue 6, 2007, p. 1302-1305.
-
Wang Y. L., Wang Z. D., Song Z. F. Present situation and development of vibration and noise control technology of submarine pipeline system. Ship Science and Technology, Vol. 30, Issue 6, 2008, p. 34-38.
-
Wang Y. P., Zhang D. C., Yu Y. F. Research on noise reduction technology of pipeline damping in tonghai system. Noise and Vibration Control, Vol. 4, 2010, p. 40-43.
-
Fang J., Lyons G. J. Structural damping of tensioned pies with reference to cables. Journal of Sound and Vibration, Vol. 193, Issue 4, 1996, p. 891-907.
-
Du D. J., Liu A. H., Huang J. D. Application of damping vibration reduction in submarine pipeline. China Shiprepair, Vol. 14, Issue 1, 2004, p. 16-19.
-
Chai X. W. Current status and development of flexible pipe connection technology for ships. Noise and Vibration Control, Vol. 5, 2007, p. 13-16.
-
He L., Shuai C. G., Zhou W. Research on JYXR series shipboard flexible joint. Ship Science and Technology, Vol. 28, Issue S2, 2006, p. 121-124.
-
Zhang X. P., He L., Zhou W. Winding model of flexible pipe with balanced arc. Ship and Ocean Engineering, Vol. 1, 2012, p. 118-123.
-
Zhou W., Shu L. H., Ye W. Study on mechanical model and its balance of curved flexible joint. Ship and Ocean Engineering, Vol. 31, Issue 2, 2009, p. 73-75.
-
Zhang X. P., He L., Zhou W. Study on the balance of Kevlar fiber reinforced flexible tube. Journal of Vibration and Shock, Vol. 31, Issue 8, 2012, p. 70-73.
-
Chen G., Zhu S. J. Discussion on rationality of testing device for vibration isolation effect of flexible joint. Journal of Naval University of Engineering, Vol. 14, Issue 5, 2002, p. 58-59.
-
Jia J. H., Zhang Z. H., Du J. Y. Design and experimental study of a new type of damper. Journal of Vibration and Shock, Vol. 27, Issue 2, 2008, p. 69-71.
-
Zeng S., Ren Y., Cheng T. Damping vibration of pipeline system by using tuned mass damper. Vibration Test and Diagnosis, Vol. 32, Issue 5, 2012, p. 823-826.
-
Xie P. A., Wang Q. Study on the effect of accumulator on the fluctuation of pipeline fluids. Noise and Vibration Control, Vol. 4, 2000, p. 2-5.
-
Li L., Wang H. T., Gong L. H. Parameter analysis and experiment of absorbing pressure fluctuation of cylindrical accumulator. Chinese Hydraulics and Pneumatics, Vol. 7, 2012, p. 3-6.
-
Cao S. P., Luo X. H., Hu J. H. Study on adaptive accumulator loop for absorbing pressure fluctuation. China Mechanical Engineering, Vol. 19, Issue 6, 2008, p. 671-674.
-
Kong J. Y., Li G. F., Hou N. Study on vibration and noise control of submarine. Noise and Vibration Control, Vol. 5, 2006, p. 1-4.
-
Shen Z. F., Wu S. M., Zhang Y. Finally, designed vibration isolation and ventilation fittings based on finite element simulation. Ship Science and Technology, Vol. 35, Issue 12, 2013, p. 73-77.
-
Peng Y. F., He H. Y., Li S. Study on shock absorption mechanism of pipeline elasticity passing through cabin and simulation analysis. Ship Science and Technology, Vol. 33, Issue 8, 2011, p. 119-122.
-
Hu D. F., Jin X., Liu S. G. Design of pipe element passing through bulkhead with elastic installation. China Shiprepair, Vol. 52, Issue 2, 2011, p. 146-153.
-
Li G. L. The Cooling and Vibration Attenuation Design of the High Temperature and High Pressure Pipe Peneration Piece. Harbin Engineering University, Harbin, 2012.
-
Qiu D. L. Dynamic Analysis of the Ship Pipes System. Harbin Engineering University, Harbin, 2012.