Abstract
A two-stage damage detection method based on strain energy and micro-search artificial fish swarm algorithm (MSAFSA) is presented for solving structural multi-damage problem. First, structural modal strain energy and energy dissipation process are analyzed and an improved modal strain energy dissipation ration index (IMSEDRI) is proposed to preliminarily detect suspected damage elements. Then, artificial fish swarm algorithm (AFSA) is used to identify damage extent of suspected damage elements. In general, the search efficiency of a basic AFSA isn’t very efficient for the search procedure. So, a micro-search artificial fish swarm algorithm is presented in this paper. The simulation results demonstrate that the damage detection method can estimate the damage locations and extent with good accuracy, and the calculated results of the proposed MSAFSA are obviously superior to those of both the basic AFSA and the AFSA with visual-step change strategy.
1. Introduction
Structural damage identification has received increasing attention in the research community in recently two decades. It has become an important and rapidly growing research area, involving civil engineering, mechanical engineering, and aeronautical engineering with the goal of assessing the health condition and the dynamic characteristics of a structure. Most of the damage identification research focuses on dynamic characteristics which can be acquired from results of dynamic testing. The main dynamic characteristics include natural frequencies, mode shapes, modal strain energy etc. Natural frequency has already been used to detect structural damage. Cawley et al. [1] described a numerical method for detecting structural damage location through the measurements of natural frequencies. Salawu [2] identified structural damage through frequency changes. Chaudhari et al. [3] and Chinchalkar et al. [4] proposed a numerical method for determining the location of a crack in a beam of varying depth when the lowest three natural frequencies of the cracked beam are considered. Zhang et al. [5] utilized the natural frequencies to detect the delamination damage. However, the natural frequencies are not sensitive to local damage and the number of measured frequencies is few [2]. Mode shape or modal strain energy can also be utilized to detect structural damage [6-8]. Allemang et al. [9] presented a modal assurance criterion method, which detect damage through comparing mode shapes. Pindey and Biswas [10] identified structural damage by solving the linear damage equations of complete mode shapes. In general, modal strain energy method is more efficient than some mode shape methods for damage identification [11-13]. Shi et al. [14] proposed a modal strain energy change index to assess the damage state of a structure. Sazonov et al. [15] studied vibration-based methods of non-destructive damage detection by utilizing curvature or strain energy mode shapes. Liu et al. [16] presented a modal strain energy dissipation ratio index (MSEDRI), which can approximately detect structural damage sites. It is necessary for the MSEDRI to calculate the modal strain energy change value in each element. However, the MSEDRI didn’t consider the modal strain energy change tendency to damage. Therefore, an improved modal strain energy dissipation ratio index will be proposed.
Artificial fish swarm algorithm is a new population-based swarm intelligent evolutionary computation technique proposed by Li et al. [17] that was inspired by the natural schooling behavior of fish. AFSA presents a strong ability to avoid local minimums in order to achieve global optimization. It has been proofed in function optimization, parameter estimation, combinatorial optimization, least squares support vector machine and geotechnical engineering problems [18, 19]. AFSA imitates three typical behaviors, defined to include “searching for food”, “swarming in response to a threat”, and “following to increase the chance of achieving a successful result”. Three major parameters involved in AFSA include visual distance (visual), maximum step length (step), and a crowd factor [17]. Here, The AFSA is proposed to detect structural damage locations and extent. In general, it is difficult for the basic AFSA to identify the multi-damage problem of complex structure. Therefore, a micro-search artificial fish swarm algorithm (MSAFSA) is presented to improve identification capability.
In this study, a two-stage damage detection method based on micro-search artificial fish swarm algorithm and IMSEDRI is proposed. First, an improved modal strain energy dissipation ration index is proposed to identify suspected damage elements. Then, after the suspected damage elements are preliminarily determined, the micro-search artificial fish swarm algorithm is presented to find the damage severity of the suspected damage elements. There are seven sections in this paper. Section 2 introduces strain energy and energy dissipation process, and presents the improved modal strain energy dissipation ration index. Section 3 briefly describes an artificial fish swarm algorithm. Section 4 proposes some improved strategies and presents the micro-search artificial fish swarm algorithm. Section 5 introduces the two-stage method based on artificial fish swarm algorithm and IMSEDRI. Section 6 gives numerical examples. Finally, Section 7 presents the conclusions.
2. Improved modal strain energy dissipation ration index
Modal strain energy can be used to detect structural damage. The modal strain energy of the jth element and the ith mode before and after the occurrence of damage is expressed as:
In which MSEuij is the undamaged modal strain energy (MSE); Φi is the ith undamaged mode shape; MSEdijis the damaged MSE; Φdi is the ith damaged mode shape; Kj is the stiffness matrix of the jth element. When the first m mode shapes are considered, the undamaged and damaged modal strain energy of the jth element can be given by:
If:
Thus, the modal strain energy change of the jth element is simply expressed as:
Damage will cause the change of MSE. In general, damage can also be described as energy dissipation process [20]. The same damage will cause the same energy change. Therefore, the modal strain energy change caused by damage should be equal to the energy dissipation caused by the same damage.
Structural damage is also the energy dissipation process. The strain energy dissipation ratio at time t is described as follows [20]:
In which t is time; σ is the stress vector; ε is the strain vector; V is the volume; c is damage coefficient. Structural damage can be described as the energy dissipation process of undamaged system. Thus, the strain energy dissipation ratio of the jth element can be expressed as:
When t= 0, no damage occurs; when t=td, damage occurs. It can be hypothesized that there is a linear relationship between cj(t) and t. Thus, the derivative ˙cj(t) is a constant. If a damage cj occurs in the jth element, the energy dissipation of the jth element can be given by:
The same damage will cause the same energy change. Therefore, the modal strain energy change should be equal to the energy dissipation caused by the same damage. Considering Eqs. (4) and (7), the following equation can be obtained:
Thus, the modal strain energy dissipation ration index [16] of the jth element is obtained as follow:
In general, damage will cause the stiffness degradation, and it will also cause the increase of modal strain energy [21]. Therefore, an improved modal strain energy dissipation ration index (IMSEDRI) is given by:
Thus, incorrect index value can be directly excluded. From Eq. (10), we can find the suspected damage elements. After the suspected damage elements are preliminarily identified, the damage extent can be determined by using an artificial fish swarm algorithm.
3. Artificial fish swarm algorithm
Artificial fish swarm algorithm (AFSA) is a new population-based optimization technique inspired by the natural feeding behavior of fish, which was first proposed by Li et al. [17]. In general, a fish is represented by its N-dimensional position Xi=(x1,x2,…,xN,), and Y(Xi) is the fitness or objective function at position Xi. The relationship between two fish is denoted by their Euclidean distance ‖Xj-Xi‖. Visual and Step stand for the perception range and the moving step of the artificial fish, respectively. The basic fish-swarm behaviors include foraging behavior, swarming behavior, following behavior and random behavior.
3.1. Foraging behavior
Foraging is a basic biological behavior adopted by fish looking for food. Let Xi be the current state of an artificial fish, and select a state Xj randomly in its Visual range. For the minimization problem, if Yj<Yi, the artificial fish moves a step in the direction of (Xj–Xi). Otherwise, select a state Xj randomly again and judge whether it satisfies the forward condition. If it cannot be satisfied after try-number times, the random behavior is performed. The foraging behavior is expressed mathematically as:
where Xnext is the next state of the artificial fish, rand is uniformly distributed random number in the interval [0, 1].
3.2. Swarming behavior
In the fish swarm, each artificial fish should explore the central position Xc of nf artificial fish in its neighborhood (dij<Visual). If Yc⋅nf<δ⋅Yi (For the minimization problem), the artificial fish Xi will go forward a step to the Xc. It is expressed mathematically as:
In which δ is the food concentration or crowd factor.
3.3. Following behavior
Let Xi be the current state of an artificial fish, and Xmin (for minimization problem) is the best companion in the current neighborhood of Xi If Ymin⋅nf<δ⋅Yi (For the minimization problem), the artificial fish Xi will go forward a step to the Xmin. The following behavior is given by:
3.4. Random behavior
The artificial fish select a position randomly in its Visual range, and then it moves towards the position. The random behavior can be written as:
In addition, artificial fish swarm algorithm will provide a bulletin to record the optimal state in the fish swarm. Each artificial fish compares its own state with the bulletin after making a step. If its state is better, the bulletin will be updated.
4. Micro-search artificial fish swarm algorithm
In general, the search efficiency of the basic AFSA isn’t very high. Therefore, it is necessary to modify the basic AFSA. Here, some improved strategies are proposed and micro-search artificial fish swarm algorithm is presented.
4.1. Visual-step change strategy
Visual and Step have an important effect on AFSA [18, 19]. Therefore, an artificial fish swarm algorithm with visual-step change strategy is proposed. The method mainly presented novel Visual equation and Step equation.
The novel Visual equation and Step equation are expressed mathematically as:
where, Visual0 is initial value of visual distance; p is change parameter of visual distance; tp is the current iteration number; m is the total iteration number; Step0 is initial value of step length; q is change parameter of step length. Thus, the visual and step will dynamically change with the iteration number. In general, the AFSA with visual-step change strategy can improve the search efficiency.
4.2. Micro-search strategy
The best location of fish in a swarm is picked out and this location is called as elitist state. Then, the elitist state will be further optimized by using the micro-search strategy. Here, we assumed the identification precision of damage is 1 %. Thus, the micro-search distance is equal to 0.01. The fish will move ±0.01 micro-search step in turn. The method is shown in Fig. 1.
Fig. 1Micro-search of the elitist state
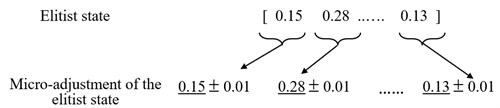
If the elitist state is understood as a location in n-dimensional space, the elitist state should contain n components. We will adjust all the n components by ±0.01 steps in turn. Thus, we will search all the potential change in the n components. If the generated elitist state is better than the original elitist state, the original elitist state will be replaced by the generated elitist state. Finally, the best state is recorded in bulletin. If the elitist state isn’t change in the next generation, the micro-search should be omitted to avoid the redundant calculation. Therefore, the micro-search strategy can easily find the best solution and improve the search efficiency.
4.3. Two termination criteria.
Two termination criteria are expressed as follows: Eq. (1) If the optimal state in the bulletin does not change in continuous t1 iterations, the iteration process will be terminated. The termination number t1 can avoid redundant iteration calculation. Eq. (2) If the calculation value of the optimal state is 0 or a very small number, which means that the optimal solution has been obtained, the iteration process will be terminated. Either of the two termination criteria is met, the iteration calculation will be ended.
The artificial fish swarm algorithm with the three improved strategies is called as micro-search artificial fish swarm algorithm (MSAFSA). The flowchart of the MSAFSA is shown in Fig. 2 and is summarized as follows:
Fig. 2Flowchart of MSAFSA
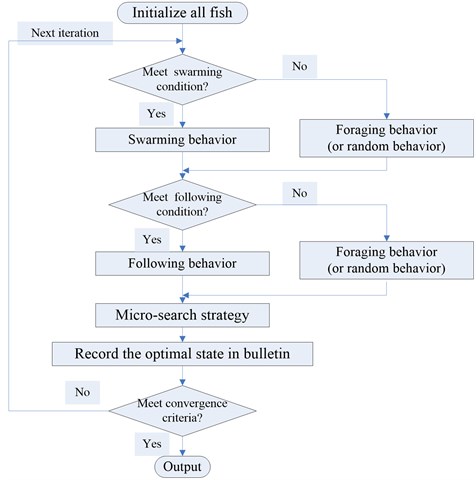
Step 1: Create all fish, and calculate the objective function of the location state of the fish.
Step 2: Perform swarming behavior if the swarming condition is met. Otherwise, perform foraging behavior or random behavior.
Step 3: Perform following behavior if the following condition is met. Otherwise, perform foraging behavior or random behavior.
Step 4: Pick out the best fish of a swarm, and update the elitist state by using micro-search strategy. If the elitist state isn’t adjusted in the next generation, the micro-search process will be ignored.
Step 5: Record the optimal state in the fish swarm in bulletin.
Step 6: Repeat Step 2-Step 5 until either of the two termination criteria is met.
5. Damage identification based on artificial fish swarm algorithm
It is difficult for artificial fish swarm algorithm to detect multiple damage of a complex structure. Here, we propose a two-stage damage identification method. First, the improved modal strain energy dissipation ration index is used to preliminarily identify the suspected damage elements. Then, the artificial fish swarm algorithm is utilized to find the damage extent of the suspected damage elements. A structure consists of NE elements. If we find ND suspected damage elements in the NE elements by using the IMSEDRI, we just need identify the damage extent of the ND suspected elements by using the AFSA (ND<NE). Thus, when the identification precision of damage extent is 1 %, the search space consists of 101ND different kinds of damage extent and we just need to find the optimal solution from 101ND different kinds of damage extent. If we directly utilize the AFSA to search true damage extent of the NE elements, we need to find the optimal solution from 101NE different kinds of damage extent. In general, 101ND<<101NE. Therefore, the proposed two-stage method is of better convergence and higher search efficiency.
The objective function of the artificial fish swarm algorithm is given by:
where, {∆f} is the change vector of measured frequency; {δD} is the theoretical damage degree of suspected damage elements; {δf({δD})} is the change vector of theoretical frequency for damage on {δD}; {∆Ф} is the change vector of measured mode shape; {δФ({δD})} is the change vector of theoretical mode shape for damage on {δD}.
Here, the suspected damage vector {δD} can be obtained by using the improved modal strain energy dissipation ration index. The best objective function value should be 0 or a small value. Therefore, this is a minimization problem.
6. Numerical examples
In order to investigate the effectiveness of the two-stage method, a two-dimensional truss structure has been used. The size of the truss structure is depicted in Fig. 3. The material property of the structure is: ρ= 2800 kg/m3, E= 72 GPa, and A= 0.001 m2. The truss model consists of 30 bar elements, 14 nodes, and 24 degrees of freedom. Damage is simulated by a reduction in the stiffness of individual bars in the structure. Damage cases are shown in Table 1. The parameters of MSAFSA are: Visual0= 0.4; change parameter of visual distance p= 0.8; Step0= 0.4; change parameter of step length q= 0.9; crowd factor δ= 0.2; identification precision is 0.01; micro-search distance is 0.01; termination parameter t1 is 20; total number of fish is 100; maximum iteration number is 100.
Fig. 3Two-dimensional truss structure
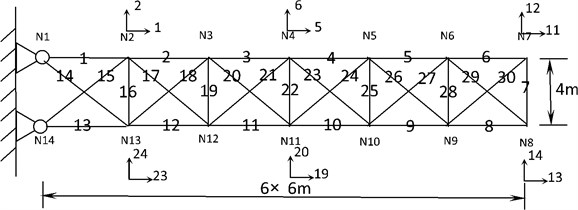
It is important to determine suspected damage elements in the damage identification process. If the number of suspected damage elements can be effectively reduced, it will be easy to find the true damage elements and extent by using artificial fish swarm algorithm. Therefore, the IMSEDRI is used to identify suspected damage elements. For a given set of suspected damage elements, the true damage extent is calculated by using the MSAFSA. In order to compare and contrast different artificial fish swarm algorithms, the basic AFSA and the AFSA with visual-step change strategy are also utilized to identify structural damage. The first ten natural frequencies and three mode shapes are applied to calculate the objective function of the algorithms.
Table 1Damage cases for two-dimensional truss
Case 1 | Case 2 | ||
Element No. (1) | Damage (2) | Element No. (3) | Damage (4) |
5 | 25 % | 7 | 15 % |
8 | 15 % | 9 | 20 % |
25 | 15 % | 28 | 20 % |
6.1. Case 1
In general, damage can be considered as the stiffness reduction. In this case, elements 5, 8 and 25 have 25 %, 15 % and 15 % stiffness reduction, respectively. The calculation procedure of the method is depicted as follows: First, the improved modal strain energy dissipation ration index is utilized to find suspected damage elements. Then, the highest five elements are selected as suspected damage elements. Finally, the AFSA is used to identify the damage extent of the suspected elements. The localization identification results of the IMSEDRI are shown in Fig. 4. An element with relatively higher IMSEDRI value means that it is more probable to be the true damage element. In general, with the increase of suspected damage elements, the calculation cost will rapidly increase. In this case, five elements meet identification requirement. Therefore, the highest five elements are selected as suspected damage elements. Thus, the elements 5, 8, 25, 26 and 28 are picked out.
Fig. 4Damage identification results of the IMSEDRI for Case 1
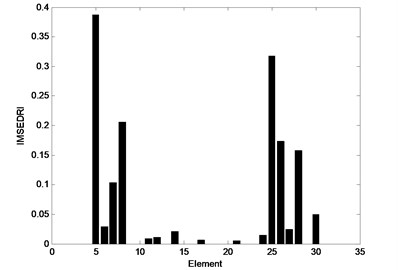
Table 2Quantitative results of 10 run using the basic AFSA for Case 1
No. | Elements and damage | Iteration number | ||||
5 | 8 | 25 | 26 | 28 | ||
1 | 0.4300 | 0.2800 | 0.1500 | 0.0600 | 0.1500 | 29 |
2 | 0.5300 | 0.3100 | 0.1300 | 0.1700 | 0.0400 | 22 |
3 | 0.6000 | 0.3400 | 0 | 0 | 0.1600 | 68 |
4 | 0.2200 | 0.1300 | 0.1400 | 0 | 0 | 83 |
5 | 0.5000 | 0.0900 | 0.1500 | 0.1100 | 0.1500 | 22 |
6 | 0.6000 | 0.0600 | 0.1300 | 0.1900 | 0.1600 | 49 |
7 | 0.6000 | 0.3500 | 0.1600 | 0.0700 | 0.0400 | 22 |
8 | 0.4800 | 0.5400 | 0.0300 | 0.1700 | 0.1500 | 22 |
9 | 0.1500 | 0.1800 | 0.1300 | 0.0300 | 0.1100 | 23 |
10 | 0.6000 | 0.2700 | 0.0700 | 0.0100 | 0.1800 | 87 |
Average | 0.471 | 0.255 | 0.109 | 0.081 | 0.114 | 42.7 |
Then, the basic AFSA, the AFSA with visual-step change strategy and the MSAFSA, are used to calculate the damage extent of the suspected elements. These algorithms only need to detect the damage extent of the five suspected elements 5, 8, 25, 26 and 28. The damage quantification results of 10 runs are shown in Tables 2-4. From Table 2, we can see that it is difficult for the basic AFSA to identify the true damage locations and extent. From Table 3, we can observe that the identification results of the AFSA with visual-step change strategy are close to the true damage extent, but the average iteration number is relatively higher. From Table 4, we can observe that the MSAFSA can find the true damage extent, and improve the convergence speed. Therefore, the MSAFSA is obviously superior to both the basic AFSA and the AFSA with visual-step change strategy.
Table 3Quantitative results of 10 run using the AFSA with visual-step change strategy for Case 1
No. | Elements and damage | Iteration number | ||||
5 | 8 | 25 | 26 | 28 | ||
1 | 0.2000 | 0.0800 | 0.0100 | 0.0100 | 0.0100 | 57 |
2 | 0.1100 | 0.0500 | 0 | 0 | 0 | 44 |
3 | 0.2500 | 0.1500 | 0.1500 | 0 | 0 | 39 |
4 | 0.6000 | 0.3600 | 0.1300 | 0 | 0 | 30 |
5 | 0.3200 | 0.1900 | 0.1900 | 0 | 0.0100 | 68 |
6 | 0.2500 | 0.1500 | 0.1500 | 0 | 0 | 56 |
7 | 0.3100 | 0.1900 | 0.2000 | 0 | 0 | 74 |
8 | 0.0900 | 0.0500 | 0.0600 | 0 | 0.0100 | 78 |
9 | 0.1400 | 0.0800 | 0.0900 | 0 | 0 | 43 |
10 | 0.2500 | 0.1500 | 0.1500 | 0 | 0 | 71 |
Average | 0.252 | 0.145 | 0.113 | 0.001 | 0.003 | 56 |
Table 4Quantitative results of 10 run using the MSAFSA for Case 1
No. | Elements and damage | Iteration number | ||||
5 | 8 | 25 | 26 | 28 | ||
1 | 0.2500 | 0.1500 | 0.1500 | 0 | 0 | 55 |
2 | 0.2600 | 0.1500 | 0.1200 | 0 | 0.0100 | 31 |
3 | 0.2500 | 0.1500 | 0.1500 | 0 | 0 | 31 |
4 | 0.2500 | 0.1500 | 0.1500 | 0 | 0 | 19 |
5 | 0.2500 | 0.1500 | 0.1500 | 0 | 0 | 26 |
6 | 0.1700 | 0.1000 | 0.1000 | 0 | 0 | 31 |
7 | 0.2500 | 0.1500 | 0.1500 | 0 | 0 | 23 |
8 | 0.2500 | 0.1500 | 0.1500 | 0 | 0 | 25 |
9 | 0.2500 | 0.1500 | 0.1500 | 0 | 0 | 9 |
10 | 0.2500 | 0.1500 | 0.1500 | 0 | 0 | 26 |
Average | 0.243 | 0.145 | 0.142 | 0 | 0.001 | 27.6 |
The representative objective function curves of the basic AFSA, AFSA with visual-step change strategy and MSAFSA, are depicted in Figs. 5-7, respectively. From Fig. 5, we can see that the objective function curve of the basic AFSA gradually tends to zero with the increasing number of generations. From Fig. 6, we can observe that the objective function curve of the AFSA with visual-step change strategy can quickly tends to zero, which show the effect of the dynamic visual and step. From Fig. 7, we can see that the objective function curve of the MSAFSA is quicker to tend to zero. The MSAFSA has the fastest convergence speed in the three algorithms. So, the MSAFSA is more effective than both the basic AFSA and the AFSA with visual-step change strategy.
In general, measurement error will affect the credibility of experimental data. Here, the frequencies with 0.15 % error and the mode shapes with 3 % error are considered. The IMSEDRI is used to identify suspected damage elements. The identification results of IMSEDRI with measurement error are depicted in Fig. 8. Here, we still select the highest five elements as suspected damage elements. So, the elements 5, 7, 8, 25 and 29 are picked out. The measurement error will also affect the identification results of the AFSAs.
Fig. 5An objective function curve of the basic AFSA for Case 1
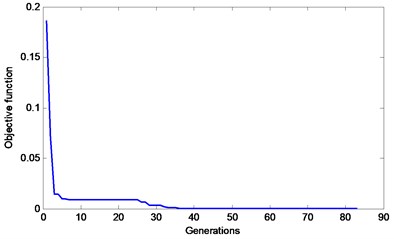
Fig. 6An objective function curve of the AFSA with visual-step change strategy for Case 1
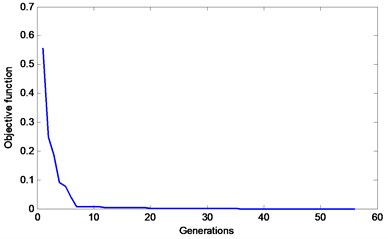
Fig. 7An objective function curve of the MSAFSA for Case 1
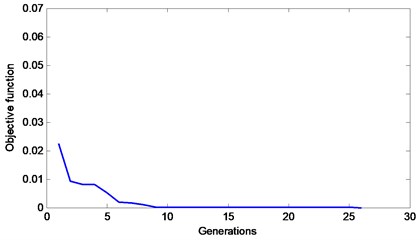
The basic AFSA, the AFSA with visual-step change strategy and the MSAFSA are used to assess the damage severity of the suspected damage elements. They only need to assess the damage severity of the suspected elements 5, 7, 8, 25, and 29. The calculation results are shown in Tables 5-7. From Table 5, we can see that the basic AFSA still cannot identify the true damage locations and extent. From Table 6, we can observe that the AFSA with visual-step change strategy can approximately find the true damage elements, but the iteration number is higher.
From Table 7, we can see that the MSAFSA can approximately find the true damage elements and improve the convergence speed. Therefore, the proposed MSAFSA is best one in the three algorithms.
Table 5Quantitative results of 10 run with measurement error using the basic AFSA for Case 1
No. | Elements and damage | Iteration number | ||||
5 | 7 | 8 | 25 | 29 | ||
1 | 0.2700 | 0.0300 | 0.0200 | 0.1900 | 0.0100 | 22 |
2 | 0.2300 | 0.0600 | 0.1100 | 0.2100 | 0 | 61 |
3 | 0.2100 | 0.4100 | 0.1100 | 0.1900 | 0 | 65 |
4 | 0.2400 | 0 | 0.1000 | 0.1500 | 0 | 48 |
5 | 0.2200 | 0.5100 | 0.0900 | 0.1800 | 0 | 88 |
6 | 0.2200 | 0.2100 | 0.0800 | 0.1300 | 0.1000 | 96 |
7 | 0.2400 | 0.0200 | 0.1000 | 0.2000 | 0 | 56 |
8 | 0.2200 | 0.0400 | 0.1700 | 0.0300 | 0.0200 | 22 |
9 | 0.2400 | 0.2600 | 0.0900 | 0.1600 | 0.0300 | 76 |
10 | 0.2100 | 0.1900 | 0.1000 | 0.1900 | 0.1300 | 22 |
Average | 0.23 | 0.173 | 0.097 | 0.163 | 0.029 | 55.6 |
Table 6Quantitative results of 10 run with measurement error using the AFSA with visual-step change strategy for Case 1
NO. | Elements and damage | Iteration number | ||||
5 | 7 | 8 | 25 | 29 | ||
1 | 0.2500 | 0 | 0.0900 | 0 | 0 | 43 |
2 | 0.2400 | 0 | 0.1000 | 0.1500 | 0 | 39 |
3 | 0.2400 | 0 | 0.1000 | 0.1500 | 0 | 48 |
4 | 0.2400 | 0.0900 | 0.1000 | 0.1500 | 0 | 50 |
5 | 0.2400 | 0 | 0.1000 | 0.1500 | 0 | 32 |
6 | 0.2400 | 0 | 0.1000 | 0.1500 | 0 | 32 |
7 | 0.2400 | 0.0100 | 0.1000 | 0.0100 | 0.0100 | 37 |
8 | 0.2400 | 0 | 0.1000 | 0.1500 | 0 | 32 |
9 | 0.2400 | 0.0900 | 0.1000 | 0.1500 | 0 | 66 |
10 | 0.2400 | 0 | 0.1000 | 0.1500 | 0 | 42 |
Average | 0.241 | 0.019 | 0.099 | 0.121 | 0.001 | 42.1 |
Table 7Quantitative results of 10 run with measurement error using the MSAFSA for Case 1
No. | Elements and damage | Iteration number | ||||
5 | 7 | 8 | 25 | 29 | ||
1 | 0.2400 | 0 | 0.1000 | 0.1600 | 0 | 8 |
2 | 0.2400 | 0.0100 | 0.1000 | 0.1500 | 0 | 9 |
3 | 0.2400 | 0 | 0.1000 | 0.1500 | 0 | 10 |
4 | 0.2400 | 0.0100 | 0.1000 | 0.1500 | 0 | 27 |
5 | 0.2400 | 0.0700 | 0.1000 | 0.1500 | 0 | 13 |
6 | 0.2400 | 0 | 0.1000 | 0.1500 | 0 | 30 |
7 | 0.2400 | 0.1400 | 0.1000 | 0.0600 | 0 | 52 |
8 | 0.2400 | 0 | 0.1000 | 0.1600 | 0 | 12 |
9 | 0.2400 | 0 | 0.1000 | 0.1500 | 0 | 16 |
10 | 0.2400 | 0.0700 | 0.1000 | 0.1500 | 0 | 14 |
Average | 0.238 | 0.03 | 0.1 | 0.143 | 0 | 19.1 |
Fig. 8Damage identification results of the IMSEDRI with measurement error for Case 1
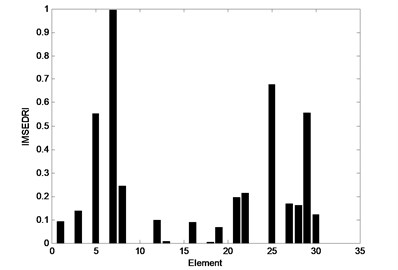
6.2. Case 2
In this case, elements 7, 9 and 28 have 15 %, 20 % and 20 % stiffness reduction, respectively. The IMSEDRI is used to detect suspected damage elements. The calculation results are depicted in Fig. 9. An element with relatively higher IMSEDRI value means that it is more probable to be the true damage element. Here, we still select the highest five elements as suspected damage elements. Thus, the elements 7, 8, 9, 27 and 28 are picked out. Then, the basic AFSA, the AFSA with visual-step change strategy and the MSAFSA are used to assess the damage severity of the suspected damage elements. They only need to assess the damage severity of the suspected elements 7, 8, 9, 27 and 28. The calculation results are shown in Tables 8-10. From Table 8, we can see that the basic AFSA can approximately detect the damage extent of suspected damage elements, but the average convergence speed isn’t very quick.
From Table 9, we can observe that the AFSA with visual-step change strategy can also approximately identify the damage extent, but the average convergence speed isn’t very quick yet. From Table 10, we can observe that the MSAFSA can find the true damage extent, and improve the convergence speed. So, it is obvious that the MSAFSA is better than both the basic AFSA and the AFSA with visual-step change strategy.
Fig. 9Damage identification results of the IMSEDRI for Case 2
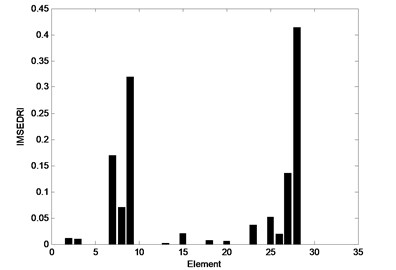
Table 8Quantitative results of 10 run using the basic AFSA for Case 2
No. | Elements and damage | Iteration number | ||||
7 | 8 | 9 | 27 | 28 | ||
1 | 0 | 0.0100 | 0.2000 | 0 | 0.2000 | 49 |
2 | 0 | 0 | 0.2000 | 0 | 0.1900 | 37 |
3 | 0.5200 | 0.0200 | 0.1900 | 0 | 0.1700 | 40 |
4 | 0.1500 | 0 | 0.2000 | 0 | 0.2000 | 41 |
5 | 0.3400 | 0 | 0.2000 | 0 | 0.1800 | 45 |
6 | 0.1500 | 0 | 0.2000 | 0 | 0.2000 | 40 |
7 | 0 | 0 | 0.2000 | 0 | 0.1900 | 54 |
8 | 0.4300 | 0.0200 | 0.2200 | 0 | 0.0100 | 41 |
9 | 0.3500 | 0 | 0.2000 | 0 | 0.1700 | 62 |
10 | 0.1500 | 0 | 0.2000 | 0 | 0.2000 | 38 |
Average | 0.209 | 0.005 | 0.201 | 0 | 0.171 | 44.7 |
Table 9Quantitative results of 10 run using the AFSA with visual-step change strategy for Case 2
No. | Elements and damage | Iteration number | ||||
7 | 8 | 9 | 27 | 28 | ||
1 | 0.1500 | 0 | 0.2000 | 0 | 0.2000 | 38 |
2 | 0.3800 | 0 | 0.2000 | 0 | 0 | 36 |
3 | 0.3100 | 0 | 0.2000 | 0 | 0.1900 | 47 |
4 | 0.1500 | 0 | 0.2000 | 0 | 0.2000 | 30 |
5 | 0.3100 | 0 | 0.2000 | 0 | 0.1900 | 33 |
6 | 0 | 0 | 0.2000 | 0 | 0.1900 | 31 |
7 | 0.1500 | 0 | 0.2000 | 0 | 0.2000 | 45 |
8 | 0.1500 | 0 | 0.2000 | 0 | 0.2000 | 39 |
9 | 0.3100 | 0 | 0.2000 | 0 | 0.1900 | 46 |
10 | 0.1500 | 0 | 0.2000 | 0 | 0.2000 | 49 |
Average | 0.206 | 0 | 0.2 | 0 | 0.176 | 39.4 |
The representative objective function curves of the basic AFSA, AFSA with visual-step change strategy and MSAFSA, are depicted in Figs. 10-12, respectively. From Fig. 10, we can see that the objective function curve of the basic AFSA gradually tends to zero with the increase of iteration number. From Fig. 11, we can observe that the curve of the AFSA with visual-step change strategy can quickly tends to zero, which show the effect of the dynamic visual and step. From Fig. 12, we can see that the objective function curve of the MSAFSA is quicker to tend to zero. The MSAFSA has the fastest convergence speed in the three algorithms. Therefore, the MSAFSA is superior to both the basic AFSA and the AFSA with visual-step change strategy.
Table 10Quantitative results of 10 run using the MSAFSA for Case 2
No. | Elements and damage | Iteration number | ||||
7 | 8 | 9 | 27 | 28 | ||
1 | 0.1500 | 0 | 0.2000 | 0 | 0.2000 | 16 |
2 | 0.3100 | 0 | 0.2000 | 0 | 0.1900 | 32 |
3 | 0.1500 | 0 | 0.2000 | 0 | 0.2000 | 12 |
4 | 0.1500 | 0 | 0.2000 | 0 | 0.2000 | 19 |
5 | 0.1500 | 0 | 0.2000 | 0 | 0.2000 | 10 |
6 | 0.1500 | 0 | 0.2000 | 0 | 0.2000 | 30 |
7 | 0.1500 | 0 | 0.2000 | 0 | 0.2000 | 10 |
8 | 0.3100 | 0 | 0.2000 | 0 | 0.1900 | 28 |
9 | 0.1500 | 0 | 0.2000 | 0 | 0.2000 | 19 |
10 | 0.1500 | 0 | 0.2000 | 0 | 0.2000 | 15 |
Average | 0.182 | 0 | 0.2 | 0 | 0.198 | 19.1 |
Fig. 10An objective function curve of the basic AFSA for Case 2
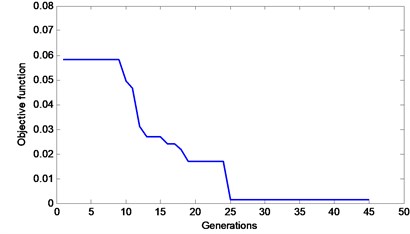
Fig. 11An objective function curve of the AFSA with visual-step change strategy for Case 2
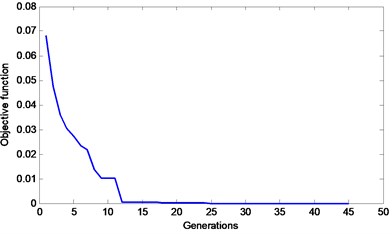
Fig. 12An objective function curve of the MSAFSA for Case 2
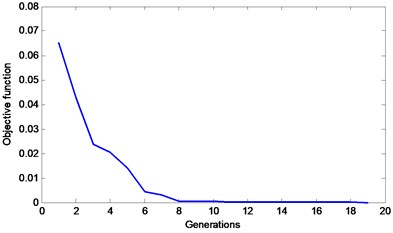
In general, measurement error will affect the credibility of experimental data. Here, the frequencies with 0.15 % error and the mode shapes with 3 % error are considered in this case. The IMSEDRI is used to identify suspected damage elements. The identification results of IMSEDRI with measurement error are depicted in Fig. 13. Here, we still select the highest five elements as suspected damage elements. Thus, the elements 7, 9, 27, 28 and 30 are picked out. The measurement error will also affect the identification results of the AFSAs. The basic AFSA, the AFSA with visual-step change strategy and the MSAFSA are used to assess the damage severity of the suspected damage elements. They only need to assess the damage severity of the suspected elements 7, 9, 27, 28 and 30. The calculation results are listed in Tables 11-13. From Table 11, we can find that the identification result of the basic AFSA isn’t very good. From Table 12, we can observe that the AFSA with visual-step change strategy can approximately find the true damage elements, but the average convergence speed isn’t very quick. From Table 13, we can observe that the MSAFSA can approximately find the true damage elements and improve the convergence speed. Therefore, the identification results of the MSAFSA are still superior to those of the basic AFSA and the AFSA with visual-step change strategy.
Fig. 13Damage identification results of the IMSEDRI with measurement error for Case 2
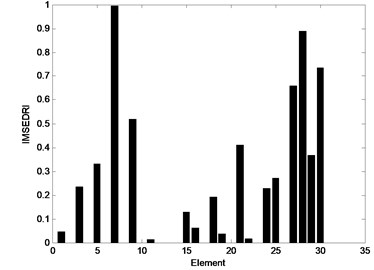
Table 11Quantitative results of 10 run with measurement error using the basic AFSA for Case 2
No. | Elements and damage | Iteration number | ||||
7 | 9 | 27 | 28 | 30 | ||
1 | 0.1800 | 0.1700 | 0 | 0.2000 | 0 | 46 |
2 | 0.0100 | 0.1700 | 0 | 0.2100 | 0 | 58 |
3 | 0.5200 | 0.1700 | 0 | 0.1700 | 0 | 41 |
4 | 0.1800 | 0.1700 | 0 | 0.2000 | 0 | 30 |
5 | 0.1800 | 0.1700 | 0 | 0.2000 | 0 | 47 |
6 | 0.1800 | 0.1700 | 0 | 0.2000 | 0 | 55 |
7 | 0.4800 | 0.1300 | 0 | 0.2100 | 0 | 56 |
8 | 0.5300 | 0.1700 | 0 | 0.1600 | 0 | 54 |
9 | 0.5300 | 0.1700 | 0 | 0.1600 | 0 | 62 |
10 | 0.5300 | 0.1700 | 0 | 0.1600 | 0 | 45 |
Average | 0.332 | 0.166 | 0 | 0.187 | 0 | 49.4 |
Table 12Quantitative results of 10 run with measurement error using the AFSA with visual-step change strategy for Case 2
No. | Elements and damage | Iteration number | ||||
7 | 9 | 27 | 28 | 30 | ||
1 | 0.1900 | 0.1800 | 0 | 0.1900 | 0 | 25 |
2 | 0.1800 | 0.1700 | 0 | 0.2000 | 0 | 31 |
3 | 0 | 0.1900 | 0 | 0 | 0 | 28 |
4 | 0.5300 | 0.1700 | 0 | 0.1600 | 0 | 41 |
5 | 0.1800 | 0.1700 | 0 | 0.2000 | 0 | 35 |
6 | 0.5300 | 0.1700 | 0 | 0.1600 | 0 | 38 |
7 | 0.1800 | 0.1700 | 0 | 0.2000 | 0 | 29 |
8 | 0.0100 | 0.1700 | 0 | 0.2100 | 0 | 26 |
9 | 0.1800 | 0.1700 | 0 | 0.2000 | 0 | 32 |
10 | 0.1800 | 0.1700 | 0 | 0.2000 | 0 | 25 |
Average | 0.216 | 0.173 | 0 | 0.172 | 0 | 31 |
From the two cases, we can find that the proposed two-stage method can detect structural damage with good accuracy. First, the IMSEDRI can approximately identify suspected damage elements. Then, the MSAFSA can calculate the damage extent of the suspected damage elements. Moreover, the proposed MSAFSA is superior to both the basic AFSA and the AFSA with visual-step change strategy.
In general, it is difficult for a single AFSA to identify structural multiple damage problem. To this problem, if the identification precision of damage extent is 1 %, we need to find the optimal solution from 10130≈ 1.3478×1060 different kinds of selection. However, the proposed two-stage method can efficiently reduce the search space. For example, in case 1, we have identified 5 suspected damage elements in the 30 elements by using the IMSEDRI. Thus, we just need to find the optimal solution from 1015≈ 1.051×1010 different kinds of selection. Actually, the average iteration number of the MSAFSA is 100×27.6=2760. Therefore, the two-stage method is of better convergence and higher search efficiency.
Table 13Quantitative results of 10 run with measurement error using the MSAFSA for Case 2
No. | Elements and damage | Iteration number | ||||
7 | 9 | 27 | 28 | 30 | ||
1 | 0.0100 | 0.1700 | 0 | 0.2100 | 0 | 27 |
2 | 0.1900 | 0.1700 | 0 | 0.2000 | 0 | 7 |
3 | 0.1800 | 0.1700 | 0 | 0.2000 | 0 | 13 |
4 | 0.1900 | 0.1700 | 0 | 0.2000 | 0 | 23 |
5 | 0.1600 | 0.1700 | 0 | 0.2000 | 0 | 8 |
6 | 0.1900 | 0.1700 | 0 | 0.2000 | 0 | 10 |
7 | 0.2200 | 0.1700 | 0 | 0.2000 | 0 | 7 |
8 | 0.2300 | 0.1700 | 0 | 0.2000 | 0 | 8 |
9 | 0.1600 | 0.1700 | 0 | 0.2000 | 0 | 6 |
10 | 0.2300 | 0.1700 | 0 | 0.2000 | 0 | 15 |
Average | 0.176 | 0.17 | 0 | 0.201 | 0 | 12.4 |
7. Conclusions
This study has applied a two-stage damage identification method to diagnose structural damages and a novel AFSA has been developed. Subsequently, the results from a simulated structure model have been used to verify the effectiveness of the two-stage method and the MSAFSA. The process of applying the two-stage method and MSAFSA is also been described. First, the improved modal strain energy dissipation ration index is used to preliminarily identify the suspected damage elements. Then, the micro-search artificial fish swarm algorithm is utilized to find the damage extent of the suspected damage elements. The main conclusions are: Eq. (1) The two-stage method based on the IMSEDRI and MSAFSA can accurately and clearly locate damages and has the potential to quantify the degree of damage. Eq. (2) The MSAFSA can perform well under the condition of small damages and their performance is robust even under the interference of measurement error. Therefore, the MSAFSA is more effective and superior than both the basic AFSA and the AFSA with visual-step change strategy.
References
-
Cawley P., Adams R. D. The location of defects in structures from measurements of natural frequencies. Journal of Strain Analysis, Vol. 14, Issue 2, 1979, p. 49-57.
-
Salawu O. S. Detection of structural damage through changes in frequency: a review. Engineering Structures, Vol. 19, Issue 9, 1997, p. 718-723.
-
Chaudhari T. D., Maiti S. K. A study of vibration of geometrically segmented beams with and without crack. International Journal of Solids and Structures, Vol. 37, Issue 5, 2000, p. 760-779.
-
Chinchalkar S. Determination of crack location in beams using natural frequencies. Journal of Sound and Vibration, Vol. 247, 2001, p. 417-429.
-
Zhang Z., Shankar K., Morozov E. V., Tahtali M. Vibration-based delamination detection in composite beams through frequency changes. Journal of Vibration and Control, Vol. 22, Issue 2, 2014, p. 496-512.
-
Law S. S., Shi Z. Y., Zhang L. M. Structural damage detection from incomplete and noisy modal data. ASCE Journal of Engineering Mechanics, Vol. 124, Issue 11, 1998, p. 1280-1288.
-
Shi Z. Y., Law S. S., Zhang L. M. Optimum sensors placement for structural damage detection. ASCE Journal of Engineering Mechanics, Vol. 126, Issue 11, 2000, p. 1173-1179.
-
Guo H., Zhang L. A weighted balance evidence theory for structural multiple damage localization. Computer Methods in Applied Mechanics and Engineering, Vol. 195, Issues 44-47, 2006, p. 6225-6238.
-
Allemang R. J., Brown D. L. A correlation coefficient for modal vector analysis. 1st International Modal Analysis Conference, 1982, p. 110-116.
-
Pindey A. K., Biswas M. Experimental verification of flexibility difference method for locating damage in structures. Journal of Sound and Vibration, Vol. 184, Issue 2, 1995, p. 311-328.
-
Venkatappa S. G. Damage Detection using Vibration Measurement. Master of Science Thesis, West Virginia University, 1997.
-
Stubbs N., Kim J. T., Farrar C. R. Field verification of a nondestructive damage localization and severity estimation algorithm. Proceedings of IMAC, Connecticut USA, Society of Experimental Mechanics, 1995, p. 210-218.
-
Hu H., Wu C. Development of scanning damage index for the damage detection of plate structures using modal strain energy method. Mechanical Systems and Signal Processing, Vol. 23, Issue 2, 2009, p. 274-287.
-
Shi Z. Y., Law S. S., Zhang L. M. Structural damage localization from modal strain energy change. Journal of Sound and Vibration, Vol. 218, Issue 5, 1998, p. 825-844.
-
Sazonov E., Klinkhachorn P. Optimal spatial sampling interval for damage detection by curvature or strain energy mode shapes. Journal of Sound and Vibration, Vol. 285, Issue 4-5, 2005, p. 783-801.
-
Liu H., Qu W. L., Yuan R. Z. Structural damage detection method based on the theory of dissipation ratio of modal strain energy. Journal of Vibration and Shock, Vol. 23, Issue 2, 2004, p. 118-121, (in Chinese).
-
Li X., Shao Z., Qian J. An optimizing method base on autonomous animates: fish swarm algorithm. Systems Engineering Theory and Practice, Vol. 22, Issue 11, 2002, p. 32-38.
-
Azad M. A., Rocha A. M. A. C., Fernandes. E. G. P. Improved binary artificial fish swarm algorithm for the 0-1 multidimensional knapsack problems. Swarm and Evolutionary Computation, Vol. 14, 2014, p. 66-75.
-
Tsai H. C., Lin Y. H. Modification of the fish swarm algorithm with particle swarm optimization formulation and communication behavior. Applied Soft Computing, Vol. 11, Issue 8, 2011, p. 5367-5374.
-
Zhou Z. B. Principle of Least Energy Dissipation and Its Application. 1st Ed., Beijing, China Science Press, 2001.
-
Seyedpoor S. M. A two-stage method for structural damage detection using a modal strain energy based index and particle swarm optimization. International Journal of Non-linear Mechanics, Vol. 47, Issue 1, 2012, p. 1-8.
About this article
This work was supported by the National Natural Science Foundation of China (Grant No. 51468058, 51578094), and the Fundamental Research Funds for the Central Universities (Grant No. 106112014CDJZR200011).