Abstract
The objective of this paper is to study behaviors of detention made by AISI4340 in high temperature environment. The detention is used to hold the rocket until the rocket launched. The rocket launched with salvo type. Therefore detentions get high temperature from exhaust gas at 1,200 Celsius blow from rockets. There are the criteria are selection and evaluation, the initial torque for tightening the detention arm. In addition to avoid the failure of material and initially-tightened torque, the understanding of the structural load on the detention is significant. As the initial investigation, this paper presents the experiment test of detention including load behavior on guide knob and on the detention arm. The initially-tightening torques for the detentions were varied from 25-40 Nm. The results showed that detention made by AISI4340 with initial-tightened torque 40 Nm maintain the rocket with force greater than 17,500 N.
1. Introduction
The Defense Technology Institute (DTI) is initiating a number of research activities in defense industry. One of research projects is development of the rocket and the one important part of the rocket is “Detention”. The detention is attached on the launch tube and the “Guide Knob” on the Rocket is inserted in the detention to hold the rocket until the holding force is sufficient to launch the missile. In this case, the holding forces greater than 17,500 N. To protect the unexpected situations, the process was developed, designed, and investigated using the design of experiment test compared to numerical validation. However in the proposed design process, the detention force is important. In this experiment test and numerical simulation, we selected the controllable parameter as the main factors, size of guide knob, speed of guide knob, and condition of annealed. In this present work, the materials of detention are made by AISI4340 and diameter of guide knob is 12 mm.
Thasin Suansakaew [1], Parametric Study of Detention Behaviors, The results showed optimum material and torque for the detention are AISI4340 and torque 25 Nm.
Achirakris Julniphitwong and Thasin Suansakaew [2], Validation numerical of rocket detention against the tested data. Based on the analysis, the maximum pulling force from finite element is different from test 4.28 %, at the beginning, tension stress occurred on the detention is greater than compression stress because tension stress includes stress from tension and moment but compression stress is from moment that is subtracted by tension. While guide knob pass through detention, tension stress and compression stress is slightly different.
2. Detention design
Fig. 1Shows the geometry of the detention
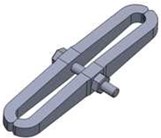
Fig. 1 shows the geometry of the detention. Detention is designed in order to hold the guide knob, attached to the rocket. The configuration of guide knob is cylinder with diameters of 12 mm. The guide knob is inserted in middle of detention.
3. AISI4340 material properties
For the mechanical properties of AISI4340, as temperature is increases the yield stress, tensile stress, hardness decreases below 50 %. As shown in Fig. 2.
Fig. 2AISI4340 material properties [3]
![AISI4340 material properties [3]](https://static-01.extrica.com/articles/16433/16433-img2.jpg)
4. Equipment
4.1. Soak in high temp
In this paper, Caldera-XL soak chamber is used to soak the detention as shown in Fig. 3. The operated on 120 volt household current and draws 15 amps.
4.2. Tensile Test
The test process is done using the Universal Tensile Machine Model: AG-100KNI M2 with reference tensile force based on the AWS D1.1/D1.1 M: 2010 standard test. The type of this experiment is tension test. The force is applied by equipment capacity of 10 tons until the distention cannot hold the guide knob and the maximum force is then measured as shown is Fig. 4.
Fig. 3Caldera-XL soak chamber for soak the detention [4]
![Caldera-XL soak chamber for soak the detention [4]](https://static-01.extrica.com/articles/16433/16433-img3.jpg)
Fig. 4Experiment test
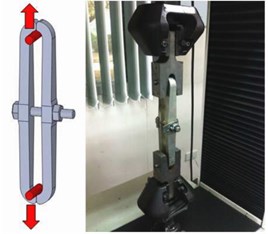
5. Experiment
5.1. Experiment test
Begin with tightened-initial torque 25 Nm [1]. We soak detention in soak chamber for 20 seconds with 1,200 Celsius [5]. Assumptions of the Launch rocket full pod. 1 Pod has 20 launch tubes. The rocket launch 1 second per rocket, Therefore the last detention that attached to the launch tube will get of thermal rocket earlier long 20 seconds. Then put detention into a tensile testing machine by pulling on the guide knob with speeds of 10 mm/min [1] and increase initial tightened torque until pulling force more than 17,500 N.
5.2. Experiment result
Results show after detention has been soak in chamber with 1,200 Celsius heat, when pull through with traction Tensile Detention lower than room temperature [1]. Obviously, the result detention pulling force is reduced due to the heat. We also found that the initial tightened torque need to pull force over 17,500 N is initial-tightened torque 40 Nm as shown in Fig. 5.
Fig. 5Pulling force for initial-tightened torque 25-40 Nm at 1,200 Celsius
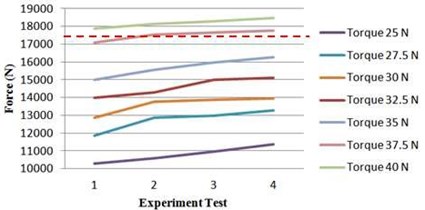
6. Finite element
6.1. Detention and guide knob model
2D plane analysis is used in finite element analysis. The 2D model is shown in Fig. 6.
6.2. Boundary condition
Fig. 7. shows boundary condition of detention and guild knob. The pulling speed is 10 mm/min.
Fig. 6The 2D model of detention
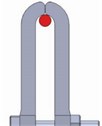
Fig. 7Boundary condition of detention and guild knob
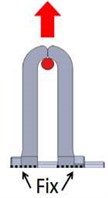
Fig. 8Shows comparison between experimental pulling force and finite element
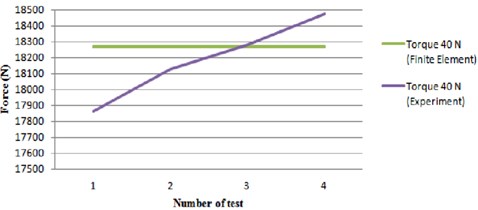
6.3. Finite element results
The experiment results shown when soak detention is soak at 1,200 Celsius for 20 second. Only initially-tightened torque 40 Nm archive force over 17,500 N. Therefore finite element simulates the pull detention only the initial-tightened torque 40 Nm. Fig. 8. Shows comparison between experimental pulling force and finite element. The maximum force pulling from finite element is 18,267 N. While from experiment test results are 17,861 N, 18,129 N, 18,283 N and 18,473 N. The average pulling force from experiment testing is 18,186 N, The difference between numerical and experimental force is 81 N or 0.45 %.
7. Conclusions
This paper applied finite element analysis and analytical model to describe the behaviors of detention. The results were validated against the tested data. Based on the analysis, we summarize that:
1) Detention properties that made by AISI4340 when temperature is increase, we found that Yield stress, tensile stress, hardness decreases below 50 %.
2) The initial-tightened torque for detention is 40 Nm for detention used for salvo launch with 1,200 Celsius.
3) The maximum pulling force from finite element is different 81 N (0.45 %) from experiment test.
References
-
Suansakaew T., Ridluan A. Parametric study of distension behaviors using design of experiment (DOE). Proceedings of Annual Conference on Engineering and Information Technology, South Korea, 2013.
-
Julniphitwong A., Suansakaew T. Numerical validation of rocket detention. Proceeding of International Congress on Natural Sciences and Engineering, Japan, 2014.
-
Joseph R. Davis ASM Specialty Handbook: Tool Materials. p. 148.
-
https://www.baileypottery.com/kilns/testkilns.htm
-
Yanga D., et al. Temperature measurement of solid rocket motor exhaust plume by absorption-emission spectroscopy. International Journal for Rapid Communication, Vol. 34, Issue 2, 2001