Abstract
Crack fault of a centrifugal impeller occurred while working. The finite element model of the impeller was established and vibrational characteristics were analyzed for to find the reason of the crack fault in this paper. The resonance frequencies of the impeller were identified with the help of Campbell diagrams. The modal experiments were carried out with hammering method, the modal parameters were obtained and the correct of the simulations was verified under the same constraints with the FEM model. Computation effort was saved while accuracy was retained making use of the cyclic symmetry technique in ANSYS. The results showed that simulating results agreed well with that of the experiments.
1. Introduction
The centrifugal impeller the axial flow compressor suffered enormous centrifugal and aerodynamic force under high-speed rotating. At the same time, workload and working environment of impeller were very complicated due to alternating load by vibration, corrosion and oxidation during working time. A crack fault occurred in the actual working was discussed about the impeller in this paper. Analysis results with fracture surface indicated a fatigue crack. Two possible reasons were preliminary speculated: resonance or forced vibration caused by the rectifying plate’s wake before the impeller [1-4]. The movement dynamics equations about the impeller of multiple degrees of freedom were written as:
where M¨u(t) and C˙u(t) are called as centrifugal force and aerodynamic force of blade surface, M,C and K as mass, damp and stiffness matrix respectively, u(t), ˙u(t) and ¨u(t) mean displacement, velocity and acceleration respectively. f(t) represent gas static pressure [5].
2. Simulation
2.1. The finite element model
The finite element model was established for the 1/16 of centrifugal impeller basing on actual centrifugal impeller structure. The vibration characteristic analysis was completed for whole of centrifugal impeller with cyclic symmetry method in this paper [5]. The impeller modals were calculated basing on the basic sectors with the help of large general structural analysis software ANSYS. The model was divided into 981522 elements and 192280 nodes and Solid 185 element was adopted in ANSYS. The inner diameter about front face and end face of the disk were constrained axially and circumferentially. The model about 3-D and grid of basic sector were shown as Fig. 1 [6].
Fig. 1Model
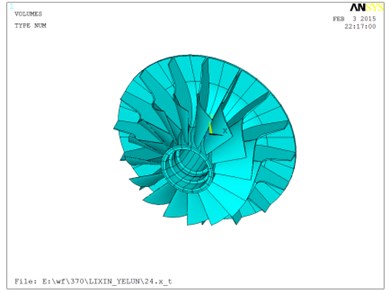
a) 3-D model
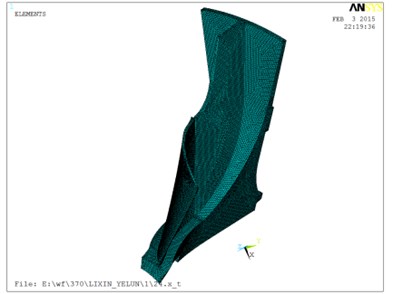
b) Grid of the basic sector
2.2. Simulation results
The Block-Lanczos method was applied to extract eigenvalues and eigenvectors. The natural frequencies changed as the rotating speed due to the rotating stiffening effect. The centrifugal force was applied by the prestress analysis in ANSYS to consider the rotating stiffening effect. Modal analysis were conducted under 700 rad/s, 1400 rad/s, 2100 rad/s, 2800 rad/s, 3500 rad/s, 4200 rad/s, respectively. The results were listed according to the number of nodal diameter. Campbell diagrams were shown as Fig. 2. The horizontal axis was the rotational speed and the vertical axis was the natural frequency [7-10].
Fig. 2Campbell diagram
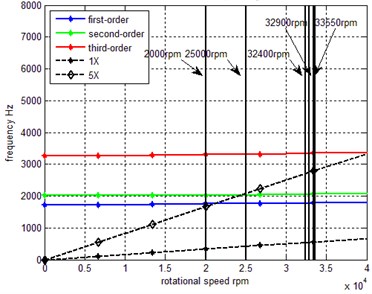
a) 0 nodal diameter
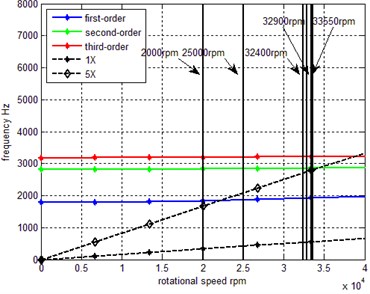
b) 1 nodal diameter
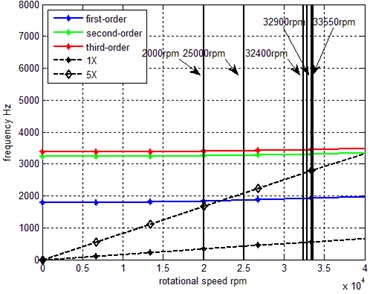
c) 2 nodal diameter
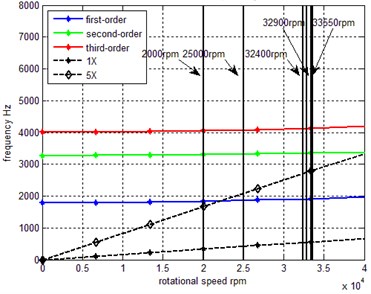
d) 3 nodal diameter
From the results of Campbell diagrams, there is no dangerous resonance frequency of 1X while there are some dangerous resonance frequencies of 5X. The dangerous frequencies occurred in the first natural frequencies of 0 nodal diameter and the second natural frequencies of 1 nodal diameter. The Fig. 2 showed that the discrepancy between resonance speed 34440 rpm and operating speed 33550 rpm was 2.65 %. Corresponding mode shapes were similar to centrifugal impeller crack failure shape, shown as Fig. 3.
Fig. 3Mode shapes
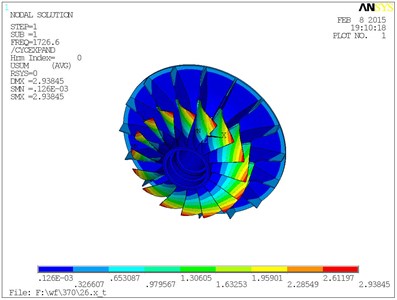
a) Mode shape of 0 nodal diameter
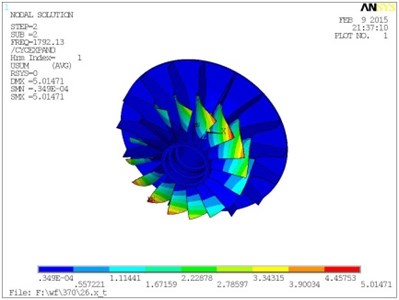
b) Mode shape of 1 nodal diameter
In addition, the common speeds operated on 20000 rpm (333.3 Hz, 2093.3 rad/s), 25000 rpm (416.7 Hz, 2612.5 rad/s), 32400 rpm (540 Hz, 3391.2 rad/s), 32900 rpm (548.3 Hz, 3443.5 rad/s), and 33550 rpm (559.2 Hz, 3511.6 rad/s) for the centrifugal impeller. According to Campbell diagram, first-order and second order of 0 nodal diameter resonant frequency occurred near by the 21000 rpm and 24000 rpm respectively. At the same time, second-order of 1 nodal diameter resonance frequency occurred near by 34000 rpm. The extreme difficulties existed for to avoid the resonance frequency. These rotating speeds likely resulted in resonance.
Fig. 4Test mode
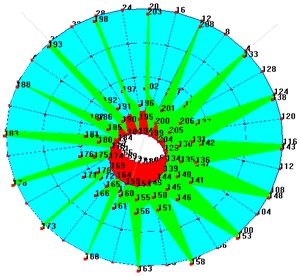
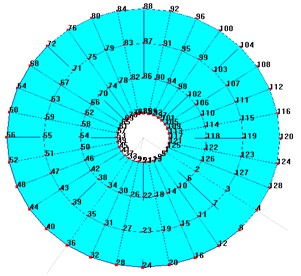
3. Modal test and analysis
The correctness of the calculation results were verified by the model analysis test with hammering method. Geometry model which needed to correspond with the transfer function was the basis of the modal animation display. The geometric structure figure, which had 208 geometric points, was shown as Fig. 4 for the impeller disk basing on experiment scheme. Every point should be measured at least 5 times and the measured mean value was used as the data of analyzing transfer function to improve the measuring accuracy in modal test. According to the defined geometric relations and directions of force, experimental data collection was completed under the same constrained condition. Every point’s input force and output response signal was calculated under the analyzing window, which could get relevant transfer function. Frequency domain method was used in the process of modal fitting. Frequency and vibration mode comparison results were shown as Fig. 5 and Table 1.
Table 1The comparison of frequency
Nodal diameter | 1 | 2 | 3 |
Test frequency (Hz) | 1637 | 3479 | 4038 |
Calculate frequency (Hz) | 1792.1 | 3357 | 4003.3 |
Error | –8.6 % | 3.6 % | 7.6 % |
Fig. 5The comparison of test modes and theoretical modes
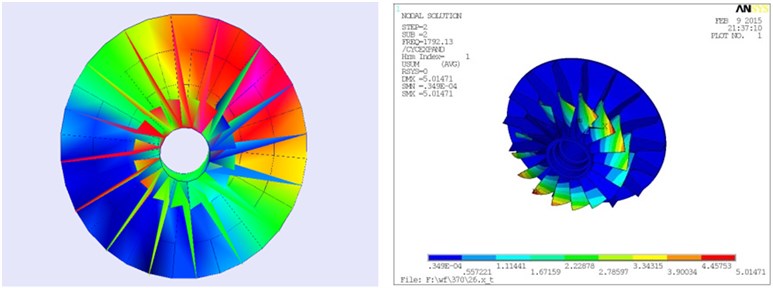
a) The comparison of test and theoretical mode shape about 1 nodal-diameter
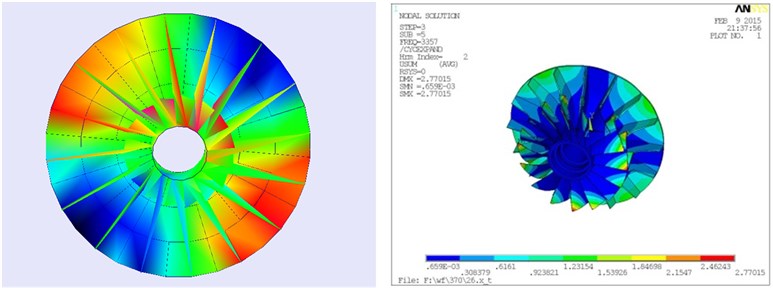
b) The comparison of test and theoretical mode shape about 2 nodal-diameter
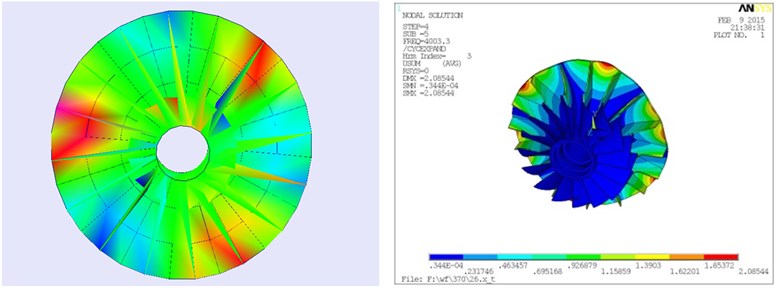
c) The comparison of test and theoretical mode shape about 3 nodal-diameter
The errors of results between calculating and testing excited –8.6 %, 3.6 % and 7.6 % separately about the impeller in the static frequency condition from Table 1 and Fig. 5. The calculating accuracy was verified by the modal test for cyclic symmetry method applied FEM in ANSYS.
4. Conclusions and future prospect
Comparing difference between the dynamic characteristics analyzed exactly by cyclic symmetry technique and taking into consideration of rotating stiffening effect in ANSYS and modal testing in the paper, the reasons of the fault were concluded as followings.
1) The resonance frequencies of the impeller were closed to multiple operating frequencies according to the Campbell diagrams. It was possible that the resonances occurred nearby the rotating speeds of 21000 rpm, 24000 rpm and 34000 rpm. Especially, the crack failure shape of the impeller was similar to the shape of the maximum strain position about second natural frequencies of 1 nodal diameter, it was possible to lead to fatigue crack failure if the impeller worked at above rotating speeds.
2) The modal parameters and mode shapes obtained by modal test about static frequency were basically agreed with the simulating results under the same constraints. The accuracy of simulating method was verified.
3) The impeller modals were extremely rich. To adjust the resonance frequencies were difficult. It was too hard to coordinate the contradiction between structure and frequency. Therefore, the vibration of the axial flow compressor should be closely monitored.
4) On the foundation, the frequency spectrum would be analyzed in consideration of the forced vibration under the aerodynamic force of the rectifying plate.
References
-
Chen Xiang, Zhu Jing, Zhang Ya Vibration characteristics analysis of blisk with cracking blades on axial flow compressor. Journal of Aerospace Power, Vol. 30, Issue 5, 2015, p. 1141-1148, (in Chinese).
-
Saito A., Castanier M. P., Pierre C. Effects of a cracked blade on mistuned turbine engine rotor vibration. Journal of Vibration and Acoustics, Vol. 131, Issue 6, 2009, p. 1-9.
-
Jin Xiangming, Gao Deping, Cai Xianxin, Wu Liqiang Analysis of integrated centrifugal impeller blade vibration reliability. Journal of Aerospace Power, Vol. 19, Issue 5, 2004, p. 610-613, (in Chinese).
-
Huang B. W. Effect of number of blades and distribution of cracks on vibration localization in a cracked pre-twisted blade system. International Journal of Mechanical Sciences, Vol. 48, Issue 1, 2006, p. 1-10.
-
Mao Yijun, Qi Datong, Xu Qingyu Numerical study on high cycle fatigue failure of a centrifugal compressor impeller blades. Journal of Xi’an Jiao Tong University, Vol. 42, Issue 11, 2008, p. 1136-1139.
-
Fang X., Tang J., Jordan E., et al. Crack induce vibration localization in simplified bladed disk structures. Journal of Sound and Vibration, Vol. 291, Issue 1, 2006, p. 395-418.
-
Laxalde D., Thouverez F., Lombard J. P. Dynamical analysis of multistage cyclic structures. Mechanical Research Communications, Vol. 34, Issue 4, 2007, p. 379-384.
-
Laxalde D., Thouverez F., Lombard J. P. Dynamical multistage bladed disks systems. Journal of Engineering for Gas Turbines and Power Vol. 129, Issue 4, 2007, p. 1058-1064.
-
Yang Xingyu, Geng Zhongxing, Cai Xianghui Fracture analysis of the 2nd stage compressor blade in an aeroengine. Journal of Aerospace Power, Vol. 16, Issue 4, 2001, p. 327-330, (in Chinese).
-
Ejaz N., Salam I., Tauqir A. Fatigue failure of a centrifugal compressor. Engineering Failure Analysis, Vol. 14, Issue 7, 2007, p. 1313-1321.