Abstract
The pipeline noise is an important part of the sources of vibration and noise for high performance marine vessels. It is vital to control the vibration and noise of the onboard pipeline to improve the acoustic stealth and life level in marine vessels. The vibration and noise caused by the onboard pipeline system was analyzed. Some methods and advices were put forwards to reduce the vibration and noise caused by the pipeline system, including the control of vibration, structural noise and fluid noise. In addition, a new concept “pressure-stabilized bladder” was created.
1. Introduction
The pipeline system is very complicated in marine vessels to fulfill its special function, such as the transference of energy, momentum and mass flow. At the same time, pipeline system is one of the sources to produce vibration and noise. Firstly, most of the mechanical equipment are not only connected with the vessels by foundation beds, but also by oil or water pipes. So the vibration and noise of the mechanical equipment can be transferred to the vessels. Secondly, because of the intermittence of the pump system (such as gear pump), it is indisputable to produce the pressure fluctuation and impulse. These kinds of vibration and noise can also be transferred to the hull and sea water. Hence it is important to control the vibration and noise of onboard pipelines.
2. Methods to control the vibration and noise of pipelines
In general, there are two methods in theory to control the vibration and noise of onboard pipelines.
1) Curb the sources of the vibration and noise (related machines or equipment). Actually, the vibration and noise of onboard pipelines are produced by mechanical equipment, and the sources of onboard pipeline vibration and noise can be divided into two groups. First, the direct sources of onboard pipeline vibration and noise, including all sorts of pumps, draught fans, air compressors, etc. These equipment contributes the fluctuation of the pressure and fluid quantity in the pipe and make them transferred in the way of wave because of the characteristics of the pipelines, thus leading to structural vibration. Feodos’ ev [1] and Niordson [2] have done many researches on the property of the fluid motion in a straight pipe and worked out some basic motion equations. The researches about Fluid-structure interaction [3-5] have been done can be divided into Poission coupling, Friction coupling, Jounction coupling and Bourdon coupling [6-7]. Another one is indirect sources of pipeline vibration and noise, such as main engine and auxiliary engine which provide power directly for those machines. The vibration and noise of them is transferred to the foundation bed or connection stuff at first. Then they are transferred to the onboard pipeline system. The direct sources are connected with the pipeline system, which can produce a huge impact on the pipeline system. So reducing the vibration and noise produced by the machines or equipment is the fundamental method to control the vibration and noise.
2) Curb the transmission by adopting some methods to prohibit the transportation of the vibration and noise. In many cases, it is hard to reduce the vibration and noise produced by the direct machines. But this kind of method can be taken effectively. In fact, this method has been widely used these days, and the results are pretty good. These are always flexible connections to reduce the transmission, damping materials to reduce the power of vibration, noise deadener and wave filter to reduce the noise of the fluid.
3. Ways to control the vibration and noise of the pipeline
The vibration and noise of the pipeline system can be divided into two sorts [8]. One is produced by all kinds of force in the machine, such as inertia force and gas explosive force, thus resulting in flexible vibration transferred to the onboard pipelines in flexible wave, then to the other places in marine vessels. This, high-frequency flexible wave, is usually called structural noise or solid-borne noise. The other one is produced by the pumps, draught fans and valves. When they are working, they can result in the fluctuation of the fluid (air, water or oil), which can be transferred by the fluid in the pipeline, always called fluid noise. Among these two sorts, structural noise is more harmful than fluid noise. This is because when structural noise is being transferred, it can produce noise in the air and strengthen the fluid noise in the pipeline. Furthermore, in some cases, fluid noise can also be transferred to structural noise and vibration of onboard pipelines.
3.1. Ways to control the structural noise
The vibration and noise of marine vessels are produced in two reasons. One is produced by the transmission of the vibration and structural noise in the connections between the machines and vessels. The other one is produced by the transmission of the fluctuation of fluid pressure, the vibration of the pipeline wall and structural noise in the connections between the pipeline and vessels. Consequently, in order to improve acoustic stealth and life level of marine vessels, the transmission of vibration and structural noise has to be curbed. The way to solve this is mainly to control the main engine and auxiliary engine.
There are two main ways that can produce the vibration of onboard pipelines and structural noise. One is the vibration produced by the machines which are connected directly with the pipeline, such as pumps and draught fans. The other one is the fluctuation of the fluid pressure or quantity when they are working. In some cases, this phenomenon can result in the structural vibration of pipeline walls and the transmission by them.
In order to reduce the transmission by these machines (pumps, draught fans etc.), vibration components can be used in pipeline systems, including vibration isolator, flexible pipe, elastic cradle, etc. [9]. For example, in order to curb the transmission and reduce the noise, flexible pipe is always used between the exit of the pump and the pipeline system. In fact, the way to use flexible pipe is to destroy the consecutiveness of the structure, thus reflecting or curbing the flexible wave of vibration. At the same time, when the displacement is too large, the flexible pipe can be the compensation. In foreign countries, many marine vessels have adopted this method (flexible pipe), they divide the pipe into many short ones to make them independent, thus curbing the vibration of one transferred to another one and reducing the fluctuation of fluid pressure in the pipe as well. Research on materials has been done by Mendelsohn [10], Falke [11], Qinghua Wang [12] and Cushman [13].
The structural noise of onboard pipelines is produced by the vibration and in order to control the structural noise, the vibration of onboard pipelines should be controlled at first. Nowadays, the common absorber is made of rubber [14]. Rubber is a kind of flexible and viscous material. The principle of rubber absorber is the characteristic of frictional damping in rubber absorber to reduce power of pipeline vibration and noise. This can isolate the vibration of onboard pipelines easily and smoothly, thus achieving the isolation of structural noise. On top of that, changing the setting ways of rubber absorber can reduce the vibration of straight pipe crosswise and lengthways. Rubber absorber has been widely used in the field of pipeline vibration control.
The instant change of the material physical property, section, the existence of valve, etc. can be the discrete points during the transmission of the flexible wave so as to reflect or curb some of the wave and reduce some of flexible wave or structural noise. Because of this phenomenon, a lot of ways can be adopted to control the vibration and structural noise, such as making the sudden change of material physical property and section, using rectangular pipe or branch pipes, flexible sandwich walls or connection equipment, etc. In addition, University of Southampton introduced a method to control the transmission of the vibration and structural noise in pipes by using air damping and circling spiral spring out of the pipes to produce frictional damping, thus achieving the reduction [15].
3.2. Ways to control the fluid noise
Fluid noise is another important noise. It can be divided into air noise and liquid noise according to different fluid (air, oil, water, etc.). Fluid noise is produced by the fluctuation of the fluid pressure or quantity, the sudden work of the valve and other external influence (the change of load), which can lead to structural vibration as well [16]. Fluid noise is mainly influenced by the machines and the impedance of system. The machines include all ones producing the fluctuation of fluid pressure or flow, such as air compressor and fluid pump. Of course, the fluctuation can also be produced by the sudden work of some fluid components, such as valve. The system impedance contains the impedance of onboard pipelines (influenced by the material and size of pipeline and property of the fluid) and the impedance of load. If the impedance of pipeline system corresponds the demands of harmonic vibration, harmonic vibration will be produced in pipeline system even though the disturbance of the machines is extremely small (such a small amplitude of the pressure fluctuation), thus leading to large fluctuation of fluid pressure and flow, severe structural vibration and noise.
In real fluid system, the fluctuation of the pressure and flow or even shock is unlikely to be vanished. Meanwhile some of these are in need in some systems when they are operating. In view of this, the possible ways to reduce vibration are limited. 1) Avoid harmonic vibration. 2) Spare no effect to reduce the amplitude of pressure and flow fluctuation in systems. In a word, to avoid or reduce the fluid noise in pipeline systems, controlling the machines and adjusting the impedance property of the system is the main way.
3.2.1. Controlling related machine or equipment
Reducing the influence of the machines is to reduce the pressure, flow quantity or shock produced by fluid components.
In general, as the power components of fluid systems (such as pump, air compressor), flow fluctuation cannot be avoided because of the working principle. As for high-pressure and high-flow pump (ram pump, gear pump, etc.), the amplitude of flow fluctuation is also very large, thus always becoming the source of vibration in pipeline systems. But this phenomenon can be improved by coping with the structure and parameters of some components. For example, theoretical analysis shows that when the number of rams in ram pump is odd, the fluctuation of flow is smaller than it is even. So most ram pumps are designed in the former way in industry. At the same time, in many pipeline systems, the shock and fluctuation of pressure and flow always occur because of the sudden work of the valve (such as water attack). Furthermore, because of the importance and irreplaceable function of valve, it is hard to vanish the shock of flow or pressure. So the main problem is to reduce the influence of valve. Generally, adjusting reasonable process of the open, close and time of the valve can reduce the pressure shock produced by water attack. In most cases, the shorter it takes to close the valve, the higher the amplitude of the pressure shock. Consequently, dividing two or three steps to close the valve can make the pressure shock smallest.
3.2.2. Adjusting the impedance property of the system
Measures in controlling machines can just partly reduce the pressure or flow fluctuation. But if the pipeline systems correspond the demands of harmonic vibration, no matter how low the amplitude is, severe vibration will be produced in the system. In this situation, the way, adjusting the impedance property of the system, should be adopted.
Adjusting the impedance of the system is to adjust the harmonic vibration point to avoid the main frequency of the machines’ pressure or flow fluctuation and avoid harmonic vibration occurred. This way is the same as reducing the impedance of machines or the impedance of load.
There are many measures to adjust the impedance and avoid the harmonic vibration frequency, thus reducing the fluctuation of pressure. For instance, changing the length of the pipe, the section size of pipe, the site of components installed and adding some fluid components can adjust the impedance of the system. Among these methods, adjusting the length of pipe is the main and the most available way. By adopting the method of impedance analysis, the impedance can be measured during the process of designing one new fluid system. So the structure and parameter can be optimized in this way, thus reducing or even vanishing the possible pressure fluctuation.
Industrially, adding a flexible pipe (corrugated pipe, elastic pipe, rubber pipe, etc.) can not only isolate the vibration, but also reduce the vibration in the fluid because of the small elasticity modulus in equivalent volume and the flexibility to absorb the flow fluctuation from pumps. While from the perspective of system impedance analysis, adding one more flexible pipe cannot necessarily reduce the pressure fluctuation of pipeline system. What is worse, sometimes this can aggravate the pressure fluctuation. The reason is that the transmission of the flexible pipe and the hard pipe frequency domain is similar. The obvious difference between them mainly is the volume elasticity modulus and the velocity of pressure wave (can be revised by an equivalent pipe length). When flexible pipe is added, the transfer matrix of the new system is the combination of the old one and the flexible pipe transfer matrix. The characteristic of the pressure fluctuation will be determined by the new system instead of the flexible pipe only. If the new system corresponds the demands of harmonic vibration, the phenomenon of severe vibration fluctuation will occur as well. So in order to add one flexible pipe, the equivalent length and harmonic vibration demands of the new system must be considered. While in fact, it is really hard to estimate the equivalent length precisely because of the non-linear property of pressure frequency of the flexible pipe (most flexible pipes are made of viscoelastic materials).
3.2.3. Adding oscillation damping or filtering components
In the fluid systems, it is extremely hard to vanish the pressure fluctuation produced by the machines. On top of that, adjusting the impedance characteristic (such as the pipe length, the components’ structure, etc.) is also influenced by the sound design of the system (such as working situation of the system, the site of the components installed). So adding oscillation damping or filtering components to the pipeline system is the only measure to reduce or absorb the fluctuation of flow pressure. In fact, this is also an important way to adjust the impedance property of the system.
Recently, in fluid engineering, the oscillation damping or filtering components used in fluid pipeline system are always different filters, accumulators, pore plates, etc. According to acoustic characteristic, they can be divided into harmonic filter and interferential filter.
Harmonic filter is also called oscillating filter. The principle of this is to absorb the fluctuation of the pressure and flow by the harmonic vibration of the fluid in the filter. For example, series harmonic filter is connected to the pipeline in series (C filter, π filter, K filter), branching harmonic filter is connected to the branch of the main pipe (L filter, H filter, T filter, taper H filter, combined H filter).
Interferential filter is a kind of parallel filters in pipeline systems. It can reduce and vanish the fluctuation of the pressure and flow by the interference among parallel pipe waves. After adopting this kind of filter, the interference among waves just causes the redistribution of the power in the pipeline, rarely influencing the machines. This filter owns great damping property, such as Quincke filter, Dulsco filter. Accumulator is always used as a kind of ease-vibration components which can absorb the flow fluctuation produced by the machine in many pipeline systems. Generally, the setting of accumulator in pipeline is similar with H or T filter and the result of reducing the vibration filter is excellent because of the squeezability of the fluid or gas in accumulator. But in fact, accumulator only suits for low frequency fluctuation as for low stiffness of accumulator, which can lead to low frequency response.
In addition, installing one or more pore plates in some reasonable places can also reduce the fluctuation of pressure and flow, thus achieving vibration easing. In engineering, this method is easier and more convenient, and the reduction is well. This is the reason why it is widely used in many occasions.
On top of that, active noise elimination technology can also be used. The main principle of this is producing a sound field equal in strength and opposite in orientation with the superposition principle of sound wave to offset the intrinsic sound wave in the same field and reduce the noise.
3.3. Pressure-stabilized bladder
A new concept “pressure-stabilized bladder” (showed in Fig. 1) has been created, which is a control component. Pressure-stabilized bladder can adjust the pressure in the pipe by changing its size, displacement, etc. It should be made of flexible materials. There are measuring instrument and active control components in pressure-stabilized bladder to fulfill this function. This bladder can especially be used in the exit of equipment (pump, air compressor, etc.), corners, branch points, etc. In addition, if there is something wrong that makes the pressure in the pipe over high, the pressure-stabilized bladder can ease the pressure by expansive action, thus protecting the pipeline systems.
More research on pressure-stabilized bladder can be done in the future, including the material, size, active control components, etc. Besides, some simulations and experiments can be conducted as well.
Fig. 1Pressure-stabilized bladder
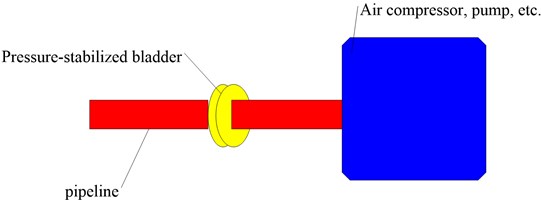
4. Conclusions
In conclusion, three main methods should be taken with the aim of reducing the vibration and noise in pipeline system.
1) Controlling the sources of vibration and noise should be the priority. This is the most effective and fundamental way. Additionally, when choosing the machines and equipment in marine vessels, which with less vibration and noise should be taken into consideration. In terms of the equipment which has been installed, distinguishing the reasons and the site of the vibration and noise produced is of paramount importance, then corresponding methods should be taken.
2) Control the process of vibration and noise transferred. Generally, the design of the machines or equipment is the first step when setting a system. After that, the pipeline system should be designed according to the whole system. Hence the design with the aim of reducing vibration should be prioritized. For instance, changing the positions of the pipes or valves and altering vibration modal parameters can both achieve the destination. Flexible connection can also isolate and reduce the vibration and noise of pipeline system. For example, using flexible pipe between the machines and the pipeline system can effectively work. Additionally, vibration absorber and installing noise deadener in pipeline system can also decrease the level of vibration and noise.
3) Measures to reduce the vibration and noise of onboard pipeline system in marine vessels should be taken according to the whole situation and total effect, thus achieving great property, high efficiency, long lifespan and easy to maintain.
With the development of the research of vibration and noise control and new material technology, computer technology and automatic control technology, the methods to control vibration and noise can be further improved, followings are some aspects:
a) More research can be done on low-noise materials.
b) New materials with high acoustic absorptivity and low damping used during the process of vibration and noise transferring.
c) Air sac, steel wire rope and new non-linear vibration isolator materials can be researched more and will be widely used in the future.
d) More research can be done on magnetostriction materials to improve the active control and automatic control.
e) Automatic control technology and adaptive technique can be researched more to further reduce the vibration and noise and improve the ability of automation.
f) More research on pressure-stabilized bladder can be done in the future, especially the material, size, active control components, etc.
References
-
Feodos'ev V. Vibrations and stability of a pipe when liquid flows through it. Inzhenernyi Sbornik, Vol. 10, Issue 1, 1951, p. 69-70.
-
Niordson F. I. Vibrations of a Cylindrical Tube Containing Flowing Fluid. Ingeniosvetenskapsakad, 1953.
-
Benjamin T. B. Dynamics of a system of articulated pipes conveying fluid. 1. Theory. Proceedings of the Royal Society of London Series a Mathematical and Physical Sciences, Vol. 261, Issue 1307, 1961, p. 457-86.
-
Tijsseling A. Fluid-structure interaction in liquid-filled pipe systems: a review. Journal of Fluids and Structures, Vol. 10, Issue 2, 1996, p. 109-46.
-
Gregory R., Paidoussis M. Unstable oscillation of tubular cantilevers conveying fluid. 1. Theory. Proceedings of the Royal Society of London Series a Mathematical and Physical Sciences, Vol. 293, Issue 1435, 1966, p. 512-527.
-
Ren Jiangting, Jiang Jieshen The development of pipeline system vibration. The Development of Dynamics, Vol. 33, Issue 3, 2003, p. 313-324.
-
Zhang Lixiang, et al. The development of fluid-structure interaction in pipeline system vibration. Chinese Journal of Hydrodynamics, Vol. 15, Issue 3, 2000, p. 366-379.
-
Shi Ying, Zhu Shijian, He Lin Power and Mechanical Noise Control in Vessels. National Defend Industry Press, Beijing, 1990.
-
Li Xiaochen, Wu Wangyang, Zhang Bo Analysis and Control on Vibration and Noise of Hydraulic System. Technology Innovation and Application, 2015.
-
Bolton R., Mendelsohn M. A., Navish Jr F. W. Sound Absorbing and Decoupling Syntactic Foam. Google Patents, 1995.
-
Falke P., Rotermund I., Schmutzer K., et al. Production of Sound-Damping and Energy-Absorbing Polyurethane Foams. Google Patents, 2001.
-
Wang Qinghua, Liu Hongyu, Li Xiaodong, et al. Research on underwater silicon rubber coating material sound absorption performance. Special Purpose Rubber Products, Vol. 29, Issue 2, 2008, p. 23-25.
-
Cushman W. B., Thomas G. B. Acoustic Attenuation and Vibration Damping Materials. Google Patents, 1995.
-
Jiang Xuewu, Zhu Shijian Application of rubber absorber in vessels. Journal of Navel University of Engineering, Vol. 4, 2000, p. 90-91.
-
Yin Rong, Hu Jianlin Vibration research on fluid pipeline. Noise and Vibration Control, Vol. 5, 1996, p. 18-23.
-
Cai Yigang Pipeline Dynamics of Fluid Transmission. Zhejiang University Press, Hangzhou, 1990.
About this article
Thank Xuewei Liu for giving advices on this paper’s structure and thanks are given to Jisuo Li for his help in searching for materials.