Abstract
The paper describes a diagnostic experiment connected with measurement of torsional vibrations of a combustion engine’s crankshaft. The aim of the experiment was to find out which of a few types of rubber torsional vibration dampers most effectively ‘damps’ the vibrations most dangerous for this engine. Exemplary results of the analysis of recorded data are shown. Obtained results prove, that in many cases there is still place to do some more effort for finding better tuned TVD than the ‘original’ one.
1. Introduction
A working combustion engine is a source of vibrations which are the result of periodically changeable forces of pressure of gases and inertia forces. These forces generate bending, axial and torsional vibrations [1]. Crankshafts are usually relatively stiff in axial and radial directions, whereas their torsional stiffness is significantly lower [2-4]. That is why, torsional vibrations is an essential problem, especially in six- and more cylinder engines (where crankshafts can be very flexible due to their long length), and/or in the engines working at high rotational speeds. In these types of engines there is a danger, that in the range of operating rotational speed, the input frequency can get close to the torsional natural frequency of shaft. Then, the resonance will occur. As a result of this phenomenon, the amplitudes of torsional vibrations of crankshaft may exceed acceptable values.
Torsional vibrations of crankshaft are more difficult to detect than bending or axial vibrations. When they are overlapped at the rotation of shaft, they usually do not lead to higher vibrations of the neighbouring elements. They are not a source of the noise also, and that is why, they may be unnoticed until the fatigue failure of shaft and high bearing wear occur as well as other unwanted side effects of things driven by shaft.
The work of engine in the range of resonance rotational speeds can be avoided by:
– The change of operating rotational speeds,
– The change of torsional stiffness of crankshaft (change of natural frequencies),
– The change of exciting forces,
– Using torsional vibration dampers (TVD).
The first three options are very difficult (in most cases impossible) to achieve because of constructional-operating reasons. Nowadays, different types of torsional vibration dampers (TVD) are used. They are located in the front end of the crankshaft (nose). Nowadays, rubber vibration dampers are most often used in automobile engines. In fact, they are dynamic eliminators of vibrations, where additionally the phenomenon of dissipation of energy as a result of internal friction in rubber element is used. That is why, they are designed to match the most dangerous resonance frequency (of the highest amplitude) – typically the first torsional natural frequency of crankshaft (or, in some cases, the frequency between two main crankshaft’s torsional natural frequencies). These dampers are often integrated into front pulley [1, 5].
2. Research experiment
The paper describes a diagnostic experiment connected with measurement of torsional vibrations of a crankshaft of six-cylinder V-type engine 3,6 V6 FSI assembled in Volkswagen Passat, Touran, Audi Q7 and Porsche Cayenne.
The aim of the experiment was to study a few types of rubber torsional vibration dampers in order to find out which of them most effectively damps the vibrations of the frequency most dangerous for this engine.
The measurements were carried out on the engine fixed in a car on the vehicle test stand (Fig. 1).
The place of fixing the sensor is shown in Fig. 2.
Fig. 1Research object on vehicle test stand
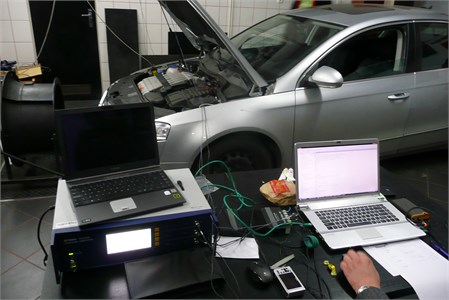
Fig. 2The place of fixing the sensor of torsional vibrations
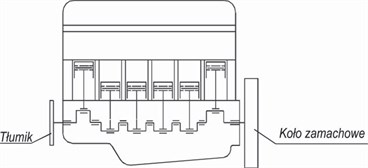
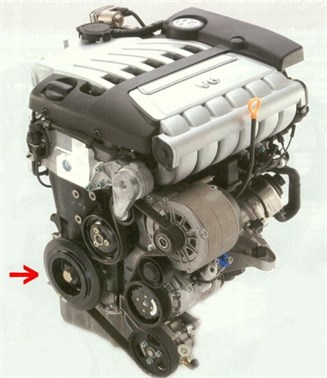
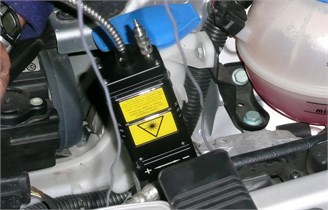
The measurement of vibrations was recorded in the range of rotational speed of the engine from 750 RPM to 5000 RPM (operating rotational speeds for the examined engine) [6].
A Polytec RLV-5500 dual beam laser sensor was used to measure the torsional vibrations (Fig. 3). This vibrometer allows for the measurement of torsional vibrations in the range of rotation speed to 20 000 RPM in frequency band up to 10 kHz. Because of its compact design the head of vibrometer allows for measurements of vibrations of the examined objects from a very small distance. An integrated system of clearing the air guards the optical elements against the pollution, dust or oil mist.
Fig. 3Laser system for measuring the torsional vibrations Polytec RLV-5500
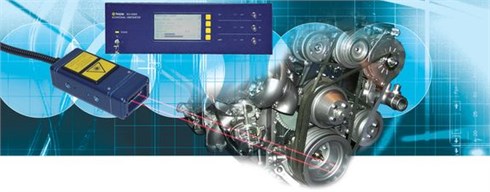
a)
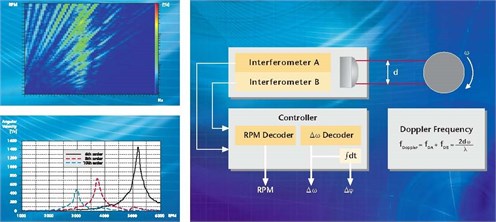
b)
Fig. 4The change in amplitude of torsional vibrations speed of the shaft is the function of rotational speed of the engine for different types of torsional dampers
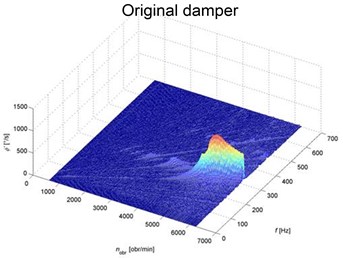
a)

b)
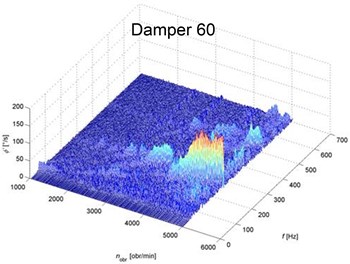
c)
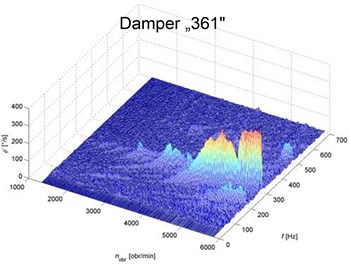
d)
An optical fiber cable was used in order to power the laser, which as a result increases assembly possibilities and options of settings (positioning) without the loss of precision.
Torsional vibrations of crankshaft were recorded when the various types of torsional dampers were fixed on the crankshaft’s nose. As it was mentioned in the introduction, rubber dampers are used in such engines, and that is why the authors decided to examine the changes of vibration response of crankshaft in function of hardness of the elastic element. The following types of dampers were examined:
– Original damper – damper originally fixed by the engine manufacturer;
– Damper ‘361’ – substitute product produced by the outsource manufacturer;
And dumpers prepared especially for the experiment [7]:
– Damper “50” – damper with rubber ring of hardness 50 Sh;
– Damper “60” – damper with rubber ring of hardness 60 Sh;
– Damper “65” – damper with rubber ring of hardness 65 Sh;
– Damper “70” – damper with rubber ring of hardness 70 Sh;
– Damper “75” – damper with rubber ring of hardness 75 Sh.
These dampers had identically designed housing (hub) and inertial ring, they differed only with elastic element made of rubber of various hardness. The aim was to carry out the analysis of the influence of the change of this parameter on the vibration response of the engine crankshaft. Fig. 4 shows the exemplary results of the analysis of the amplitude changes of torsional vibrations speed of the shaft in the function of rotational speed of the engine for chosen types of torsional dampers.
3. Conclusion
Torsional vibration damper is chosen or designed individually for a certain type of engine (drive system) on the basis of the results of harmonic analysis of torsional vibrations of crankshaft. The analysis allows for obtaining the resonance amplitude of the shaft, and it allows mainly for obtaining the torsional natural frequencies, which are the starting point in the design of the optimal torsional damper. Optimal torsional damper is the one which minimizes the level of maximum shear fatigue stress in the whole range of operating rotational speeds of the engine. It can be achieved i.a. by appropriately chosen geometric parameters of a damper: mass moments of inertia of the damper elements – especially inertial ring and/or the choice of optimum physical properties of rubber, which is the material that the flexible element connecting hub and inertial ring is made of. Operating research of dampers is not only the most reliable but also the most expensive. Significant lowering the costs of research which lead to finding the best solution can be achieved by the choice of the damper on the basis of the simulation research carried out on less or more simplified dynamic models [8]. Lots of manufacturers are following this trend. As the analysis of the experiment results showed, following this road allows for choosing the torsional damper which reduces the maximum torsional angles of crankshaft below the ones which are allowed by the manufacturer ±1,5°. The experiment showed that during the operating research, it is possible to find the solution even more effective in damping torsional vibrations by modifying only one parameter of a damper – hardness of rubber.
References
-
Homik W. Broadband Torsional Dampers. The Institute for Sustainable Technologies – National Research Institute, Rzeszów 2012, (in Polish).
-
Burdzik R., Folęga P., Łazarz B., Stanik Z., Warczek J. Analysis of the impact of surface layer parameters on wear intensity of friction pairs. Archives of Metallurgy and Materials, Vol. 57, Issue 4, 2012, p. 987-993.
-
Folęga P., Siwiec G. Numerical analysis of selected materials for flexsplines. Archives of Metallurgy and Materials, Vol. 57, Issue 1, 2012, p. 185-191.
-
Folęga P. Analysis of stress state of toothed ring of flexspline by means the BEM. Archives of Materials Science and Engineering, Vol. 59, Issue 1, 2013, p. 40-45.
-
Pankiewicz J., Homik W. Examinations of torsional vibration dampers used in reciprocating internal combustion engines. Polish Journal of Environmental Studies, Vol. 20, Issue 5A, 2011, p. 108-111.
-
Pankiewicz J., Górnicka D. Torsional vibrations of VW 3,6 V6 FSI engine crankshaft. XXXVIII Symposium on Machines Diagnostics, Wisła, 2011, (in Polish).
-
Pankiewicz J., Dziurdź J. Examinations of various torsional vibrations dampers. XXXVII Symposium on Machines Diagnostics, Wisła, 2010, (in Polish).
-
Pankiewicz J., Deuszkiewicz P., Dziurdź J., Zawisza M. Modeling of powertrain system dynamic behavior with torsional vibration damper. Proceedings of Modern Technologies in Industrial Engineering, 2014.