Abstract
Bearings are widely used in rotating machines. Its health status is a significant index to indicate whether machines run continually or not. Detecting the bearing defects timely is very important for the maintenance decision making. In this paper, a novel bearing defects detection method based on EMD and Fractal Dimension is developed. The original data is decomposed into a set of intrinsic mode functions (IMFs) using EMD, and the fractal dimension of IMFs which contains bearing fault characteristic information are calculated, and these characteristic parameters are used to identify bearing fault types. The effectiveness of this methodology is demonstrated using experimental data.
1. Introduction
Researchers pay great attention to rolling element bearings because they are key components of mechanical systems and always play important roles in mechanical transmission. Proper functioning of mechanical systems depends on the smooth and normal running of the bearings. Therefore, bearing fault diagnosis is very important to prevent the machine failure and save costs. Generally, two techniques are commonly used to diagnose the bearing faults: model-based methods, and data-driven methods. In model-based methods, the goal of signal models (such as wavelet analysis [1], morphological theory [2], etc.) are to find the fault frequencies of different locations (like inner race, out race, ball, and cage). In practice, it is impossible to store all the vibration signals for vibration analysis. On the contrary, data-driven methods can diagnose the bearing faults using features extracted from the vibration signals without the demand to store a large amount of data.
Boutros and Liang [3] developed a discrete Hidden Markov Model (HMM) to determine the fault location and classify the fault severity. In this paper, energies of five frequency bands were used as the fault features. Kang and Zhang [4] used a continuous HMM to detect the incipient faults. Like HMM, Support Vector Machine (SVM) [5-7] and Artificial neural network (ANN) [8, 9] were widely used in bearing fault diagnosis. In these models, fault features are the key factors affecting the model performance. Therefore, in bearing fault diagnosis, extracting good features is a more important thing than model selection. Recently, many researchers pay main attention to the fault feature extraction methods. For bearing fault diagnosis, the research goal is to enhance the impulsive contents in the signal and depress the noise. Many novel methods such as Spectral Kurtosis [10, 11], Minimum Entropy Deconvolution (MED) [11], etc. were developed for bearing fault diagnosis. Recently, an adaptive morphological gradient lifting wavelet was proposed in [12] for detecting the bearing defects. In this paper, the updating filters can be appropriately selected based on the local features in the signal. This enabled the fault characteristic frequency of bearing can be detected effectively. Morphology theory was used to diagnose the bearing fault and attracted considerable attention for a long time. Raj and Murali [13] proposed a new algorithm in which the structuring elements was selected based on kurtosis. This enabled the morphological operators more robust for bearing fault diagnosis.
However, features extracted using above mentioned methods are very effective to determine the fault location under the assumption that training sets and test sets are collected form the same fault severity bearing produced by the same factory. In engineering practice, there will have many severity levels fault bearings waiting to be classified. Therefore, the training sets and test sets will be different. Some traditional feature extraction methods will be ineffective in this circumstance. In order to solve this dilemma, this paper developed a new fault diagnosis method based on Empirical Mode Decomposition and Fractal Dimension.
The remaining sections of this paper are organized as follows. In Section 2, framework of the proposed method is introduced. Section 3 describes the experiment and applies the proposed method to bearing defects detecting. Finally, conclusions are given in Section 4.
2. Framework of the proposed method
2.1. Empirical mode decomposition
Hilbert Huang Transform (HHT) is a new signal processing method which developed by Huang et al. [14, 15]. It contains two parts: EMD and Hilbert spectrum analysis method. As the kernel of HHT, EMD has been developed and widely used in fault diagnosis of rotating machinery recently. Using EMD, the complex signal can be decomposed into a set of complete, simple and almost orthogonal components named intrinsic mode functions (IMF). The IMFs represent the natural oscillatory mode embedded in the signal and work as the basis functions, which are determined by the signal itself. And the IMFs should satisfy the following two conditions: (1) In the whole data set, the number of extreme and the number of zero-crossings must either be equal or differ at most by one; and (2) At any point, the mean value of the envelope defined by local maxima and minima must be zero. Namely, local signal is symmetrical about the time axis.
EMD is developed based on the assumption that any signal consists of many different IMFs. The procedures of decomposing a given signal x(t) to different IMFs can be categorized into the following steps. First, identify all the local extreme from the given signal and then connect them with a cubic spline line as the upper envelope lmax(t). Second, repeat the first step for the local minima to produce the lower envelope lmin(t). The upper and lower envelopes should cover the entire signal between them. Third, compute their mean as m1(t) and the difference between the signal x(t) and m1(t) is h1(t):
Ideally, after the sifting operation of Eq. (1), h1(t) should be the first IMF. The construction of h1(t) described above seems to satisfy all the requirements of IMF. However, during the practical process, the theoretical upper envelope lmax(t) and lower envelope lmin(t) are very difficult to calculate. In addition, any little inflection points of the monotonous signal can be transformed to new extrema. And these new extremas should be contained by the next sifting operation. To solve this dilemma, Huang et al. repeated the sifting process of Eq. (1) as many times as required to reduce the extracted signal to an IMF. Therefore, the fourth step is to repeat the sifting process by treating h1(t) as the original signal as follows:
The sifting process will be repeated k times until h1k(t) becomes a true IMF, that is:
Then, make c1(t)=h1k(t), and can be seemed as the first IMF. Remove c1(t) from the signal x(t), namely:
And generate the residue signal r1(t). Treating r1(t) as a new original signal and repeating the same sifting process above, the second IMF can be got. Similarly, a series of IMFs (ci(t) (i=1, 2,…, n)) can be obtained until the final residue rn(t) is monotonous. Then the original signal x(t) can be reconstructed as:
The IMFs c1, c2,…, cn represent different frequency bands ranging from high to low. The frequency components contained in each frequency band are different and they change with the variation of the original signal x(t), and rn(t) represents the central tendency of signal x(t).
2.2. Fractal dimension
The vibration signals of mechanical equipment always have non-linear. Fractal theory is an effective means to deal with this dilemma. As an essential parameter in fractal theory, fractal dimension (FD) has been widely used in many areas of science, including the capability of quantitative measurement for fractal characteristics of nonlinear systems and the ability of space-filling capacity measurement for signals. In mechanical fault diagnosis, the influences of nonlinear factors for mechanical vibration signals are different under diverse fault status. Fractal dimension describes the fault features of mechanical system and recognizes the fault status of mechanical device effectively. In the field of vibration signal processing, fractal box dimension and correlation dimension are two parameters that usually used by researchers. However, the calculate process of correlation dimension is very complicated. So this paper mainly studies the fractal box dimension.
Assume that Y⊂Rn, Y≠Φ, if there are N(ε) hypercube can cover Y, then:
Eq. (6) is the definition of fractal box dimension.
2.3. The bearing defects detecting method
The flow chart of the method based on EMD and FD which proposed in this paper is shown in Fig. 1. It consists of the following procedural steps. (1) Obtain several IMFs by EMD decomposition. (2) Compute out the FD of each IMF. (3) Gain the detecting result.
Fig. 1Flowchart of the proposed method
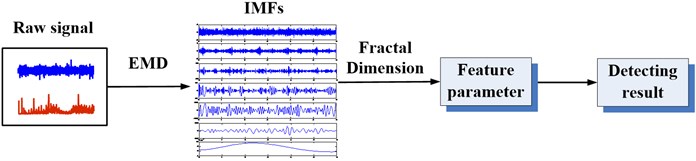
3. Case study
3.1. Experimental setup and data acquisition
A mechanical test bed in the RCM laboratory of Mechanical Engineering College is used in this research to validate the effectiveness of the proposed method in this paper. The gearbox is driven by a 4 KW three phase asynchronous drive motor. In addition, the speed and torque sensors are used to acquire the speed and torque information, a magnetic powder brake is utilized to provide load. These components are connected by couplings, as shown in Fig. 2. The sampling frequency of this experimental system is 20 kHz.
Bearings are defected after experiment. This paper chooses four states to analyzing. The four states are normal state, ball defect, inner face defect and outer face defect, as Fig. 3 shows.
Fig. 2The test rig
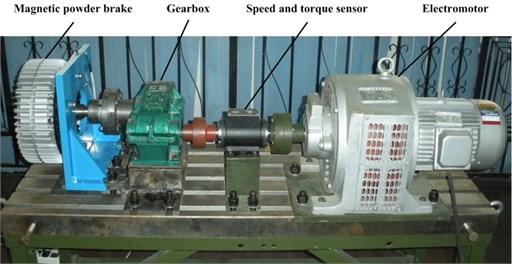
Fig. 3The states of bearings

3.2. Results analysis and discussion
The vibration signal acquired from the test rig is utilized to analyzing according to the method proposed in Section 2.3. Fig. 4 is the detecting results using the method proposed in this paper. It can be seen from the figure that the classification result is very obvious.
Fig. 4Detection results using the proposed method
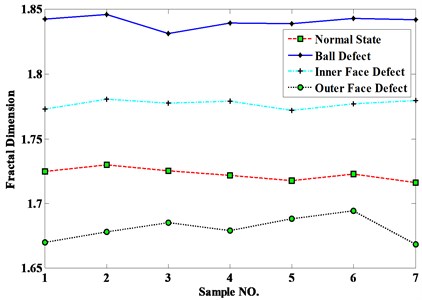
In order to validate the necessity of EMD, this paper analyzes the data but without processed by EMD and the results can be seen in Fig. 5. The detecting results of normal state, inner face defect and outer face defect are confused. So, the necessity of EMD can be validated.
In order to validate the effectiveness of method proposed in this paper, a method based on wavelet and fractal dimension is utilized. It can be seen from Fig. 6 that all of the four states are confused seriously. So, the effectiveness of the method can be validated.
Fig. 5Detection results without EMD
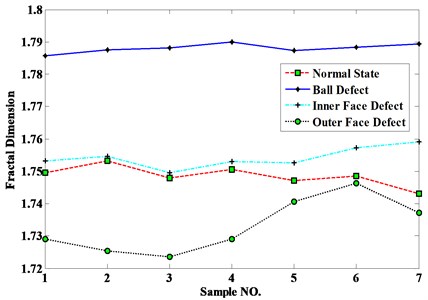
Fig. 6Detection results using wavelet and FD
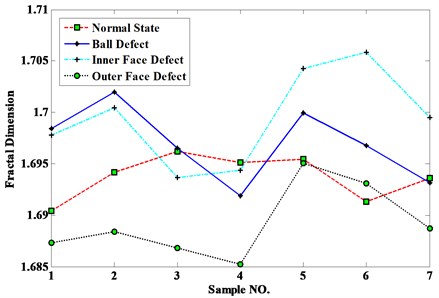
4. Conclusions
In this paper, the dilemmas of bearing defects detection are point out firstly. Then a novel method based on EMD and FD is proposed to solve this problem. In the proposed method, IMFs are obtained after the original vibration signal processed by EMD first. Then compute the fractal dimensions of IMFs. Finally, gain the detecting results through compare all the fractal dimensions of four states. A gearbox test rig is established and four kinds of states are utilized. Furthermore, the effectiveness of the proposed method and the necessity of EMD are validated by experimental data.
References
-
Jiang Y. H., Tang B. P., Qin Y., Liu W. Y. Feature extraction method of wind turbine based on adaptive Morlet wavelet and SVD. Renewable Energy, Vol. 36, Issue 8, 2011, p. 2146-2153.
-
Wang J., Xu G. H., Zhang Q., Liang L. Application of improved morphological filter to the extraction of impulsive attenuation signals. Mechanical Systems and Signal Processing, Vol. 23, Issue 1, 2009, p. 236-245.
-
Boutros T., Liang M. Detection and diagnosis of bearing and cutting tool faults using hidden Markov models. Mechanical Systems and Signal Processing, Vol. 25, Issue 6, 2011, p. 2012-2124.
-
Kang J. S., Zhang X. H. Application of hidden Markov models in machine fault diagnosis. Information – An International Interdispilinary Journal, Vol. 15, Issue 12, 2012, p. 5829-5838.
-
Kumar H., Kumar T. A. R., Amarnath M., Sugumaran V. Fault diagnosis of antifriction bearings through sound signals using support vector machine. Journal of Vibroengineering, Vol. 14, Issue 4, 2012, p. 1601-1606.
-
Konar P., Chattopadhyay P. Bearing fault detection of induction motor using wavelet and support vector machines (SVMs). Applied Soft Computing, Vol. 11, Issue 6, 2011, p. 4203-4211.
-
Abbasion S., Rafsanjani A., Farshidianfar A., Irani N. Rolling element bearings multi-fault classification based on the wavelet denoising and support vector machine. Mechanical Systems and Signal Processing, Vol. 21, Issue 7, 2007, p. 2933-2945.
-
Yu Y., Yu D. J., Chen J. S. A roller bearing fault diagnosis method based on EMD energy entropy and ANN. Journal of Sound and Vibration, Vol. 294, Issues 1-2, 2006, p. 269-277.
-
Wang H. Q., Chen P. Intelligent diagnosis method for rolling bearing faults using possibility theory and neural network. Computers and Industrial Engineering, Vol. 60, Issue 4, 2011, p. 511-518.
-
Chen B. Q., Zhang Z. S., Zi Y. Y., He Z. J., Sun C. Detecting of transient vibration signatures using an improved fast spatial-spectral ensemble kurtosis kurtogram and its applications to mechanical signature analysis of short duration data from rotating machinery. Mechanical Systems and Signal Processing, Vol. 40, Issue 1, 2013, p. 1-37.
-
Sawalhi N., Randall R. B., Endo H. The enhancement of fault detection and diagnosis in rolling element bearings using minimum entropy deconvolution combined with spectral kurtosis. Mechanical Systems and Signal Processing, Vol. 21, Issue 6, 2007, p. 2616-2633.
-
Li B., Zhang P. L., Mi S. S., Hu R. X., Liu D. S. An adaptive morphological gradient lifting wavelet for detecting bearing defects. Mechanical Systems and Signal Processing, Vol. 29, Issue 5, 2012, p. 415-427.
-
Rai A. S., Murali N. Early classification of bearing faults using morpological operators and fuzzy inference. IEEE Transactions on industrial electronics, Vol. 60, Issue 2, 2013, p. 567-574.
-
Huang N. E., Shen Z., Long S. R. The empirical mode decomposition and the Hilbert spectrum for nonlinear and nonstationary time series analysis. Proceeding of the Royal Society of London, Series A, Vol. 454, 1998, p. 903-995.
-
Huang N. E., Shen Z., Long S. R. A new view of nonlinear water waves: The Hilbert spectrum. Annual Review of Fluid Mechanics, Vol. 31, 1999, p. 417-457.