Abstract
In order to meet the requirement of the movement flexibility of crawling robot, a kind of crawling robot imitating spider gait manufactured from polylactic acid (PLA)material was proposed. The motion mechanism of the robot is analyzed by gait decomposition method. Based on the Arduino platform, the control system of bionic spider gait crawling robot is developed. The mobile App software and Bluetooth module are used to realize the wireless control of the robot and the motion performance test. The experimental results show that when the steering angle is 30°, the average moving speed of the spider gait crawling robot is 4.5 mm/s. The movement speed of each leg of the crawling robot increases non-linearly with the increase of steering gear angle. And with the stride time changes, the crawling speed of the robot changes steadily. Besides, the turning angle of the robot increases with the increase of the steering angle of the steering gear. The results lay a foundation for improving the overall performance of spider gait mimicking crawling robot.
1. Introduction
With the development of science and technology, robots are widely used in production and life. Robots can replace people to complete some dangerous and difficult tasks, such as underwater detection, outdoor inspection, laser welding and so on [1-3], and greatly improving production efficiency. Bionic robot is a hot topic in the field of robotics. The so-called bionic robot is a robot that imitates the body structure, movement mode and behavior characteristics of animals in nature, and can carry out biological work through these systems. For bionic robots, scholars have carried out a lot of research.
Holley et al. [4] developed a self-stabilized swimming bionic robot, which can complete pitching, depth and rolling without external intervention. Kashi et al. [5] observed the liquid flow around the flippers simulated by the sea lion robot using particle imaging velodrometer. The study found that the flapping motion of the sea lion robot brought a large amount of fluid momentum, which developed into a spindle vortex and had an important impact on downstream momentum. Inspired by the passive grasping mechanism of caterpillar, Rozen-Levy et al. [6] proposed a flexible branch crawling robot, which can realize horizontal crawling, vertical crawling and climbing along branches, demonstrating the key advantages of soft robots over traditional rigid robots. Cizek et al. [7] developed a four-DOF six-legged walking robot with one leg and controlled its motion in rough terrain. Besides, Gamus et al. [8] designed a three-link inchworm crawling robot, simulated the passive friction contact in the hybrid dynamic crawling of the robot, and tested the good performance of the robot through experiments. Han et al. [9] manipulated the miniature graphene spider with light to make it crawl. The principle is to modify the thermal conductivity of the material by using the method of laser reduction of graphene oxide, so as to change the thermal conductivity of key parts. In order to improve the adaptability of the hexapod robot to rugged terrain, He et al. [10] conducted a comparative study on the discrete gait control strategy and phase difference control strategy of earthworm-like mobile robot. What’s more, Wang et al. [11] designed a new inchworm microrobot, which used shape memory alloy spring to imitate inchworm movement. When the robot was heated for 2.7 s, the crawling speed of the robot could reach 4.1 mm/s.
Through the analysis of the research status, it can be seen that the bionic robot realizes some special functions by imitating the form or action of nature. As a tiny insect, spider can move quickly and flexibly. It is the focus of this paper to design a spider crawling robot by imitating spider movement. Compared with the existing achievements, the spiderlike robot designed in this paper adopts Arduino to accurately control the moving gait, and the crawling speed of the robot can be adjusted by altering the gait time and steering angle.
In this paper, a micro quadruped crawling robot imitating spider gait is designed. Based on Arduino platform, the control system is designed to realize the motion gait control of the spider gait mimicking robot. Compared with the traditional bionic crawling robot, the crawling robot designed in this paper can realize low speed, flexible and high precision gait movement. This paper presents the design process of the robot, analyzes the gait of the robot, and tests the motion performance of the crawling robot through experiments.
2. Design
The structure of the spider-gait mimicking crawling robot is shown in Fig. 1. The robot is composed of four legs and Arduino control system. Each leg is composed of a forward mechanism and a lifting mechanism, which are respectively driven by a steering gear.
In order to ensure the stability of the center of gravity of the robot, the mechanism of the legs should follow a line trajectory relative to the body during the robot’s movement, so that the center of gravity of the body will not swing up and down during the movement. The robot moves with at least one leg touching the ground, alternately supporting the body. Therefore, the legs must have the rigidity and support of the fuselage in order to walk properly.
The bionic spider crawling robot designed in this paper takes the spider in nature as the bionic object, and simplifies each leg into two joints to realize the spider robot leg forward, backward and rise, fall and other actions.
Fig. 1Structure of the proposed micro crawling robot

a) Three-dimensional diagram
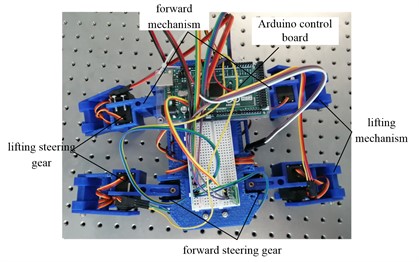
b) Prototype
In the bionic spider gait crawling robot designed in this paper, each time one leg is raised and stepped forward, the other leg is used as the support leg, but each leg may move as the first leg, or the last leg. According to the probability theory, there are many possibilities. Considering the motion characteristics of spiders and the stability of the robot during working, the motion scheme with high stability is selected here. Each leg movement order is: right frontleg – left hind leg – left front leg – right hind leg – right front leg. The gait movement of the robot is shown in Fig. 2, and the movement process is as follows:
(1) In the initial state, each leg does not move forward or upwards. When the robot starts to move, the right front leg is raised by 30° (Fig. 2(b)), and then the right front leg moves forward by 30° (Fig. 2(c)). When the right front leg falls, the left rear leg is raised by 30° (Fig. 2(d)).
(2) The left hind leg moves to the next step, advancing 30° (Fig. 2(e)), then falling (Fig. 2(f)), the left hind leg moves forward one step.
(3) The next step is the left front leg movement, the left front leg raises 30° (Fig. 2(g)), then the left front leg forward 30° (Fig. 2(h)), after the left front leg drops, the right hind foot raises 30° (Fig. 2(i)), so the left front leg completes a step forward action.
(4) In the next step, the right hind leg moves forward 30° (Fig. 2(j)), then the right hind leg falls, and the right hind leg moves forward further. So far, each leg of the robot completes the forward step.
Fig. 2Gait movement of the crawling robot
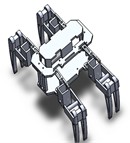
a) Initial state
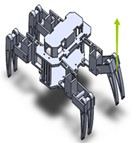
b) Right front leg lifting
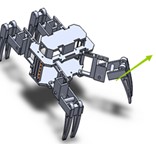
c) Right front leg forward
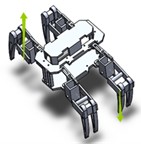
d) Left rear leg lifting
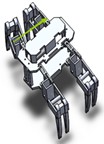
e) Left hind leg forward
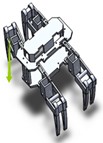
f) Left hind leg falling
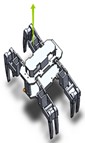
g) Left front leg lifting
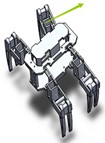
h) Left front leg forward
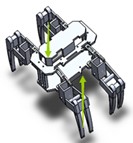
i) Right hind foot lifting
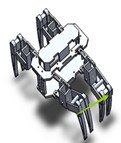
j) Right hind foot forward
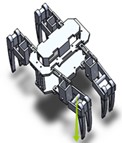
k) Right hind foot falling
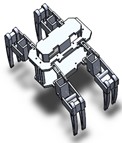
l) Initial state
Each leg of the spider-gait mimicking crawling robot has two degrees of freedom, which are formed by connecting the steering gear with the forward mechanism and the lifting mechanism. In this design, when the leg is in contact with the ground, the angle of the contact between the forward mechanism and the lifting mechanism is 180°, and the swing angle is 30°. Thus, when the leg is raised, the lifting mechanism lifts up by an angle of 30° and the angle between it and the forward mechanism becomes 150°.
Force analysis is carried out on the legs of the bionic spider gait crawling robot, as shown in Fig. 3, where G1~G3 are the gravity of each part, M is the torque to be overcome during lifting of the lifting mechanism, and P is the reverse support force received by the legs.
According to Fig. 3, the generalized balance equation of the feet of the bionic spider gait crawling robot is:
where, l2 and l3 are the transverse and longitudinal dimensions of the lifting mechanism respectively; θ2 and θ3 are the angle between the lifting mechanism and the horizontal plane and the angle between the transverse and longitudinal parts of the lifting mechanism respectively.
When θ2= 180° and θ3= 120°, the torque required for lifting is the maximum, and the maximum value is:
Fig. 3Gait movement of the crawling robot
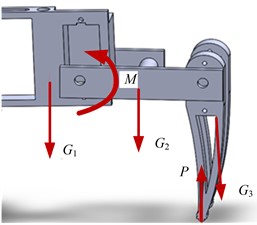
3. Experimental testing and analysis
Experiments are carried out to test and verify the motion performance of the spider gait robot designed in this paper. Fig. 4 shows the test system diagram of the crawling robot. The crawling robot adopts DC power supply. The motion control of the robot is realized through the mobile App software and Bluetooth module, and the crawling speed of the robot is calculated by taking the position of the robot at different times with the high-speed camera.
Fig. 4Experimental test system of crawling robot
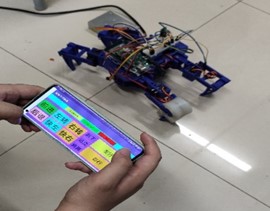
a) Experimental testing
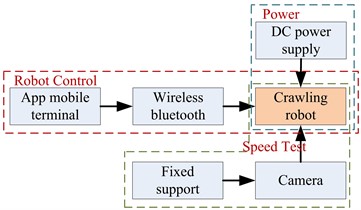
b) Experimental scheme
Fig. 5(a) shows the crawling speed of each leg of the robot at different steering angles, and Fig. 5(b) shows the maximum speed difference between each leg at different steering angles. From Figs. 5 and 6, it can be seen that:
(1) When the steering gear angle is different, the crawling speed of each leg of the robot is different, and with the increase of the steering gear angle, the crawling speed of each leg of the robot increases nonlinearly.
(2) When the steering gear angle is constant, the crawling speed of each leg is similar, and the maximum speed difference is relatively stable, so the crawling robot runs smoothly when working.
Fig. 5Crawling speed of the robot
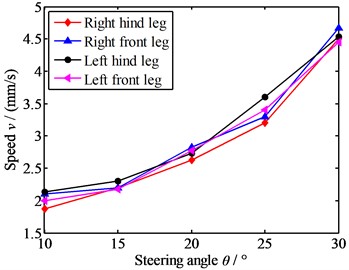
a) Crawling speed of each leg
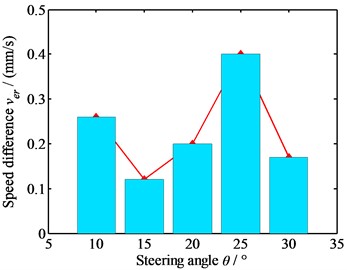
b) Maximum speed difference
Fig. 6 shows the average crawling speed of robots at different steering angles. It can be seen from the figure:
The average crawling speed of the robot increases with the increase of the steering angle, and the increasing trend of the crawling speed is consistent with the trend of each leg. When the steering angle is 30°, the average moving speed of the spiderlike crawling robot is 4.5 mm/s.
Fig. 6Average crawling speed of the robot at different steering gear angles
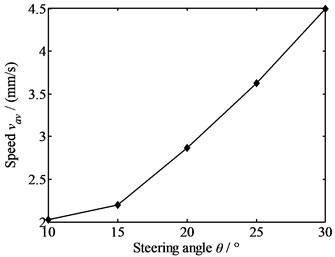
The turning angle of the crawling robot has an important influence on its turning efficiency. The variation of turning angle with the steering angle of the steering gear is studied experimentally, as shown in Fig. 7. As can be seen from the figure: the turning angle of the robot increases with the increase of the steering angle, and there is a certain deviation in the turning angle between left and right. When the steering gear angle is less than 15°, the corresponding turning angle of right turn is greater than that of left turn, while when the steering gear angle is greater than 15°, the turning angle of left turn is larger.
Fig. 7The turning angle varies with the steering gear angle
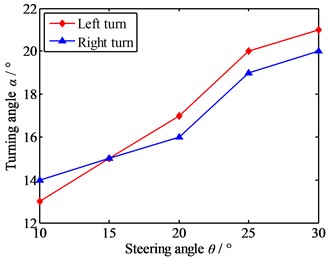
Fig. 8The average speed of the robot varies with stride time
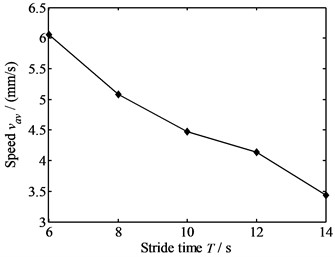
Fig. 8 shows the average moving speed of crawling robot changing with stride time. It can be seen from the figure: with the increase of stride time, the average moving speed of the robot decreases ap-proximately linearly, indicating that the moving speed of the crawling robot changes steadily with the change of stride length.
4. Conclusions
In this paper, a micro crawling robot that mimics spider gait is designed, and the working principle and design process is analyzed. The structure of the control system of spider - like crawling robot is given, and the performance of the robot is tested experimentally. The results show that:
1) With the increase of steering angle, the crawling speed of each leg of the robot in-creases nonlinearly, and when the steering angle is constant, the speed of each leg is similar;
2) The turning angle of the robot increases with the increase of the steering angle of the steering gear, and there is a certain deviation of the turning angle between the left and right turns;
3) When the stride time changes, the robot speed changes steadily.
The results lay a theoretical and experimental foundation for improving the motion performance of crawling robot imitating spider gait.
References
-
S. J. Cho, F. M. Zhang, and C. R. Edwards, “Learning and detecting abnormal speed of marine robots,” International Journal of Advanced Robotic Systems, Vol. 18, p. 17298, 2021.
-
F. Rocha et al., “ROSI: a robotic system for harsh outdoor industrial inspection – system design and applications,” Journal of Intelligent and Robotic Systems, Vol. 103, No. 2, pp. 1–22, Oct. 2021, https://doi.org/10.1007/s10846-021-01459-2
-
Q. Wang, Y. Cheng, W. Jiao, M. T. Johnson, and Y. Zhang, “Virtual reality human-robot collaborative welding: A case study of weaving gas tungsten arc welding,” Journal of Manufacturing Processes, Vol. 48, pp. 210–217, Dec. 2019, https://doi.org/10.1016/j.jmapro.2019.10.016
-
M. T. Holley, N. Nagarajan, C. Danielson, P. Zorlutuna, and K. Park, “Cardiac muscle-cell based actuator and self-stabilizing biorobot – part 1,” Journal of Visualized Experiments, Vol. 125, No. 125, p. 55642, Jul. 2017, https://doi.org/10.3791/55642
-
E. Kashi, A. A. Kulkarni, G. Perrotta, and M. C. Leftwich, “Flowfields produced by a robotic sea lion foreflipper starting from rest,” Bioinspiration and Biomimetics, Vol. 15, No. 3, p. 035002, Mar. 2020, https://doi.org/10.1088/1748-3190/ab6a62
-
S. Rozen-Levy, W. Messner, and B. A. Trimmer, “The design and development of Branch Bot,” The International Journal of Robotics Research, Vol. 40, No. 1, pp. 24–36, Jan. 2021, https://doi.org/10.1177/0278364919846358
-
P. Cizek, M. Zoula, and J. Faigl, “Design, construction, and rough-terrain locomotion control of novel hexapod walking robot with four degrees of freedom per leg,” IEEE Access, Vol. 9, pp. 17866–17881, 2021.
-
B. Gamus, A. Gat, and Y. Or, “Dynamic inchworm crawling: performance analysis and optimization of a three-link robot,” IEEE Robotics and Automation Letters, Vol. 6, pp. 111–118, 2021.
-
B. Han, Y.-L. Zhang, and H.-B. Sun, “Remote light control of graphene spider robot,” Chinese Science Bulletin, Vol. 65, No. 36, pp. 4152–4153, Dec. 2020, https://doi.org/10.1360/tb-2020-0755
-
Z. H. He, H. B. Fang, and J. Xu, “Comparison of the discrete gait control and phase-difference control for earthworm-like locomotion robots,” Robot, Vol. 42, pp. 697–708, 2020.
-
W. H. Wang and J. F. Hu, “Design and experiment of bionic – inchworm micro – robot,” Transducer and Microsystem Technologies, Vol. 39, pp. 90–93, 2020.
About this article
This research was funded by National Natural Science Foundation of China (grant No. 51905228), Qing Lan Project of Jiangsu Province (1024902201).
The datasets generated during and/or analyzed during the current study are available from the corresponding author on reasonable request.
The authors declare that they have no conflict of interest.