Abstract
Heavy vehicles are the most important transportation tools. In order to study deeply the fatigue damage problem of the heavy vehicles, we propose favoring the virtual simulation method. Firstly, the definition and development status of fatigue damage is introduced. Then we pay more attention to the fatigue damage simulation research of heavy vehicle, especially the finite element analysis and fatigue life prediction by related software. Some findings are introduced to be the references for researchers. Fatigue damage virtual simulation research on heavy vehicle is correct, convenient, simple and low cost by the verification of the real vehicle test.
1. Introduction
With the sustained and rapid development of the national economy, the transportation vehicles are developing to the direction of the high-speed and heavy, and the heavy vehicle structure fatigue damage and fracture caused by the accident will cause huge property damage and casualties. According to statistics, 70 % of the vehicle components damage is caused by the fatigue damage and fatigue damage is the main damage forms of vehicle structure, especially for the heavy vehicle, due to its high loading mass and large vertical acceleration, in the operation process is more easily leading to damage to the pavement and its spare parts, so the vehicle reliability and durability with fatigue strength and fatigue life as the main content become the quality evaluation basis of heavy vehicle [1].
As early as the beginning of 1980s, the U.S. House of Representatives Committee on Science and Technology conducted a large-scale investigation about the damage caused by the fracture, found that the vehicle industry's fracture damage amounted to more than $125 billion a year. In recent years, the total sale of heavy vehicle exceeds 180 million in our country, the economic losses caused by fatigue damage due to the factors of design and the use environment will be enormous. At the same time, it will cause a large number of casualties and bad social influence. Obviously, the fatigue damage of heavy vehicles has become an important issue that affects the safety of transportation and the development of the society.
2. The definition and development situation of fatigue damage
2.1. The definition of fatigue damage
The fatigue is the process of producing permanent cumulative damage of the materials in one or several positions when the materials are acted on the cyclic stress and strain, after the number of cycle times, the crack or sudden fracture occur. The fatigue life, or the stress or the cyclic times of the strain of the materials fatigue failure, which is the subject that designers and engineers pay close attention to, and is also related to the majority of users. However, it is a very difficult problem to calculate the fatigue life under the action of complex fatigue loads.
2.2. The development situation of fatigue damage
With the rapid development of computer application technology and finite element numerical calculation theory and its application, the development trend of life prediction is to use the virtual technology of the computer to realize the life prediction of components. With the rapid development of CAD/CAE technology, as well as the further improvement of the theory of computational mechanics, CAE technology has been successfully applied to the structural design of various engineering departments. Computer aided design (CAD) can be used to make parts of the geometric models. Computer aided engineering (CAE) and then can be used to carry out finite element analysis. For the fatigue, if loading history, boundary condition and material properties known, we can use the finite element method to analyze the stress and strain of the established virtual geometric models, based on the stress and strain, combined with relevant theory to analyze the fatigue life, in order to obtain a virtual model of fatigue life distribution.
3. The fatigue damage simulation research of heavy vehicle
In recent decades, the virtual analysis has been widely used in developed countries, and it has just started in China. In order to improve the international advanced level in a short period of time, we should introduce and promote the virtual fatigue life analysis.
3.1. CAD and finite element analysis of heavy vehicle structure
For heavy vehicle structure, Building the models by CAD has been the most commonly using method, which is the basis of else analysis. More commonly used modeling software includes Pro/E, UG, CATIA, Solidworks etc.
Finite element analysis (FEA) is a kind of modern computing method for the rapid development of structural mechanic’s analysis. It is widely used in machinery, electrical machinery, and so on, almost all of the scientific research and engineering technical field. Common general-purpose finite element software, including MSC.Nastran, LUSAS, Ansys, Abaqus, LMS-Samtech, Algor, Nastran, Femap/NX, Hypermesh, Multiphysics, COMSOL, FEPG, etc.
There are many researchers studying FEA. The FEA model of the double intermediate shaft transmission case is built by applying Hypermesh software through the reasonable simplification, and the contact nonlinear finite element theory is adopted to analyze the strength of the transmission case by considering the influence on the case strength by gears, bearings and gear shafts [2]. Gu Xuesong takes the FEA as the means, the study of the equilibrium axis static strength under fixed load, based on Hypermesh/Radioss, the static strength analysis and calculation of the platform are carried out to study the reliability of the balance axle housing [3]. Zhu et al. establishes the FEM of the inducer by Hypermesh software, and the calculation of the structural strength is carried out [4]. In addition, they analyze the structural strength of a certain type of track based on FEM, the largest deformation and the largest stress are shown in Figure 1 [5].
Fig. 1The largest stress and deformation nephograms
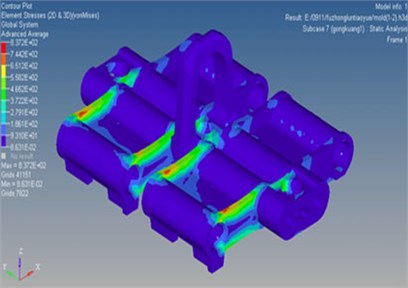
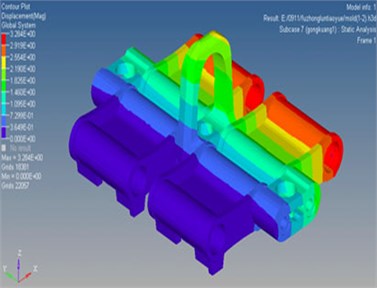
3.2. Fatigue damage virtual simulation of heavy vehicle structure
As we all known, real vehicle fatigue damage test has many shortcomings, such as the analysis process depends on experience, longer time consuming and more input. So, virtual simulation analysis methods become the most popular way.
Ju et al. use the ncode GlyphWorks 9.0 software, and the average stress amplitude of the 6 measuring points of the frame is calculated by rain flow counting and statistical analysis [6]. Yu et al. use the FE-SAFE software to obtain the number of breaks of rear axle after calculating the fatigue strength, and open the fatigue stress image in ABAQUS, to determine the fatigue vibration frequency of the break occurrence is 96.038 times, and the fatigue life of the connection position of the spring plate with middle axle is the smallest [7, 8]. Liu et al. analyze the fatigue strength of fracturing truck frame in multiple operating conditions, the analysis of fracturing truck’s fatigue life is conducted in five operating conditions, including tire suspension, road bumping, braking, ordinary pressure vibration impact and high pressure vibration impact [9]. Zhao et al. analyze the fatigue life of the bracket by simulation, based on the S-N method, the sine wave load spectrum and Radioss tool. The results show that the support of the steering device meets the requirements of static strength, but there are some problems with poor local life and poor consistency [10]. Chen et al. study a method to evaluate fatigue life of the main frame. Based on the finite element analysis data, the strain gauge is pasted, and the stress measurement system is set up, the strain time history of field and road condition is measured, and the strain data are preprocessed. The stress and dynamic load characteristics are analyzed, and the nCode Software complete fatigue life prediction [11]. Gao et al. find out the parts of stress concentration and fatigue failure according to fatigue property data and fatigue damage model based on FE-Safe software, then get the result of fatigue analysis [12]. Li et al. establish the finite element model of the frame and analyze its static character. Then by setting time series and material parameters, choosing S-N curve fatigue design and static analysis method, and adopting the nCode Design-Life, which is a specialize software, fatigue reliability analysis of the frame is conducted. Meanwhile, fatigue nephograms and fatigue life of every node are obtained. The nephograms show that the fatigue failure position and life of this Semi-Trailer frame [13]. Mi et al. taking dynamics analysis results as random load of fatigue life analysis of rear axle housing, fatigue life contours are obtained under normal conditions and the minimum life meets the engineering requirement.
Fig. 2Fatigue life prediction of the control arm
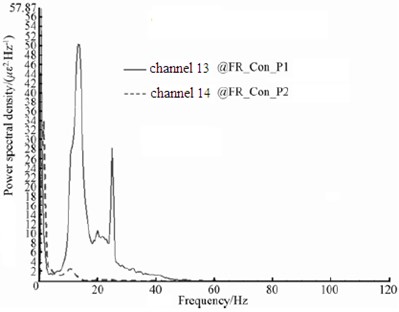
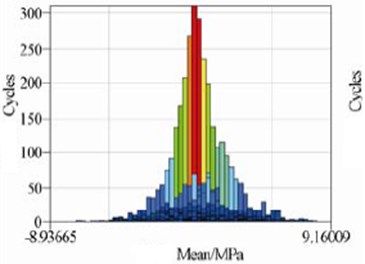
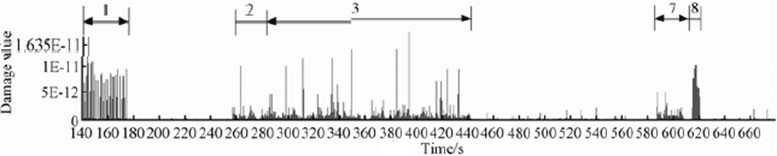
For the purpose of studying the sensitivity between load change and fatigue life, the impact of fatigue life under amplitude changes of the three loads is contrastively analyzed, which gets that the load of rear tie rod and suspension have greater impact on fatigue life of rear axle housing. Otherwise, the change of load frequency also plays a great role in fatigue life. The results show that the change of load frequency has a greater influence on fatigue life of rear axle housing than the change of load amplitude [14]. Y.C. Liu et al. study the fatigue damage of the control arm and the life prediction, the control arm measured point load PSD analysis, the load mean distribution on measured point and the fatigue damage value and distribution of test points etc. are processed by the virtual simulation and shown in Figure 2 [15, 16].
4. Conclusions
Nowadays, virtual simulation analysis has been the most important studying method in the heavy vehicle fatigue damage field. Especially the FEA and the fatigue life calculation by related software are key steps. Moreover, by the experimental verification of the real vehicle, the simulation analysis is more accurate, convenient, and can save a lot of cost. In the future, the more advanced simulation research will make greater contributions for the society.
References
-
Sun L., Liu Y. C. Review of vehicle-road vertical coupling. 2nd International Conference on Consumer Electronics, Communications and Networks (CECNet), 2012, p. 2827-2830.
-
Kang Y. P., Huo F. X., Wei D. Y., Wang C. M. Finite element analysis and experimental verifications of the transmission case strength. Journal of Machine Design, Vol. 28, 2011, p. 21-23.
-
Gu X. S. Finite element analysis of commercial vehicle balancing shaft shell. Automobile Technology, Vol. 4, 2000, p. 19-20.
-
Zhu X. G., Gu L. Structure strength analysis on idler wheel of tracked vehicle. Journal of Taiyuan University of Technology, Vol. 46, 2015, p. 274-277.
-
Zhu X. G., Gu L., Yang C. S., Zhao F. Structure strength analysis of a certain type of track based on FEM. Manufacturing Automation, Vol. 37, 2015, p. 44-46.
-
Ju B., Li J. W., Liu D. W. Study on the load spectrum of the front discharge concrete-mixer transportation truck frame. Journal of Qingdao University, Vol. 30, 2015, p. 47-51.
-
Yu H., Yang H. P., Liu Z. E., Yan F. W. Fatigue life analysis of truck axle load. Journal of Wuhan University of Technology, Vol. 38, 2014, p. 667-671.
-
Deng G. H., Li Y., Yang E. C., Ou J., Zhang Y. Body structure strength and fatigue analysis on the gear-box of heavy vehicle. Journal of Chongqing University of Technology (Natural Science), Vol. 30, 2016, p. 12-16.
-
Liu J., Xiao L. S., Wu H. H., Liu Z. Y., Pang H., Xiao W. S. Analysis of the fatigue life of oilfield fracturing truck frame in multiple operating conditions. China Petroleum Machinery, Vol. 42, 2014, p. 75-78.
-
Zhao W. Y., Gu X. S., Wang K., Wei L., Cao Z. Q. Simulation for fatigue life of commercial vehicle steering gear bracket. Journal of Chang’an University (Natural Science Edition), Vol. 31, 2011, p. 90-94.
-
Chen Z., Zhou L., Zhao B., Liang X. X. Study on fatigue life of frame for corn combine chassis machine. Transactions of the Chinese Society of Agricultural Engineering (Transactions of the CSAE), Vol. 31, 2015, p. 19-25.
-
Gao Y. D., Hu X. X. The multi-axial fatigue of concrete mixer sub-frame. Machinery Design and Manufacture, Vol. 6, 2015, p. 211-214.
-
Li C. L., Song S. S., Han Z. N. Fatigue reliability analysis of frame based on nCode design-life. Journal of Graphics, Vol. 35, 2014, p. 42-45.
-
Mi C. J., Gu Z. Q., Wu W. G., Tao J., Liang X. B., Peng G. P. Fatigue life analysis of rear axle housing of mining dump truck under random load. Journal of Mechanical Engineering, Vol. 48, 2012, p. 103-109.
-
Liu Y. C., Wang G. L., Sun L. Fatigue damage analysis and life prediction for vehicle control arm. Transactions of the Chinese Society of Agricultural Engineering, Vol. 29, 2013, p. 83-91.
-
Liu Y. C., Wang G. L., Sun L. Prediction method on subframe’s fatigue life based on measured load spectrum. Automobile Technology, Vol. 4, 2014, p. 58-62.
About this article
This work is supported in part by the Project of National Natural Science Foundation of China (Grant No. 51505172), Jiangsu Planned Projects for Postdoctoral Research Funds (Grant No. 1402017C), Six Talent Peaks Project in Jiangsu Province (Grant No. JXQC2015008), and the Project of the Natural Science Foundation of the Jiangsu Higher Education Institutions of China (Grant No. 13KJB580001).