Abstract
The automobile industry has shown increased interest in the use of composite leaf spring due to its high strength to weight ratio. The introduction of composite materials has made it possible to reduce the weight of the leaf spring without any reduction in load carrying capacity and stiffness. In this paper, results of research on vibration suppression in steel and composite (Glass Fibre Reinforced plastic – GFRP) leaf springs are presented. Polymeric composite leaf springs and steel springs are studied. Composite springs were designed in such a way that they could replace steel springs in a van. The amplitude of vibrations and the reaction of props were measured and recorded. These parameters rendered it possible to calculate the coefficient of vibration suppression for steel and composite leaf springs. It is concluded that composite leaf springs in comparison to steel springs about three times better suppress vibrations, they are about five times lighter and generate smaller dynamic burdens to vehicle bodies.
1. Introduction
The aim of this research is to study the ability of composite spring leafs to suppress vibrations. The composite spring was designed in such a way that it could replace steel springs in a delivery van. A comparison of the properties of the steel and composite spring was made.
Composite materials allow any formation of transverse sections of elements being produced, at the same time affecting the stiffness of such elements. Thus, it is possible to construct suspensions with the prescribed characteristics as well as integrated elements of suspensions which work as springy and leading elements. Due to the above it has been possible to simplify the construction of vehicle suspension and to lower considerably its weight and costs of production. Moreover, a greater capacity of composite materials to accumulate springy energy may allow the use of smaller and simpler dampers. Numerous researchers [1-6] prove that springy elements constructed from composites materials in comparison with steel springs are characterized by higher fatigue durability, they are resistant to corrosion and they are many times lighter. A great advantage of composite materials is the way they get damaged under fatigue loading. Elements made of these materials, as opposed to steel elements, do not break or get damaged rapidly. This in turn increases considerably the safety of vehicle operation. The above mentioned properties of composite materials will decide about their wider application in the construction of vehicles, including also the construction of springy elements of suspensions. Increasing competition and innovation in automobile sector tends to modify the existing products by usage new and advanced material – polymer composites. The leaf spring absorb the vertical vibrations by means of vibrations in the spring and the energy absorbed is stored in spring as strain energy and then released slowly. The strain energy of composite material used for spring is the very important property. In next part of article the study of vibration damping ability will become proven.
2. Experimental researches
In order to carry out the research it was necessary to produce composite springs of the same properties as the steel ones. Many technical problems had to be overcome in order to obtain repeatability of properties. This problems was described in [4]. The composite springs were of the same dimensions as the steel springs and were installed in the same way as the steel springs. Fig. 1 presents the composite leaf spring. The springs have a constant width and a changing thickness. The shape of the leaf spring is parabolic. Every layer was made of an epoxy composite which was strengthened with continuous glass fibre. Such a structure of the leaf spring resulted from the necessity to assure sufficient shear strength of the central layers and the required flexibility. A detailed description of constructing such a spring is presented in [4].
Fig. 1Composite leaf spring
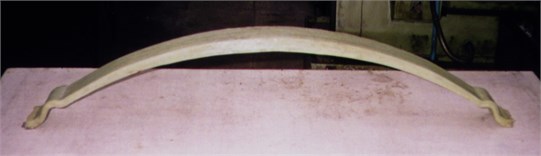
Table 1Basic dimensions of leaf spring
Parameter | Leaf spring | |
Composite | Steel | |
Spring’s width [mm] | 80 | 80 |
Spring’s length [mm] | 1305 | 1305 |
Spring’s mass [kg] | 12 | 50 |
Fig. 2Diagram of the research device: 1 – leaf spring; 2 – sensor of force; 3 – sensor of dislocations; 4 – amplifier; 5 – PC computer; 6 – striking part; 7 – runners; 8, 9 – steering components; 10 – body of the device
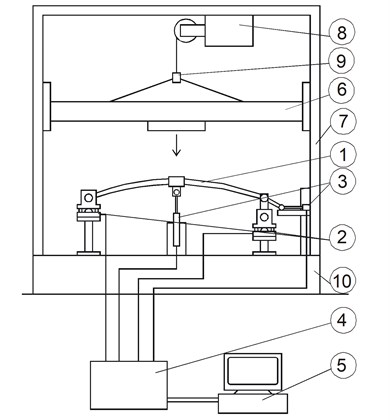
The device on which the research was carried out is shown in Fig. 2. It includes two principle components: the loading component and the measurement – registering component. The loading unit comprises a striking part – 6 and the steering component – 8. The measurement and registering component includes the sensor of force – 2, sensor of perpendicular dislocations of the centre of the spring – 3, sensor of horizontal dislocations of the ends of the spring – 3. The device made possible both the static and dynamic loading of the leaf spring. Loading has been carried out by free lowering of the striking part of 350 kg, which was hung on a rope and placed in runners. The strength of props was measured by the sensor of force, whereas perpendicular and horizontal dislocations of the central part of the spring as well as those of its movable end were measured by the sensors of dislocations. Signals from the sensors were transmitted to a PC where they were recorded in textual files. Steel and composite leaf springs were investigated.
Data from the sensors were recorded in textual files in a PC. Using these data, for each test graphs were made which showed the radial diffraction and the sum of perpendicular reactions of props as a function of time. Also, for each test the coefficient of vibration suppression was calculated. Fig. 3 present measurement data for the composite leaf spring, whereas Fig. 4 show the data for the steel leaf spring.
Fig. 3Diffraction and total perpendicular reaction of props in function of time composite leaf spring
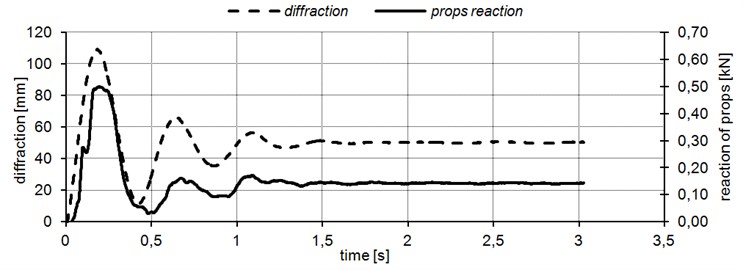
Fig. 4Diffraction and total perpendicular reaction of props in function of time steel leaf spring
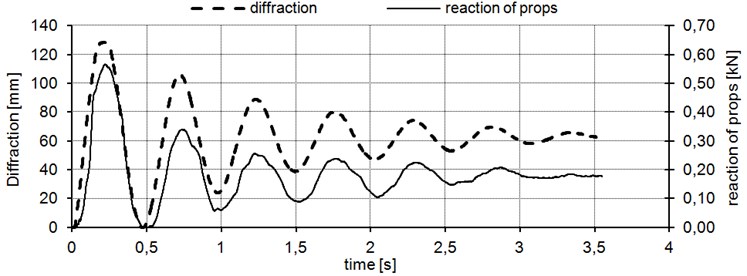
3. Recapitulation
Data from the sensors were recorded in textual files in a PC. Using these data, for each test graphs were made which showed the radial diffraction and the sum of perpendicular reactions of props as a function of time. Also, for each test the coefficient of vibration suppression was calculated.
Table 2 shows the coefficient of vibration suppression in steel and composite leaf springs. The coefficients of vibration suppression were calculated using the research results and the following equation:
where: D – logarithmic decrement of suppression; T – period of vibrations [s]; an – first (larger) inclination; an+1 – next inclination.
Fig. 5Diffraction and total perpendicular reaction of props in function of time steel leaf spring
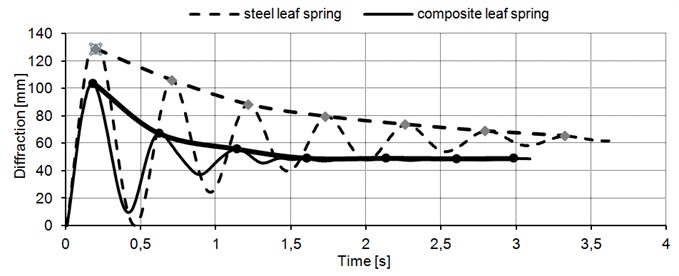
Table 2Suppression coefficients of vibrations composite and steel leaf springs
Test No. | Energy of hitting | Leaf spring coefficients of vibrations | |
Composite | Steel | ||
1 | Static load, Q= 3500 N | 2.77 | 1.12 |
2 | Static load, Q=3500 N | 3.30 | 1.18 |
3 | Static load, Q= 3500 N | 3.07 | 1.18 |
4 | 1400 J | 2.53 | 1.05 |
5 | 1400 J | 3.53 | 1.06 |
6 | 1400 J | 3.63 | 1.00 |
7 | 1750 J | 2.91 | 0.83 |
8 | 1750 J | 1.95 | 0.68 |
9 | 1750 J | 1.84 | 0.81 |
A comparison of the property of vibration suppression of some composite leaf springs and steel leaf springs is shown in Fig. 6.
Fig. 6Suppression coefficients of vibrations composite and steel leaf springs
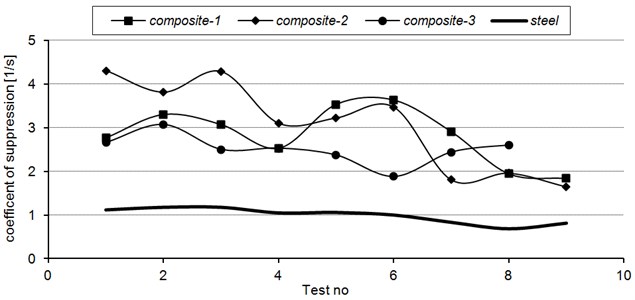
Coefficients of vibration suppression of leaf springs are very different. In the case of composite springs this value ranges from 1.65 to 3.63. The coefficients for steel springs do not reach such different values. The values are from 0.68 to 1.18 (Table 2).
Coefficients of vibration suppression of steel leaf springs are in the range of 1, they are about three times smaller than the coefficients for composite springs (Fig. 6).
Not only the value of vibration suppression coefficients of steel leaf spring is smaller, but also their sensibility to a change of loading. The coefficients of composite leaf springs clearly decrease when load is increased. At the same dynamic load, reactions of steel springs are larger than the reactions of composite springs. The difference is about 20 %.
4. Conclusions
1) Leaf springs made of a glass-epoxy composite have a greater ability to suppress vibrations than steel springs.
2) Composite materials offer a possibility of forming any shape of vehicle suspension components. Therefore, it is possible to obtain the desired stiffness, elasticity and vibration suppression in components made of these materials.
3) Vehicle components made of glass-epoxy composites are about 5 times lighter than made of steel.
4) The use of composite materials for the construction of vehicle components is a good way to reduce emissions of greenhouse gases.
References
-
Pozhilarasu V., Parameshwaran T. Pillai performance comparison of conventional and composite leaf spring. International Journal of Engineering Science and Technology, Vol. 4, Issue 12, 2012, p. 4827-4831.
-
Abdul Rahim, et al. Developing a composite based elliptic spring for automotive applications. Journal of Materials and Design, 2010, p. 475-484.
-
Al–Qureshi H. A. Automobile leaf springs from composite materials. Journal of Materials Processing Technology, 2001, p. 58-61.
-
Romanów Fr., Maćkiewicz J., Papacz Wł. Wybrane parametry wytrzymałościowe belek kompozytowych w aspekcie zastosowania na resory samochodowe. Konferencja KBN Zielona Góra, 2000.
-
Dave R. Automotive suspension systems benefit from composites. Journal of Reinforced Plastics, 2003, p. 18-21.
-
Deshmukh B., Jaju S. B. Design and analysis of glass fibre reinforced polymer (GFRP) leaf spring. Emerging, Trends in Engineering and Technology, 2011, p. 82-87.