Abstract
In allusion to the phenomenon that single stress is being used to conduct accelerated storage test currently, in order to establish a reasonable accelerated storage test program, an optimization design method of temperature and vibration step-down-stress accelerated storage test based on cumulative damage method was proposed. The minimum asymptotic variance of product’s medium life estimated value at normal working stresses is taken as optimum target, each accelerated stress level as design variable. Meanwhile, employing maximum likelihood estimation theory for fisher matrix, the mathematic model of multi-stress accelerated storage test plan’s optimal design was built. Comparing the minimum asymptotic variance of each scheme by an example of space electric connector, 5 is determined to be the optimal scheme. Using Monte-Carlo simulation to analyze volatility of minimum asymptotic variance and mean minimum asymptotic variance, it further proves the scheme when is 5 to be optimal. The optimized test plan can not only solve optimization design and evaluation for small sample accelerated storage test, but also can ensure the accuracy of evaluation, reduce test times, shorten test time and save cost.
1. Introduction
With the development of social requirement and technology, more and more attention is paid to high-reliability and long-lifetime products of aviation, aerospace and other applications; especially the reliability of current products has become more sophisticated, and it takes a long time to gain the storage reliability of product in a natural environment. Therefore, accelerated life testing (ALT) methodology is becoming a central issue in the reliability testing domain. The single stress acceleration model has been widely used in engineering currently, such as Arrhenius model, etc. [1]. However, products during actual storage period will be affected by two or more environmental stresses at the same time, such as temperature, vibration, humidity, etc. In order to simulate the real environmental stresses when electromechanical products encountered in usage, Nelson put forward the accelerated life test plan and optimization method under multiple stresses [2]. Under the precondition of no interaction among stresses, Escobar and Meeker put forward the optimization design method and criterion used for censored data of double stresses accelerated life test plan [3]. The theory and method of multi-stress accelerated life testing scheme optimization design under temperature and vibration is given in Ref. [4-5]. Ref. [6] discussed multiple stresses accelerated life testing scheme optimization design theory and method based on temperature and vibration test regularly under constant stress. However, among all kinds of accelerated life test methods, constant stress accelerated life test is mostly applied at present, while step-down-stress method is least seen both at home and abroad. The multi-stress accelerated storage test based on step down stress, as a test method of more efficient and closer to actual working environment [7-8], has become a development direction of accelerated storage test in the practical engineering application.
In this paper, taking electromechanical products as research object, a general model for describing failure processes is established by converting degradation processes at each stress level to the first stress level based on accumulative damage theory [9]. Taking the minimum asymptotic variance of electromechanical products medium life as optimization goal [12-15], this paper put forward an optimization design method of temperature-vibration multi-stress accelerated storage test scheme, which provides technical support for high reliability and long life electromechanical products multi-stress accelerated storage test based on step down stress.
2. Reliability statistical model of electromechanical products
2.1. The failure distribution function
Under the impact of environmental stresses during the long storage period, the life distribution of electronic equipment obeys Weibull distribution [9], denoted as Weibull (, ).
2.2. Accelerated model
The general Eyring model [10], which is applicable to the condition where the failure is caused by temperature stress and vibration stress at the same time, can be represented as follows:
where, denotes characteristics of products; is activation energy, usually in electron-volts; stands for the Boltzmann’s constant; represents the absolute Kelvin temperature; represents vibration strength (unit: g2/Hz); and are parameters to be estimated, 0.
Taking logarithm function on both sides, let the distribution parameters of product lifetime is the function of stress and , namely:
3. Stress accumulation effect
Assuming that: The remaining lifetime of specimens only depends on the currently cumulative fraction failed and current stress regardless how the fraction accumulated [11]. Specifically, the cumulative failure probability cumulated under stress level by time is equal to the cumulative failure probability cumulated under stress level by time . Under Weibull distribution, there is:
According to the basic assumption , the acceleration factor of relative to can be represented as:
Under step-down-stress accelerated storage test, the failure time is not the product’s real lifetime under besides . Therefore the real lifetime data under stress level can be represented as:
where . is the compensation of failure time converted by working time under .
4. The maximum likelihood estimation (MLE) of test optimization scheme
4.1. Likelihood function of censored samples
In order to simplify the formula, let , the Weibull distribution can be transformed to extreme value distribution. Its probability density function is:
where, . For th test specimen, the failure time under stress combination is . Then:
Therefore, the likelihood function of th test specimen can be denoted as follows:
Let , where, . The likelihood function of the whole test sample can be represented as follows:
4.2. Fisher information matrix and covariance matrix
According to the maximum likelihood estimation theory, the variance and covariance matrix of model parameter estimates can be presented as:
where, is the inverse matrix of information matrix, namely, . While, the information matrix is the expectation of likelihood function’s negative second order partial derivative matrix. Combined with Eq. (10), there is:
where, is mathematical expectation of parameters .
5. Mathematical model of testing scheme optimization design
5.1. Objective function
Assuming that temperature stress levels and vibration stress levels are both , which satisfies , . And test sample is . According to uniform design theory, the SDSAST only need to be conducted steps [12]. For linear extremum model, under the stress combination the order quantile of product life distribution is [13]. When 0.5, –0.3665, the order quantile of product lifetime is the product’s median life [2]. Under the normal stress level combination the asymptotic variance can be represented as:
Regarding the minimum asymptotic variance of normal stress level combination as objective function, namely solving [14].
5.2. Selection of design variables
Now that the maximum temperature stress level, the highest vibration stress level, normal temperature and vibration stress level are all given, the order quantile estimates of normal life distribution only depends on the rest two groups of -1 stress levels and failure time considering stress accumulation effect, namely, the optimization design variables are mainly , , and accumulation failure time , ,…, .
5.3. Constraint conditions
1) Stress level: Before stress combination, temperature stress levels must satisfy and vibration stress levels must satisfy .
2) In order to guarantee a certain acceleration effect, the acceleration factor of all levels relative to normal stress level must be bigger than a certain value, namely: and .
3) The combination of temperature and vibration stress should satisfy uniform design table.
5.4. Optimization model
Summing up conditions above, the mathematical model of multi-stress ALT optimization design scheme can be concluded as follows:
6. Numerical example
6.1. Multi-stress accelerated storage test optimization design of an electric connector
6.1.1. Multi-stress accelerated storage test of an electric connector
Space electric connectors obey Weibull distribution. There are 6 sets of products to be conducted SDSAST. Temperature and vibration are the accelerated stresses. Test is started from the highest stress combination and turned to the next stress combination when there is a failure product and will be continued unless there is a failure product under the stress combination of . Under the storage condition, the normal temperature and vibration stress level are 25°C and respectively. The initial temperature accelerated stress can be determined by work limit stress through reliability enhancement testing, which is 158°C. By referring other test experience, the required highest vibration stress is determined to be . The least temperature level and vibration stress level are 95°C and .
6.1.2. Optimized design results
The estimates of can be obtained by referring prior experience. Employing Monte-Carlo simulation, the failure data of electromechanical products by simulation can be obtained. The asymptotic variances of product’s median life is minimum when 5, which is 0.0034. So, it is determined that the scheme is optimal when 5. The optimized multi-stress accelerated storage test scheme is shown as Table 1.
Table 1Optimization design scheme of accelerated storage test when k= 5
No. | Temperature (K) | Temperature level | Vibration (g2/Hz) | Vibration level |
1 | 431.15 | 2.3194 | 0.80 | –0.2231 |
2 | 413.46 | 2.4186 | 0.20 | –1.6094 |
3 | 397.17 | 2.5178 | 0.60 | –0.5108 |
4 | 382.11 | 2.6170 | 1.00 | 0 |
5 | 368.15 | 2.7163 | 0.40 | –0.9163 |
6.2. Monte-Carlo simulation and verification
In order to illustrate the rationality of optimization scheme, 100 groups of experimental data are generated employing Monte-Carlo to simulate each accelerated storage test schema.
Fig. 1Minimum asymptotic variance value volatility of each program
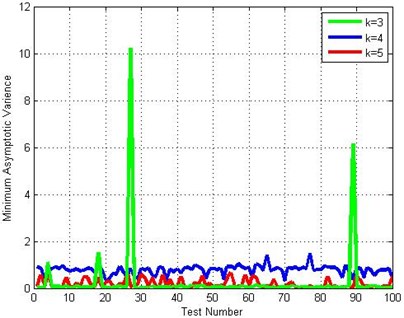
Fig. 2Minimum asymptotic variance mean value volatility of each program
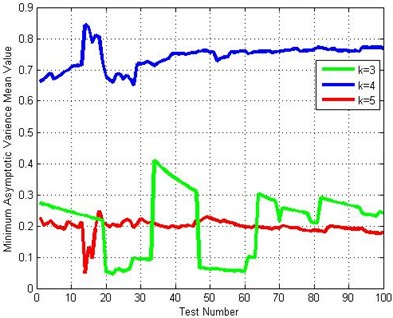
Drawing the variation tendency figure of the minimum asymptotic variance and the minimum asymptotic variance mean value changing with experiment times, which are shown as Fig. 1 and Fig. 2. From Fig. 1, it is easy to see that the asymptotic variance of median life is minimum when 5. From Fig. 2, we see that the minimum asymptotic variance mean value is maximum when 4, median when 3, but has a bigger fluctuation. While the minimum asymptotic variance mean value is minimum when 5 and has a smaller fluctuation. In conclusion, the combination scheme is optimal when 5 in the combination schemes.
7. Conclusion
1) This paper develops an optimum design scheme of multi-stress SDSAST based on uniform design theory, which tackles the problem that testing is difficult to conduct when the factors and stress levels are bigger. Using this method, it can reach the result very close to full times test with less experiment times under the premise of estimation precision basically maintaining unchanged.
2) Considering cumulative damage effect, this paper put forward a method of establishing multi-stress SDSAST optimization design mathematical model of electromechanical equipment regarding the minimum asymptotic variance of equipment median life estimation under normal stress as the goal.
References
-
Nelson W. Accelerated life testing step-stress models and data analysis. IEEE Transaction on Reliability, Vol. R-29, Issue 2, 1980, p. 103-108.
-
Nelson W. Accelerated Testing-Statistical Model, Test Plans and Data Analysis. A Wiley-Interscience Publication, John Wiley & Sons, New York, 1990.
-
Escobar L. A, Meeker Jr. W. Q. Planning accelerated life tests with two or more experimental factors. Technometrics, Vol. 37, Issue 4, 1995, p. 411-427.
-
Chen W. H., Li SH. H., Lian W. ZH., et al. Accelerated life test and statistical analysis of aerospace electrical connecters under multiple environmental stresses. Journal of Zhejiang Unversty, Vol. 40, Issue 2, 2006, p. 348-351, (in Chinese).
-
Chen W. H., Feng H. Y., Qian P., et al. Theory and method for optimum design of accelerated life test plan under multiple stresses. Chinese Journal of Mechanical Engineering, Vol. 42, Issue 12, 2006, p. 101-105, (in Chinese).
-
Chen W. H., Qian P., Ma Z. K., et al. Optimum design of multiple stress accelerated life test plan under periodic inspection. Chinese Journal of Scientific Instrument, Vol. 30, Issue 12, 2009, p. 2544-2550, (in Chinese).
-
Zhang CH. H. Theory and method of step-down-stress accelerated life testing. Graduate School, National University of Defense Technology, Changsha, 2002, (in Chinese).
-
Li X. SH. Method and application of step-down-stress accelerated testing. Structure an Environment Engineering, Vol. 39, Issue 6, 2012, p. 59-62, (in Chinese).
-
Mao SH. S., TangY. C., Wang L. L. Reliability Statistics. Higher Education Press, Beijing, 2008, (in Chinese).
-
Peck D. S. Comperhensive model for humidity testing coreltion. Proc.24th Ann. Int Reliability Physics Symposium, 1986, p. 44-50.
-
Fang K. T., Ma CH. X. Orthogonal and Uniform Design. Science Press, BeiJing, 2001, (in Chinese).
-
Nasser F., Chen H. L. Optimal simple step stress accelerated life test design for reliability prediction. Journal of Statistical Planning and Inference, Vol. 139, Issue 1, 2009, p. 1799-1808.
-
Preeti W. S., Nidhi J. Optimum ramp-stress accelerated life test for m identical repairable systems. Applied Mathematical Modelling, Vol. 35, Issue 1, 2011, p. 786-793.
-
Elsayed E. A, Zhang H. Design of optimum reliability test plans under multiple stresses. Quality and Dependability, Vol. 3, Issue 1, 2005, p. 16-18.
-
Meng Y. F., Han R. L., Pan G. Optimal design of multiple step-down-stress accelerated life test with competing risks base on Monte-Carlo simulation. Instrument Technique and Sensor, Vol. 1, Issue 3, 2014, p. 92-95, (in Chinese).