Abstract
In order to analyze the effect of the combination of long and short inertia channels and orifice flow channels on the time domain response of hydraulic mounts. Firstly, six hydraulic mounts with different combinations of inertia channels and orifice flow channels are proposed. And then, the transfer functions of dynamic stiffness and upper chamber pressure for six structures of hydraulic mounts are derived using the lumped parameter method. Next, the time domain analytic formulas for the transfer force and upper chamber pressure for six structural hydraulic mounts under steady-state excitation and step excitation are obtained using the convolution method. Finally, the analytical formula is compared with the hydraulic mount’s model built by AMEsim; Meanwhile, the effects of inertia terms of inertia channels, damping, and damping of orifice flow channels on hydraulic mounts transfer forces are analyzed; Analyze the effect of transfer force variation and excitation amplitude on hydraulic mounts damping for different configurations of structures. Research shows that inertia channels and orifice flow channels directly affect the low-frequency dynamic characteristics of hydraulic mounts. At the same time, the effective damping height of the hydraulic mounts depends on the excitation amplitude.
Highlights
- six hydraulic mounts with different combinations of inertia channels and orifice flow channels are proposed. And then, the transfer functions of dynamic stiffness and upper chamber pressure for six structures of hydraulic mounts are derived using the lumped parameter method.
- the time domain analytic formulas for the transfer force and upper chamber pressure for six structural hydraulic mounts under steady-state excitation and step excitation are obtained using the convolution method.
- the analytical formula is compared with the hydraulic mount's model built by AMEsim; Meanwhile, the effects of inertia terms of inertia channels, damping, and damping of orifice flow channels on hydraulic mounts transfer forces are analyzed.
1. Introduction
The mounts are vibration isolation elements connected between the engine and the vehicle frame, supporting the static engine load-bearing capacity, isolating the engine vibration transmitted to the vehicle frame, and reducing the impact of road impact on the engine, limiting the engine movement space. The ideal powertrain components should exhibit large stiffness and large damping at low frequencies and low stiffness and low damping at high frequencies to achieve vehicle vibration isolation performance under different operating conditions [1]. Due to the strong frequency and amplitude dependence of the mounts themselves, passive hydraulic mounts that are superior to passive rubber mounts are proposed [2]. Meanwhile, semi-active or active mounts have recently become a major research topic [3-5]. However, passive hydraulic mounts are still widely used due to their simple design and low cost.
Singh [6] proposed a linear time-invariant model with aggregate mechanics and fluid cells and validated the model by comparing dynamic stiffness predictions with experimental data for a frequency range of 1-50 Hz, emphasizing the modeling of free and fixed types of decouplers. Tiwari [7] conducted an experimental study on the hydraulic mount of an inertial channel and free-floating decoupler, identifying the inertial channel resistance, the top and bottom chamber compliance, and the effective piston area of the top chamber, and characterizing it in the frequency and time domains. Yoon and Singh [8, 9] proposed an indirect method based on the quasi-linear fluid system formulation to estimate the power transmitted by a fixed or free decoupled hydraulic mount on a rigid base to compensate for the inaccuracy of the mechanical system model. Farzad [10] proposed a variable stiffness decoupler membrane structure to replace the conventional decoupled membrane channel, and the new decoupled membrane structure can adjust the membrane stiffness according to the excitation frequency to achieve the optimal vibration isolation performance of the mounts. Liao [11] used ABAQUS software to build a fluid-structure coupling model of multi-inertial channel hydraulic mounts and to identify the structural parameters.
Studies on multi-inertia channel hydraulic mounts or bushings are mainly conducted by Zhang [12] to study the effects of the number, size, and length of inertia channels on the low-frequency dynamic performance of hydraulic mounts, revealing that different numbers of inertia channels can change the relationship between the stiffness and loss angle of hydraulic mounts and the excitation frequency. Yang [13, 14] established a multi-inertia channel-multi-throttle orifice type hydraulic bushing set parameter model, and derived formulas for stiffness and loss angle to analyze the relationship between the dynamic characteristics of multi-channel hydraulic bushings and the number of channels. It was shown that increasing the number of inertia channels and/or orifices can significantly improve the dynamic stiffness, the amplitude of loss angle, and the corresponding frequency of the bushing, thus greatly improving the performance of the bushing. Tan Chai [15-17] developed a controllable conceptual hydraulic bushing model with two parallel unequal inertia channels and a flow control unit to analyze the dynamic and time-domain characteristics of a multi-flow channel bushing numerically and experimentally. Lu [18] studied the n= 2 inertial channels mainly to derive a linear set of total parameters model for the hydraulic mount with n= 2 and analyzed its dynamic characteristics. Li [19] proposed an inertial channel optimization method based on a linearized low-frequency model excluding the effect of decoupling membranes, considering multiple arrangements of inertial channel and orifice combinations. Also, the predictions of the hydraulic mounts model were referred to the relevant references by Shishegaran [20-30]. It is shown that the use of two configurations can reduce the relative engine and body displacement transmissibility. Although studies on the time and frequency domain characteristics of multi-inertia channel hydraulic bushings have been reported, there are still some differences between the hydraulic bushing and hydraulic mount characteristics [31], and the time-domain characteristics of multi-flow channel hydraulic mounts cannot be well understood by hydraulic bushing time-domain analysis. Meanwhile, although the analysis of dynamic characteristics of multi-flow channel hydraulic mounts has been studied, the frequency domain characteristics and transient characteristics of multi-flow channel hydraulic mounts considering various combinations simultaneously have not been reported yet.
Based on the above review, the specific research objectives of this paper are as follows: To propose a lumped parameter model of the hydraulic mounts for 6 configurations of long and short inertia channels combined with orifice flow channels, and to solve the corresponding dynamic stiffness and upper chamber pressure transfer functions. Solve the time domain expressions for the steady-state response and ideal step response of the transfer force and upper chamber pressure based on the derived dynamic stiffness and upper chamber pressure transfer functions. The effects of upper chamber compliance, fluid viscosity, inertia, and damping of long and short inertia channels and orifice flow channel damping on hydraulic mount transfer force are analyzed based on time-domain expressions, and the effect of excitation amplitude on damping is also analyzed.
2. Hydraulic mount prototype study
2.1. Hydraulic mount structure
Fig. 1 shows a schematic diagram of the hydraulic mount, where Fig. 1(a) shows the structure of the passive hydraulic mount, and Fig. 1(b) shows the lumped parameter model of the passive hydraulic mount. In this case, the hydraulic mount structure includes an inertial channel and an orifice flow channel. The flow rates in the inertial and orifice flow channels are denoted by qi and qo, respectively. The rubber unit is modeled using the rubber stiffness Krand the viscous damping coefficient Br. The compliances of the upper and lower chambers of the hydraulic mount are C1 and C2 respectively, and the pressure of the upper chamber #1 is P1, and the pressure of the lower chamber #2 is P2. where the inertial channel and the orifice flow channel are represented by the fluid inertia Ii and Io and the fluid resistance Ri and Ro, respectively.
Fig. 1Hydraulic mount: a) structure diagram, b) lumped parameter model
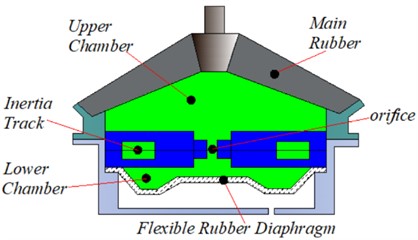
a)
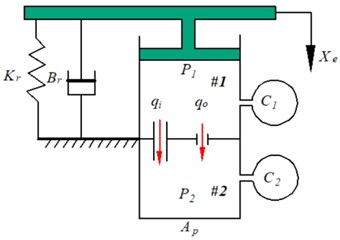
b)
2.2. Hydraulic mount flow channel design with multiple configurations
From the literature [12, 32], it is known that increasing the number of hydraulic mount inertia channels can improve the peak frequency of the dynamic stiffness and loss angle of the mount, and the combination of different flow channels can broaden the range of hydraulic mount vibration isolation frequency. However, these literature studies are all from the mount frequency characteristics and rarely involve the analysis of multi-flow channel hydraulic mount time domain characteristics. To investigate common multi-flow hydraulic mounts, six prototype configurations as shown in Table 1 and Fig. 2 were analyzed.
Fig. 2Multiple configurations of the hydraulic mount prototype a) single long inertia channel, configuration Z1, (L1= 212 mm, D1= 8.53 mm), configuration Z2 (L2=4L1, D2=D1); b) parallel combination of long inertia channel and orifice flow channel, configuration Z3 (L3=4L1, D3=D1, Lo1= 2 mm, Do1= 0.2 mm); configuration Z4 (L4=4L1, D4=D1, Lo2=Lo1, Do2=5Do1); c) parallel combination of three long inertia channels, configuration Z5 (L51=L52=L1, L53=4L1, D51=D52=D53=D1), configuration Z6 (L51=L52=L53=L1, D51=D52=D53=D1)
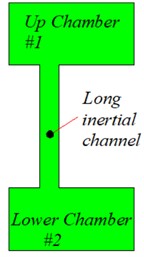
a)
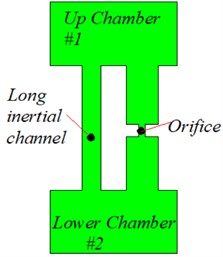
b)
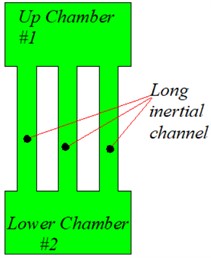
c)
The first configuration (named Z1, Z2) hydraulic mount upper and lower chambers are connected only by long inertia channels, this structure is the most common at present. Where, the length of Z1 inertia channel L1= 212 mm, the length of Z2 inertia channel L2=4L1, the diameter of Z1 and Z2 inertia channels are equal D1=D2= 8.53 mm. In the second configuration (named Z3 and Z4), the upper and lower chambers of the hydraulic mount are connected in parallel by long inertia channels and orifice flow channel. Where Z3 and Z4 inertia channels have equal lengths and diameters, L3=L4=4L1, D3=D4=8.53 mm, respectively; The length of the Z3 configuration orifice flow channel and Z4 are equal to Lo1=Lo2= 2 mm, the diameter of the Z3 orifice flow channel is Do1= 0.2 mm, and the diameter of the Z4 orifice flow channel is Do2= 1 mm. The third configuration (named Z5, Z6) is a parallel combination of the number of long inertia channels n=3. Where the diameters of the Z5 and Z6 inertial channels are equal D5=D6= 8.53 mm, L51=L52=L1, L53=4L1 in the Z5 configuration; the lengths of the three inertial channels in the Z6 configuration are equal L61=L62=L63=L1.
Fig. 3 shows the effect of variation in inertial channel length and cross-sectional area on the flow rate of the decoupler membrane channel. The decoupler membrane channel flow increases slightly with increasing inertial channel length. The flow rate of the decoupler membrane channel decreases slightly as the cross-sectional area of the inertial channel increases.
Table 1Study configuration: prototype hydraulic engine mounts with inertia channel and orifice flow channel
Design | n | Description (also see Fig. 2) |
Z1 | 1 | Baseline configuration (A long inertia channel, L1, D1) |
Z2 | 1 | A long inertia channel (L2=4L1, D2=D1) |
Z3 | 2 | Parallel combination of long inertia channel and orifice flow channel (L3=4L1, D3=D1,Lo1,Do1) |
Z4 | 2 | Parallel combination of long inertia channel and orifice flow channel (L3=4L1, D3=D1, Lo2=Lo1, Do2=5Do1) |
Z5 | 3 | Long inertia channel parallel combination (L51=L52=L1, L53=4L1, D51=D52=D53=D1) |
Z6 | 3 | Long inertia channel parallel combination (L61=L62=L63=L1, D51=D52=D53=D1) |
Fig. 3Effect of hydraulic mount inertia channel length and cross-sectional area variation on decoupling membrane channel flow: a) length variation; b) cross-sectional area variation
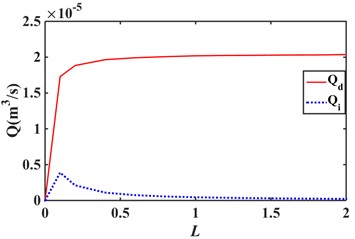
a)
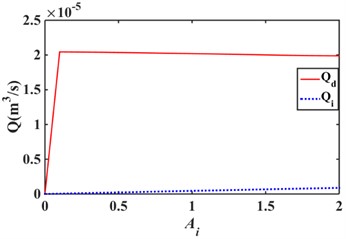
b)
2.3. AMEsim-based hydraulic mount study
Fig. 4 shows the hydraulic mounts models of six configurations built using AMEsim software.
Fig. 4(a) shows the hydraulic mounts of Z1 and Z2 configurations, Fig. 4(b) shows the hydraulic mounts of Z3 and Z4 configurations, and Fig. 4(c) shows the hydraulic mounts of Z5 and Z6 configurations.
Build 6 hydraulic mounts configurations using AMEsim, and the dynamic characteristics of the combined inertial channel and orifice flow channel hydraulic mounts were simulated for the above six configurations. The test uses a sinusoidal displacement excitation xe(t)=Asinωt, where A is the amplitude of the harmonic input and f=ω/2π is the frequency of the excitation, where the unit is Hz. The transfer forces of the hydraulic mounts and the dynamic pressures P1(t) and P2(t) within the upper and lower chambers are calculated in 1 Hz increases between 1 and 30 Hz in Xe=0.3 mm, Xe= 0.9 mm and, where Xe=2A is the peak-to-peak (P-P) value. The calculated dynamic stiffness and loss angle for a given excitation amplitude Xe= 0.3 mm and Xe= 0.9 mm hydraulic mounts can be obtained as shown in Fig. 4. It is worth noting that configurations Z5 and Z6 exhibit greater dynamic stiffness and loss angle peak frequency. While configurations Z3 and Z4 show the smallest peak frequencies for dynamic stiffness and hysteresis angle, this is due to the inclusion of orifice flow channels in both configurations. Finally, the dynamic stiffness and loss angle of Z1 and Z2 are relatively small relative to the peak, due to the number of flow channels of one in the configuration. When the excitation amplitude Xe is increased from 0.3 mm to 0.9 mm, the dynamic stiffness and hysteresis angle of the hydraulic mounts decrease, which is more obvious for Z1, Z2, Z5 and Z6.
Fig. 4AMEsim hydraulic mount model: a) single inertia channel; b) combination of inertia channel and orifice flow channel; c) combination of 3 inertia channels
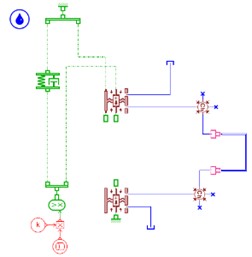
a)
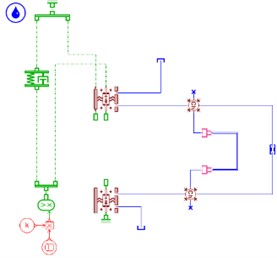
b)
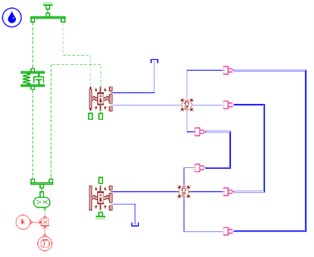
c)
Fig. 5Dynamic stiffness and loss angle of six configurations of hydraulic mount: a) Xe= 0.3 mm; b) Xe= 0.9 mm
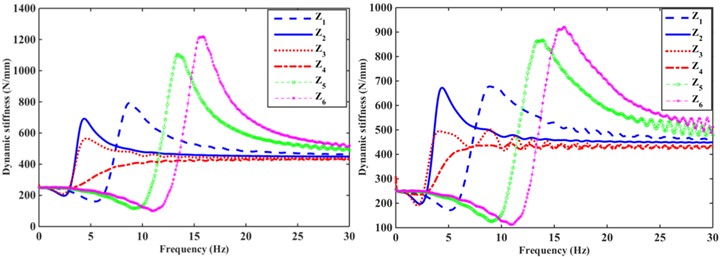
a)
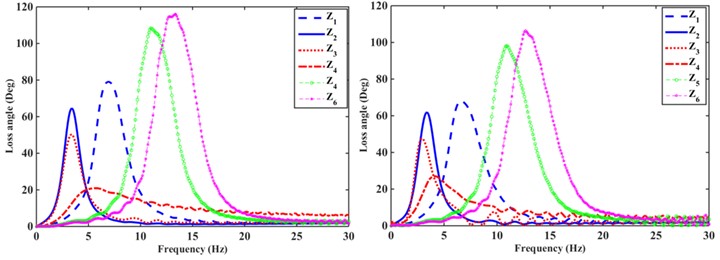
b)
3. Multi-flow channel hydraulic mount analysis model
3.1. Model I single inertia channel hydraulic mount
When the hydraulic mount is excited by xe(t), applying the continuity equation to the fluid control hydraulic unit in combination with Fig. 1 and Fig. 1(a), the following Eq. (1)-(5) are obtained. Where the fluid inertia Ii and the fluid resistance Ri are expressed:
where ρ is the density of the fluid, L is the length of the flow channel, Ai is the cross-sectional area of the flow channel, and v is the viscosity of the fluid, Dh is the equivalent “hydraulic diameter” of the flow channel. The first term on the right side of Eq. (1) is the pressure drop due to the fluid in the inertial channel due to inertia; the second term on the right side is the pressure drop due to the viscous damping of the fluid in the inertial channel.
Therefore, the hydraulic mount transfer force FT under external excitation Xe is defined as follows:
Then, by Laplace transformation of Eq. (6), the expressions for the variation of the transfer complex stiffness and the upper chamber pressure with the excitation amplitude for a single-flow channel hydraulic mount are obtained as follows:
Since 1/C1=K1, 1/C2=K2, and K1≫K2. So, Eqs. (7) and (8) can be further simplified as follows:
Eq. (9) and Eq. (10) can be simplified to a standard second-order system:
Thus, Eq. (11) can be transformed into the following standard form, where λ=A2pK1, τ=Ri/Ii:
where ς2=√R2i/4K1Ii, ωn2=√K1/Ii.
3.2. Model II combined inertial channel and orifice flow channel hydraulic mount
According to Fig. 1 and Fig. 2(b), the fluid equation of the hydraulic mount subjected to displacement excitation xe(t) for the parallel combination of inertial channel and orifice flow channel can be obtained as shown below:
In the equation, R0 is the fluid resistance of the orifice flow channel. Since the inertia in the orifice flow channel is negligible, Eq. (16) only considers the viscous damping term resulting in the hydraulic mounts differential pressure change. Reference [33] shows that when the fluid is assumed to be in the form of laminar flow in the orifice flow channel, the fluid resistance of the orifice flow channel is solved for by the following expression:
where, Do is the diameter of the orifice flow channel.
Thus, the hydraulic mounts parallel to the inertial channel and the orifice flow channel transfer the complex stiffness Kd2(s) and the variation of the upper chamber pressure with the excitation amplitude G(s) defined as follows:
Since 1/C1=K1, 1/C2=K2, and K1≫K2 can be simplified by Eqs. (20) and (21) as follows:
So, reduced to the standard second-order system form shown:
where the expressions for ωn2, ς2, κ and F are shown:
3.3. Model III parallel combination of 3 flow channel hydraulic mount
To easily solve for the multi-inertia channel hydraulic mount transfer complex stiffness Kd3(s) and the upper chamber pressure variation G(s) with excitation amplitude for the Z5 and Z6 configurations. The lumped parameter model of the multi-inertia channel hydraulic mounts with Z5 and Z6 configurations of Fig. 6(a) is equated to the equivalent mechanical model of Fig. 6(b). Because the cross-sectional area of the hydraulic mount inertia channel is much smaller than the equivalent cross-sectional area of the rubber main spring, when the fluid flows through the inertia channel, the fluid velocity is amplified to play the role of vibration attenuation, the literature [6] referred to it as a velocity amplification of large absorbing array.
Fig. 6Multi-inertia channel hydraulic mount: a) lumped parameter model, b) equivalent mechanical model
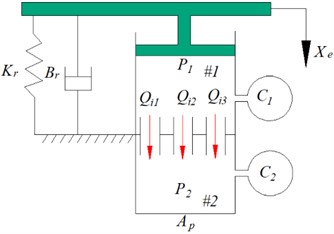
a)
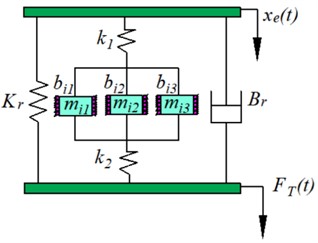
b)
According to Fig. 6(a), the mathematical model equation of the lumped parameters of the multi-inertia channel hydraulic mounts can be obtained as follows:
where, qi1, qi2, qi3 are the flow rate through the three inertia channels of configuration Z5 and Z6 respectively, Ii1, Ii2, Ii3 are the inertia flow through the three inertia channels respectively, Ri1, Ri2, Ri3 are the liquid resistance flow through the three inertia channels respectively.
In Fig. 6(b), k1=A2p/C1 is the equivalent linear stiffness of the upper chamber of the hydraulic mount, k2=A2p/C2 is the equivalent linear stiffness of the lower chamber of the hydraulic mount, bin (n=1, 2, 3) is the equivalent damping of the fluid in the inertia channel of the hydraulic mount, and min (n=1, 2, 3) is the equivalent mass of the fluid in the inertia channel of the hydraulic mount [34]. It is known that the flow rate q=Ai˙xi, where Ai is the cross-sectional area of the inertial channel and ˙xi is the average flow velocity of the fluid in the inertial channel. Therefore, Eqs. (32-35) can be written as shown in the following equation:
where, Ai1, Ai2, Ai3 are the cross-sectional areas of the three inertial channels in configurations Z5 and Z6, and xi1, xi2, xi3 are the displacements of the fluid flowing through the three inertial channels in configurations Z5 and Z6, respectively.
Combining the equivalent mechanical model of the multi-inertia channel hydraulic mount in Fig. 6(b) and the literature [2] the Eqs. (33-36) can be written as follows:
Because C1≪C2, The equivalent masses of the three inertia channels of the hydraulic mounts of the Z5 and Z6 structures are mi1=Ii1A2p, mi2=Ii2A2p, mi3=Ii3A2p, and the equivalent damping of the three inertial channels of the hydraulic mounts of the Z5 and Z6 are bi1=Ri1A2p, bi2=Ri2A2p, bi3=Ri3A2p respectively. Therefore, Eqs. (37)-(39) can be further simplified as shown below:
Referring to the literature [32], the equivalent mass and equivalent damping of the inertial channel can be expressed as follows:
Therefore, the Eqs. (40-43) can be reduced to the following expression:
As a result, the transfer function expressions for the transfer complex stiffness and the upper chamber pressure variation with excitation for the multi-inertia channel hydraulic mounts of Z5 and Z6 structures are as follows:
Therefore, the expressions for Eqs. (48) and (49) reduced to a standard second-order system are shown below:
where the expressions for κ, ωn2 and ς2 are as follows:
The key parameters of the hydraulic mount can be obtained by combining model I, model II and mode III as shown in Table 2.
Table 2Key parameters of the system for the analytical model.
System parameters | Model I | Model II | Mode III |
λ | A2pK1 | A2pK1 | k1 |
κ | RiIi | RiIi | beqmeq |
ωn2 | √K1Ii | √(Ri+R0)K1IiR0 | √K1meq |
ς2 | √R2i4K1Ii | (RiR0+K1Ii)2√1K1IiR0(Ri+R0) | beq2√1K1meq |
4. Multi-fluid hydraulic mount time domain analytical formula
4.1. Time domain steady-state harmonic response
To analyze the hydraulic mounts in Models I, II, and III configurations for steady-state harmonic response, the hydraulic mounts transfer the force FT(t) and the pressure P1(t) in the upper chamber, the specific derivation process was referred to the reference [15, 16]. According to the convolution of the bishop function:
where x(t)*y(t) is the mathematical expression of the convolution.
Therefore, the analytical equations of the transfer force FT(t) and the pressure P1(t) in the upper chamber under the steady-state harmonic response in the time domain for models I, II and III of the hydraulic mount configurations can be solved according to Eq. (52), which is expressed as the following equation:
4.1.1. Model I hydraulic mount
For the single inertial channel of model I, the third e hydraulic path of the right-hand side of Eq. (13) and Eq. (14) can be written as the following expressions:
The inverse Laplace transform of Eqs. (55-56) is shown:
where ωd=ωn2√1-ς22 is the damped self-oscillation angular frequency of the system.
Therefore, combining Eq (53) and (54) give the following expression for the sine excitation xe(t)=Asinωt, the analytic expression for the model I hydraulic mounts transfer force FT(t) and the pressure P1(t) in the upper chamber:
+e-atcsinωdt+e-atacosωdt-csinωt-acosωtω2+ω2n2-2ωdω),
--e-atcsinωdt-e-atacosωdt+csinωt+acosωtω2+ω2n2-2ωdω).
The expressions of a, b and c, in the form are as follows: a=ωn2ς2, b=ω+ωd, c=ω-ωd.
4.1.2. Model II hydraulic mount
Re-express the third term on the right-hand side of Eqs. (24) and (25) as Eqs. (61) and (61):
The following expression for the inverse Laplace transforms of Eqs. (61-62):
where θ=tan-1(√1-ς22/ς2).
Combining Eqs. (53) and (54), the hydraulic mount with parallel combination of inertia channel and orifice flow channel in model II configuration can be obtained for the transfer force FT(t) and the pressure P1(t) in the upper chamber at a sinusoidal excitation xe(t)=Asinωt:
∙(-e-atacosωdt+e-atbsinωdt+acosωt+bsinωtω2+ω2n2+2ωdω
--e-atacosωdt-e-atcsinωdt+acosωt+csinωtω2+ω2n2-2ωdω)
+(2ςn2ωn2-κ)2√1-ς2n2({-e-atacos(ωdt-θ)+e-atbsin(ωdt-θ)+acos(ωt-θ)+bsin(ωt-θ)}ω2+ω2n2+2ωdω
-{-e-atacos(ωdt-θ)-e-atcsin(ωdt-θ)+acos(ωt-θ)+csin(ωt-θ)}ω2+ω2n2-2ωdω)}.
4.1.3. Model III hydraulic mount
Re-express the third term on the right-hand side of Eqs. (50) and (51) as Eqs. (67) and (68):
The following expression for the inverse Laplace transforms of Eqs. (67), (68):
Combining Eqs. (53) and (54), the hydraulic mount for the parallel combination of inertial channels in the Model III configuration can be obtained for the transfer force FT(t) and the pressure P1(t) in the upper chamber at a sinusoidal excitation xe(t)=Asinωt:
-Aλωn22√1-ς2n2(e-atbsinωdt-e-atacosωdt+bsinωt+acosωtω2+ω2n2+2ωdω
+e-atcsinωdt+e-atacosωdt-csinωt-acosωtω2+ω2n2-2ωdω)+Aλ(2ςn2ωn2-κ)2√1-ς2n2
∙(e-atbsin(ωdt-θ)-e-atacos(ωdt-θ)+bsin(ωt-θ)+acos(ωt-θ)ω2+ω2n2+2ωdω
+e-atcsin(ωdt-θ)+e-atacos(ωdt-θ)-csin(ωt-θ)-acos(ωt-θ)ω2+ω2n2-2ωdω),
∙(-e-atacosωdt+e-atbsinωdt+acosωt+bsinωtω2+ω2n2+2ωdω
--e-atacosωdt-e-atcsinωdt+acosωt+csinωtω2+ω2n2-2ωdω)
+(2ς2ωn2-κ)2√1-ς2n2({-e-atacos(ωdt-θ)+e-atbsin(ωdt-θ)+acos(ωt-θ)+bsin(ωt-θ)}ω2+ω2n2+2ωdω
-{-e-atacos(ωdt-θ)-e-atcsin(ωdt-θ)+acos(ωt-θ)+csin(ωt-θ)}ω2+ω2n2-2ωdω)}.
4.2. Transient response of ideal step excitation
Using Section 2, and the convolution method in Section 3.1, the analytical equations for the transfer force FT(t) and the pressure P1(t) in the upper chamber at step excitation xe(t)=A1u(t) are derived for the hydraulic mounts configurations in Models I, II, and III.
The analytical equations for the transfer force FT(t) and the pressure P1(t) in the upper chamber of the hydraulic mount of model I under the step excitation xe(t)=A1u(t) are as follows:
The analytical equations for the transfer force FT(t) and the pressure P1(t) in the upper chamber of the hydraulic mount of model II under the step excitation xe(t)=A1u(t) are as follows:
+A1K1Ap2ς2ωn2-κωdωn2{e-at[asin(ωdt-θ)+ωdcos(ωdt-θ)]+asinθ-ωdcosθ}.
The analytical equations for the transfer force FT(t) and the pressure P1(t) in the upper chamber of the hydraulic mount of model III under the step excitation xe(t)=A1u(t) are as follows:
+A1K1Ap2ς2ωn2-κωdωn2{e-at[asin(ωdt-θ)+ωdcos(ωdt-θ)]+asinθ-ωdcosθ}.
5. Effect of different parameters on hydraulic mount
5.1. Compliance of the upper chamber and the viscosity of the fluid
The upper chamber compliance C1 of model I was varied in order to study the effect of the variation of C1 on the hydraulic mount. The value of C1 varies from 0.1C1 to 10C1, and the variation of the hydraulic mount transfer force is shown in Fig. 7(a). When changing the compliance of the hydraulic mount upper chamber of model I to 0.1 C1, the amplitude of the transfer force increases significantly and the period decreases, as shown in the solid blue line in Fig. 7(a). Because according to Table 1 and Eq. (59), a decrease in C1 leads to an increase in λ, ωn2. Similarly, when C1 increases from 1.0C1 to 10C1leads to a decrease in λ and ωn2, so the amplitude of the transfer force of the hydraulic mount of model 1 decreases significantly and the period increases for the same reason. When the viscosity vis is increased from 0.1vis to 10vis, it is clear from Fig. 7(b) that the transfer force of the hydraulic mount of model I gradually decreases, especially when increasing the fluid viscosity to 10vis is the most obvious. This is due to the increase in viscosity vis leads to an increase in damping of the fluid flow through the inertia channel in Eq. (5), combined with the increase in κ and ς2 obtained from Table 1, and the decrease in the transfer force FT(t) of the hydraulic mount of model I according to Eq. (59).
Fig. 7Effect of upper chamber compliance and fluid viscosity on hydraulic mount transfer force: a) different C1 values, b) different fluid vis
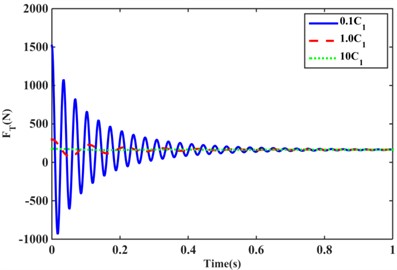
a)
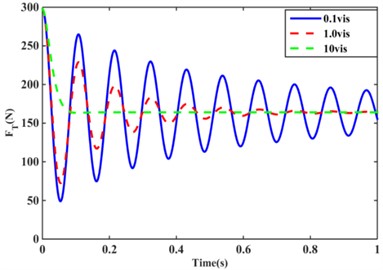
b)
5.2. Effect of inertia channel and orifice flow channel parameters on hydraulic mount
The effect of inertia and damping of the Z4 structural inertia channel fluid of model II on the transfer force of the hydraulic mount under ideal step excitation is shown in Fig. 8(a), (b). As can be seen from Eq. (4), the value of Ii is regulated by varying the length L and effective cross-sectional area Ai of the inertia channel, which has a significant effect on the peak and period of oscillation of the hydraulic mount under external excitation. Fig. 8(a) shows that as Ii increases, the period of oscillation td=2π/ωd and the peak value of the transfer force increase. This is due to the combination of Table 1 and Eq. (75) increasing Ii leads to a decrease in the rate of decay of the transfer force. As shown in Fig. 8(b), the step response of the hydraulic mount transfer force changes from an under-damped response to an over-damped response as the value of Ri changes. At the same time, the increase in Ri reduces the amplitude of the system oscillation, but the oscillation period Td increases slightly. Fig. 8(c), (d) shows the step response of the hydraulic mount transfer force by varying the damping values of the short flow channel of the Z3 and Z4 structures for the Model II configuration. Increasing the damping values R01 and R02 of the orifice flow channels Z3 and Z4, the transfer force FT(t) oscillation increases. Instead, as the damping values R01 and R02 decrease, the transfer force FT(t) decays more rapidly. However, comparing Fig. 8(c) with Fig. 8(d) shows that the larger the cross-sectional area of the orifice flow channel the more rapidly the transfer force of the system decays.
5.3. Effect of different structural configurations on transfer force
In order to compare the effects of different combinations of inertia channels and orifice flow channels on the performance of hydraulic mounts. Fig. 9 shows the variation of the transferred force for Z2 in model 1 configuration, Z4 in model 2 configuration and Z6 in model 3 configuration for the same step excitationxe(t)=A1u(t)and sinusoidal excitation xe(t)=A1sin(ωt). It can be observed in Fig. 9 that the Z4 structure in the model II configuration has the fastest decay of transfer force, followed by the Z6 structure in the model III configuration, and the Z2 structure in the model I configuration has the slowest decay of transfer force. As a result, it can be concluded that the presence of the orifice flow channel increases the damping of the system and minimizes the overshoot of the transfer force step response. Meanwhile, comparing the Z2 and Z6 structures, it can be found that although the Z6 structure decays faster than the Z2 structure, the oscillation period Td and the amount of overshoot of the Z6 structure are significantly larger than those of the Z2 structure.
Fig. 8Effect of model II hydraulic mount transfer force under ideal step excitation: a) inertia channel inertia; b) inertia channel damping; c) Z3 structural orifice flow channel damping; d) Z4 structural orifice flow channel damping
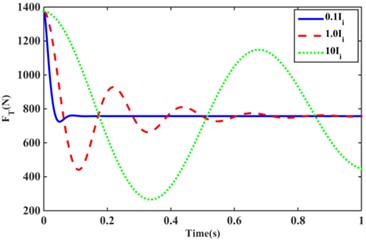
a)
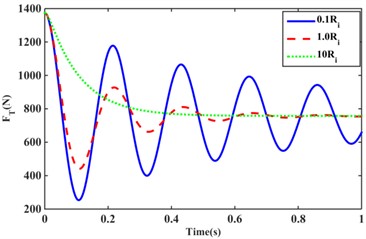
b)
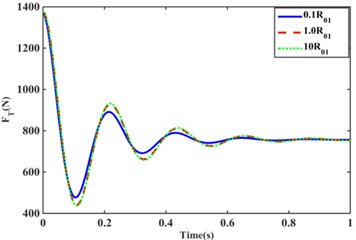
c)
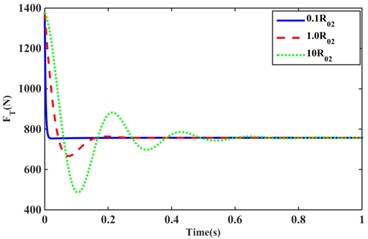
d)
Fig. 9Combination of hydraulic mounts with different inertia channels to transfer forces: a) step excitation; b) half sine excitation
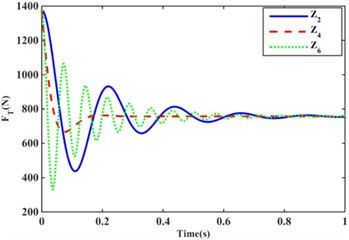
a)
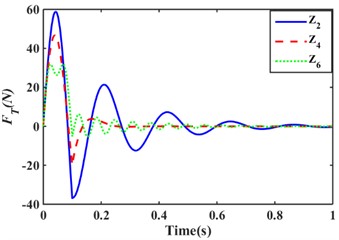
b)
6. Time-domain response analysis
6.1. Steady-state harmonic excitation response analysis
The blue line in Fig. 10 compares the response of the hydraulic mount transfer force and upper chamber pressure using the analytical solution of the steady-state response for Models I, II, and III solved in Section 3 with the red dashed line modeled using AMEsim. Fig. 10 show that the steady-state responses of the transfer force and upper chamber pressure solved using the analytical formula are in good agreement with the steady-state responses of the hydraulic mount solution built by AMEsim. For example, the errors between the RMS of the transfer force and the upper chamber pressure response solved by the two methods for the Z1 the structure are 4.92 % and 9.81 %, respectively. The RMS of the transfer force and the pressure in the upper chamber of the Z4 structure was 97.4724 N and 0.0178 MPa, respectively, when solved analytically, while the transfer force and the pressure in the upper chamber were 91.03 N and 0.01529 MPa when solved by AMEsim, with RMS errors of 6.61 % and 14.1 %. Similarly, the errors between the RMS of the transfer force and the upper chamber pressure response solved by the two methods for the Z5 structure are 6.08 % and 10.81 %, respectively.
Fig. 10Steady-state response of transfer force and upper chamber pressure for Z1, Z4 and Z5 structures at 25 Hz, amplitude of 0.3 mm: a) Z1 structure; b) Z4 structure, c) Z5 structure
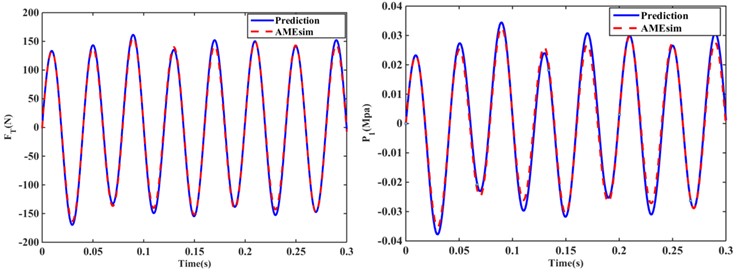
a)
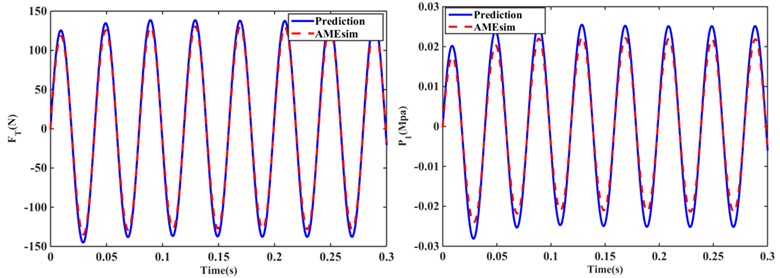
b)
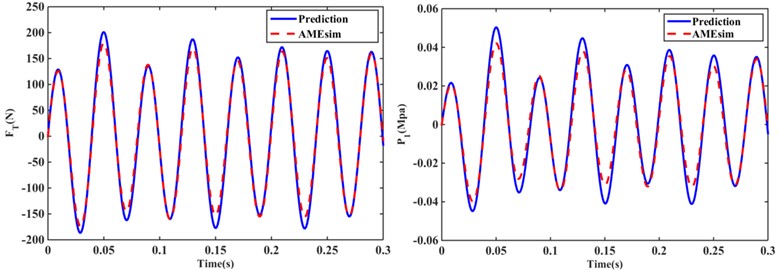
c)
6.2. Ideal step excitation response analysis
The transfer forces for the structure of Model 1 configuration at amplitudes A1= 1.0 mm, 2.0 mm, 3.0 mm are normalized and then overlapped in the same plot as shown in Fig. 11(a). From Fig. 11(a), it is observed that the overshoot of the transfer force decreases with the increase of the excitation amplitude and the transfer force decays faster while the oscillation period is longer. This means that as the excitation amplitude increases, the natural frequency and damping ratio of the system changes. To further illustrate whether the hydraulic mounts in the inertial channel configuration are damping related when the excitation amplitude varies leading to changes in the transfer force. The transfer force step response solved using the model 1 configuration Z1 structure in Section III is shown in Fig. 11(b) by changing the damping value of the inertia channel from 1.0Ri to an increased value of 3.0Ri. Comparing Fig. 11(a), (b), it can be found that the damping of the inertial channel depends directly on the excitation amplitude. This conclusion is similar to that of reference studies on multi-inertia channel bushings [14].
Fig. 11Transfer force response of Z1 structure with different step excitation for model I configuration: a) Normalized response of transfer force with different excitation amplitude under AMEsim; b) Transfer force response with different damping values solved analytically
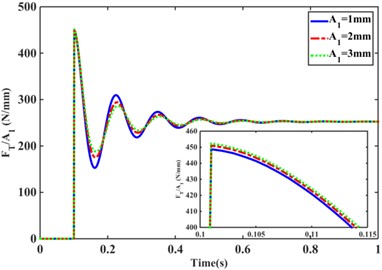
a)
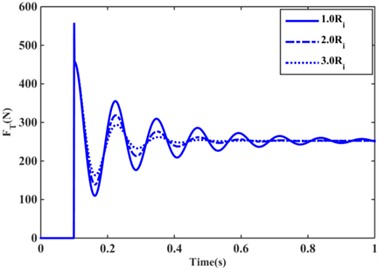
b)
7. Conclusions
The main contribution of the article is to investigate the time domain response of hydraulic mounts for the combination of long and short inertia channels and orifice flow channels since there are few studies on the time domain of hydraulic mounts for the combination of long and short inertia channels and orifice flow channels. A combination of numerical analysis and hydraulic analysis software AMEsim was used to compare the steady-state response and step response of different combinations of short and long inertia channels and orifice flow channels. Firstly, the transfer functions of dynamic stiffness and an upper chamber pressure of the hydraulic mounts of six configurations are derived using the lumped model. Secondly, the convolution method is used to solve the time domain analytic equations for the steady-state and step responses of the hydraulic mounts conFig.d in Model I, Model II, and Model III. Study shows that (1) increased compliance and fluid viscosity in the upper chamber of the hydraulic mount can rapidly decrease the transfer force; (2) Reducing the inertia of the inertia channel of the hydraulic mount and increasing the damping of the inertia channel can make the fastest transfer force reach the minimum value while increasing the cross-sectional area of the orifice flow channel can improve the damping value of the hydraulic mount. (3) The transfer forces and upper chamber pressures of the hydraulic mounts of different configurations obtained by the analytical method are in good agreement with the steady-state response of the mounts built by the hydraulic software AMEsim; (4) The effective damping is dependent on the excitation amplitude for hydraulic mounts.
References
-
Y. Yu, N. G. Naganathan, and R. V. Dukkipati, “A literature review of automotive vehicle engine mounting systems,” Mechanism and Machine Theory, Vol. 36, No. 1, pp. 123–142, Jan. 2001, https://doi.org/10.1016/s0094-114x(00)00023-9
-
G. Kim and R. Singh, “A study of passive and adaptive hydraulic engine mount systems with emphasis on non-linear characteristics,” Journal of Sound and Vibration, Vol. 179, No. 3, pp. 427–453, Jan. 1995, https://doi.org/10.1006/jsvi.1995.0028
-
Zhaoxue Deng, Qinghua Yang, and Xuejiao Yang, “Optimal design and experimental evaluation of magneto-rheological mount applied to start/stop mode of vehicle powertrain,” Journal of Intelligent Material Systems and Structures, Vol. 31, No. 3, 2020.
-
Fu-Long Xin, X. Bai, and Li-Jun Qian, “Principle, modeling, and control of a magnetorheological elastomer dynamic vibration absorber for powertrain mount systems of automobiles,” Journal of Intelligent Material Systems and Structures, Vol. 28, No. 16, pp. 2239–2254, 2017.
-
B.-H. Lee and C.-W. Lee, “Model based feed-forward control of electromagnetic type active control engine-mount system,” Journal of Sound and Vibration, Vol. 323, No. 3-5, pp. 574–593, Jun. 2009, https://doi.org/10.1016/j.jsv.2009.01.033
-
R. Singh, G. Kim, and P. V. Ravindra, “Linear analysis of automotive hydro-mechanical mount with emphasis on decoupler characteristics,” Journal of Sound and Vibration, Vol. 158, No. 2, pp. 219–243, Oct. 1992, https://doi.org/10.1016/0022-460x(92)90047-2
-
M. Tiwari, H. Adiguna, and Rajendra Singh, “Experimental characterization of a nonlinear hydraulic engine mount,” Noise Control Engineering Journal, Vol. 51, No. 1, pp. 212–223, 2003.
-
Jong-Yun Yoon and Rajendra Singh, “Dynamic force transmitted by hydraulic mount: Estimation in frequency domain using motion and/or pressure measurements and quasi-linear models,” Noise Control Engineering Journal, Vol. 58, No. 4, 2010.
-
J.-Y. Yoon and R. Singh, “Indirect measurement of dynamic force transmitted by a nonlinear hydraulic mount under sinusoidal excitation with focus on super-harmonics,” Journal of Sound and Vibration, Vol. 329, No. 25, pp. 5249–5272, Dec. 2010, https://doi.org/10.1016/j.jsv.2010.06.026
-
F. Fallahi et al., “A modified design for hydraulic engine mount to improve its vibrational performance,” Proceedings of the Institution of Mechanical Engineers, Part C. Journal of Mechanical Engineering Science, Vol. 23, No. 23, 2021.
-
X. Liao, X. Sun, and H. Wang, “Modeling and dynamic analysis of hydraulic damping rubber mount for cab under larger amplitude excitation,” Journal of Vibroengineering, Vol. 23, No. 3, pp. 542–558, May 2021, https://doi.org/10.21595/jve.2021.21921
-
Y.-Q. Zhang and W.-B. Shangguan, “A novel approach for lower frequency performance design of hydraulic engine mounts,” Computers and Structures, Vol. 84, No. 8-9, pp. 572–584, Mar. 2006, https://doi.org/10.1016/j.compstruc.2005.11.001
-
C. Yang et al., “Experiment and calculation of the low frequency performance of a hydraulic bushing with multiple tracks,” Journal of Vibration Measurement and Diagnosis, 2016.
-
C.-F. Yang, Z.-H. Yin, W.-B. Shangguan, and X.-C. Duan, “A study on the dynamic performance for hydraulically damped rubber bushings with multiple inertia tracks and orifices: parameter identification and modeling,” Shock and Vibration, Vol. 2016, pp. 1–16, 2016, https://doi.org/10.1155/2016/3695950
-
T. Chai, J. T. Dreyer, and R. Singh, “Frequency domain properties of hydraulic bushing with long and short passages: System identification using theory and experiment,” Mechanical Systems and Signal Processing, Vol. 56-57, pp. 92–108, May 2015, https://doi.org/10.1016/j.ymssp.2014.11.003
-
T. Chai, J. T. Dreyer, and R. Singh, “Time domain responses of hydraulic bushing with two flow passages,” Journal of Sound and Vibration, Vol. 333, No. 3, pp. 693–710, Feb. 2014, https://doi.org/10.1016/j.jsv.2013.09.037
-
T. Chai, R. Singh, and J. Dreyer, “Dynamic stiffness of hydraulic bushing with multiple internal configurations,” SAE International Journal of Passenger Cars – Mechanical Systems, Vol. 6, No. 2, pp. 1209–1216, May 2013, https://doi.org/10.4271/2013-01-1924
-
Lu M. and Ari-Gur J., “Study of hydromount and hydrobushing with multiple inertia tracks,” in JSAE Annual Congress Proceedings, 2002.
-
Y. Li, J. Z. Jiang, and S. A. Neild, “Optimal fluid passageway design methodology for hydraulic engine mounts considering both low and high frequency performances,” Journal of Vibration and Control, Vol. 25, No. 21-22, pp. 2749–2757, Nov. 2019, https://doi.org/10.1177/1077546319870036
-
A. Shishegaran, H. Varaee, T. Rabczuk, and G. Shishegaran, “High correlated variables creator machine: Prediction of the compressive strength of concrete,” Computers and Structures, Vol. 247, p. 106479, Apr. 2021, https://doi.org/10.1016/j.compstruc.2021.106479
-
A. Shishegaran, M. Saeedi, S. Mirvalad, and A. H. Korayem, “Computational predictions for estimating the performance of flexural and compressive strength of epoxy resin-based artificial stones,” Engineering with Computers, Vol. 39, No. 1, pp. 347–372, Feb. 2023, https://doi.org/10.1007/s00366-021-01560-y
-
A. Shishegaran, M. R. Khalili, B. Karami, T. Rabczuk, and A. Shishegaran, “Computational predictions for estimating the maximum deflection of reinforced concrete panels subjected to the blast load,” International Journal of Impact Engineering, Vol. 139, p. 103527, May 2020, https://doi.org/10.1016/j.ijimpeng.2020.103527
-
A. Shishegaran, A. N. Boushehri, and A. F. Ismail, “Gene expression programming for process parameter optimization during ultrafiltration of surfactant wastewater using hydrophilic polyethersulfone membrane,” Journal of Environmental Management, Vol. 264, p. 110444, Jun. 2020, https://doi.org/10.1016/j.jenvman.2020.110444
-
B. Karami, A. Shishegaran, H. Taghavizade, and T. Rabczuk, “Presenting innovative ensemble model for prediction of the load carrying capacity of composite castellated steel beam under fire,” Structures, Vol. 33, pp. 4031–4052, Oct. 2021, https://doi.org/10.1016/j.istruc.2021.07.005
-
M. A. Naghsh et al., “An innovative model for predicting the displacement and rotation of column-tree moment connection under fire,” Frontiers of Structural and Civil Engineering, Vol. 15, No. 1, pp. 194–212, Feb. 2021, https://doi.org/10.1007/s11709-020-0688-2
-
A. Shishegaran, M. Saeedi, A. Kumar, and H. Ghiasinejad, “Prediction of air quality in Tehran by developing the nonlinear ensemble model,” Journal of Cleaner Production, Vol. 259, p. 120825, Jun. 2020, https://doi.org/10.1016/j.jclepro.2020.120825
-
A. Shishegaran, M. Moradi, M. A. Naghsh, B. Karami, and A. Shishegaran, “Prediction of the load-carrying capacity of reinforced concrete connections under post-earthquake fire,” Journal of Zhejiang University-SCIENCE A, Vol. 22, No. 6, pp. 441–466, Jun. 2021, https://doi.org/10.1631/jzus.a2000268
-
A. Shishegaran, B. Karami, E. Safari Danalou, H. Varaee, and T. Rabczuk, “Computational predictions for predicting the performance of steel 1 panel shear wall under explosive loads,” Engineering Computations, Vol. 38, No. 9, pp. 3564–3589, Sep. 2021, https://doi.org/10.1108/ec-09-2020-0492
-
A. Shishegaran, M. Shokrollahi, A. Mirnorollahi, A. Shishegaran, and M. Mohammad Khani, “A novel ensemble model for predicting the performance of a novel vertical slot fishway,” Frontiers of Structural and Civil Engineering, Vol. 14, No. 6, pp. 1418–1444, Dec. 2020, https://doi.org/10.1007/s11709-020-0664-x
-
A. Bigdeli, A. Shishegaran, M. A. Naghsh, B. Karami, A. Shishegaran, and G. Alizadeh, “Surrogate models for the prediction of damage in reinforced concrete tunnels under internal water pressure,” Journal of Zhejiang University-SCIENCE A, Vol. 22, No. 8, pp. 632–656, Aug. 2021, https://doi.org/10.1631/jzus.a2000290
-
Yang C. F. et al., “Comparison of working mechanisms of hydraulic damped bushings and hydraulic engine mounts,” Journal of South China University of Technology (Natural Science Edition), 2015.
-
B. Barszcz, J. T. Dreyer, and R. Singh, “Experimental study of hydraulic engine mounts using multiple inertia tracks and orifices: Narrow and broad band tuning concepts,” Journal of Sound and Vibration, Vol. 331, No. 24, pp. 5209–5223, Nov. 2012, https://doi.org/10.1016/j.jsv.2012.07.001
-
E. O. Doebelin, “System dynamics: modeling, analysis, simulation, design,” Marcel dekker, Inc, 1998.
-
S. He and R. Singh, “Estimation of amplitude and frequency dependent parameters of hydraulic engine mount given limited dynamic stiffness measurements,” Noise Control Engineering Journal, Vol. 53, No. 6, pp. 271–285, 2005.
About this article
Science and Technology Guidance Project in Sanming City (2020-G-57), Fujian Province, China. China National Innovation and Entrepreneurship Training Program for college students (201911311010). Authors were supported by a grant from the Science and Technology Plan Project (2018Z016) of Quanzhou City, Fujian Province, China for the research in this paper. Sanming University introduced high-level talents scientific research start-up funding (Project number: 23YG01). Major Science and Technology Special Project of Fujian Province (2022HZ026025). Sanming science and technology plan project 2022-G-16. Fujian Province regional development project 2022H4009. Sanming University introduced high-level talents scientific research start-up funding (Project number: 23YG01). Sanming City Guiding Science and Technology Plan Project (Project Number: 2023-G-1).
The datasets generated during and/or analyzed during the current study are available from the corresponding author on reasonable request.
Zhihong Lin – conceptualization, methodology, software, investigation, formal analysis, writing-original draft. Chunrong Wang – conceptualization, funding acquisition, writing-review and editing. Yunxiao Chen – software, validation. Mingzhong Wu – visualization, writing-review and editing. Feijie Zheng – software, validation. Jian Wei – visualization, writing-review and editing.
The authors declare that they have no conflict of interest.