Abstract
The construction technology of traffic marking has a significant influence on its retroreflective performance. To study the effect of different construction processes on the service performance of traffic markings, two-component spraying paint and two different glass beads were chosen to produce traffic markings that were prepared by single-layer or double-layer spraying, as well as once and twice surface spraying of glass beads. The effects of glass bead coating, spraying times of glass beads and paints on the surface morphology and retroreflective performance of traffic markings were investigated, as well as the variation of the retroreflective coefficient (RC) at the early and middle stages. The results indicated that double-layer spraying was more effective than single spraying. The coated glass beads would decrease the initial RC of the markings, but improved their long-term service performance. The TP-21C has the finest overall retroreflective performance and the lower construction complexity.
1. Introduction
Traffic marking plays an important role in exerting road function, preventing and reducing the occurrence of accidents. Even the nighttime traffic volume accounts for only approximately a quarter of total traffic volume, nighttime traffic accident fatalities accounts for half of all traffic accident fatalities, according to the U.S. traffic safety statistics [1]. Therefore, improving the performance of traffic markings is conducive to improving traffic safety [2-3]. However, the performance of existing traffic markings varies greatly, and the initial reflection retroreflective coefficient (RC) ranges from 100 mcd·lx-1·m-2 to more than 500 mcd·lx-1·m-2 [4]. In addition to materials, the biggest factor affecting the performance of traffic markings is its construction technology [5]. Although the use of higher-quality marking paint and higher refractive index glass beads might obtain relatively higher RC, in some cases, even if the same material was used, the difference of RC was large, and even the use of high-quality materials might lead to lower RC [6-8].
The construction technology of traffic markings mainly consists of spraying and scraping, and certain structural markings have a dumping type construction. In general, when the paint is scraped or sprayed onto the road, a layer of glass beads is then spread on the surface, waiting for the glass beads to be infiltrated by the paint and bonded tightly with the paint matrix as the paint cures [9-10]. Some of the glass beads embedded in the coating matrix play the role of retro-reflecting light, and some of them are also treated with silane coupling agent in order to enhance the adhesion between the glass beads and the coating [11-14].
According to previous studies, the retroreflective coefficient of traffic marking is highly correlated with the degree of embedding of glass beads [4]. Too much or too little embedding of glass beads will cause the retroreflective performance to decrease, and some studies point out that the optimal embedding depth of glass beads should be between 1/2 and 2/3 [4-5]. On the one hand, if the glass beads are embedded too shallow, it is difficult to retain on the surface of the traffic markings, so its practical value is low. On the other hand, the light is mostly projected from the glass beads and will not form retroreflection. Many practical tests support the above conclusion that the RC of markings with nearly half of the embedding degree is significantly higher than that of glass beads embedded too deep or too shallow. However, these studies have not given how to properly control the embedding depth of glass beads in the markings. In the laboratory, researchers often use artificial or some mechanical auxiliary spread glass beads, but it is difficult to accurately control the degree of embedding [4]. The standard procedure is to produce many experimental plates from which to pick the necessary specimens. When it comes to engineering, it is more challenging to ensure a wide variety of building quality that satisfies standards. Numerous projects cannot be managed without the expertise of construction experts. Therefore, the real performance of traffic markings is largely determined by the professional abilities of construction staff.
In summary, construction technology should be explored in order to improve the service performance of traffic markings and maximize the utilization of marking materials. Consequently, this paper investigated the impact of two-component traffic marking spraying method, spraying thickness, and glass bead type on the performance of traffic marking and recommended the most suitable construction technology.
2. Materials and methods
2.1. Materials
In this experiment, two-component spraying traffic marking paint was selected and the performance parameters are shown in Table 1. The coated and uncoated glass beads with refractive index of 1.5 were utilized for surface spraying. The sieving curve is shown in Fig. 1, and glass bead A is coated and glass bead B is uncoated. Two-component self-propelled sprayers were used for spraying, and benzoyl peroxide (BPO) was used as curing agent.
Table 1Performance parameters of the two-component spraying traffic marking paint
Properties | Requirements | Performance parameter |
Coverage rates | ≥ 95 % | 97 % |
Density | 1.5≤ρ≤2 (g/cm3) | 1.8 (g/cm3) |
Luminance factor | ≥ 0.80 | 0.90 |
Gel time | ≥ 10 (min) | 15 (min) |
Fig. 1Sieving curve of glass beads; glass bead A is coated and glass bead B is uncoated
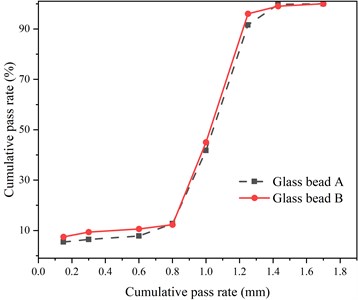
2.2. Experimental design
In this study, a sprayer was used once or twice to obtain a marking thickness of about 0.6 mm or 1.2 mm respectively. For the traffic marking with thickness of 1.2 mm, after the first spraying, it is divided into spraying beads and not spraying glass beads. The first spraying amount was 200 g/m2, and the second were both. Each group of experiments were conducted using both coated and uncoated glass beads. For the traffic marking with thickness of 0.6mm, after the spraying, the glass beads of 500 g/m2 were then sprayed on the traffic markings. The experimental design is shown in Table 2. The code TP-21C means that the paint was sprayed twice and the coated glass beads were sprayed once.
When the glass beads are spread, the height of the glass beads outlet and the road surface is adjusted to 20 cm, the spraying machine travel rate is 60 m/min, and the length of a line is 10 m.
Table 2Experimental design
No. | Coating thickness / mm | Spay times of glass beads | Type of glass beads |
TP-21C | 1.2 | 1 | Coated |
TP-21N | 1.2 | 1 | Not coated |
TP-22C | 1.2 | 2 | Coated |
TP-22N | 1.2 | 2 | Not coated |
TP-11C | 0.6 | 1 | Coated |
TP-11N | 0.6 | 1 | Not coated |
2.3. Performance test
Referring to “Specification and test method for road traffic markings” (GB/T 16311-2009), the RCs and thickness of the above traffic markings were tested respectively. Five points were randomly selected every ten meters for measurement, and the average of the measured values was used as the test results.
3. Results and discussion
3.1. The RC and thickness of the traffic markings
The RC and thickness of the six test markings were measured and shown in Table 3.
Table 3The measured RCs and thickness of the six groups of test sections
No. | Retroreflective coefficient (mcd·lx-1·m-2) | Average film thickness (mm) | ||||
1 | 2 | 3 | 4 | 5 | ||
TP-21N | 453 | 410 | 390 | 462 | 440 | 1.18 |
TP-21C | 401 | 415 | 396 | 390 | 362 | 1.20 |
TP-22N | 440 | 360 | 402 | 330 | 345 | 1.25 |
TP-22C | 412 | 390 | 386 | 340 | 332 | 1.30 |
TP-11N | 380 | 400 | 361 | 422 | 350 | 0.68 |
TP-11C | 393 | 350 | 398 | 356 | 404 | 0.63 |
The interval diagram of the test data is shown in Fig. 2. It can be seen from the figure that TP-21C, that is, the marking with double sprayed layer of paint and only once uncoated glass beads, has the highest RC. The marking with double sprayed layer of paint and twice sprayed coated glass beads (TP-22C) has the lowest RC.
Comparing the actual photos of single spraying and double spraying (Fig. 3), it can be seen that the single spraying layer is thin and the spraying uniformity is poor due to the structural depth of the road surface, and some glass beads float on the surface of the thinner coating aggregate. For double-layer traffic markings, when the glass beads are not sprayed on the first layer, the filling effect of the coating increased the smoothness of the surface during the second spraying and achieve a better glass bead distribution effect. When the glass beads were sprayed on the first layer, embedded glass beads caused uneven surface of the paint, so that the distribution uniformity of spraying paint and glass beads was poor. Therefore, it can be seen from Fig. 2 and Fig. 3 that the RC distribution interval of TP-22C and TP-22N traffic markings is large, and the RC is quite different, up to mcd·lx-1·m-2. The dispersion degree of TP-11C and TP-11N inverse reflection coefficient distribution is less than that of the above two groups. TP-21C and TP-21N have the lowest dispersion degree, and the distribution of coated glass beads is more concentrated.
Fig. 2Distribution of the inverse reflection coefficient of the traffic marking
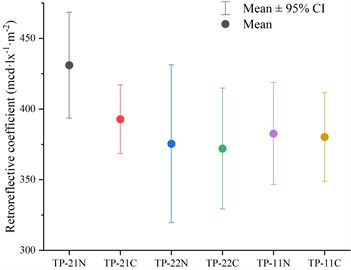
Fig. 3Distribution of glass beads on test road
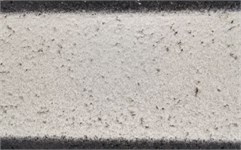
a) TP-21N
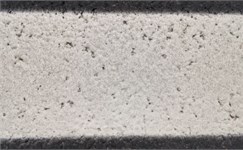
b) TP-21C
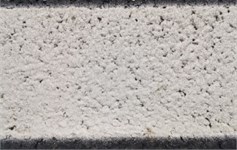
c) TP-22N
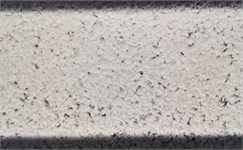
d) TP-22C
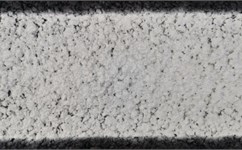
e) TP-11N
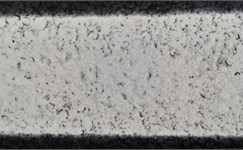
f) TP-11C
3.2. RC variation of traffic markings during service
As is shown in Fig. 4, the RC of the traffic markings on the test section was measured for 3 months and 10 months.
It can be seen from Fig. 4 that with the increased serving time of traffic marking, the RC gradually decreased, and the decline rate of traffic markings with different construction methods was significantly different. Within 3 months, the RCs of TP-21N and TP-11N decreased the fastest, followed by TP-22N, TP-21C and TP-11C, and the RC of TP-22C decreased the slowest. The shedding of uncoated glass beads and coated glass beads was shown in Fig. 5. It can be found that the RC of the uncoated glass beads decreased faster due to its poor adhesion to the painting and were more likely to fall off or peel off. The retroreflective ability of the traffic markings was mainly provided by glass beads, so that the RC of the markings was reduced when the glass beads fell off.
When the serving time reaches 10 months, the RC of traffic markings decreased to 200-300 mcd·lx-1·m-2, among which TP-21 N had the fastest decline rate. The decline rate of TP-11N and TP-11C was similar to TP-21N but the absolute value of the RC was lower. As the single spray painting was thin, when the marking was often subject to vehicle rolling, coating wear was more serious, thus the coat of glass beads had little impact on the shedding of glass beads.
Fig. 4RC of traffic markings for 3 and 10 months
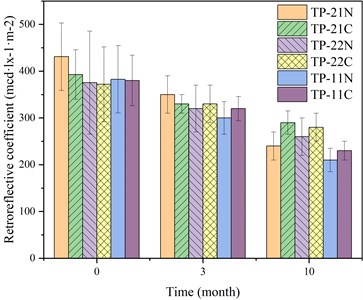
Fig. 5The shedding of uncoated glass beads and coated glass beads
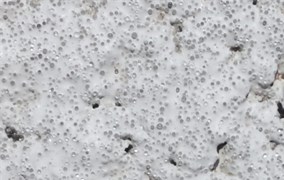
a) The shedding of uncoated glass beads
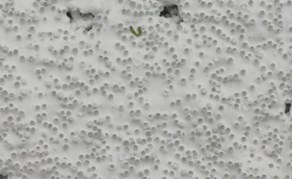
b) The shedding of coated glass beads
4. Analysis of influencing factors
4.1. Influence of construction technology on the RC of traffic markings
As can be seen from the data in Table 3, the average film thickness of a single spray traffic marking was about 0.65 mm which was half of the double layer markings, and only 40 % to 50 % of some larger glass beads were embedded in the markings. Therefore, the glass beads were easy to fall off under the action of external force. With the wear of the markings, the glass beads fell off more and more, and the embedded glass beads also fell off. The number of the retroreflective unit of the marking line decreased, so the RC decreased rapidly.
Fig. 6Microscopic picture uncoated glass beads and coated glass beads
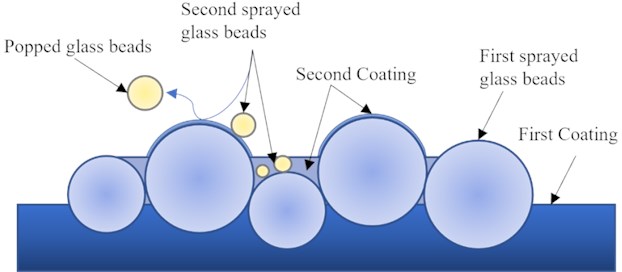
For the double-layer sprayed markings, spreading glass beads during the first spraying would cause the initial RC to decrease. The second layer got uneven distribution of paint due to the first spread glass beads forming a rough surface. Thus, some paint converged at low-lying areas, and glass beads were completely embedded in the area. The liquid film of some convex parts was thin, and the glass beads were not embedded deep enough or bounced by the bottom glass beads, so that they were not able to be embedded in the painting. The process is shown in Fig. 6.
In this instance, the embedding degree of glass beads was inconsistent, and the embedding degree of some secondary-sprayed glass beads was excessive, resulting in a poor RC for the marking. The reason behind this is that the refractive index of the glass beads and the deflection angle must be compatible for the glass beads to produce retroreflective light. The refractive index of glass beads is more than √2, satisfying the retroreflection criterion. When the glass beads were implanted too deeply, however, the incident light was refracted within the glass beads and blocked by the painting matrix, which failed to satisfy the deflection angle relationship and hence the RC was extremely low.
When the coating was sprayed for the first time without spraying glass beads, the paint filled the uneven portion of the road surface. Thus, the glass beads sprayed on the second layer were more equally dispersed. From the RCs change of TP-21C and TP-21N, it was evident that the coefficient dropped gradually.
4.2. Influence of glass beads coating on the RC of traffic markings
Comparing the retroreflective coefficient of the traffic markings between coated glass beads and non-coated glass beads reveals that the coating of glass beads will decrease the initial retroreflective coefficient of the marking line. For long-term performance, however, coated glass beads can be advantageous. Coated glass beads are more tightly mixed with marking paint and less likely to detach [14]. The 3-month and 10-month statistics for the RCs further prove this argument. The three sets of markings created with coated glass beads are greater than their counterparts created with uncoated glass beads.
5. Conclusions
1) The RC of traffic marking with two layers of paint and one spray of glass beads was relatively higher than that of the rest markings. Long-term retro-reflective properties of single-layer painted markers were difficult to maintain due to wear and tear.
2) The double-layer sprayed line was superior to the single-layer sprayed line because the glass beads were less likely to slip off with the increasement of its service life. Some glass beads buried in the double-layer sprayed markings may continue to play a role during the middle and late stages.
3) The initial RC of coated glass beads was slightly lower than that of uncoated glass beads. However, its long-term retroreflective performance was better than that of uncoated glass beads due to its closer combination with the marking paint. In summary, TP-21C had better retroreflective performance, and the complexity of the construction process was lower than TP-22C and TP-22N.
References
-
B. A. Bektas, K. Gkritza, and O. Smadi, “Pavement Marking Retroreflectivity and Crash Frequency: Segmentation, Line Type, and Imputation Effects,” Journal of Transportation Engineering, Vol. 142, No. 8, p. 04016030, Aug. 2016, https://doi.org/10.1061/(asce)te.1943-5436.0000863
-
T. E. Burghardt, A. Pashkevich, and H. Mosböck, “Yellow pedestrian crossings: from innovative technology for glass beads to a new retroreflectivity regulation,” Case Studies on Transport Policy, Vol. 7, No. 4, pp. 862–870, Dec. 2019, https://doi.org/10.1016/j.cstp.2019.07.007
-
S. M. Mirabedini, F. Zareanshahraki, and V. Mannari, “Enhancing thermoplastic road-marking paints performance using sustainable rosin ester,” Progress in Organic Coatings, Vol. 139, p. 105454, Feb. 2020, https://doi.org/10.1016/j.porgcoat.2019.105454
-
D. Babić, T. E. Burghardt, and P. Prusa, “Analysis of characteristics and application of waterborne road marking paint,” in Second International Conference on Traffic and Transport Engineering (ICTTE), pp. 265–274, 2014.
-
O. Smadi, N. Hawkins, B. Aldemir-Bektas, P. Carlson, A. Pike, and C. Davies, “Recommended Laboratory Test for Predicting the Initial Retroreflectivity of Pavement Markings from Glass Bead Quality,” Transportation Research Record: Journal of the Transportation Research Board, Vol. 2440, No. 1, pp. 94–102, Jan. 2014, https://doi.org/10.3141/2440-12
-
T. V. Dormidontova and A. V. Filatova, “Research of influence of quality of materials on a road marking of highways,” Procedia Engineering, Vol. 153, pp. 933–937, 2016, https://doi.org/10.1016/j.proeng.2016.08.256
-
E. Hadizadeh, S. Pazokifard, S. M. Mirabedini, and H. Ashrafian, “Optimizing practical properties of MMA-based cold plastic road marking paints using mixture experimental design,” Progress in Organic Coatings, Vol. 147, p. 105784, Oct. 2020, https://doi.org/10.1016/j.porgcoat.2020.105784
-
J. Nance and T. D. Sparks, “From streetlights to phosphors: A review on the visibility of roadway markings,” Progress in Organic Coatings, Vol. 148, p. 105749, Nov. 2020, https://doi.org/10.1016/j.porgcoat.2020.105749
-
R. D. Ellis, J.-H. Pyeon, S.-H. Lee, and B. Kim, “Evaluation of seal coating treatments to manage temporary pavement paint markings during highway construction,” KSCE Journal of Civil Engineering, Vol. 14, No. 4, pp. 461–471, Jul. 2010, https://doi.org/10.1007/s12205-010-0461-5
-
P. Songchitruksa, G. L. Ullman, and A. M. Pike, “Guidance for cost-effective selection of pavement marking materials for work zones,” Journal of Infrastructure Systems, Vol. 17, No. 2, pp. 55–65, Jun. 2011, https://doi.org/10.1061/(asce)is.1943-555x.0000043
-
K. Nagata et al., “Mechanical properties of poly(vinyl chloride)/silane-treated glass beads composite: effects of organofunctional group and alkoxy group numbers of silane coupling agent,” Composite Interfaces, Vol. 9, No. 3, pp. 273–287, Jan. 2002, https://doi.org/10.1163/156855402320257357
-
D. Arencón, M. L. Maspoch, and J. I. Velasco, “The effect of compatibilizing and coupling agents on the mechanical properties of glass bead filled PP/PET blends,” Macromolecular Symposia, Vol. 194, No. 1, pp. 225–232, Apr. 2003, https://doi.org/10.1002/masy.200390087
-
Y. Guo, Z. Zhang, Z. Cao, and D. Wang, “Wear behavior of hollow glass beads (HGB) reinforced nitrile butadiene rubber: Effects of silane coupling agent and filler content,” Materials Today Communications, Vol. 19, pp. 366–373, Jun. 2019, https://doi.org/10.1016/j.mtcomm.2019.03.003
-
S. G. Moghadam, S. Pazokifard, and S. M. Mirabedini, “Silane treatment of drop-on glass-beads and their performance in two-component traffic paints,” Progress in Organic Coatings, Vol. 156, p. 106235, Jul. 2021, https://doi.org/10.1016/j.porgcoat.2021.106235
Cited by
About this article
The research was supported by the Transportation Science and Technology Project in Shaanxi Province (Nos. 19-21K, 20-16K, 20-22K), and the Fundamental Research Funds for the Central Universities, CHD (300102310501).
The datasets generated during and/or analyzed during the current study are available from the corresponding author on reasonable request.
The authors declare that they have no conflict of interest.