Abstract
One of the first approaches to the development of a grinding process monitoring system based on audible sound sensors is presented in the paper. Electroplated diamond tools (abrasive D64 and D107) were used in a modified single-disc lapping machine configuration for flat grinding of ceramics (Al2O3). The main aim of the machine modification was to reduce the vertical vibration in order to decrease the tool wear and to increase the material removal rate. The sound generated by the material processing was analysed in the aspect of actual abrasive ability of the grinding tools. The abrasive properties of the tool are decreasing during machining due to the wear of diamond grains. The results from experiments, such as the material removal rates and waveforms of recorded sound are presented and discussed in the paper.
1. Introduction
Electroplated diamond tools, used for flat grinding in a single-disc lapping machine configuration, contain a single layer of diamond grains held on a steel disc surface by an electroplated nickel bond. The reason for choosing the lapping kinematics is that the lapping is very effective in eliminating the waviness errors, while conventional surface grinding is not. The natural way for the better technological effects is to combine these technologies (grinding and lapping) into one process. This can be realized by the application of grinding wheels including electroplated tools on single- or double-disc lapping machines [1-3].
Electroplated CBN and diamond tools are becoming widely used for machining of precise components. Unlike other conventional and superabrasive wheels, the topography of single-layer superabrasive tools is not periodically restored by truing or dressing [4] what is the technological advantage of their use. The basic difficulty in the application of these tools is the prediction of their life and wear, what was investigated by Hwang et al. for high speed grinding of silicon nitride [5]. The useful life of these wheels is restricted by the single abrasive layer that exist and by the limited amount of crystal exposure above the nickel plating. The results from [6] show that the wear rate depends more on crystal exposure than on active grain density. The image processing analysis indicated that the tool wear was caused not only by attrition, but also by grain fracture and pullout [1]. The longer tool life and improvements in the surface finish were achieved by the reduction of the vertical vibration, which directly influenced the tool wear. Higher vibrations increase the grain fracture and grain pullout, negatively affecting the final shape accuracy, which depends also on the tool shape error. The moderate rate of a fracturing phenomena is desirable for the electroplated tools because abrasive particles are not removed at once from the active tool surface, but still work as loose abrasive, like in lapping process – three-body abrasion. On the other hand the excessive removal of abrasive slurry from the active surface of the tool decreases the material removal rate and cutting properties of the electroplated wheel. The audible sound generated during grinding depends strongly on the actual abrasive properties of the tool. Machining process monitoring systems based on audible sound sensors were successfully applied for milling [7, 8] and turning [9, 10]. The vibration of the tool holder, together with the cutting insert, was considered as the main source of sound associated with tool wear [9]. Ease of mounting on the machine with good ratio cost/benefit were pointed out by authors as the main advantages of these sensors which are basically microphones. Results obtained by this approach for low frequency signal analysis could complete data from processes monitoring based on acoustic emission sensors for high frequency signal analysis - concept of sensor fusion technology [8].
The proposition of monitoring grinding process with the use of an audible sound sensor is the subject of the paper. Electroplated diamond tools (abrasive D64 and D107) were used in a single-disc grinding machine configuration for flat grinding of ceramics (Al2O3). The vertical vibration was reduced by the machine modification in order to decrease the tool wear and to increase the material removal rate. The sound generated by the material processing is presented as the waveforms analysed in the aspect of actual abrasive ability of the grinding tools, at the beginning and at the end of a tool life. Application of microphones as audible sound sensors seems to be a prospective approach for monitoring the grinding process mainly because of the low noise generated by elements of a designed machine tool. The flow of a cutting fluid (3 ml/min) and low kinematical parameters allowed for mounting the microphone quite far from the machine drives and very close to the machining area at the distance of ~10 mm.
2. Experimental set-up and procedure
Electroplated diamond tools used for flat grinding were mounted to the rotational steel base of a grinding machine – Fig. 1. The microphone MT392 was located close to the machining area (~10 mm). Ceramic workpieces were placed in a separator and loaded against a rotating tool. In the first solution without the spring damping, the steel weights were placed on the samples what occasionally caused their striking and tilting. In the second solution with damping, the load was induced by the spring (Fig. 2), allowing to decrease the tool wear due to the fact of the vertical vibration reduction. The highest cutting speed applied for both arrangements and all tests was vmax=1.4 m/s, with the average value v=0.8 m/s. Cutting fluid (based on kerosene and machine oil) was introduced drop by drop into the contact region between the workpieces and the diamond electroplated tool at the flow rate Q=3 ml/min. The linear material removal rate was checked with a micrometer of sensitivity 1 µm (from Mitutoyo company, Japan, Kawasaki). The height of the samples Δhw reduced by grinding was measured individually after each test.
Fig. 1Experimental set-up of a grinding machine with an electroplated tool and a microphone
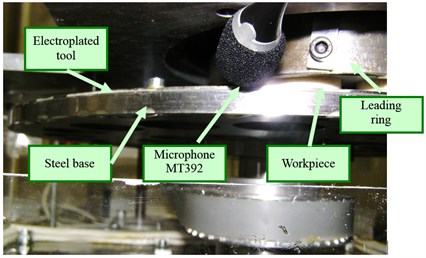
Fig. 2Cross-section of a leading ring with a spring damping
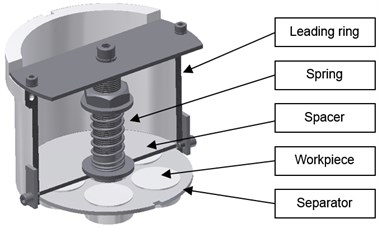
3. Kinematics model of the single-tool grinding process
The schematic illustration of the executory system of a single-tool grinding machine is presented in Fig. 3. The workpiece (3) loaded against a rotating tool (1) is placed in the separator (2) driven by a leading ring (4). Displacement trajectories of any point P from the workpiece surface can be determined in two co-ordinate systems with the equations given in Table 1. The relative co-ordinate system (x-y) belongs to the rotating grinding tool. Displacement trajectories are the cyclic curves so the grinding velocity and acceleration also change in cycles [1].
Fig. 3The executory system of the single-tool grinding machine: 1 – grinding tool, 2 – separator, 3 – workpiece, 4 – leading ring
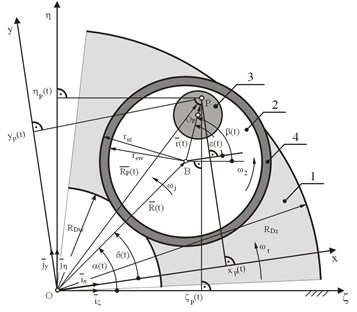
Table 1Equations for displacement trajectories in absolute and relative co-ordinate systems
Absolute co-ordinate system ζ-η | Relative co-ordinate system x-y |
-RP(t)=ζP(t)-iζ+ηP(t)-jη, [ζP(t)ηP(t)]=R[cosαsinα]+r[cosβsinβ], α(t)=ωjt,β(t)=ω2t. | -RP(t)=xP(t)-ix+yP(t)-jy, [xP(t)yP(t)]=R[cosδsinδ]+r[cosεsinε], δ(t)=(ωj-ωt)t,ε(t)=(ω2-ωt)t. |
where: ωt – angular velocity of the tool, ω2 – angular velocity of the leading ring and the separator, ωj – angular velocity of the arm 0-B. |
The cycle time is calculated from the equation:
Grinding speed (changing in cycles) of any workpiece point P as a function of time can be calculated using the formula:
4. Grinding results for ceramics
The first three tests were carried out on ceramic workpieces (Al2O3) with the use of the diamond electroplated tool (grains D107). The velocity of the tool nt=62 rpm and of the leading ring (workpiece holder) n2=120 rpm as well as the load on the contact area (p=2.7 kPa) were set, and tests (T1÷T3) were run for total machining time of 3 minutes for each test. Every three minutes, five workpieces were removed from the separator and, after cleaning, the material removal rate, surface roughness and waviness parameters were measured. Next tests (T4÷T6) were carried out also on ceramic workpieces (Al2O3) with the use of the electroplated diamond tool with grains D64. The test T4 was run for total machining time of 3 minutes and next tests T5 and T6 for 2 minutes each test. The machining time was reduced in order to minimize the wear of a single-layer electroplated diamond tool. The wear ratio was higher comparing to the previous set of tests (T1÷T3) because of smaller grains – D64. Contrary to expectations, experiments conducted with the smaller grains (D64) show similar level of the height reduction of ceramic workpieces Al2O3 (Fig. 4) as for bigger grains (D107) and just small improvements in the surface finish (Fig. 5). The same tendency was recorded for grinding with the spring damping but the values of average material removal rates were noticeably higher comparing to grinding without damping (Fig. 6).
Fig. 4The height reduction of ceramic workpieces Al2O3 after grinding without damping with the use of electroplated diamond tools
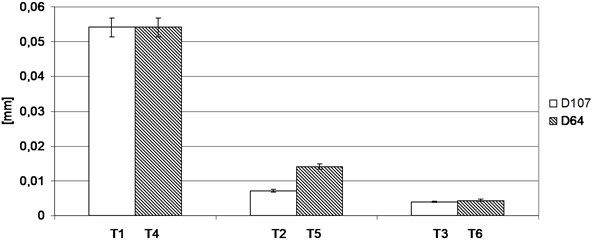
Fig. 5Average surface roughness and waviness parameters after grinding with diamond electroplated tools with grains D107 and D64 – grinding without damping
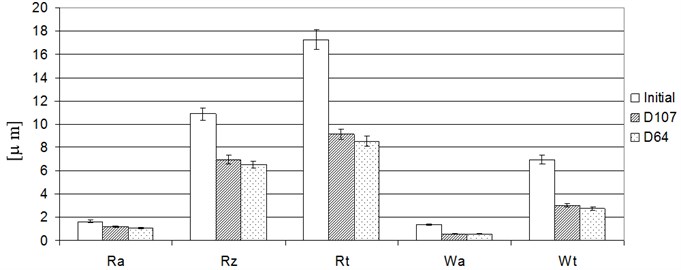
Fig. 6Average material removal rates (MRR) for ceramic workpieces Al2O3 and electroplated diamond tools with abrasive D107 and D64
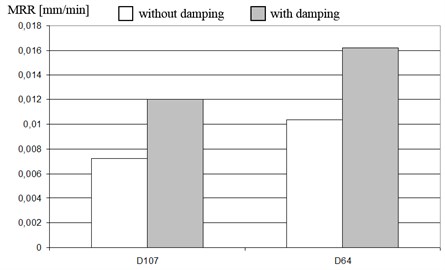
5. Audio tracks analysis
Audio tracks recorded during grinding experiments were analysed with the use of a free digital audio editor Audicity 2.0.3 (http://audacity.sourceforge.net). The audio tracks can be displayed in a default for Audicity waveform view with a linear vertical scale from –1.0 to +1.0 – Fig. 7. The waveform display can be also switched to a dB logarithmic view and the frequency analysis can be carried out for the chosen time period. During first tests T1 (grains D107) and T4 (grains D64), unworn electroplated tools had the highest abrasive ability, which was reflected in the wider shape of the audio waveform – Fig. 7(a), 7(c). The top and the bottom of the waveform are located further from the zero line, which is characteristic for the louder audio at the beginning of the tool life. During the last minute of tests T3 (grains D107) and T6 (grains D64) the abrasive grains located on the active surfaces of electroplated tools were worn. The wear of abrasive grains, caused by attrition as well as by grain fracture and pullout, decreased the material removal rate – Fig. 4. Lower abrasive properties of the grinding tools at the final stage of machining are illustrated by the narrower audio waveforms – Fig. 7(b), (d). The audio tracks were quieter at the end of the tool life due to the wear of the abrasive grains, with the top and bottom of the waveforms closer to the zero line.
Fig. 7Audio tracks in a waveform view with a linear vertical scale from –1.0 to +1.0 (dimensionless unit): the first minute of test T1 (a) and the last minute of test T3 (b) during grinding with the use of the electroplated tool with grains D107; the first minute of test T4 (c) and the last minute of test T6 (d) during grinding with the use of the electroplated tool with grains D64
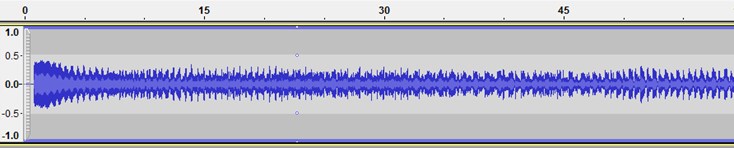
[s]
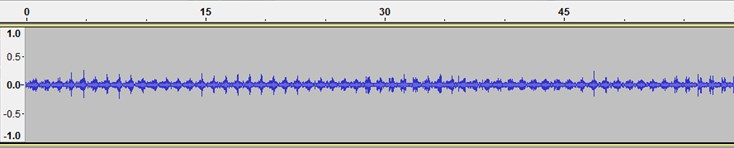
[s]
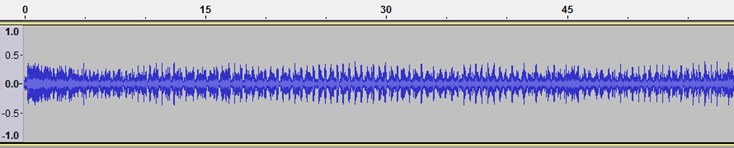
[s]
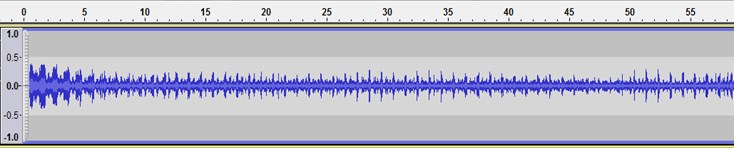
[s]
6. Conclusions
The proposition of monitoring the grinding process with the use of an audible sound sensor is the subject of the paper. Electroplated diamond tools (abrasive D64 and D107) were used in a single-disc machine configuration for flat grinding of ceramics (Al2O3). The vertical vibration was reduced by the machine modification in order to decrease the tool wear and to increase the material removal rate (MRR). The average MRR were noticeably higher for grinding with the spring damping comparing to grinding without damping.
One of the first approaches to the development of a grinding process monitoring system based on audible sound sensors is also presented in the paper. The sound generated by the material processing is illustrated as the waveforms analysed in the aspect of actual abrasive ability of the grinding tools, at the beginning and at the end of a tool life. Ease of mounting of the microphone close to the machining area (the distance of ~10 mm) and good ratio cost/benefit are the main advantages of these type of sensors. Presented results show close relationship between the actual state (abrasive properties) of the active surface of the tool and recorded audio tracks. Results obtained by this approach for low frequency signal analysis could complete data from grinding process monitoring based on acoustic emission (AE) sensors for high frequency signal analysis. Further analysis will be carried out to find the correlation between the surface roughness parameters (technological effects) and the waveform parameters of recorded audio tracks.
References
-
Barylski A., Deja M. Finishing of ceramics in a single-disk lapping machine configuration. Solid State Phenomena, Vol. 165, 2010, p. 237-243.
-
Beyer P., Marc van Ravenzwaaij Innovative flat honing with vitrified-bond grinding and conditioning tools. Industrial Diamond Review, Vol. 4, 2005, p. 47-50.
-
Sanchez L. E. A., Jun N. Z. X., Fiocchi A. A. Surface finishing of flat pieces when submitted to lapping kinematics on abrasive disc dressed under several overlap factors. Precision Engineering, Vol. 35, 2010, p. 355-363.
-
Shi Z., Malkin S. Wear of electroplated CBN wheels. ASME Manufacturing Science and Engineering, Vol. 128, 2006, p. 110-118.
-
Hwang T. W., Evans C. J., Whitenton E. P., Malkin S. High speed grinding of silicon nitride with electroplated diamond wheels, part 1: wear and wheel life. Manufacturing Science and Engineering, Vol. 122, Issue 1, 2000, p. 32-41.
-
Upadhyaya R. P., Fiecoat J. H. Factors affecting grinding performance with electroplated CBN wheels. CIRP Annals – Manufacturing Technology, Vol. 56, Issue 1, 2007, p. 339-342.
-
Ai C. S., et al. The milling tool wear monitoring using the acoustic spectrum. International Journal of Advanced Manufacturing Technology, Vol. 61, Issue 5-8, 2012, p. 457-463.
-
Rubio E. M., Teti R. Cutting parameters analysis for the development of a milling process monitoring system based on audible energy sound. Journal of Intelligent Manufacturing, Vol. 20, Issue 1, 2009, p. 43-54.
-
Lu M. C. Jr., E. Kannatey-Asibu E. Flank wear and process characteristic effect on system dynamics in turning. Journal of Manufacturing Science and Engineering, Vol. 126, Issue 1, 2004, p. 131-140.
-
Salgado D. R., Alonso F. J. An approach based on current and sound signals for in-process tool wear monitoring. International Journal of Machine Tools and Manufacture, Vol. 47, 2007, p. 2140-2152.
About this article
Scientific work financed from Polish budget funds for science for the years 2010-2011 as a research project N N503 157638.
The author would like to thank Assistant Professor Józef Kotus from Gdansk University of Technology (Faculty of Electronics, Telecommunications and Informatics, Department of Multimedia Systems) for his suggestions and remarks.