Abstract
The free vibration of parallelogram plate with varying thickness and thermal effect are investigated in the present study. Using the separation of variables method, the governing differential equation has been solved for vibration of visco-elastic orthotropic parallelogram plate. An approximate but quite convenient frequency equation is derived by using Rayleigh-Ritz technique with a two-term deflection function. The frequencies corresponding to the first two modes of vibrations are obtained for a parallelogram plate for different values of taper constant and thermal gradient.
1. Introduction
Visco‐elastic behaviour may be defined as material response that exhibits characteristic of both a viscous fluid and an elastic solid. A visco‐elastic material combines these two properties it returns to its original shape after being stressed, but does it slowly enough to oppose the next cycle of vibration. The degree to which a material behaves either viscously or elastically depends mainly on temperature and rate of loading (frequency). Many polymeric materials (plastic, rubbers, acrylics, silicones, vinyls, adhesive, etc.) having long chain molecules exhibit visco‐elastic behaviour. The dynamic properties (shear modulus, extensional modulus, etc.) of linear visco-elastic materials can be represented by the complex modulus approach.
Plates of various geometries are commonly used as structural elements in various fields of engineering such as civil, naval and mechanical. Their design requires an accurate determination of their natural frequencies and mode shapes. In particular, rectangular plates are widely used in ocean structures and aerospace industry. Plates with varying thickness possess a number of attractive features such as material saving, weight reduction, stiffness enhancing, high strength and also meet the desirability of economy.
Vibration effects have always been a principle concern of engineers. In the epoch of science and technologies it is desired to design large machines with smooth operation and unwanted vibrations. Sometimes unwanted vibration causes fatigues. Unwanted vibration can damage electronic components of aerospace system, damage buildings by earthquake, bring tsunami, and contribute to toppling of tall smokestacks, collapse of a suspension bridge in a windstorm. There are a multitude of applications where vibration effect is required e.g. in string and percussion instruments, in the design of loudspeakers, space shuttles, satellites where discrepancies in the temperature also affects the vibration effect. Controlled vibration effects are also required in health industry, paper industry, design of structures, building construction, reducing soil adhesion and many more areas engross vibration upshot.
Recently, Leissa [1, 2] has given the solution for rectangular plate of variable thickness. Gupta, Johri and Vats [3] have discussed the thermal effect on vibration of non-homogeneous orthotropic rectangular plate having bi-directional parabolically varying thickness. Gupta and Khanna [4] have solved the problem of free vibration of visco-elastic rectangular plate with linearly thickness variations in both directions. Singh and Saxena [5] have discussed the transverse vibration of rectangular plate with bi-directional thickness variation. Sobotka [6] has investigated the vibration of rectangular orthotropic visco-elastic plates. A. K. Gupta, Amit Kumar, Dhram Veer Gupta [7] studied vibration of visco-elastic orthotropic parallelogram plate with parabolically thickness variation. Warade and Deshmukh [8] discussed thermal deflection of a thin clamped circular plate due to partially distributive heat supply. Sobotka [9] discussed rheology of orthotropic visco-elastic plates. Gupta and Kumar [10] analyzed vibration of non-homogeneous visco-elastic rectangular plates with linearly varying thickness. Khanna A., Kaur N., Sharma A. K. [11] have discussed effect of varying poisson ratio on thermally induced vibrations of non-homogeneous rectangular plate. Sharma S. K., Sharma A. K. [12] have discussed the mechanical vibration of orthotropic rectangular plate with 2d linearly varying thickness and thermal effect. Khanna A. and Sharma A. K. [13] have solved the problem on vibration analysis of visco-elastic square plate of variable thickness with thermal gradient. Kumar Sharma A., Sharma, S. K. [14] have discussed the vibration computational of visco-elastic plate with sinusoidal thickness variation and linearly thermal effect in 2d. Khanna A., Kumar A., Bhatia M. [15] has investigated the computational prediction on two dimensional thermal effects on vibration of visco-elastic square plate of variable thickness. Khanna A., Sharma A. K. [16] studied natural vibration of visco-elastic plate of varying thickness with thermal effect. Kumar Sharmas A., Sharma S. K. [17] discussed free vibration analysis of visco-elastic orthotropic rectangular plate with bi-parabolic thermal effect and bi-linear thickness variation. Sharma S. K., Sharma A. K. [18] discussed effect of bi-parabolic thermal and thickness variation on vibration of visco-elastic orthotropic rectangular plate. Khanna A. and Sharma A. K. [19] mechanical vibration of visco-elastic plate with thickness variation. Khanna A., Kaur N., Sharma A. K. [20] effect of varying poisson ratio on thermally induced vibrations of non-homogeneous rectangular plate. Khanna A. and Sharma A. K. [21] analysis of free vibrations of visco elastic square plate of variable thickness with temperature effect.
Hence vibrations totally affect our day-to-day life. Thus for design engineers and scientist, it has always been a necessity to optimize or to control the effect of unwanted vibrations as much as possible. Present work is a full-fleshed endeavour to assist the design officers, industry people to come up to the situation.
The object of the present study is to determine the effect of a constant thermal gradient on the frequencies of a clamped parallelogram plate with linearly varying thickness. All the edges are taken as clamped. The Rayleigh-Ritz technique has been used to determine the frequencies equation of the plate. The frequency to the first two modes of vibration is obtained for a clamped parallelogram plate for various values of thermal gradient and taper constant.
2. Parallelogram plate and analysis
The parallelogram plate Z is shown in the Fig. 1 with oblique and rectangular co-ordinate system.
Fig. 1Parallegram plate
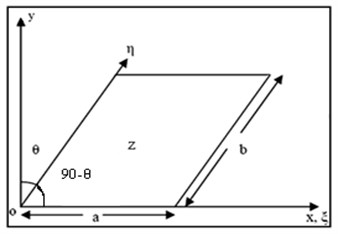
The parallelogram plate Z be defined by the three number a, b and θ as shown Fig. 1. The special case of rectangular plate follows by putting θ= 0°, here:
Bending and twisting moments of visco‐elastic parallelogram plate of variable thickness are related to displacement by:
where, Dξ and Dη are flexural rigidities of plate, Dξη is torsional rigidity of plate, ˇD is unique rhelogical operator.
The governing differential equation of transverse motion of visco‐elastic orthotropic parallelogram plate of variable thickness, ξ‐ and η‐ co‐ordinates, is [7]:
+(secθ)(6Dηtan2θ+2H)w,ξξηη-4(Dηtanθsec3θ)w,ξηηη
+(Dηsec4θ)w,ηηηη+2(H,ξtan2θ-H,ηtanθ+Dξ,ξ-Dη,ηtan3θ)w,ξξξ
-2(secθ)(2H,ξtanθ-H,ηtanθ-3Dη,ηtan2θ)w,ξξη
+2sec2θ(H,ξ-3Dη,ηtanθ)w,ξηη+2(Dη,ηsec3θ)w,ηηηη
+(Dξ,ξξ+Dη,ξξtan4θ-2Dη,ξηsecθtan3θ+Dη,ηηsec2θtan2θ
+3D1,ξξtan2θ-2D1,ξηsecθtanθ+D1,ηηsecθ+4Dξη,ξξtan2θ
-4Dξη,ξηsecθtanθ)w,ξξ-2Dη,ξξsecθtan3θ+4Dη,ξηsec2θtan2θ
-2Dη,ηηsec3θtanθ-2D1,ξξsecθtanθ-4Dξη,ξξsecθtan2θ
+4Dξη,ξηsec2θ)w,ξη+(Dη,ξξsec2θtan2θ-2Dη,ξηsec3θtanθ
+Dη,ηηsec4θ+D1,ξξsec2θ)w,ηη]+ρhw,tt=0.
A comma followed by a suffix denotes partial differential with respect to that variable. The solution of Eq. (3) can be taken in the form of products of two functions as for free transverse vibration of the visco‐elastic orthotropic parallelogram plate, w(ξ,η,t) can be expressed as:
where T(t) is the time function and W is the maximum displacement with respect to time t.
Substituting Eq. (4) into Eq. (3), one obtains:
+(secθ)(6Dηtan2θ+2H)W,ξξηη-4(Dηtanθsec3θ)W,ξηηη
+(Dηsec4θ)W,ηηηη+2(H,ξtan2θ-H,ηtanθ+Dξ,ξ-Dη,ηtan3θ)W,ξξξ
-2(secθ)(2H,ξtanθ-H,ηtanθ-3Dη,ηtan2θ)W,ξξη
+2sec2θ(H,ξ-3Dη,ηtanθ)W,ξηη+2(Dη,ηsec3θ)W,ηηη
+(Dξ,ξξ+Dη,ξξtan4θ-2Dη,ξηsecθtan3θ+Dη,ηηsec2θtan2θ
+3D1,ξξtan2θ-2D1,ξηsecθtanθ+D1,ηηsecθ+4Dξη,ξξtan2θ
-4Dξη,ξηsecθtanθ)W,ξξ-2Dη,ξξsecθtan3θ+4Dη,ξηsec2θtan2θ
-2Dη,ηηsec3θtanθ-2D1,ξξsecθtanθ-4Dξη,ξξsecθtan2θ
+4ξηsec2θ)W,ξη+(Dη,ξξsec2θtan2θ-Dη,ξηsec3θtanθ
+Dη,ηηsec4θ+D1,ξξsec2θ)W,ηη]/ρhW=-T,tt/ˇDT.
The proceding equation is satisfied if both of its sides are equal to a constant. Denoting this constant by p2, we get two equations:
+(secθ)(6Dηtan2θ+2H)W,ξξηη-4(Dηtanθsec3θ)W,ξηηη
+(Dηsec4θ)W,ηηηη+2(H,ξtan2θ-H,ηtanθ+Dξ,ξ-Dη,ηtan3θ)W,ξξξ
-2(secθ)(2H,ξtanθ-H,ηtanθ-3Dη,ηtan2θ)W,ξξη
+2sec2θ(H,ξ-3Dη,ηtanθ)W,ξηη+2(Dη,ηsec3θ)W,ηηη
+(Dξ,ξξ+Dη,ξξtan4θ-2Dη,ξηsecθtan3θ+Dη,ηηsec2θtan2θ
+3D1,ξξtan2θ-2D1,ξηsecθtanθ+D1,ηηsecθ+4Dξη,ξξtan2θ
-4Dξη,ξηsecθtanθ)W,ξξ-2Dη,ξξsecθtan3θ+4Dη,ξηsec2θtan2θ
-2Dη,ηηsec3θtanθ-2D1,ξξsecθtanθ-4Dξη,ξξsecθtan2θ+4ξηsec2θ)W,ξη
+(Dη,ξξsec2θtan2θ-Dη,ξηsec3θtanθ+Dη,ηηsec4θ+D1,ξξsec2θ)W,ηη]
-ρp2hW=0.
Eqs. (6) is the differential equation of motion for visco‐elastic orthotropic parallelogram plate of variable thickness.
2.1. Equation of motion
The expressions for the strain energy, Smax, and kinetic energy, Kmax, in the visco‐elastic parallelogram plate when executing transverse vibration of mode shape W(ξ,η) are [7]:
+2D1W,ξξ(W,ξξtan2θ+2W,ξηtansecθ+W,ηηsec2θ)+4Dξη(-W,ξξtanθ
+W,ξηsecθ)2]cosθdηdξ,
Assuming that parallogramic plate of engineering material has a steady two dimensional linear temperature distribution i.e.:
where τ denotes the temperature excess above the reference temperature at any point on the plate and τ denotes the temperature at any point on the boundary of plate and a and b are the length of a side of square plate. The temperature dependence of the modulus of elasticity for most of engineering materials can be expressed in the:
where, E0 is the value of the Young’s modulus at reference temperature i.e. τ= 0 and γ is the slope of the variation of E with τ. The modulus variation become:
where α=γτo (0 ≤α≤ 1), thermal gradient.
Now, thickness variation of visco – elastic orthotropic parallelogram plate parabolically in ξ and η directions, as:
where β1 and β2 is the taper constant in ξ and η directions and h0=h at ξ=η= 0.
2.2. Equation of frequency and its solution
Rayleigh‐Ritz technique requires that maximum strain energy be equal to the maximum kinetic energy. So it is necessary for the problem consideration that:
for arbitrary variations of W are satisfying relevant geometrical boundary conditions.
For a visco‐elastic orthotropic parallelogram plate clamped (C-C-C-C) along all the four edges, the boundary conditions are:
and the corresponding two‐term deflection function is taken as:
Now assuming the non‐dimensional variable as:
and:
and component of E*1, E*2, E* and G are E*1, E*2secθ, E*secθ and Gsecθ respectively ξ‐ and η‐ direction. Using Eqs. (12), (15), (16) and (17) in Eqs. (7) and (8), then substituting the values of Kmax and Smax from Eqs. (7) and (8) in Eq. (13), one obtains:
where:
+4(G0/E*1)sin2θcos2θ}W2,XY∫10∫b/a02{(E*2/E*1)sin2θ+(E*/E*1)cos2θ}W,XXW,YY
-4{(E*2E*1)sin3θ+2(E*E*1)sinθcos2θ}}W,XXW,XY
-4(E*2E*1)sinθW,YYW,XY]dYdX,
and λ2=(E*1h02/12a2ρcos5θ).
Here limit of X and Y is 0 to 1 and 0 to b/a respectively.
But Eq. (17) involves the unknown A1 and A2 arising due to the substitution of W(ξ,η) from Eq. (14). These two constants are to be determined from Eq. (18), as follows:
Eq. (21) simplifies to the form:
where bn1, bn2 (n= 1, 2) involve parametric constants and the frequency parameter.
For a non‐trivial solution, the determinant of the coefficient of Eq. (22) must be zero. So gets the frequency equation as:
From Eq. (23), one can obtain quadratic equation in λ2 can be found.
3. Result and discussion
The frequency Eq. (23) is a quadratic equation in λ2 from which values of λ2 can be found. The frequency parameter λ corresponding to the first two modes of vibration of a clamped parallelogram plate has been computed for various values aspect ratio (a/b), thermal constant (α), taper constant (β1 and β2) and skew angle. The Poisson’s ratio (ν) is taken as 0.3. These results are summarized in Tables 1-4.
Tables 1 contains the value of frequency parameter of a clamped parallelogram plate for different values of thermal constant (α) for fixed value of aspect ratio (a/b)=1.0 and taper constants β1=β2=0.4 for the first two modes of vibration for two values of skew angle (θ).
Table 1Frequency parameter (λ) of a clamped parallelogram plate for different value of thermal constant (α)
α | a/b=1.0, θ= 0° and β1=β2=0.4 | a/b= 1.0, θ= 60° and β1=β2=0.4 | ||
First mode | Second mode | First mode | Second mode | |
0.0 | 40.58 | 160.98 | 213.89 | 804.12 |
0.2 | 38.68 | 154.26 | 204.62 | 169.99 |
0.4 | 36.92 | 146.86 | 194.92 | 732. 62 |
0.6 | 34.89 | 139.87 | 184.64 | 692.95 |
0.8 | 32.78 | 131.75 | 173.86 | 652.88 |
1.0 | 30.62 | 123.66 | 162 .22 | 611.73 |
Table 2 gives the value of frequency parameter of a clamped parallelogram plate for different values of aspect ratio (a/b) and the combinations of:
– α= 0.0, β1=β2=0.0 and θ= 0°.
– α= 0.0, β1=β2=0.4 and θ= 60°.
It is seen from the tables that as aspect ratio increases frequency parameter increases in all the cases for both modes of vibration.
Table 3 have the value of frequency parameter of a clamped parallelogram plate for different values of taper constant (β1) for fixed value of a/b= 1.0, θ= 0°, α= 0.4 and β2=0.4. It is seen from the tables that as taper constant increases frequency parameter increase in all the cases for both modes of vibration.
Table 4 contains the value of frequency parameter of a clamped parallelogram plate for different values of skew angle (θ) and the combinations of:
– a/b= 1.0, α= 0.0 and β1=β2=0.0.
– a/b= 1.0, α= 0.4 and β1=β2=0.4.
It is seen from the tables that as skew angle increases frequency parameter increases in all the cases for both modes of vibration.
Table 2Frequency parameter (λ) of a clamped parallelogram plate for different value of aspect ratio (a/b)
a/b | α= 0.0, θ= 0° and β1=β2=0.2 | α= 0.0, θ= 60° and β1=β2=0.4 | ||
First mode | Second mode | First mode | Second mode | |
0.5 | 117.14 | 26.52 | 464.66 | 118.71 |
1.0 | 156.52 | 39.22 | 697.77 | 184.88 |
1.5 | 267.82 | 67.08 | 1165.66 | 303.99 |
2.0 | 439.77 | 109.12 | 1861.88 | 478.66 |
2.5 | 666.12 | 163.88 | 2775.92 | 701.12 |
3.0 | 892.33 | 211.04 | 3668.22 | 1021.11 |
Table 3Frequency parameter (λ) of a clamped parallelogram plate for different value of taper constant (β1)
β1 | a/b= 1.0, θ= 0°, α= 0.4 and β2=0.4 | a/b= 1.0, θ= 0°, α= 0.4 and β2= 0.4 | ||
First mode | Second mode | First mode | Second mode | |
0.0 | 31.04 | 124.88 | 34.11 | 139.02 |
0.2 | 32.88 | 135.03 | 37.88 | 150.99 |
0.4 | 36.12 | 146.11 | 41.01 | 164.89 |
0.6 | 40.32 | 158.88 | 44.98 | 179.01 |
0.8 | 42.88 | 172.08 | 48.01 | 194.88 |
1.0 | 46.23 | 176.13 | 52.22 | 210.77 |
Table 4Frequency parameter (λ) of a clamped parallelogram plate for different value of Skew angle (θ)
θ | a/b= 1.0, α= 0.0 and β1=β2=0.0 | a/b= 1.0, α= 0.4 and β1=β2=0.4 | ||
First mode | Second mode | First mode | Second mode | |
0o | 139.01 | 34.01 | 160.99 | 40.01 |
30o | 192.93 | 48.99 | 222.93 | 56.77 |
45o | 301.01 | 78.11 | 346.02 | 90.03 |
60o | 623.98 | 163.88 | 715.88 | 189.99 |
4. Conclusion
The Rayleigh‐Ritz technique has been applied to study the effect of the taper constants on the vibration of clamped visco‐elastic isotropic parallelogram plate with linearly varying thickness in two directions on the basis of classical plate theory.
On comparison with [7], it is concluded that the value of the frequency comes smaller in this paper when we compare both the paper results.
In this way, authors concluded that linear variation in both directions is more useful than parabolic variation in one direction.
References
-
Leissa A. W. Vibration of Plate, NASA SP-160, 1969.
-
Leissa A. W. Recent studies in plate vibration 1981-1985 part II, complicating effects. Shock and Vibration Digest, Vol. 19, 1987, p. 10-24.
-
Gupta A. K., Johri T., Vats R. P. Thermal effect on vibration of non-homogeneous orthotropic rectangular plate having bi-directional parabolically varying thickness. Proceeding of International Conference in World Congress on Engineering and Computer Science, San-Francisco, USA, 2007, p. 784-787.
-
Gupta A. K., Khanna A. Vibration of visco-elastic rectangular plate with linearly thickness variations in both directions. Journal of Sound and Vibration, Vol. 301, 2007, p. 450-457.
-
Singh B., Saxena V. Transverse vibration of rectangular plate with bi-directional thickness variation. Journal of Sound and Vibration, Vol. 198, 1996, p. 51-65.
-
Sobotka Z. Vibration of rectangular orthotropic visco-elastic plate. Acta Techanica CSAV, 1969, p. 511-514.
-
Gupta A. K., Kumar Amit, Gupta Dhram Veer Vibration of visco-elastic orthotropic parallelogram plate with parabolically thickness variation. International Journal of Engineering, Vol. 8, Issue 2, 2012, p. 61-70.
-
Warade R. W., Deshmukh K. C. Thermal deflection of a thin clamped circular plate due to a partially distributive heat supply. Ganita, Vol. 55, 2004, p. 179-186.
-
Sobotka Z. Free vibration of visco-elastic orthotropic rectangular plates. Acta Techanica CSAV, 1978, p. 678-705.
-
Gupta A. K., Kumar L. Thermal effect on vibration of non-homogenous visco-elastic rectangular plate of linear varying thickness. Meccanica, Vol. 43, 2008, p. 47-54.
-
Khanna A., Kaur N., Sharma A. K. Effect of varying poisson ratio on thermally induced vibrations of non-homogeneous rectangular plate. Indian Journal of Science and Technology, Vol. 5, Issue 9, 2012, p. 3263-3267.
-
Sharma S. K., Sharma A. K. Mechanical vibration of orthotropic rectangular plate with 2D linearly varying thickness and thermal effect. International Journal of Research in Advent Technology, Vol. 2, Issue 6, 2014, p. 184-190.
-
Khanna A., Sharma A. K. Vibration analysis of visco-elastic square plate of variable thickness with thermal gradient. International Journal of Engineering and Applied Sciences, Vol. 3, Issue 4, 2011, p. 1-6.
-
Kumar Sharma A., Sharma S. K. Vibration computational of visco-elastic plate with sinusoidal thickness variation and linearly thermal effect in 2D. Journal of Advanced Research in Applied Mechanics and Computational Fluid Dynamics, Vol. 1, Issue 1, 2014, p. 46-54.
-
Khanna A., Kumar A., Bhatia M. A computational prediction on two dimensional thermal effect on vibration of visco-elastic square plate of variable thickness. Proceeding of CONIAPS XIII, Deharadun, 2011.
-
Khanna A., Sharma A. K. Natural vibration of visco-elastic plate of varying thickness with thermal effect. Journal of Applied Science and Engineering, Vol. 16, Issue 2, 2013, p. 135-140.
-
Kumar Sharma A., Sharma S. K. Free vibration analysis of visco-elastic orthotropic rectangular plate with bi-parabolic thermal effect and bi-linear thickness variation. Journal of Advanced Research in Applied Mechanics and Computational Fluid Dynamics, Vol. 1, Issue 1, 2014, p. 10-23.
-
Sharma S. K., Sharma A. K. Effect of bi-parabolic thermal and thickness variation on vibration of visco-elastic orthotropic rectangular plate. Journal of Advanced Research in Manufacturing, Material Science and Metallurgical Engineering, Vol. 1, Issue 2, 2014, p. 26-38.
-
Khanna A., Sharma A. K. Mechanical vibration of visco-elastic plate with thickness variation. Journal of Applied Mathematical Research, Vol. 1, Issue 2, 2012, p. 150-158.
-
Khanna A., Kaur N., Sharma A. K. Effect of varying Poisson ratio on thermally induced vibrations of non-homogeneous rectangular plate. Indian Journal of Science and Technology, Vol. 5, Issue 9, 2012, p. 3263-3267.
-
Khanna A., Sharma A. K. Analysis of free vibrations of visco elastic square plate of variable thickness with temperature effect. International Journal of Applied Engineering Research, Vol. 2, Issue 2, 2011, p. 312-317.