What is finite element method (FEM) simulation? A structure, whatever, living or inanimate has infinite points in its composition. When calculating the effect of forces or pressures exerted on this structure for various purposes such as fatigue analysis, point of failure, plastic or elastic deformations suffered by the structure under pressures, etc. The number of points where these calculations would have to be made is infinite practically making the calculation impossible. This calculation is a calculation made in the so-called continuous domain where there are no gaps in the range (of the structure) to be calculated. To enable this type of calculation, we started to use the method called discrete, which is to calculate what occurs at a separate point, with nothing around it, without intermediate intervals or values i.e., a finite set of values or an infinite set of countable values.
In the FEM simulation, the discrete method is used, it calculates what occurs a certain number of points of the structure submitted to a load and extrapolates to the entire structure. Despite a reliable response, bench testing is required to check the response by FEM that sometimes does not match.
What is FEM simulation for in Dentistry? Pre-clinical testing of materials with the most diverse utilities. These tests may include both what happens with the material subjected to load and what will be the behavior of this material in relation to biological tissues. It can be used in the development of health devices. See the development example of the gnathodynamometer shown below. The simulation of the initial geometry resulted in failure leading to the generation of new geometries until it arrived in a promising for the bench tests.
At Fig. 1 it can be observed that the tips touch, invaliding the clamp. At the internal inferior corner of the clamp a red line can be observed showing a region of failure. At the right side of the figure there is a color scale showing von Mises tension scale that shows the tension at each part of the clamp. The metal used in the clamp simulation supports, without failure, tension represented only in blue and green colors, yellow, orange, and red denotes sites of failure of the structure. In Fig. 2 a FEM simulation of the new geometry of the clamp where there is no touch of the tips and no site of failure. The simulation saves time and money by reducing the number of structures tested in a teste machine on the bench and bench testing time.
Besides its use in the development of devices for human health, FEM simulation is being using to help the development of new materials to use in dental restoration and their geometry. Hussein et al. [1] used FEM simulation to study the effects on the posterior region of the mandible with different implants thread and shape. Prados-Privado et al. [2] used FEM simulation to study implant connections and Skamniotis et al. [3] used FEM to study the behavior of bio-composites.
Fig. 1FEM simulation. First geometry tested for a clamp that will be used to build a gnathodynamometer (Figure extracted from Santiago Jr thesis)
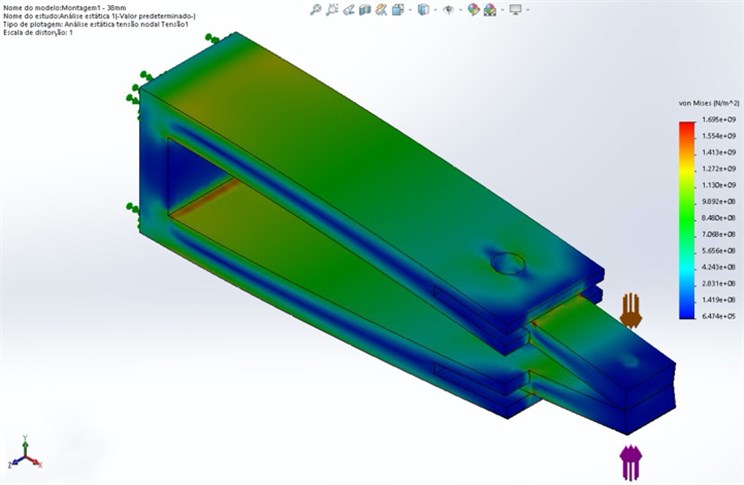
Fig. 2FEM simulation of a new clamp geometry already adapted based on previous simulations (Figure extracted from Santiago Jr thesis)
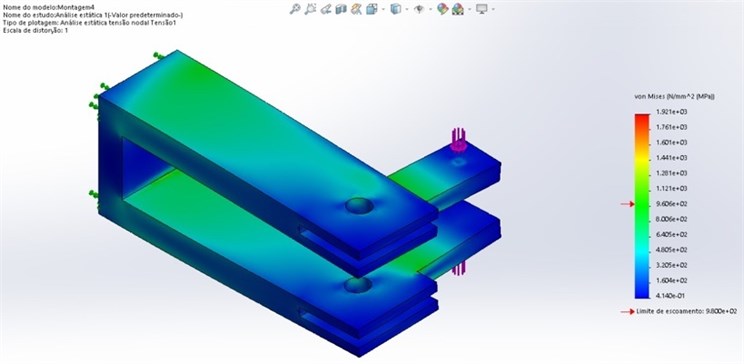
From my point of view there is a huge field of research of FEM in Jaw Functional Orthopedics (JFO), with several research lines such as the development of new polymers that allow the reduction of acrylic volume on the mouth improving functional orthopedic appliance (FOA) conditions of use by the patient. Development of new metal alloys or use of different metal alloys to improve FOA wires resistance to fractures or improve efficiency of resorts used for instance with memory wires. Other research line is to test FOA elements position and look at what positions change can influence direction and intensity of stimulus of FOA in maxillary bones or in the tongue. Another one is to test what different activation intensity promotes on mandibular and maxillary bones with regards to response and side effects. For instance, individuals with distinct mandibular bones density can be submitted to different stimulus intensity of FOA. Individuals with distinct maxillary bones geometry, or distinct craniofacial geometry (craniofacial biotypes) can be submitted to different stimulus intensity, or different stimulus direction according to biotypes can improve treatment results. Blood circulation in the periodontal ligament, or in the temporomandibular joint, for instance, can be simulated by FEM to test what happens with different stimulus intensity, distinct mandibular posture change, etc. There are so many questions to be answered that it is better to stop here otherwise this editorial will not end.
There is another thing that one can have in mind, that depending on FEM simulation results many open other research lines to test FEM simulation responses in vivo, and this investigation can take JFO to another level. Improve FOA efficiency and patient comfort, allow to increase use time, or allow adults to use FOA in their daily routine as with aligners today.
This issue is dedicated to Prof. Hans Peter Bimler that developed his appliances components (type of material used and shape), his excellent pliers shape with numerical simulation, by trial and error. A real genius.
References
-
L. Sabri, F. Hussein, K. Salloomi, B. Abdulrahman, and A. Al-Zahawi, “Effect of thread depth and implant shape on stress distribution in anterior and posterior regions of mandible bone: A finite element analysis,” Dental Research Journal, Vol. 16, No. 3, p. 200, 2019, https://doi.org/10.4103/1735-3327.255745
-
M. Prados-Privado, S. A. Gehrke, R. Rojo, and J. C. Prados-Frutos, “Complete mechanical characterization of an external hexagonal implant connection: in vitro study, 3D FEM, and probabilistic fatigue,” Medical and Biological Engineering and Computing, Vol. 56, No. 12, pp. 2233–2244, Dec. 2018, https://doi.org/10.1007/s11517-018-1846-8
-
C. G. Skamniotis, M. Elliott, and M. N. Charalambides, “On modelling the constitutive and damage behaviour of highly non-linear bio-composites – Mesh sensitivity of the viscoplastic-damage law computations,” International Journal of Plasticity, Vol. 114, pp. 40–62, Mar. 2019, https://doi.org/10.1016/j.ijplas.2018.10.001