Abstract
In view of the non-stationary and time-varying characteristics of the pressure fluctuation signal in the draft tube of hydraulic turbine, a method combining noise reduction based on Singular Value Decomposition (SVD) with Cascade Correlation (CC) neural network to analyze the pressure fluctuation signal is developed. Firstly, the singular value decomposition based on an improved threshold is used to reduce the noise, and then the signal component of different frequency band is extracted, finally the feature vector is applied to the CC neural network for pattern recognition, obtaining the different patterns of pressure fluctuation in the draft tube. The results show that this method is effective in identifying states of pressure fluctuation in the draft tube.
1. Introduction
With the improvement of unit capacity and size of a turbine, its running stability is very important [1-4]. According to the actual survey showing that about 10 % of turbines produce vibration, 60 % of which are made up of water pressure pulsation and rotator imbalance. Pressure fluctuation of the draft tube brought by vortex belt is the most familiar hydraulic vibration of the hydraulic turbine. When spreading to each part, the pressure fluctuation may cause the vibration of unit, the periodic swing of big axis, and the fluctuation of power and pressure fluctuation of flow in the piping, even can force to stop the unit and result in huge loss to the power station. There are three important states in the vibration characteristics of draft tube; they are normal state, vortex belt with the initial stage and vortex belt with the serious period [5-7].
The method of SVD is a powerful tool in signal processing and data analyzing, which is representing signal in time-frequency domain, it has been implemented in a variety of applications like the multiple pattern extraction [8], the signal enhancement of seismic data [9], the feature extraction method of non-stationary vibration [10], owing to the characteristics of singular value, the method of SVD is suitable for the noise processing of signal, for example, the electrocardiogram signal denoising [11], the noise reduction in dual microphone [12] and being a denoising tool for airborne time domain electromagnetic data [13].
The vibration signals are non-stationary random signal, aiming at such problems, this paper puts forward the vibration signal analysis method [14-16] which is based on singular value decomposition with an improved threshold used for noise reduction and Cascade Correlation neural network, this method is used to identify the hydraulic pressure pulsation of the draft tube, thus improving the running stability of the turbine.
2. Noise reduction based on singular value decomposition
Singular value decomposition has a good algebraic and geometric invariance, which has been widely applied for regularisation, noise reduction, signal processing and so on [17]. Any matrix whose numbers of rows and columns can be written as the product of a column orthogonal matrix , a diagonal matrix of singular values and the transpose of an orthogonal matrix are defined as follows:
where we define as the singular matrix of , and all of the diagonal elements of are the singular values which are as follows:
where is the rank of matrix .
The actual vibration signal with noise is one-dimensional , which should be segmented:
The larger singular values corresponding to denote actual signals, whereas the smaller singular values denote noise, so the smaller singular values need to be set to zero, then the adjusted singular value matrix be inversed by:
where is transformed into one-dimensional matrix , which is the real vibration signal without noise. For the noise reduction, the key point is how to choose a threshold from which the rest singular values will be set to zero. An improved method determining threshold is proposed, is the mutation value of singular values, which is correspondent with the maximum of :
where the singular value sequences are transformed to matrix, is the group number of singular value sequences, then the threshold may be determined by:
3. Cascade correlation neural network and pressure fluctuation analysis
3.1. Cascade correlation neural network
Cascade correlation is a supervised learning algorithm for artificial neural networks which was developed by Fahlman and Lebiere [18]. It starts with a minimal network consisting only of an input and an output layer, then by minimizing the overall error of a network; it adds step by step new hidden units to the hidden layer to create a multi-layer structure, the method learns much faster than the usual learning algorithms.
It mainly consists of two key ideas: firstly, the cascade architecture, in which hidden units are joined to the architecture every time and is not altered after they have been joined in. Secondly, the learning method would generate and then install the new hidden units. We would try to magnify the magnitude of the cascade correlation between the output and the remainder of the error we are trying to evaluate.
We start on the first cycle, a single new hidden unit is generated and a weight connection from each input unit is given [19, 20]. The learning should be continued only if the error value does not meet the specific requirement, so a candidate node hidden unit is added to the network, but its output is not connected to the network, at this time, the weights of the candidate node can be trained while all the other weights in the network are frozen. During the candidate node training the goal is to maximize the value of correlation between the output of the candidate node and network output error:
where is the candidate’s output for the sample , is the error at output node for the sample , and are the mean values of the outputs and output errors over the all patterns of the training sample, the gradient ascent algorithm is usually used to obtain the maximization.
The second cycle gives the output of the new hidden unit a weight connection for each output unit. The entire set of connections to those from all input and hidden units would be trained through minimizing the sum squared error equation:
where and are the network output for pattern and the expected output for this pattern respectively.
3.2. Feature extraction
Feature extraction is to analyze the basic data and get the characteristics of data, in this paper, the pressure pulsation signal is decomposed by wavelet, the appropriate frequency band signal is chosen, the root mean square value of each frequency band is the recognition parameter, and the band of the RMS value is:
where is the RMS value in node , is the discrete amplitude of reconstruction signal, is the number of data points to reconstruct the signal.
The flowchart of the CC neural network learning combined with singular value decomposition for the vibration signal of draft tube is given in Fig. 1.
4. Identification of pressure pulsation signal draft tube
4.1. Test procedure and measuring point layout
In order to get the hydraulic pressure fluctuation signal of the draft tube, the pressure pulsation test of the mixed flow turbine is carried on at turbine energy test stage in China institute of water resources and hydropower research, the main parameters of the model turbine: the wheel nominal diameter is 0.35 m, the blade number of the runner is 14, the height of the guide vane is 0.2 m, the distribution circle diameter of the guide vane is 1.18 m, the number of the fixed guide vane is 24, and the spiral angle is 350°.
Fig. 1The chart of vibration signal identification
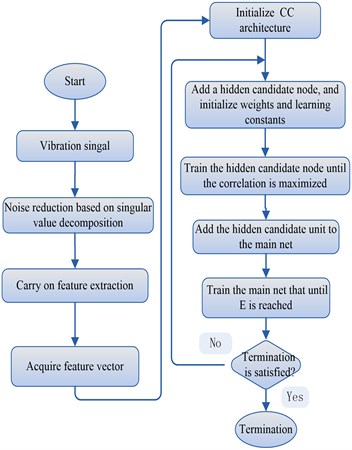
Fig. 2Measuring point layout
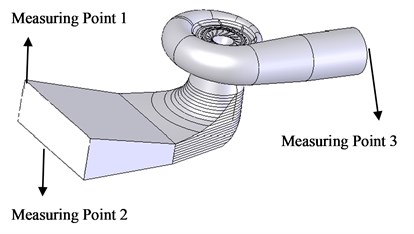
4.2. Data collection
Before the test, the pressure pulsation sensor is installed on the measuring point, the end face of the sensor must be flush with the port side of wall, after setting the calibration, the relationship between voltage and pressure is set up. In the experiment, the signals from the sensor are conveyed to the computer. The 69 signal data are obtained in each measuring point, the data length is 25600 from the collected vibration signals, the part data are as follows in Table 1.
Table 1The part nodes and the corresponding amplitude
Sample 1 (amplitude) | Sample 2 (amplitude) | |||||
node | CH0 | CH1 | CH2 | CH0 | CH1 | CH2 |
1 | 0.175 | –0.952 | –0.73 | 2.686 | 0.6 | –0.585 |
2 | –0.325 | –1.039 | –0.87 | 2.213 | 0.357 | –1.339 |
3 | –0.875 | –1.456 | –1.077 | 1.986 | 0.173 | –1.767 |
4 | –0.844 | –1.688 | –1.293 | 2.125 | 0.439 | –2.009 |
5 | –0.679 | –1.559 | –0.963 | 1.691 | 0.243 | –2.295 |
6 | –0.564 | –1.446 | –0.51 | 1.452 | 0.218 | –2.332 |
7 | –0.384 | –1.419 | –0.193 | 1.136 | 0.045 | –2.756 |
8 | –0.08 | –1.285 | 0.197 | 0.985 | 0.04 | –2.823 |
9 | –0.122 | –1.063 | 0.324 | 2.162 | 0.681 | –2.8 |
10 | 0.106 | –1.236 | –0.356 | 3.187 | 0.77 | –2.716 |
... | ... | ... | ... | ... | ... | ... |
4.3. Noise reduction and feature extraction
The noise reduction based on singular value decomposition is used to deal with the data, the analysis results are shown in the below figures, we can see from Fig. 3 that the noise of the original signal obtained has the bigger degree of inhibition, which is beneficial to the follow-up feature extraction. The collected signals in sample 1 and 2 are decomposed by the wavelet decomposition, the analysis results are shown in the below Fig. 4.
[2.8076, 1.5926, 0.7937, 0.3440, 0.0865, 0.0215],
4.5107, 1.1953, 0.5801, 0.2964, 0.0961, 0.0601].
Fig. 3a) The original waveform of vibration signal, b) the waveform after noise reduction
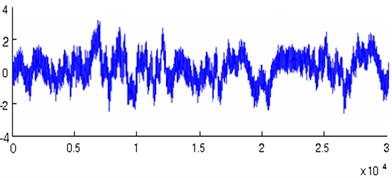
(a)
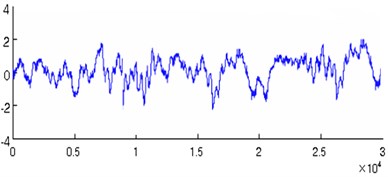
(b)
Fig. 4a) Low frequency and high frequency of 1-5 layers in sample 1, b) low frequency and high frequency of 1-5 layers in sample 2
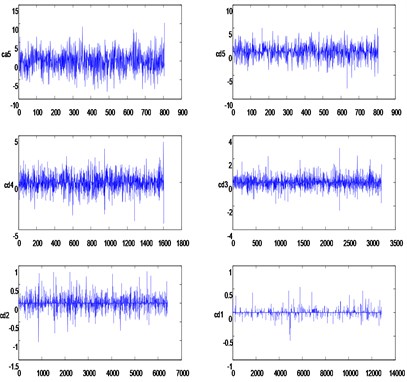
(a)
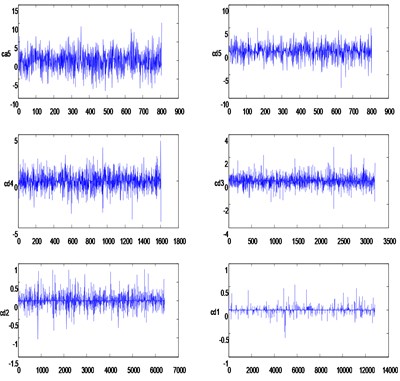
(b)
The signal information in each frequency band can be seen from above figures, the standard deviations of each frequency band for all samples are shown in Table 2.
Table 2Each frequency pressure pulsation standard deviation statistical data of taper section up stream
No. | Ca5 | Cd5 | Cd4 | Cd3 | Cd2 | Cd1 |
1 | 2.807 | 1.592 | 0.793 | 0.344 | 0.086 | 0.021 |
2 | 4.51 | 1.195 | 0.58 | 0.296 | 0.096 | 0.06 |
3 | 4.584 | 0.495 | 0.312 | 0.225 | 0.095 | 0.077 |
4 | 2.263 | 0.223 | 0.138 | 0.105 | 0.082 | 0.046 |
5 | 1.205 | 0.209 | 0.1 | 0.094 | 0.045 | 0.033 |
6 | 0.892 | 0.213 | 0.067 | 0.065 | 0.043 | 0.026 |
7 | 0.806 | 0.051 | 0.051 | 0.043 | 0.034 | 0.02 |
8 | 5.048 | 0.04 | 0.026 | 0.016 | 0.028 | 0.016 |
9 | 1.321 | 0.027 | 0.012 | 0.006 | 0.013 | 0.004 |
10 | 1.186 | 0.111 | 0.043 | 0.015 | 0.012 | 0.004 |
… | … | … | … | … | … | … |
69 | 1.5 | 0.27 | 0.359 | 0.335 | 0.192 | 0.136 |
4.4. The analysis of pressure pulsation based on cascade connection network
From the synthetic characteristic curve [21-23], we can get the pressure fluctuation value of corresponding samples, which are shown in Table 3. According to the pressure fluctuation value, the hydraulic pressure pulsation can be divided into three states including the normal state, the early vortex and the severe vortex. The corresponding value of the first state is between 1 % to 3 %, indicating that the pressure pulsation is lighter; the corresponding value of the second state is between 4 % to 5 %, indicating that the pressure fluctuation is bigger; the corresponding value of the third state is between 6 % to 8 %, indicating that the pressure pulsation is serious, the samples distributions are shown in Table 4.
Table 3Tail pipe pressure pulsation classification in modeling results
Category | 1 | 2 | 3 | 4 | 5 |
Pressure fluctuation value | 1 % | 2 % | 3 % | 4 % | 5 % |
Sample | 8, 10, 11, 12, 13, 23, 24, 25, 26, 27, 28, 37, 38, 39, 40, 41, 42, 52, 53, 54, 55, 56 | 6, 7, 9, 14, 15, 51, 67, 68, 69 | 4, 5, 21, 22, 23, 35, 36, 50, 66 | 1, 2, 3, 16, 17, 18, 20, 29, 30, 31, 33, 34, 48, 49 | 19, 32, 43, 44, 45, 46, 47, 64, 65 |
Table 4The category results of samples
No. | Category | Sample |
1 | First | 4, 5, 6, 7, 9, 10, 11, 12, 13, 21, 22, 23, 24, 25, 26, 27, 28, 35, 36, 37, 38, 39, 40, 41, 42, 50, 51, 52, 53, 54, 56, 66, 67, 68, 69 |
2 | Second | 1, 2, 3, 8, 14, 15, 16, 17, 18, 19, 20, 29, 30, 31, 32, 33, 34, 43, 47, 48, 49, 55, 64, 65 |
3 | Third | 44, 45, 46, 57, 58, 59, 60, 61, 62, 63 |
The 69 groups of feature vectors are as the input samples, the input node number of CC is six, and the output node number is three. After determining the number of the input and output, the adaptive learning based on the CC is applied to the model, the training results in 13 hidden neurons added to the actual network, finally the stable network model is 6-13-3 structure as shown in Fig. 5. Then the training the CC network is tested for accuracy and generalization using a testing set.
Fig. 5The network model based on CC
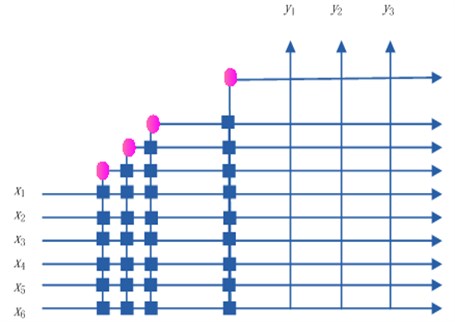
Six pressure pulsation points are taken from the comprehensive characteristic curve of the turbine as validation samples, and a comparison with BP neural network is made in order to evaluate the method properly. The BP network is trained using fast back-propagation method. Training parameters are set as follows: the learning rate is 0.02 and the momentum constant is 0.9. The weights and biases are initialized randomly. The BP network is trained with the same training samples, and the same test samples are used too in testing. The error is set as 0.001, 0.0003 and 0.0001 respectively. The results of the comparison between the two methods are shown in Table 5.
Table 5Comparison between BP and CC network
Method | CC | BP1 | BP2 | BP3 |
Error (SSE) | 0.0003 | 0.001 | 0.0003 | 0.0001 |
Training time | 12.6 s | 26.5 s | 36.5 s | 57.2 s |
Test accuracy | 99.71 % | 97.76 % | 98.15 % | 96.28 % |
Compared with BP network, the result in Table 5 shows that the most evident characteristics of the proposed method are its robustness and less training time. If the number of hidden units of BP network is appropriate, it can improve its performance by reducing the error, but it can be seen that when the error is drop down from 0.001 to 0.0003, the error is down too. But when the error is small enough, due to the over-fitting, one cannot improve the result by reducing the error anymore. The test accuracy achieved with CC is 99.71 % using 13 hidden units, CC network has been shown to be capable of good generalization when it is applied to the pressure fluctuation identification of draft tube, the experiment with different numbers of hidden units is not necessary and the training time is 12.6 seconds less than that with standard BP networks with different hidden units, exhibiting good classification accuracy and rapid convergence speed.
5. Conclusions
This paper has presented a method integrating noise reduction based on singular value decomposition with Cascade Correlation neural network to identify the pressure fluctuation signal of draft tube. In particular, we have developed an improved threshold method used for adjusting singular values. Compared with other methods, the experimental results shows that the method is effective in identifying states of the pressure fluctuation in the draft tube. On the basis of further research, this method can be used to guide the stable operation of the turbine in the hydropower station.
References
-
F. Shi, H. Tsukamoto Numerical study of pressure fluctuations caused by impeller-diffuser interaction in a diffuser pump stage. Transactions of the ASME, Vol. 123, Issue 3, 2001, p. 466-474.
-
Sun Yuekun, Liu Shuhong, Liu Jintao, Wu Yulin, Zuo Zhigang Experiment study of pressure fluctuation of a pump-turbine in starting. Journal of Engineering Thermophysics, Vol. 33, Issue 8, 2012, p. 1330-1333.
-
Liu Jintao, Liu Shuhong, Sun Yuekun Prediction of pressure fluctuation of a pump turbine at no load opening. Journal of Engineering Thermophysics, Vol. 33, Issue 3, 2012, p. 411-414.
-
Wang Junxing, Du Shaolei, Chen Liqi Model test research on fluctuation pressure on emptying tunnel of Kajiwa hydropower station. Engineering Journal of Wuhan University, Vol. 45, Issue 4, 2012, p. 436-441.
-
Wang Baoluo, Zheng Yuan Study on model test of vibration of draft tube of large size Francis turbine-generating unit. Water Power, Vol. 34, Issue 3, 2008, p. 83-87.
-
Xiao Ruofu, Sun Hui, Liu Weichao, Wang Fujun Analysis of characteristics and its pressure pulsation of pump-turbine under pre-opening guide vanes. Journal of Mechanical Engineering, Vol. 48, Issue 8, 2012, p. 174-179.
-
Li Chenjun Test and analysis on the pressure pulse of pumped storage unit. Journal of Hydropower, Vol. 5, 2001, p. 53-56.
-
Kanjilal P. P., Palit S. On multiple pattern extraction using singular value decomposition. IEEE Transactions on Signal Processing, Vol. 43, Issue 6, 1995, p. 1536-l540.
-
Bekara M., Baan M. V. Local singular value decomposition for signal enhancement of seismic data. Geophysics, Vol. 72, Issue 2, 2007, p. 59-65.
-
Zhao L., Cheng F. B., Huang D. R. The feature extraction method of non-stationary vibration signal based on svd gauss wavelet. Modern Scientific Instruments, Issue 1, 2012, p. 27-30.
-
Mojtaba Bandarabadi, Mohammad Reza Karami-Mollaei, Amard Afzalian, Jamal Ghasemi ECG denoising using singular value decomposition. Australian Journal of Basic and Applied Sciences, Vol. 4, Issue 7, 2010, p. 2109-2113.
-
Maj J. B., Royackers L., Moonen M., Wouters J. SVD-based optimal filtering for noise reduction in dual microphone hearing aids: a real time implementation and perceptual evaluation. IEEE Transactions on Biomedical Engineering, Vol. 52, Issue 9, 2005, p. 1563-1573.
-
Martelet G., Deparis J., Perrin J., Chen Y. Singular value decomposition as a denoising tool for airborne time domain electromagnetic data. Journal of Applied Geophysics, Vol. 75, Issue 2, 2011, p. 264-276.
-
Zhang Fei, Gao Zhongxin, Pan Luoping, Ge Xinfeng Study on pressure fluctuation in Francis turbine draft tubes during partial load. Journal of Hydraulic Engineering, Vol. 42, Issue 10, 2011, p. 1234-1238.
-
Yin Junlian, Liu Jintao, Wang Leqin Prediction of pressure fluctuations of pump turbine under off design condition in pump mode. Journal of Engineering Thermophysics, Vol. 32, Issue 7, 2011, p. 1141-1144.
-
Liu Yang, Yin Chongqing Wavelet analysis on non-stationary vibration signal of hydraulic turbines. Yangtze River, Vol. 43, Issue 2, 2012, p. 101-104.
-
A. J. Van Der Veen, E. F. Deprettere, A. Lee Swindlehurst Subspace-based signal analysis using singular value decomposition. Proceedings of the IEEE, Vol. 81, 1993, p. 1277-1308.
-
Fahlman S. C., Lebiere C. The cascade correlation learning architecture. Advance in Neural Information Processing Systems, Vol. 2, 1990, p. 524-530.
-
Mitchell A. Potter A genetic cascade-correlation learning algorithm. Proceedings of Combinations of Genetic Algorithms and Neural, Networks Maryland, 1992.
-
Ilona Magdisyuk Using the cascade-correlation algorithm to evaluate investment projects. Informatica, Vol. 12, Issue 2, 2001, p. 101-108.
-
Zhao Linming, Chu Qinghe, Dai Qiuping, Wang Liying Analysis of pressure fluctuation in draft tube based on wavelet analysis and artificial neural networks. Journal of Hydraulic Engineering, Vol. 42, Issue 9, 2011, p. 1075-1080.
-
Zhang Siqing, Hu Xiucheng, Zhang Lixiang Study on pressure fluctuations of Francis turbine with long and short blades based on CFD. Journal of Hydroelectric Engineering, Vol. 31, Issue 2, 2012, p. 216-221.
-
Zhang Yuning, Liu Shuhong, Wu Yulin Detailed simulation and analysis of pressure fluctuation in Francis turbine. Journal of Hydroelectric Engineering, Vol. 28, Issue 1, 2009, p. 183-186.
About this article
This work is supported by the Science and Technology Research Project of University of Hebei Province No. Y2012016, the Science Research Foundation of Hebei Education Department of China No. 2009422, and the Natural Science Foundation of Hebei Province of China No. E2010001026.