Abstract
An interest to novel methods of non-destructive testing (NDT) used for composite structures has been growing during the last decade due to the industrial necessities and development of measurement devices. The promising approach applied for NDT of composite structures is the vibration-based analysis with further processing of measurement data using advanced signal processing techniques, in particular wavelet transforms. In this paper, the 2D undecimated fractional wavelet transform was introduced, which allows for overcoming the problem of initial dataset reduction during performing a wavelet transform. The proposed approach was tested on various composite structures with different types of damages including cracks, delaminations, impact damages in laminates and the core damages and interface damages in sandwich composite structures. Obtained results confirm the effectiveness of the proposed approach and prove the universality of the modal-based NDT with wavelet analysis.
1. Introduction
Due to increasing applicability of composites as structural elements in various fields of industry (machine design, aircraft, naval and civil engineering, etc.) the development of adequate non-destructive testing (NDT) and structural health monitoring (SHM) methods become critically important for ensuring structural integrity and safety of composite elements being in operation. It should be mentioned that developed methods should be sensitive to the typical damages in materials (such as cracks), but also to the damages specific to the internal structure of composites being under consideration (delaminations and interlaminar cracks, interface damages or combinations of previously mentioned damages) and not occurring in homogeneous materials. The problem becomes important when considering the specific scenarios of damaging of composites, e.g. in the case of impact damaging the large-area delaminations may occur inside the structure, but the damages on the surface of a structure may be invisible. Following this, the rapid increase in development of novel NDT and SHM methods has been observed over the last two decades.
The NDT methods applied for composites can be classified according to the measurement techniques used for the damage detection, localization and identification. One of the most popular methods applied for NDT of composite structures is an infrared-based technique. The main advantages of this technique are the quickness of performing the inspection and comparatively good accuracy of detection and localization of damages. In the case of active thermography the damages can be easily and quickly detected and localized [1-3], however the technique requires expensive equipment and is proper to be applied only for relatively thin structures [4]. Other widely applied NDT technique for composites is the group of methods based on ultrasonic measurements. The most popular types of such measurements are polar and C-scans [5, 6] as well as Lamb wave-based approaches [7-9]. Although the ultrasonic tests are also characterized by great sensitivity to the various types of damages, they require specific equipment and it is often necessary to immerse a tested element in the coupling medium. Several exceptions, when the air-coupled testing was applied, were described in [10, 11]. The Lamb wave-based techniques also require special and expensive measurement systems for performing the tests. Other methods, which were effectively applied in structural diagnostics problems of composites are the optical-based methods. One can mention the deflectometry [12] and the digital image correlation [13], which were successfully used for damage detection. Finally, the most accurate method to-date for structural diagnostics of composites is the computed tomography (CT). Actual resolution of tomographs applied nowadays in structural testing varies from micrometers to tenth of nanometers, which makes possible an evaluation of almost all damages in macro-, meso- and microscale. Several studies on detection and localization of various types of damages in composite structures were described in [14-17]. However, in spite of superior accuracy of CT-based methods there are some difficulties with interpretation of results and the cost of testing equipment is very high.
From the great variety of NDT and SHM methods applied for composite structures the vibration-based approach with further post-processing of measurement data is one of the less expensive methods, which gives comparatively accurate results of damage detection and localization. The methods, which use modal analysis are quite effective in damage detection problems. The authors of [18, 19] describe the method based on modal analysis and nonlinear acoustics for damage detection in composite structures. They analysed the power spectra obtained from modal testing in order to identify the characteristic frequencies responsible for particular types of damages. This approach is quite sensitive to the structural damages, however it can be used only for detection of damages. Similarly, the approaches based on energy damage indices [20] or other statistical factors [21-23] allow only for detection without a possibility of localization of the damage. The damage detection and localization using vibration-based methods is possible when the modal shapes are considered for the analysis as input data. The modal shapes reveal much better sensitivity to the damages and, with appropriate post-processing signal analysis, can be good sources of diagnostic information about condition of a tested structure. The approach of the analysis of modal shapes was intensively developed using various measurement techniques and post-processing signal analysis methods and gives comparatively accurate results in damage detection and localization. The authors of [24] used various formulations of damage indices and successfully detected and localized the damages in beam-type structures. The authors of [25] analysed the modal shapes of vibration using fractal dimension-based algorithm, which also allows for detection and localization of damages. However, one of the most sensitive post-processing methods is the wavelet analysis. The activity in application of wavelet-based methods in structural diagnostics problems has been increasing rapidly over the last years. The wavelet-based approaches can be classified into several categories regarding the transforms used during analyses. The first studies using wavelet-based algorithms were performed using continuous wavelet transform (CWT) for the damage detection and localization in beam-type and plate-type structures [26-30]. Application of CWT has some advantages and disadvantages: on the one hand almost arbitrary functions can be used as basic ones during the analysis, but on the other hand CWT is redundant and it is necessary to select the range of values of the scale parameter. Contrary to CWT, discrete wavelet transform (DWT) is not redundant, but has some limitations regarding the wavelets which can be applied to the analysis. However, it was proven in [31] that application of B-spline wavelets guarantees the comparable accuracy and sensitivity to the damages in comparison with Gabor wavelets applied in [30] and they were recognized as the best wavelets in CWT-based algorithms. The DWT-based algorithms for structural diagnostics of composites were mainly developed by the author of these papers [11, 31-33]. An alternative approach based on the stationary wavelet transform (SWT) was developed mainly by Zhong and Oyadiji [34-36]. Although SWT is redundant with respect to DWT, SWT does not downsample an input signal during decomposition, what results in the fact that the output signal is of the same size as the input one (as opposed to DWT, where the downsampling procedure causes reduction of size of a signal twice on each level of decomposition). This property seems to be useful in application of structural diagnostics, i.e. lack of reduction of signal size allows for improvement of damage detection and localization capabilities as well as better visualization and interpretation of results. However, SWT restricts the signal size, i.e. the number of elements in the analysed signal should be equalled the power of 2. In order to avoid this restriction the more general transform can be applied, namely the undecimated wavelet transform (UWT).
Several attempts were made in order to improve basic transforms and wavelets applied for post-processing of NDT. Recently, the great attention has been paid to hybrid algorithms, where, besides the wavelet-based algorithm, other techniques of optimization and artificial intelligence have been used. The authors of [37, 38] used artificial neural networks in combination with the wavelet-based algorithm in order to improve abilities of detection and localization of damages in structures. Xiang and Liang [39] presented a combination of wavelet-based algorithm with optimization procedure. The approach developed by the author’s team is based on fractional wavelet transform (FrWT) with fractional B-spline wavelets (what gives a possibility of selection of appropriate wavelet order from the real numbers) and optimization algorithms, which make possible an additional improvement of the detectability of damages in structures. The application of these algorithms to the structural diagnostics of composites for beam-like and plate-like structures was described in [40] and [41], respectively.
The main goal of such improvements is to enhance the detection, localization and identification capabilities of the developed algorithms. During application of FrWT the initial dataset is reduced twice at each level of decomposition, therefore, in order to avoid such reduction the decimation procedure should be omitted. In the research described in this paper, the undecimated fractional wavelet transform (UFrWT) was introduced. Application of this transform allows for using fractional B-spline wavelets and simultaneously omitting of the decimation procedure, so that the size of the analysed dataset is the same before and after application of the transform. In order to highlight the universality of the proposed approach several examples were presented for various composite structures with different types of damages.
2. Theoretical background and identification procedure
2.1. Two-dimensional undecimated fractional wavelet transform (2D UFrWT)
The FrWT is based on the Mallat’s multiresolution algorithm with use of complex B-spline scaling functions and wavelets of fractional order introduced by Unser and Blu in [42]. Considering that the mentioned functions are fractional and complex they are driven by two parameters: fractional order α and shift parameter τ, which can be real numbers. The general form of α, τ-B-spline scaling functions presented in [42] is as follows:
where:
and Γ(α+1) is the Euler’s gamma function, which is defined as:
The B-spline scaling functions of fractional order are not symmetric and have not compact support (except the cases, when α∉Z – in this case the integer B-spline scaling functions can be obtained by holding an additional relation: τ=(α+1)/2 [42]). However, they hold a two-scale relation [43]:
where hατ[k] is a refinement filter.
The B-spline wavelets ψατ of fractional order also hold a two-scale relation [42]:
Similarly to scaling functions, B-spline wavelet functions of fractional order have no compact support, when α∉Z. In order to avoid this problem Unser and Blu proposed the algorithm, in which the Fourier series are used [42]. Further developments [43] allow for obtaining the direction-oriented complex fractional B-spline wavelets, which were constructed basing on Hilbert transform pairs of them. The complexification is based on combination of wavelets with the same value of α, but different values of τ, i.e.:
Basing on the separability property of the above-described wavelets Chaudhury and Unser proposed [43] their 2D analogs obtained from the permutation of tensor products of scaling and wavelet functions. The processing step using FrWT algorithm consists of prefiltering of the input signal using projection procedure and then performing of the 2D DWT algorithm. Considering that the complexified wavelets have the following analytic form:
where H denotes the Hilbert transform, it is possible to obtain 12 separable complex wavelets and, basing on them, 6 direction-oriented 2D complex wavelets [43]:
ψ3(x,y)=β(x)ψα(y),ψ4(x,y)=Hβ(x)ψα(y),
ψ5(x,y)=2-1/2ψα(x)ψα(y),ψ6(x,y)=2-1/2ψ*α(x)ψα(y),
where 2-1/2 is a scaling factor applied for wavelets and ψ*α has the different sign during construction of 2D wavelets (see [43] for details).
2.2. Identification procedure
The processing procedure is based on the modal shapes of vibration si of a tested structure. The modal shapes are considered as input to the processing algorithm. There are more than one modal shape M considered during the analysis for a given structure since the magnitudes of obtained coefficients after the decomposition are dependent on the magnitudes of displacements or velocities of vibration of modal shapes and in the case of damage location in the low-magnitude region of a given modal shape the damage can be undetectable.
The application of 2D FrWT proposed in [43] resulted in lowering the dimensions of 2D original signal (N×N) to N/2×N/2, what is caused by the downsampling procedure. In order to avoid this problem the downsampling (or decimation) procedure should be omitted in the processing algorithm. This causes that UFrWT-based algorithm is redundant with respect to FrWT one, but allows for avoiding the problem with resolution.
The processing procedure is as follows. Firstly, the DWT was performed, which can be considered as a filtering procedure using the sets of low-pass ˜h and high-pass ˜g filters applied along x and y directions. Then, the permutation of obtained subbands c is performed, after which the sets of complex coefficients can be presented in the form:
where ΛR and ΛI are the block matrices, using which allow for perfoming the orthonormal transforms [43]:
and ζm,n and ξm,n are the permuted sets of coefficients cp (p is connected with appropriate pairs of filters in x and y directions, namely ˜h˜h, ˜h˜g, ˜g˜h and ˜g˜g) obtained from DWT:
ξm,n=(c˜g˜hm,n(3),c˜g˜hm,n(4),c˜h˜gm,n(2),c˜h˜gm,n(4),c˜g˜gm,n(2),c˜g˜gm,n(3)).
After obtaining of 6 sets of complex coefficients wm,n the real values of them were extracted and added up for the better visual representation purposes, what gave a single set of coefficients Wi. Such an operation is known as an isotropic undecimated wavelet transform [44] (in the above-investigated case the isotropic undecimated fractional wavelet transform – IUFrWT). Finally, addition of all sets Wi for all considered modal shapes resulted in obtaining a single set of coefficients W. The difference between the algorithm applied in [41, 45] and the proposed one is that here the downsampling (or decimation) procedure is omitted.
3. Specimens and testing procedures
In order to validate the universality of proposed method various composite structures with various types of damages specific to these composites were considered during testing and the analysis. Three groups of specimens were analyzed in this paper.
The first group consisted of glass-epoxy laminate plates with artificial damages introduced by the milling machine in the form of through-the-width crack, spatial square damage and a case with multiple damages in the form of two spatial square damages with various dimensions and one short crack. All of the damages have the depth of 20 % (0.5 mm) with respect to the thickness (2.5 mm) of plates. The detailed description of the investigated cases with specific dimensions and locations of the damages was presented in [31, 41].
The second group consisted of plates of the same material as in the first group, but damaged using impact drop-weight machine with various values of impact energy and various impactors. All of the damages were introduced in the geometrical centres of the considered plates. During the impact damaging different damages were observed, i.e. typical cracks in the area of contact of a specimen with impactor as well as additional delaminations around the mentioned area. Several representative cases were selected for the analysis. The detailed description of these specimens and damaging procedure and images of the damaged structures can be found in [11].
The last group consisted of sandwich plates made of aramid paper saturated by phenolic resin (which constitutes a core of a sandwich) and glass-epoxy laminate (used for face sheets). A total thickness of the specimens is 4.1 mm. Various artificial damages were introduced in these structures. The damages of a core were introduced during the manufacturing process. In this study three cases of such damages were considered: full local lack of a core of irregular shape, partial local lack of a core of irregular shape and a delamination between a core and a face sheet of a square shape with dimensions of 60×60 mm in the geometric centres of plates. In the second subgroup the impact damages were introduced after the manufacturing process using the same damaging procedure as for the cases from the second group. One of the cases with an impact damage was selected for this study. The details on the materials used for manufacturing of the specimens and introduced damages for these cases were described in [45].
All of the tested specimens have the same spatial dimensions of 300×300 mm. In order to acquire modal shapes the laser Doppler vibrometers (LDVs) were used. The scanning was performed using Polytec® PSV-400 scanning LDV connected with a vibrometer controller OFV-5000 with built-in velocity and displacements decoder. The plates were clamped around their borders using a frame connected by 24 bolts. On the available area of a plate the net of scanning points was defined in the vibrometer-dedicated software PSV v.8.7 with dimensions of 64×64 equidistant points, which resulted in 4096 measurement points. The excitation of a plate was performed by the electrodynamic shaker TIRA® TV-51120 connected with the power amplifier TIRA® BAA-500. A pseudo-random noise signal was used as excitation of a tested plate. For the acquisition of a reference signal the Polytec® PDV-100 point LDV was used, which laser beam was focused on the steel frame. In order to ensure better focusing of a laser beam the plate and a frame was covered by Helling® anti-glare spray dedicated for laser scanning. The exemplary experimental setup is shown in Fig. 1. For each point defined on the measurement net the frequency response function (FRF) was obtained. Five averaging cycles were defined for each measurement point. From the resulted FRFs for the whole net of measurement points the modes were selected for further analysis according to the rule that the magnitude of velocity for a given peak should be at least 20 % of the maximal peak in the analysed FRF.
Fig. 1Experimental setup during the modal analysis
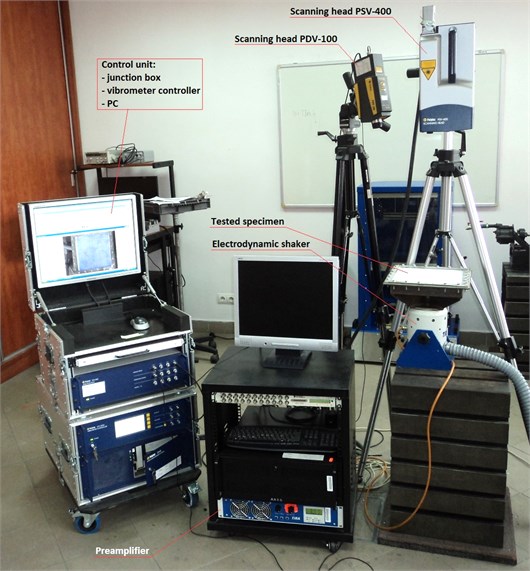
4. Results and comparative studies
4.1. Identification of crack and spatial damages in laminated composites
The acquired modal shapes for all specimens were prepared for the analysis in the Matlab® environment. Using the procedures described above the IUFrWT-based algorithm was applied. The parameters of the fractional B-spline wavelet were selected by trial-and-error method and assumed as follows: order α= 0.8, τ=(α+1)/2 for FrWT- and IUFrWT-based algorithms, for DWT-based algorithm the quadratic B-spline wavelet was selected. The results of damage identification using DWT-based algorithm presented in [31], FrWT-based algorithm presented in [41] and IUFrWT-based algorithm applied for experimental data are presented in Fig. 2.
Fig. 2Results of identification of crack and spatial damages in laminated composites using the algorithms based on a)-c) DWT, d)-f) FrWT, g)-i) IUFrWT based on experimental data
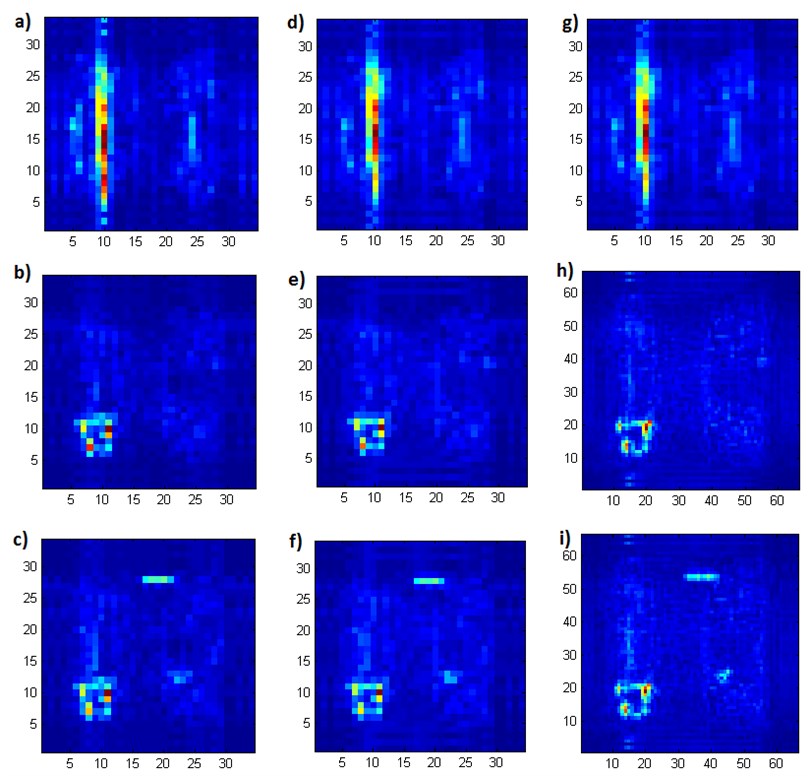
It can be noticed that the damages were properly detected by all of considered algorithms, however the better resolution of IUFrWT-based algorithm provides better localization performance and better identification of damages. The better localization is observed for the large spatial damage in the second and the third case in experimental data (Fig. 2(h) and Fig. 2(i)) and the small spatial damage is localized with higher precision (Fig. 2(i)) than in the cases with use of DWT- (Fig. 2(c)) and FrWT-based (Fig. 2(f)) algorithms. The results for through-the-width crack are comparable for all considered algorithms.
4.2. Identification of impact damages in laminated composites
Similarly as for the previous group of damages the comparative study with use of the same algorithms and the same parameters was performed. The results of the study consist of two selected cases of impact damages in the laminate plates: done by the impactor with edge-ended immersed stone and impact energy of 40 J and by the impactor with vertex-ended immersed stone and impact energy of 35 J. The comparison of the results obtained using the mentioned algorithms is presented in Fig. 3.
Fig. 3Results of identification of impact damages in laminated composites using the algorithms based on a)-b) DWT, c)-d) FrWT, e)-f) IUFrWT based on experimental data
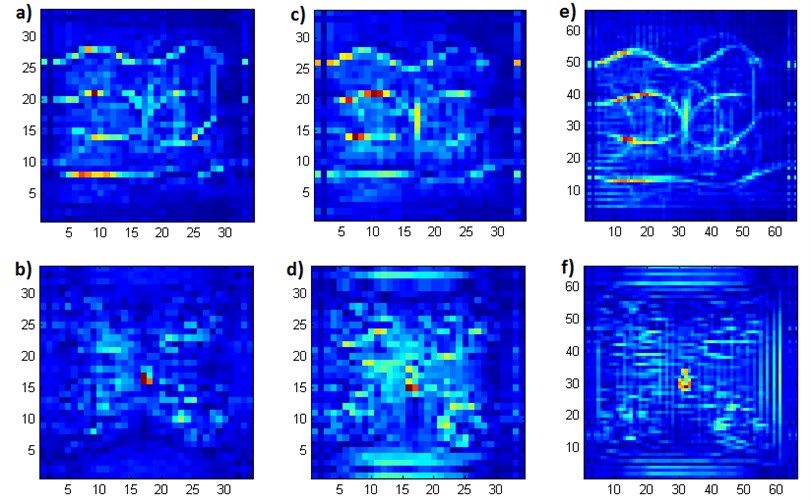
One can observe that in these cases significant influence of measurement and filtering noise is visible. The noise is resulted mainly from the higher-order modes, which contain many extrema. This causes that wavelet transforms, among the damaged region, detected also sudden changes in modal shapes, which were so significant that they were not able to filter them out by filtering procedures. In the first case presented in Fig. 3(a)-(c) this influence is very well visible. However, IUFrWT-based algorithm produced better results than other considered algorithms and the impact-caused crack (vertical line in the centre) is well identifiable in Fig. 3(c). For the second considered case the DWT-based algorithm gives better results than FrWT-based one (cf. Fig. 3(b) and Fig. 3(d)), in the latter case the results are noisy. The proposed algorithm (see Fig. 3(f)) gives the best results, both in resolution and identification ability, which proves its effectiveness for detection and localization of impact damages, which are hardly recognizable in general (using vibration-based testing).
4.3. Identification of damages in sandwich composites
Four cases were considered: partial and full local lack of a core, delamination between a core and a face sheet and the impact damage achieved using rounded-end impactor with an impact energy of 25 J. The resulted comparison for considered algorithms is presented in Fig. 4.
Fig. 4Results of identification of core and impact damages in sandwich composites using the algorithms based on a)-d) DWT, e)-h) FrWT, i)-l) IUFrWT based on experimental data
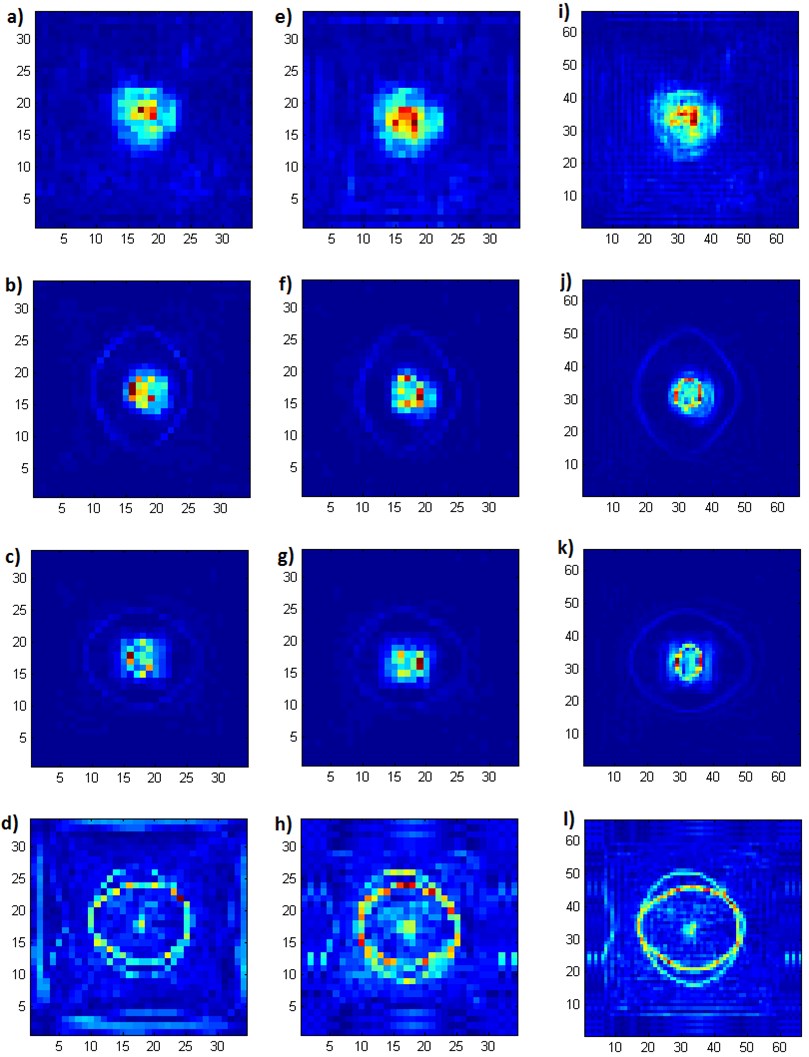
One can notice that in the case of damages of a core by all algorithms these damages were properly detected and localized due to their significant influence on the local stiffness loss of a structure. However, in the case of IUFrWT-based algorithm, due to the increased resolution, the shapes of damages are more adequate to the real damages (compare with photographs of the damages in [45]). In the case of impact damage the degree of stiffness loss was much smaller than in the previous cases, thus the additional artefacts (rings) are visible along with the impact damage in the centre. An improvement of damage identification is well visible during comparison of the obtained results (see Fig. 4(d), Fig. 4(h) and Fig. 4(l)).
5. Conclusions
The presented novel wavelet transform allows enhancing the performance of detectability, localization ability and identification of damages with respect to other considered wavelet transforms. The application of IUFrWT is critically important when the low number of measurement points is considered during the analysis, because the processing algorithm does not reduce the dimensions of sets of resulted coefficients with respect to the original signals. This is due to the substitution of classical DWT decomposition procedure inside FrWT algorithm by undecimaded DWT. In order to prove the universality of this method in application for various types of composite structures with characteristic damages for them several studies were performed basing on the experimental results obtained from artificially damaged composite specimens. Obtained results show that, besides the improvement of resolution, the IUFrWT-based algorithm in numerous cases allowed for recognition of the shapes of damages better than the other considered algorithms.
The proposed approach could improve the inspection procedures of composite structures being maintained in industrial applications. The application of IUFrWT could be expanded on other engineering disciplines, e.g. advanced signal processing, image processing, pattern recognition problems and many others.
References
-
Maldague X. P. V. Introduction to NDT by active infrared thermography. Materials Evaluation, Vol. 60, 2002, p. 1060-1073.
-
Lahiri B. B., Bagavathiappan S., Reshmi P. R., Philip J., Jayakumar T., Raj B. Quantification of defects in composites and rubber materials using active thermography. Infrared Physics and Technology, Vol. 55, 2012, p. 191-199.
-
Usamentiaga R., Venegas P., Guerediaga J., Vega L., López I. Automatic detection of impact damage in carbon fiber composites using active thermography. Infrared Physics and Technology, Vol. 58, 2013, p. 36-46.
-
Montanini R., Freni F. Non-destructive evaluation of thick glass fiber-reinforced composites by means of optically excited lock-in thermography. Composites: Part A, Vol. 43, 2012, p. 2075-2082.
-
Vandreumel W. H. M., Speijer J. L. Non-destructive composite laminate characterization by means of ultrasonic polar-scan. Materials Evaluation, Vol. 39, 1981, p. 922-925.
-
Kersemans M., De Baere I., Degrieck J., Van Den Abeele K., Pyl L., Zastavnik F., Sol H., Van Paepegen W. Nondestructive damage assessment in fiber reinforced composites with the pulsed ultrasonic polar scan. Polymer Testing, Vol. 34, 2014, p. 85-96.
-
Ramadas C., Padiyar J., Balasubramaniam K., Joshi M., Krishnamurthy C. V. Lamb wave based ultrasonic imaging of interface delamination in composite T-joint. NDT&E International, Vol. 44, 2011, p. 523-530.
-
Ben B. S., Ben B. A., Vikram K. A., Yang S. H. Damage identification in composite materials using ultrasonic based Lamb wave method. Measurement, Vol. 46, 2013, p. 904-912.
-
Dao P. B., Staszewski W. J. Lamb wave based structural damage detection using cointegration and fractal signal processing. Mechanical Systems and Signal Processing, Vol. 49, 2014, p. 285-301.
-
Imielińska K., Castaings M., Wojtyra M., Haras J., Le Clezio E., Hosten B. Air-coupled ultrasonic C-scan technique in impact response testing of carbon fibre and hybrid: glass, carbon and Kevlar/epoxy composites. Journal of Materials Processing Technology, Vol. 157-158, 2004, p. 513-522.
-
Katunin A. Stone impact damage identification in composite plates using modal data and quincunx wavelet analysis. Archives of Civil and Mechanical Engineering, (In press).
-
Devivier C., Pierron F., Wisnom M. R. Impact damage detection in composite plates using deflectometry and the Virtual Fields Method. Composites: Part A, Vol. 48, 2013, p. 201-218.
-
Feissel P., Schneider J., Aboura Z., Villon P. Use of diffuse approximation on DIC for early damage detection in 3D carbon/epoxy composites. Composites Science and Technology, Vol. 88, 2013, p. 16-25.
-
Scott A. E., Mavrogordato M., Wright P., Sinclair I., Spearing S. M. In situ fibre fracture measurement in carbon-epoxy laminates using high resolution computed tomography. Composites Science and Technology, Vol. 71, 2011, p. 1471-1477.
-
Hufenbach W., Böhm R., Gude M., Berthel M., Hornig A., Ručevskis S., Andrich M. A test device for damage characterisation of composites based on in situ computed tomography. Composites Science and Technology, Vol. 72, 2012, p. 1361-1367.
-
Bull D. J., Spearing S. M., Sinclair I., Helfen L. Three-dimensional assessment of low velocity impact damage in particle toughened composite laminates using micro-focus X-ray computed tomography and synchrotron radiation laminography. Composites: Part A, Vol. 52, 2013, p. 62-69.
-
Hufenbach W., Hornig A., Gude M., Böhm R., Zahneisen F. Influence of interface waviness on delamination characteristics and correlation of through-thickness tensile failure with mode I energy release rates in carbon fibre textile composites. Materials and Design, Vol. 50, 2013, p. 839-845.
-
Aymerich F., Staszewski W. J. Impact damage detection in composite laminates using nonlinear acoustics. Composites: Part A, Vol. 41, 2010, p. 1084-1092.
-
Klepka A., Pieczonka L., Staszewski W. J., Aymerich F. Impact damage detection in laminated composites by non-linear vibro-acoustic wave modulations. Composites: Part B, (In press).
-
Esmaeel R. A., Taheri F. Delamination detection in laminated composite beams using the empirical mode decomposition energy damage index. Composite Structures, Vol. 94, 2012, p. 1515-1523.
-
Hu H., Wang B. T., Lee C. H., Su J. S. Damage detection of surface cracks in composite laminates using modal analysis and strain energy method. Composite Structures, Vol. 74, 2006, p. 399-405.
-
Lakhdar M., Mohammed D., Boudjemâa L., Rabiâ A., Bachir M. Damages detection in a composite structure by vibration analysis. Energy Procedia, Vol. 36, 2013, p. 888-897.
-
Pérez M. A., Gil L., Oller S. Impact damage identification in composite laminates using vibration testing. Composite Structures, Vol. 108, 2014, p. 267-276.
-
Radzieński M., Krawczuk M., Palacz M. Improvement of damage detection methods based on experimental modal parameters. Mechanical Systems and Signal Processing, Vol. 25, 2011, p. 2169-2190.
-
Hadjileontiadis L. J., Douka E. Crack detection in plates using fractal dimension. Engineering Structures, Vol. 29, 2007, p. 1612-1625.
-
Wang Q., Deng X. Damage detection with spatial wavelets. International Journal of Solids and Structures, Vol. 36, 1999, p. 3443-3468.
-
Chang C. C., Chen L. W. Vibration damage detection of a Timoshenko beam by spatial wavelet based approach. Applied Acoustics, Vol. 62, 2003, p. 1217-1240.
-
Loutridis S., Douka E., Hadjileontiadis L. J. A two-dimensional wavelet transform for detection of cracks in plates. Engineering Structures, Vol. 27, 2005, p. 1327-1338.
-
Rucka M., Wilde K. Application of continuous wavelet transform in vibration based damage detection method for beams and plates. Journal of Sound and Vibration, Vol. 297, 2006, p. 536-550.
-
Fan W., Qiao P. A 2-D continuous wavelet transform of mode shape data for damage detection of plate structures. International Journal of Solids and Structures, Vol. 46, 2009, p. 4379-4395.
-
Katunin A. Damage identification in composite plates using two-dimensional B-spline wavelets. Mechanical Systems and Signal Processing, Vol. 25, 2011, p. 3153-3167.
-
Katunin A. Vibration-based damage identification in composite circular plates using polar discrete wavelet transform. Journal of Vibroengineering, Vol. 15, 2013, p. 355-363.
-
Katunin A., Holewik F. Crack identification in composite elements with non-linear geometry using spatial wavelet transform. Archives of Civil and Mechanical Engineering, Vol. 13, 2013, p. 287-296.
-
Zhong S., Oyadiji S. O. Crack detection in simply supported beams without baseline modal parameters by stationary wavelet transform. Mechanical Systems and Signal Processing, Vol. 21, 2007, p. 1853-1884.
-
Zhong S., Oyadiji S. O. Crack detection in simply supported beams using stationary wavelet transform of modal data. Structural Control and Health Monitoring, Vol. 18, 2011, p. 169-190.
-
Zhong S., Oyadiji S. O. Detection of cracks in simply supported beams by continuous wavelet transform of reconstructed modal data. Computers & Structures, Vol. 89, 2011, p. 127-148.
-
Rucka M., Wilde K. Neuro-wavelet damage detection technique in beam, plate and shell structures with experimental validation. Journal of Theoretical and Applied Mechanics, Vol. 48, 2010, p. 579-604.
-
Hein H., Feklistova J. Computationally efficient delamination detection in composite beams using Haar wavelets. Mechanical Systems and Signal Processing, Vol. 25, 2011, p. 2257-2270.
-
Xiang J., Liang M. A two-step approach to multi-damage detection for plate structures. Engineering Fracture Mechanics, Vol. 91, 2012, p. 73-86.
-
Katunin A., Przystałka P. Detection and localization of delaminations in composite beams using fractional B-spline wavelets with optimized parameters. Eksploatacja i Niezawodnosc – Maintenance and Reliability, Vol. 15, 2014, p. 391-399.
-
Katunin A., Przystałka P. Damage assessment in composite plates using fractional wavelet transform of modal shapes with optimized selection of spatial wavelets. Engineering Applications of Artificial Intelligence, Vol. 30, 2014, p. 73-85.
-
Unser M., Blu T. Fractional splines and wavelets. SIAM Reviews, Vol. 42, 2000, p. 43-67.
-
Chaudhury K. N., Unser M. Construction of Hilbert transform pairs of wavelet bases and Gabor-like transforms. IEEE Transactions on Signal Processing, Vol. 57, 2009, p. 3411-3425.
-
Starck J. L., Fadili J., Murtagh F. The undecimated wavelet decomposition and its reconstruction. IEEE Transactions on Image Processing, Vol. 16, 2007, p. 297-309.
-
Katunin A. Vibration-based spatial damage identification in honeycomb-core sandwich composite structures using wavelet analysis. Composite Structures, Vol. 118, 2014, p. 385-391.
About this article
The research project was financed by the National Science Centre (Poland) granted according the decision No. DEC-2011/03/N/ST8/06205. The financial support for publishing of the Rector of the Silesian University of Technology within the habilitation Grant No. RGH-9/RMT6/2014 is gratefully acknowledged.