Abstract
A Power Assist Suit (PAS) for agricultural work was developed in this study. The objective is to reduce the strain involved in agricultural labor by mounting motor- and spring-assisted mechanisms on the PAS. However, such mounting might affect the operation of the PAS. Hence, an evaluation method that uses the degree of freedom (DOF) of the joint motions defined on the basis of the operable range of motion of the human body with the limbs in basic positions is proposed as an indicator of the ease of mobility. The articular structure of the PAS for agricultural work was evaluated using this method, and the feasibility of the labor-assist mechanisms was examined by analyzing the motions. The mechanisms reduced the labor involved in fruit tree pruning, which requires lesser joint motions.
1. Introduction
In recent years, population aging has become a serious problem in Japan, as it is also rapidly affecting agriculture. In order to reduce labor requirements and increase efficiency, initiatives to deal with such problems by mechanizing and automating production systems have been taken; however, its introduction to agricultural machinery has been limited to large farms and a few crops. In response to such circumstances, the development of wearable power assist suits (PAS) as robots to help elderly people perform farm work had begun. Those already available for agricultural use include the Raku Vest ARM-1 developed by Kubota Corp. and WAS-LiBERo [1] developed by Wakayama University.
To conduct this study, researchers visited many farms where they interviewed actual farm workers about strenuous work and the work where they wanted support. The results demonstrated that harvesting fruit or pruning place heavy burdens on the workers’ arms and lower backs, demanding immediate improvement of the work posture [2]. As a result of the evaluation, three motions-lifting heavy objects, maintaining a half-sitting and half-standing posture when picking fruit for example, and keeping one’s arms extended when pruning-were selected as the motions to be supported.
Based on the above, PAS for a light work was developed to support a person in the same posture for a long period of time in order to reduce the burden of labor on farm workers. Attaching a power assist unit to that PAS permits it to assist heavy work such as transporting harvested crops and allows a single unit to be used for both light work and heavy work.
In order to promote the development of this agricultural PAS, it is necessary to evaluate its range of motion when it is worn. Motion when it is worn occurs in a restricted range of motion, and the specific range of motion for actual motion has not yet been clarified. So this study used an index called the DOF achievement rate to evaluate the structure, which is an important element of an agricultural PAS in order to evaluate the DOF of joints of the human body. Moreover, the achievability of actual agricultural work motions was digitalized to study the possibility of assistance by the agricultural PAS.
2. Agricultural PAS
Fig. 1 shows the external appearance of the agricultural PAS. The frame that is an exoskeleton structure is made of CFRP, and its total weight is 7 kg. The design standard was set to a height of 170 cm and body weight of 65 kg, which approximates the average physique of a Japanese adult male. The size can be varied by adjusting the location of each part on the frame. It is fixed to the human body at the waist, on arms, and on the legs, allowing a worker to put it on without help within a minute.
Fig. 2 shows the power assist mechanisms of the agricultural PAS. A ratchet mechanism is built into the shoulder joints, supporting the wearer’s arms, thereby easing the burden on his arms of greenhouse crop harvesting work. The switch of the ratchet mechanism is a flange, and the wearer can turn the assistance on and off even when his hands are full by rotating his shoulder outwards to operate this flange. Further, a spiral spring is attached to the knee joint so that the spring’s repulsive power assists the wearer when he is in a half-sitting position. The spring mechanism is turned on and off by a switch installed on the thigh frame, permitting the wearer to cause it to act on any desired place. Along with these assist mechanisms for light work, a power unit to aid lifting work is attached so that it could assist heavy work The maximum output torque of the motor (EC 90 flat motor made by maxon motor) is 444 mNm, and the reduction ratio of its reduction gear (SHD-17-100 by Harmonic Driver Systems) is 1/100. The power assist unit is installed on the side surface of the wearer’s waist and its total weight is 9 kg (including the control use PC and batteries). When the operator is lifting a heavy weight, a myoelectric potential sensor detects change in the electric potential of the operator’s muscles to provide the assistance at appropriate times. When the power assist unit is not used, its arm is removed from the frame so that basic motions are not obstructed. Assuming that the heavy object, which is given assistance, is one cardboard box used to ship harvested crops weighing 10 kg or about 20 kg of fertilizer, then the maximum assist force of the power assist unit is 230 N (23.6 kgf).
Fig. 1Agricultural power assist suit
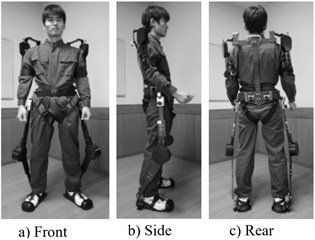
Fig. 2Power assist mechanism
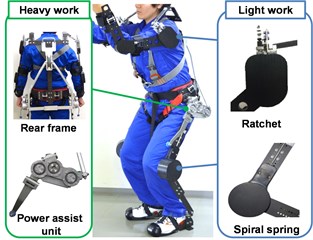
3. Evaluation using the DOF achievement rate
As a method of evaluating the structure, focusing on the DOF of human joints and on the range of human joint motions, the ranges of motion of human joints and those of the joints of the agricultural PAS were compared to define and evaluate the DOF achievement rate.
3.1. DOF achievement rate
The DOF achievement rate is a rate that expresses ease of motion, and it is defined according to the movable range, which can be achieved by the anatomical basic position of a human body [3]. The DOF rate of each joint is defined by the following Eqs. (1-2) assuming that the range of human joint motion is represented by , the range of motion of the joint motion for the agricultural PAS by , and the deviation angle of the rotating axis of the human joint and the agricultural PAS joint by :
For example, in the case of a joint with three degrees of freedom-flexion/extension, abduction/adduction, and external rotation/internal rotation-representing the ratio of the range of joint motion as , it is obtained as follows Eq. (3):
And representing the DOF achievement rate of the entire agricultural PAS as , the DOF achievement rate of each joint as , and the ratio between the ranges of joint motions as , is defined by the following Eq. (4):
The subscripts are as follows, : shoulder, : elbow, : rear, : hip, : knee, : ankle.
3.2. Defining the ranges of joint motions and evaluation based on DOF achievement rate
The ranges of joint motions for the average physique of Japanese adult male, which was the manufacturing standard of the agricultural PAS, the range of joint motions for the design model, and part of the range of joint motions when wearing the agricultural PAS are each listed in Table 1. Informed consent was obtained for the measurement of the ranges of joint motions.
Using data from Table 1, the DOF achievement rates when wearing the PAS were calculated by solving Eqs. (1-4). Fig 3 shows the design model describing the joint rotation axes. Fig. 3(a) shows the joint model of humans. Fig 3(b) shows the joint model of PAS, including passive joints, ratcheted passive joints, active joints, and the assist mechanisms. Fig. 4 shows the results of calculating the DOF achievement rates, for the design model, each joint when the PAS is worn, and for the whole body. The DOF achievement rates, for design model and for the whole body wearing the PAS, are shown as values approximating 0.83 and 0.76, respectively, indicating that motion of 70 % or more of body motions are possible. The DOF achievement rate for each joint differed at the ankles and shoulders between the design model and the PAS when it is worn. The values when it is worn were lower than those of the design model. At other joints, the difference was within 5 %. At the ankle, the distance between the bottoms of the foot is fixed; thus, differences in the center of rotation of the joint and narrowing of its range of motion occurred. At the shoulder joint, the directions of motions in which the range of motion when wearing the PAS is particularly reduced from that of the design model are adduction and flexion. This occurs because interference with the shoulder joint that covers the top of the clavicle prevents the wearer from raising his arms. In order to broaden the range of motion, it is necessary to form clearance with the clavicle by holding the shoulder joint in an arch-shape. Further, regarding flexion, an increase in the angle of flexion elevates the shoulder girdle, so under present conditions, it is necessary to improve the range of motion, which is 0°. For the back, the value was low for both the design model and the PAS when it is worn. The back frame has to support the upper body part of the PAS, so later flexion and rotation joints are not provided. Flexion and extension can be realized by the rotating joint of the hip joint.
Since it is an exoskeleton, the ranges of motion of the design model of the agricultural PAS differ from those of agricultural PAS when it is worn. Problems when it is worn, which are not revealed by the model alone, are clarified by the calculation of the DOF achievement rate.
Table 1Ranges of joint motion
Joint | Joint No. | Motion direction | Joint of human body | Design model | Wearing PAS | ||
Shoulder | Shoulder | Complex | 1 | Flexion | 160 | 125 | 90 |
Extension | 40 | 40 | 40 | ||||
2 | Abduction | 130 | 110 | 80 | |||
Adduction | 25 | 30 | 20 | ||||
3 | External rotation | 50 | 10 | 15 | |||
Internal rotation | 65 | 10 | 10 | ||||
Shoulder | Girdle | 4 | Flexion | 15 | 0 | 0 | |
Extension | 15 | 0 | 0 | ||||
5 | Elevation | 15 | 0 | 0 | |||
Deprassion | 5 | 0 | 0 |
Fig. 3Design model
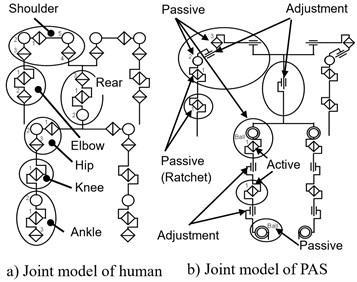
Fig. 4Comparison of DOF achievement rate
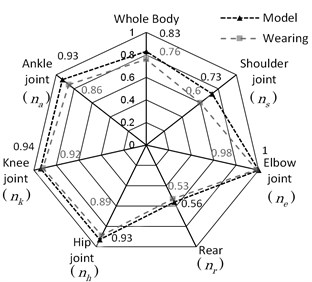
4. Analysis of farming operation
To use the agriculture PAS, it is necessary to understand the actual motions performed during agricultural work. So to measure the joint angles during the work, a variable resistance type rotary sensor (RDC502010A from ALPS ELECTRIC) was used to build a joint angle sensor and to measure angle data from the shoulder, elbow, thigh, and knee joints. Moreover, a video camera recorded videos of the work, motion patterns were classified based on the videos, and the evaluation was done by the OWAS method. The agricultural work to be evaluated was selected according to the opinions of researchers at the Tokyo Metropolitan Agricultural and Forestry Research Center as harvesting radishes harvesting cucumbers, and pruning fruit trees as shown in Fig. 5, and their agricultural work motions were analyzed. The test subject was one male who had given informed consent.
4.1. Work for harvesting radish
The work posture according to evaluation of posture by the OWAS method is often a half-sitting posture, with the back bent forward and with both upper limbs lower than the shoulders. The operation of the lower limb joints while harvesting radishes was a repetitious constant pattern of motions. Next, the motion of the lower limbs was accompanied by constant motion of the upper limbs, which cyclically repeated identical motions.
4.2. Work for harvesting cucumber
Cucumbers are generally grown on fence-shaped racks and harvesting of ripened cucumber is done whenever necessary. The working posture according to posture evaluation by the OWAS method is often one where the lower limbs in a half-sitting posture with both legs bent, the back bent forward, and both the upper limbs are held at a level lower than the shoulders. Unlike the case when harvesting radishes, the motion pattern is not repetitive. The reason is that the location of the harvested crop is not regular was it is in the case of the radishes. Cucumbers are at various heights from the top to the bottom of the racks, so the workers frequently raise or lower their bodies to find the cucumbers amidst the leaves and branches, or to peer into the leaves and branches.
Further, the upper limbs move irregularly because it is necessary for the workers to push aside the leaves and branches in order to search for cucumbers and pick them.
4.3. Work for pruning fruit tree
Fruit trees are generally cultivated on flat shelves at locations slightly higher than the height of the workers. Therefore, the branches and fruits are above the workers’ heads so their arms are both raised and they are facing upwards. The work posture according to the posture evaluation by the OWAS method is often one where the workers are standing straight up with both arms extended, the backs are extended, and both arms are higher than the shoulders.
Pruning work is usually done with the shoulder joints flexed at around 90° and the elbow joints flexed at around 60° and performing small motions within a range of 30° according to the height of the branches and fruit. Since the workers elevate their arms for long periods of time, fatigue accumulates from the shoulders to the upper arms. The lower limbs remain almost straight, with the knee and waist joints occasionally flexing slightly when the worker moves. As this shows, when pruning fruit trees, workers often stand straight with their arms held above their shoulders, so this PAS is expected to lighten the work by supporting the upper limbs.
Fig. 5Farm work
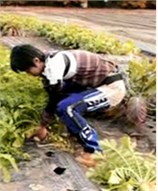
a) Radish
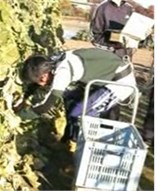
b) Cucumber
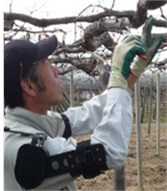
c) Fruit
4.4. Evaluation based on adaptability
Adaptability is defined as the extension of the DOF achievement rate, and is defined according to the range of motion of each joint manifested in the object of agriculture work motions and the range of joint motion of when the agricultural PAS is worn. It is defined by the following Eq. (5) when the range of joint motions of the body of a worker performing normal agricultural work is represented by , and the range of motion of joints during agricultural work by a worker wearing the agricultural PAS as :
The values of for each joint and for the whole body are calculated in the same way as the DOF achievement rate. The DOF achievement rate was obtained according to the maximum range of motion of the joints, but the operation of joints during work rarely achieves the maximum range of motion, and adaptability is a value higher than the DOF achievement rate. Fig. 6 shows the results of calculating adaptability.
It is possible to harvest radishes with well-balance motions, and a high whole body adaptability score of 0.92 was achieved. The whole body scores for harvesting cucumber and pruning fruit tree were relatively high scores of 0.84 and 0.83, respectively. However, in both cases, the values for the shoulder joints were low, and in cucumber harvesting, the score for the back was particularly low. For this reason, it is presumed to be necessary to improve adaptability for shoulder joints, or in other words, improve the range of joint motions of the shoulder joints. Next, the adaptability of the back in harvesting cucumber must be improved.
Evaluation based on adaptability revealed differences in the applicability of agricultural PAS to different types of agricultural work, permitting the identification of joints where there are problems.
Fig. 6Comparison of adaptability
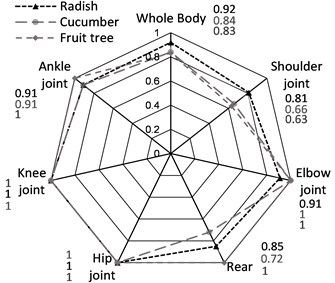
5. Conclusions
The agricultural PAS that had been developed was structurally evaluated, confirming that it achieved an approximately 70 % DOF of the human body and more than 90 % improvement of the DOF needed for work for harvesting radish. As this work showed, it was confirmed that a comparison of the DOF achievement rate of the design model and that of the worn model of the agricultural PAS can quantitatively define parts where motion of the human body is almost entirely achieved, and parts where motion is obstructed. Therefore, it showed the usefulness of evaluating the structure of an agricultural PAS. On the other hand, joints where reduction of the range of motion of the joint is a problem could be identified. Moreover, one type of agricultural work that will be particularly lightened according to analysis of agricultural work motions is pruning fruit tree, which involves only a few operations of joints in view of adaptability.
In the future, the shoulder joint structure, which showed a low DOF achievement rate, will be improved. At the same time the labor lightening effects on various types of agricultural work will be verified.
References
-
Sato M., Yagi E. A study on power assist suit using pneumatic actuators based on calculated retaining torques for lift-up motion. Proceedings of SICE Annual Conference, 2011, p. 628-632.
-
Nwe Y. Y., Toyama S., Akagawa M., Yamada M., Sotta K., Tanzawa T., Kikuchi C., Ogiwara I. Workload assessment with Ovako working posture analysis system (OWAS) in Japanese Vineyards with focus on pruning and berry thinning operations. Journal of the Japanese Society for Horticultural Science, Vol. 81, 2012, p. 320-326.
-
Toyama S., Yamamoto G. Wearable agrirobot. Journal of Vibroengineering, Vol. 12, 2010, p. 287-291.