Abstract
The influence of coupling to the fluid field is neglected in the classic fluid mechanics theory. United Lagrangian-Eulerian method is used to solve the fluid-structure interaction (FSI) problem of the nonviscous and incompressible fluid flow around an elastic box plate taking into account the influence of deformation of the elastic plate. In this approach, each material is described in its preferred reference frame. Fluid flows are given in Eulerian coordinates whereas the elastic body is treated in a Lagrangian framework. The coupling between the fluid and elastic body domains is kinematic and dynamic conditions at the body surface. The kinematic and dynamic conditions are given in Eulerian and Lagrangian coordinates. The dynamic equation of the elastic box plate is expressed combining the dynamic conditions at the interface. The knowledge of both dynamic and static deformations, static pressure and velocity distributions is given by using the Taylor expansions method. The effect of plate deformation is taken into account for the obtained solutions.
1. Introduction
This paper deals with the mathematical analysis of problems dealing with steady fluid-structure interactions (FSI) phenomena by a new theoretical method. Our attention is the both dynamic and static deformations, static velocity and pressure when flow around the elastic bodies immersed in a fluid stream. Such immersed-body flows are commonly encountered in engineering studies: aerodynamics (airplanes, rockets, projectiles), hydrodynamics (ships, submarines, torpedoes), transportation (automobiles, trucks, cycles), wind engineering (building, bridges, water towers, wind turbines), and ocean engineering (buoys, breakwaters, pilings, cables, moored instruments) [1-3]. And these phenomena have been studied by many authors over the past few years from different points of view (theoretical algorithm, numerical analysis and simulation, etc) [4-7].
Typically, fluid and structure are given in different coordinate systems making a common solution. Fluid flows are given in Eulerian coordinates whereas the structure is treated in a Lagrangian framework. We use united Lagrangian-Eulerian method to present the deformation, pressure and velocity of flow of a nonviscous, incompressible fluid around an elastic box plate. It is a new method of where fluid and structure equations are given in their preferred reference frames. The coupling between the fluid and structure domains is kinematic and dynamic conditions at the body surface. The effect of deformation of the elastic plate is taken into account by united Lagrangian-Eulerian method. It is different from the classic fluid mechanics.
A schematic of steady and irrotational flow of a nonviscous, incompressible fluid around an elastic box plate is shown in Fig. 1. Thus the effect of viscosity, compression and fluid rotation are neglected. An orthogonal xyz coordinate system is used, and all investigated values of the plate and fluid are assumed to be functions independent of the coordinate z. The surfaces A and B of box plate are elastic, and the others are rigid. The surface A is very close to B. This article mainly studies the simply supported plate A. The pressure inside of the box plate is assumed to be constant. The physical parameters of the two-dimensional plate are: the mass density ρs, length H, thickness h and bending stiffness D=Eh/[12(1-ν2)]3, where E is Young’s modulus and ν is the Poisson ratio.
Fig. 1Schematic of flow around an elastic box plate
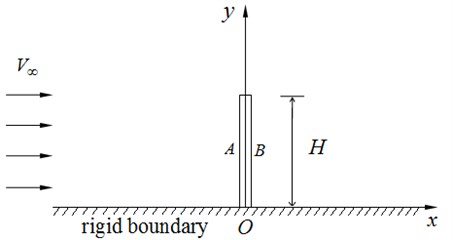
2. Dynamic equations
In this section the governing equations for the separate fluid and structural problems are presented together with the surface coupling conditions.
2.1. Structure equations
The displacement field of the middle surface of the surface A of the box plate is given by the following components: w, u; for x and y axes, respectively.
The theory of minor deflection of the plate is used. The middle surface of the plate can not be flexed. We have the following dynamic equation [8, 9]:
where Z1 is projection of the external mass forces, t is time.
2.2. Fluid equations
The fluid state equations can be written in an Eulerian reference frame. The steady state equations for a potential flow can be described as:
in which φ is the velocity potential, p is the pressure. And φ satisfies the condition:
where p∞, ρ∞ and V∞ are the pressure, mass density, and velocity of the stationary flow on the infinite boundary, respectively.
2.3. United Lagrangian-Eulerian method
The structure and fluid state equations can be written in Lagrangian and Eulerian reference frames, respectively. The coupling between the fluid and structure are kinematic and dynamic conditions at the surface, as illustrated in Fig. 2. The kinematic condition is the no slip condition, i.e., continuity in velocity, and the dynamic condition is surface continuity in tractions [9]. They are written as:
in which v is the velocity vector of fluid flow, u is the displacement vector of structure, p and pi are the pressures along outward and inward normal directions. k*3 is the outward unit normal vector to the structure at the surface between structure and fluid in the deformed configuration. This can be expressed as:
E3=(1+e11)(1+e22)-e12e21,
Fig. 2Two positions of structural elements in space

The scalar contact conditions are given by:
where vi and Zi (i= 1, 2, 3) are the projections of the velocity and the external force vector at point M*. The velocity function v(r) and pressure function p(r) can be written in an Eulerian reference frame at point M. The function v(r+u) and p(r+u) can be expressed in terms of Taylor expansion of v(r) and p(r). Then the kinematic and dynamic conditions can be written as [9]:
where V1, V2 and V3 are the projections of the velocity vector at point M. They can be expressed as:
+u3h3[∂v1∂x3-∂h3h1∂x1v3]+V'1(u21h21∂v1∂x1,⋯).
The complex functions V'1, V'2, V'3 are the velocity components concerned with the quadratic expressions of Taylor expansions.
Taking into account the minor deformation of the structure, the kinematic condition of the structure can be expressed as:
-u3h3[∂v3∂x3+∂h3h1∂x1v1+∂h3h2∂x2v2].
The dynamic conditions can be expressed as:
In this study, for the box plate, u3=w, u2=u, α2=x2=y, α3=x3=x, h2=1, h3=1, H2=1, H3=1, substituting these terms into Eqs. (16) and (17), the kinematic and dynamic conditions can be written as:
Thus the dynamic equation of the plate is expressed as:
This article studies minor deflection of plate, then displacement u is neglected.
3. Theoretical solutions of dynamic equations
We study the dynamic and static fluid- structure interactions problems. When the plate is assumed to be absolutely rigid (w1≡0), the relative velocity potential φ1 and the pressure p1 of fluid are introduced. The velocity potential φ2 and the pressure p2 which concerning the thin plate bend, w2 is the deflection of elastic plate, then we obtain:
Then substituting Eq. (21) into Eqs. (2)-(4) and (18)-(20), the following expressions for φ1 and p1 can be written:
The following expressions for φ2 and p2 can be written:
Eq. (20) can be written as:
The expression of velocity potential φ1 is given by [10]:
Substituting Eq. (31) into (23), the pressure p1 can be written as:
-[y+y(H2+x2-y2)-2x2y√4x2y2+(H2+x2-y2)2]22[√4x2y2+(H2+x2-y2)2+H2+x2-y2]}.
Let us consider the general forms of the displacement and velocity potential:
where Wn and Ai are coefficients to be determined, cosθ=x/√x2+y2, ω=2πf,f is frequency of disturbance force, j is imaginary unit. Taking into account the minor deflection of the plate, one item is used for φ2.
Substituting Eqs. (33) and (34) into (29) and (30), and using Taylor expansions at y=H/2, the following expressions can be written:
The solutions of the set of Eqs. (35)-(37) are:
-36S(243Q2S-27QT+512H2Sμ2+1152Sμγ-96πH2Qμ2-216πQμγ)9Q(162π2μQ2-1728πμQS+4608μS2),
where:
The solutions of the corresponding static equations are:
4. Numerical examples and discussion
In this section, numerical examples are presented. The test elastic plate and fluid flow have the following characteristics: plate mass density ρs=7850 kg/m3, thickness h=1×10-3 m, length H=1 m, Young’s modulus E=200×109 N/m2, Poisson’s ratio ν=0.3, flow velocity V∞=0.06 m/s, mass density ρ∞=1000 kg/m3, pressure p∞=1×105 Pa. The obtained time histories of the deflection and the vibration velocity are shown in Fig. 3 and Fig. 4, respectively. These figures show that the modal shapes of the different frequencies of the vibration plate are different.
The corresponding statics results are shown in Fig. 5-Fig. 10.
Fig. 5 shows the deformation w by varying the length of plate. The deformation w is the maximum value near the middle of the plate, closer to y=0. And w is zero at y=0, H, respectively.
In Fig. 6, the pressures of the plate surface are given for different length of plate. To examine the effect of deformation, we compared the pressure considering the effect of deformation and without the effect (Fig. 7). It shows the pressures considering the effect of deformation are very close to those without the effect of deformation. Thus the effect of deformation can be ignored for the problem of minor deformation.
We define the pressure coefficient Cp=2(p-p∞)/ρ∞V2∞. Fig. 8 shows the positive pressure coefficient changes slightly from y=0. The pressure coefficient is negative near y=H and the value changes sharply.
Fig. 3Time history of the deflection with f= 2 Hz and f= 10 Hz
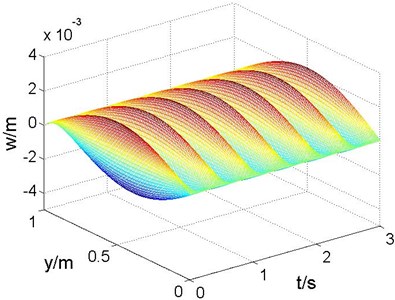
a)f= 2 Hz
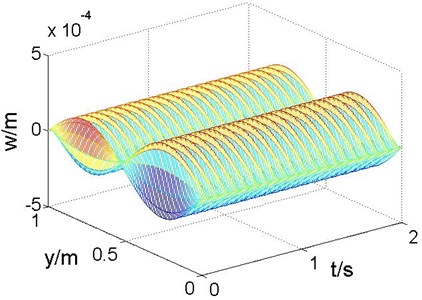
b)f= 10 Hz
Fig. 4Time histories of the vibration velocity
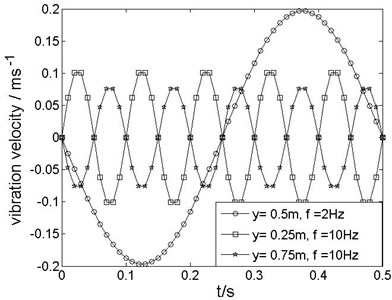
Fig. 5Deformations of plate for H= 0.9 m, 1.0 m and 1.1 m
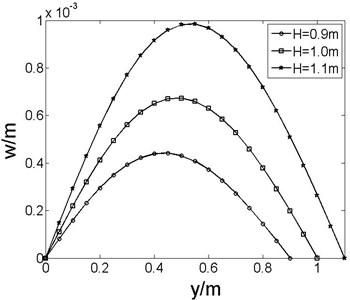
Fig. 6Pressure of the plate surface
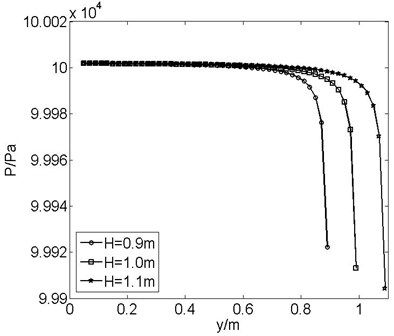
Fig. 7Comparison the pressure of plate surface considering the effect of deformation and without the effect
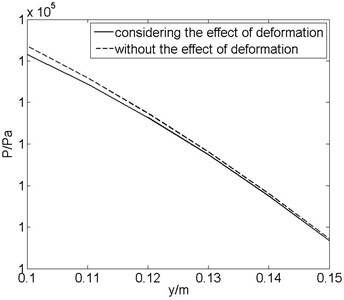
Fig. 9 and Fig. 10 illustrate the fluid velocity from united Lagrangian-Eulerian method. It is seen that a stagnation point where V=0 exists the point y=0 on the front side of the box plate. Bernoulli's equation predicts a maximum pressure at stagnation point because the velocity is zero at such points. A maximum velocity, and thus a minimum pressure, would exist near the plate tips.
An example of finite element method (FEM) is presented to illustrate the united Lagrangian-Eulerian method for FSI problems discussed in the present paper. The FEM model is depicted in Fig. 11. On the inflow boundary (the bottom) the velocities are prescribed Vx=0.06 m/s and Vy=0, the displacements are prescribed zero. On the outflow boundary (the top) the pressure is zero. The fluid displacement Uy (for y axes) and velocity Vy of flow are zero on the left and the right boundaries. The domain has the dimensions 2 m×2 m. The model consists of 60802 nodes and 60000 elements: fluid 141 elements for the fluid and plane 42 elements for the structure. The time step is 0.1 s.
Fig. 8Pressure coefficient of plate surface for H= 0.9 m, 1.0 m and 1.1 m
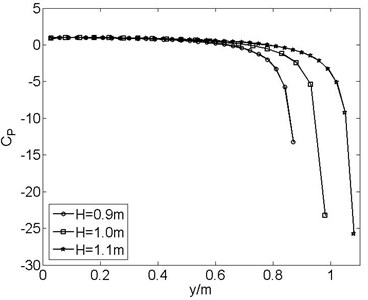
Fig. 9Fluid velocity with V∞= 0.06 m/s and H= 1 m
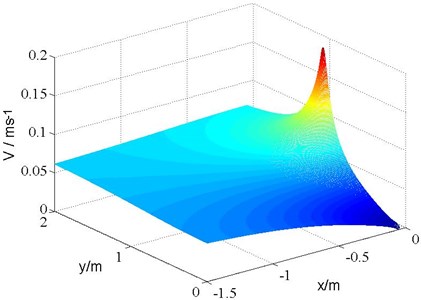
Fig. 10Vx-x, Vx-y, Vy-x and Vy-y curves when V∞= 0.06 m/s and H= 1 m at various values of x or y
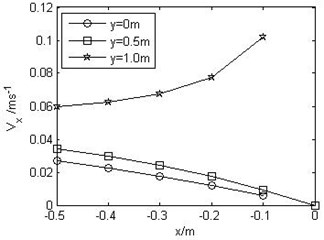
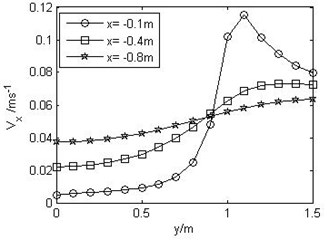
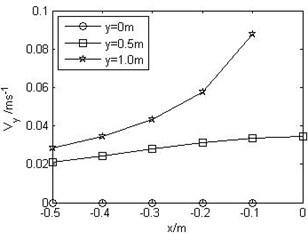
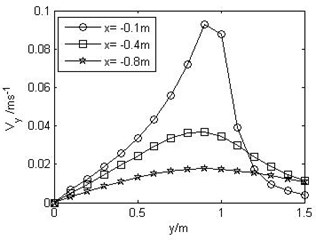
Fig. 12 and Fig. 13 present the deformation of the plate and the velocity vector of the fluid, which are obtained from FEM. It is seen that FEM solutions are consistent with theoretical results.
Fig. 11FEM model of fluid flow around an elastic plate
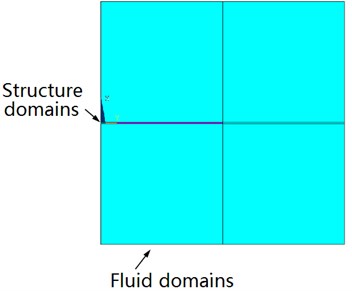
Fig. 12Deformation profile of FEM
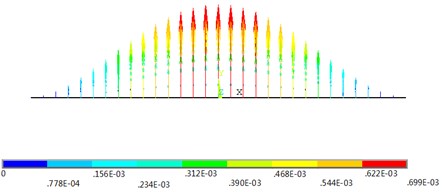
Fig. 13Velocity vector profile of FEM
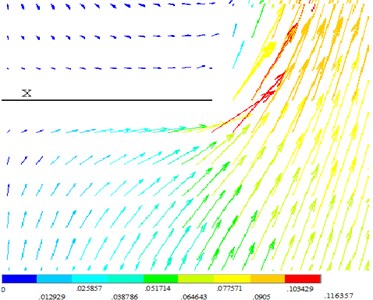
5. Conclusions
Flow around an elastic box plate provides an example in this study. To united Lagrangian-Eulerian method, the plate and fluid state equations can be written in Lagrangian and Eulerian reference frames, respectively. The coupling between the fluid and plate domains is kinematic and dynamic conditions at the surface. The theoretical deformation, pressure and velocity of the problem of flow around an elastic box plate have been derived. Numerical results reveal the streamlines with very high velocities and low pressures near the plate tips. It is shown that the united Lagrangian-Eulerian method is an effectively method for the problem of elastic structure acted by ideal fluid flow.
References
-
NayerG. D., Kalmbach A., Breuer M., Sicklinger S., Wuchner R. Flow past a cylinder with a flexible splitter plate: A complementary experimental–numerical investigation and a new FSI test case (FSI-PfS-1a). Computers and Fluids, Vol. 99, 2014, p. 18-43.
-
Yakubov S., Cankurt B., Abdel-Maksoud M., Rung T. Hybrid MPI/OpenMP parallelization of an Euler-Lagrange approach to cavitation modeling. Computers and Fluids, Vol. 80, 2013, p. 365-371.
-
Flores F., Garreaud R., Muñoz R. C. CFD simulations of turbulent buoyant atmospheric flows over complex geometry: Solver development in Open FOAM. Computers and Fluids, Vol. 82, 2013, p. 1-13.
-
Chen S. S. A review of flow-induced vibration of two circular cylinders in cross-flow. ASME Journal of Pressure Vessel Technology, Vol. 108, 1986, p. 382-393.
-
Zdravkovich M. M. Review of interference-induced oscillations in flow past two parallel circular cylinders in various arrangements. Journal of Wind Engineering and Industrial Aerodynamics, Vol. 28, 1988, p. 183-200.
-
Chen W. Q., Ren A. L., Deng J. Numerical simulation of flow-induced vibration on two circularcylinders in a cross-flow; Part I: transverse y-motion. Acta Aerodynamica Sinica, Vol. 23, 2005, p. 442-448, (in Chinese).
-
Lee T. R., Chang Y. S., Choi J. B., Kim D. W., Liu W. K., Kim Y. J. Immersed finite element method for rigid body motions in the incompressible Navier-Stokes flow. Computer Methods in Applied Mechanics and Engineering, Vol. 197, 2008, p. 2305-2316.
-
Kovalenko A. D., Grigorenko I. M., Iljin L. A. Theory of Conical Thin Shell. Kyiv, Ukraine Academy of Sciences Press, 1963, (in Russian).
-
Iljgamov M. A. The Introduction to Nonlinear Hydroelasticity. Moscow, Nauka, 1991, (in Russian).
-
Dong Z. N., Zhang Z. X. Nonviscous Fluid Mechanics. Beijng, Tsinghua University Press, 2003, (in Chinese).
About this article
This work was supported by National Natural Science Foundation of China (No. 11102181) and by Natural Science Foundation of Hebei Province (No. A2012203117).