Abstract
The article presents preliminary results of study, which have on aim non–invasive qualification of technical state of rollers in belt conveyor after certain time of exploitation. The measurements of jacket’s vibrations of rollers installed on laboratory stand were conducted. Next, registered vibration signals were processed. The comparison of analyses results for new and wear rollers allow qualifying usability wear rollers to further operation.
1. Introduction
The largest groups of devices designed to continuous transport are belt conveyors. Belt conveyors characterize simple construction; it was assembled first of all from going and reversible barrels, barrels they stretch the belt and belt leading rollers.
Belt conveyors are used to transportation of many different materials. It was estimated, that in Poland total length of belt conveyor’s routes carries out about 2000 km. The largest application (about 80 % length all routs) falls on mining, in which conveyors provides to moving winning. From remaining important branches of industry in which belt conveyors find large application are metallurgy, heat and power generating plants and the power stations.
With attention on scale of applications of belt conveyors, it applies the high importance to reliability their construction how also to reduction of costs of their work. The big influence on both these factors has technical state of the most numerous elements of conveyor that is rollers. In dependence from length of conveyor, the kind of transported material etc., number of rollers can differ significantly, and cost of their exchange can make up the different part in value of whole conveyor [1].
With point of view of operation significant is also, that from number of rollers depend the losses of energy on rolling motion of the belt on jacket of roller, also the friction of belt with the jacket of rollers, as well overcome turn resistances of rollers.
Having on attention above mentioned matters, the aim of presented investigations was verification of the possibility of rollers diagnostics with use vibroacoustics methods.
On presented stage of investigation, researches was led on laboratory stand, what had on aim the preliminary develop of guidelines of technical state rollers evaluation. Various tests, which selected results are presented, are only the basis for the created database symptoms of the technical condition of rollers.
Guidelines of evaluation technical state of rollers can prevent the exchange of rollers whose condition allows further exploitation, as well be a basis for a possible an exchange of worn rollers, which, according to the current evaluation criteria for such an exchange is not yet eligible [2].
Conducted in this manner diagnosis of a conveyor belt can avoid emergency conveyor standstills and is economically justified.
2. Research object
The research object was rollers of belt conveyor type Gwarek 1200, working in mine KWK Mysłowice–Wesoła and transporting winning to output shaft on level 665 m. The belt conveyor is driven with two electric engines with 90 kW power every. The length of conveyor carries out 140 m, average angle of inclination – 9°. The maximum efficiency of conveyor is 1200 t/h [3, 4].
Upper rollers in presented belt conveyor was spaced every 1.5 m, while bottom rollers every 3 m. With attention on number of rollers, assurance of proper their technical state can contribute to lower consumption of necessary energy to drive of belt conveyor.
In contrast to previously used rollers in tested belt conveyor, the studied rollers were modified through use the C4 class of seal in bearings as well as the labyrinth seal U4Exp 62/65 with cover 2LU4 in construction of roller. In construction of roller were applied bearings 6305 ETN9/C4, produced by SKF with poliamid basket strengthened with glass fibre.
The construction of roller is shown on Fig. 1.
Fig. 1The construction of belt roller: 1 – jacket, 2 – bearing, 3 – labyrinth seal, 4 – cast iron hub, 5 – axle [4]
![The construction of belt roller: 1 – jacket, 2 – bearing, 3 – labyrinth seal, 4 – cast iron hub, 5 – axle [4]](https://static-01.extrica.com/articles/15586/15586-img1.jpg)
In studies were used four rollers. Three rollers were disassembled from belt conveyor working in mine and have visible symptoms of wear. Fourth roller was delivered to laboratory in new condition.
3. Research method
The aim of the study was to obtain information on the effects of vibration caused by ball bearings mounted in roller whose condition directly affects its resistance to rotation.
Diagnosing of rolling bearings and evaluation of their condition may be accomplished in many ways. In laboratories is possible a simple method based on evaluation of sounds generated during operation of the bearing. The method is subjective and not always allowing for the proper diagnosis. The testing method use traditional or electronic stethoscopes. The method of listening is an important drawback – the sense of hearing, and the ability of its perception tends to get used to the processes that occur gradually. Regardless of used equipment, the organoleptic methods are effective only when a specialized person performs a diagnosis.
For elimination subjective character, studies were based on more modern methods of bearings’ diagnosis. They use for evaluation diagnostic equipment, which record residual processes resulting from the operation of the machine.
The studies was assumed that will be conducted vibration measurements of jacket roller. During test resigned from the measurements of another residual process – changes in sound pressure, due to the inability to use this method during operation of the conveyor. This result from the impossibility of full isolation the acoustic signal generated by a roller, in particular by its bearings from other noise sources. Conveyor’s work characterizes too high noise, in addition there are much external interferences from other devices nearby.
Vibration measurements of roller’s jacket were carried out with use acceleration transducers PCB. During the study was made simultaneous measurements of linear accelerations of jacket on the hub bearing. The study took place in laboratory environment, with the reverse method of drive the roller. During operation in normal conditions (in belt conveyor), axle of roller remains stationary while the jacket rotates. During the measurements jacket was attached in a manner preventing its rotation, while the drive is adjusted to the axle direct from motor rotating at a speed ~650 rpm.
Vibration acceleration sensors (standard ICP) allow registration of vibrations with frequencies up to 10 kHz. The signals are sampled at a frequency of 31.25 kHz, which allowed in accordance with the Nyquist criterion for the registration of whole range of vibration acceleration measured by sensors.
The signals were recorded using 8-channel data acquisition card. As a result of signal processing, taking into account radial cylindricity deviation of jacket, was made filtration of recorded vibration signals. In result was received the time courses of vibrations caused by the work of the bearings.
4. Results of preliminary research
Changes in the vibration signal caused by operational wear of bearings mounted in roller were determined by a number of simple amplitude measurements derived from time courses. As well, the analysis in time–frequency domain was carried too.
The basic information on the changes in the vibration signal caused by operational wear delivers RMS value of vibration accelerations. In Fig. 2 are presented the changes of the RMS value of vibration accelerations of jacket rollers after 9 months of operation (aRMS(wearroller)) related to the values obtained for the new roller (aRMS(newroller)). In Fig. 3 are presented changes of variance values of jacket vibration acceleration related to the values obtained for the new roller.
Fig. 2The changes of RMS values of vibration acceleration of jacket all examined rollers in relation to the new roller
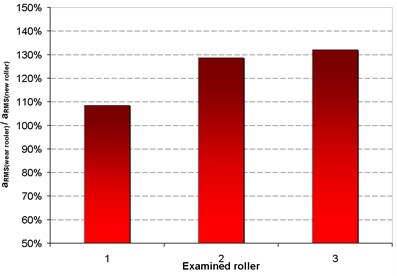
Fig. 3The changes of variance values of vibration acceleration of jacket all examined rollers in relation to the new roller
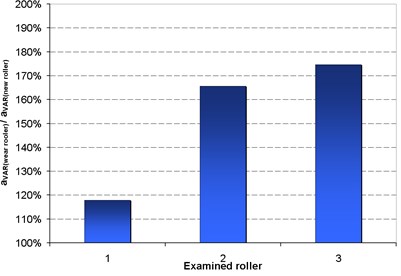
The largest increase of RMS value of jacket vibration acceleration of wear rollers in relation to the new roller (about 32 %) was observed for the third examined roller. The smallest difference (about 8 %) occurred for the first roller. Approximately 24 % difference of values obtained for the rollers with the same operation time due, inter alia, from different place of roller installation on the conveyor.
Analogous to the changes in the RMS values of vibrations, occurred changes the values of variance. The results in Fig. 3 show, that the increase of values ratio is in the range from about 18 % to 75 %.
Analysis conducted in the time–frequency domain enabled to determine changes in the frequencies components of the signal. Comparison of the spectra obtained for new and wear roller (first examined) is shown in Fig. 4.
Wear after 9 months of operation for each roller caused the appearance in the spectrum of high-amplitude components in the range 6-8 kHz. This is most evident in the case of a third of the examined belt roller. For the first roller in the spectrum are also clearly visible frequency components in the range 2-3 kHz.
Fig. 4Spectrum of vibration acceleration signals obtained for the new and wear roller
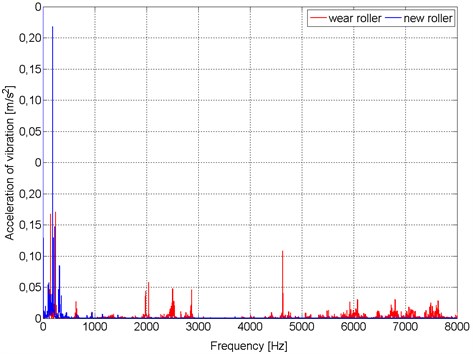
5. Conclusions
The study shows that the operational wear of rollers affect on the level and structure of the generated vibrations. It is mapped in simple amplitude measures, but a more complete picture of changes in the vibration signal provides time–frequency analysis. From the diagnostic point of view, the most useful frequency band is 6-8 kHz, wherein in each examined case the differences were seen. Further studies are aimed at building measures, which are sensitive on wear of rollers' bearings, based on the results of the vibration signal analysis.
Additional laboratory tests carried out on rollers, which characterize new, presented in article construction, has shown that, despite the significant differences seen in the vibration signal caused by the occurrence of wear, they still have a low static and dynamic resistance to rotation. Small values of resistance were also confirmed by measurements of the energy consumption of the conveyor drive carried out at each stage of the research.
References
-
Gładysiewicz L., Król R. Investigation of the effect of operating conditions on the resistance of rotating rollers. Industrial Transport, 2003, (in Polish).
-
PN-M-46606:2010: Belt conveyor – Rollers.
-
Opasiak T., Gąska D., Łazarz B. Analysis of the resistance movement of the conveyor belt and rollers in coal mine KWK Mysłowice–Wesoła. International Conference PKM, Szczyrk, 2013, (in Polish).
-
Opasiak T., Peruń G. Testing laboratory the reinforced construction rollers bearing hubs. International Conference Transport Problems, Katowice, 2014.