Abstract
Greenhouses are a popular agricultural production method by providing artificial climatic conditions. Providing optimum climatic conditions depends on the equipment of the greenhouse. Greenhouse equipment consists of systems such as heating, ventilation, shading, irrigation, and fertilization. In modern greenhouse cultivation, all these have become controllable with smart systems. These modern greenhouses, in other words smart greenhouses, can read the ambient conditions in real-time with their advanced sensor systems and enable processes such as irrigation, adjustment of ambient temperature, and ventilation to be carried out autonomously. In this study, the working principle, general structure, design, and types of equipment used in the greenhouse automation system are explained, and the system is designed and simulated on the Unity Engine.
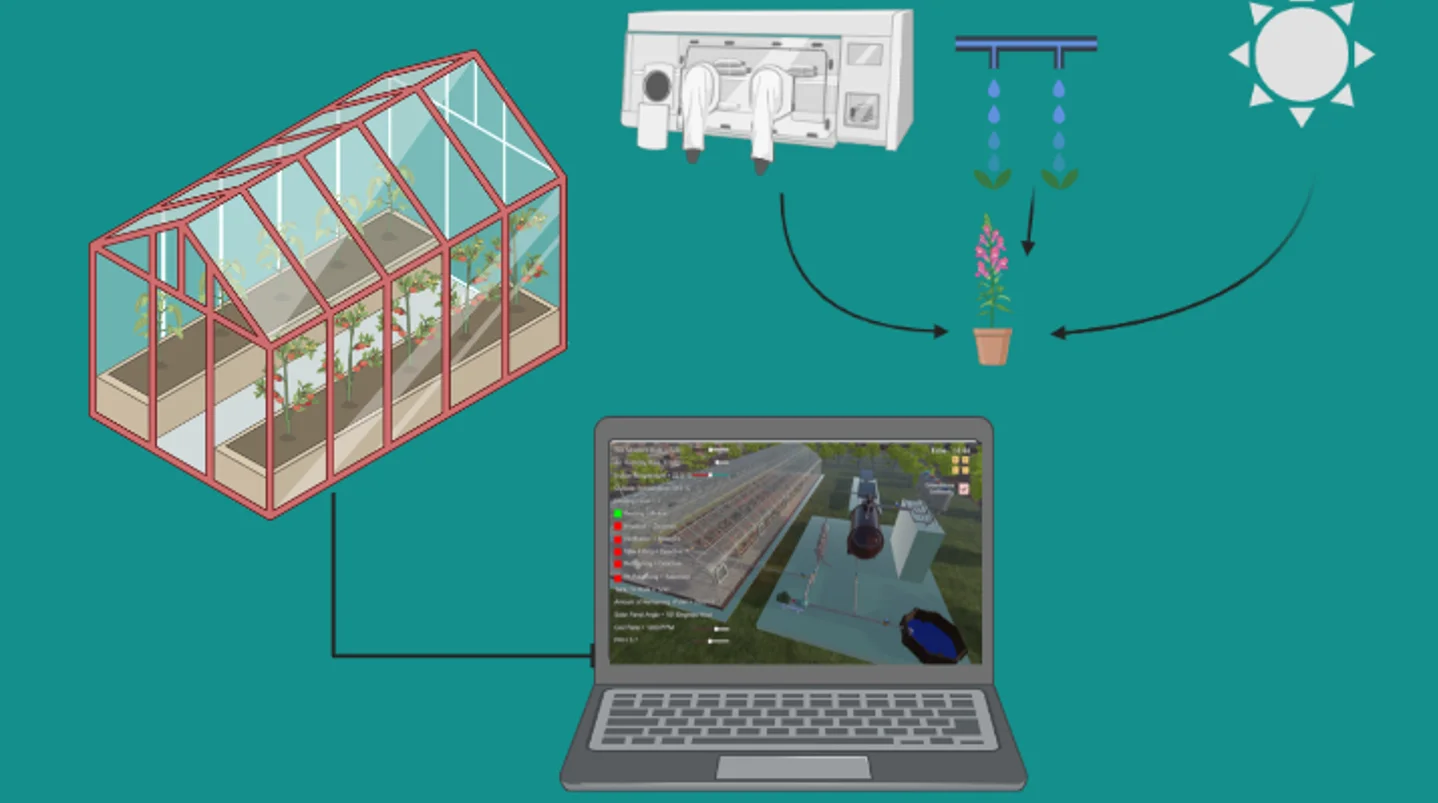
1. Introduction
Today, human life is trying to be made more livable by making use of advanced technologies in many areas and agriculture is one of these areas as the most important production area in human life [1]. A substantial proportion of the nutritional resources of humanity are obtained from agricultural production, and for this reason, it is of vital importance that the plants produced are grown in healthy and correct conditions. Controlling factors such as irrigation, soil moisture, and temperature make it more possible to grow crops under optimum conditions [2]. Agricultural lands have a wide variety of production areas from conventional production to micro fields. Two issues are important in these areas: Efficiency and sustainability. Technology is expected to produce solutions in this area because the ever-increasing world population has to be met by decreasing agricultural areas every year [3]. In addition, it is not possible to grow every plant under all conditions [4] and it depends on factors such as soil structure and climatic conditions of the geographical region [5]. In addition to these reasons, soil, water, and air pollution [6] and lack of water [7] make agriculture very difficult. Serious measures should be taken against these problems and the required production should be ensured continuously. One of these measures is greenhouse systems that provide better quality, healthier and sustainable agriculture where environmental conditions can be controlled for the environment [8].
Bringing the indoor air conditions in the greenhouses to the desired standards ensures the improvement of the properties such as the quality, growth rate, and yield of the products grown in the greenhouse [9]. The increase or decrease in values such as indoor air temperature, relative humidity, and carbon dioxide amount, which are among the most important climatic characteristics of the greenhouse [11], significantly affect the quality of the product [10]. In the study, it was aimed to grow tomato plants [12], which are sensitive to production conditions [13] and soil structure [14], in a digital greenhouse.
2. Method
Unity is a software that offers the opportunity to make games or simulations with realistic graphics with its advanced interface and graphic design support. It is a cross-platform game engine used to develop 2D or 3D video games and simulations for game consoles, computers, and mobile devices. C# is used as its programming language. It is aimed to simulate the greenhouse automation design in order to examine, evaluate and analyze the features and behaviors of the system by simulating it in the computer environment before the designed greenhouse automation system is implemented in real life. With the control parameters such as temperature, humidity, CO2 ratio, water quality entered in the system information base in line with the needs of some pre-set plants, it is possible to see how the system will behave and possible error situations and results. The reason for using Unity for simulation is that Unity software can work in an optimized way on many platforms, is easy to access, and can be programmed with a competent programming language such as C#.
Fig. 1a) Display of carbon dioxide sensor, b) temperature sensor, c) humidity sensor, d) water level sensor, e) Ph sensor used in greenhouse automation
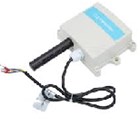
a)
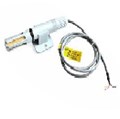
b)
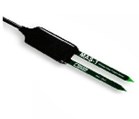
c)
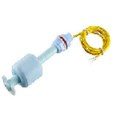
d)
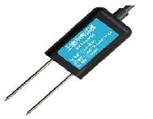
e)
Parameters such as CO2 rate, Ph rate, indoor and outdoor temperature, water pressure-flow rates, soil, and air humidity can be monitored in the simulation. Depending on these parameters, system ventilation, heating or cooling, irrigation, pump power, water quality, and energy control can be provided.
Greenhouse, irrigation installation, solar panels, water pump, water tank, water filter, water well, ventilation fans and pipes, heaters, control panel, sensors, valves, fertilizer and spraying tanks, ph balancing tanks, and plants are modeled in the digital greenhouse application.
Fig. 2a) Solar panels, b) Well filter, c) ventilation system, and d) pump system, which can be monitored in the Digital Greenhouse System
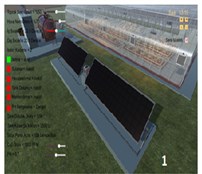
a)
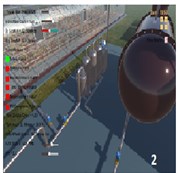
b)
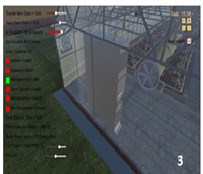
c)
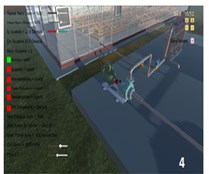
d)
3. Results
In the selection of greenhouse materials, some important features such as economical, durable, and lightweight construction materials, energy-saving, easy maintenance, and being suitable for physical conditions should be taken into consideration. The foundation, which is the part where the structure is placed, carries the area covered by the structure. The foundation can transmit the entire load of the greenhouse, which comes on itself with the columns, to the foundation ground without cracking, splitting, and breakage. It can ensure that breakages do not occur, especially in glass greenhouses. The fact that the permeability rate of glass (89-93 %) is higher than other coatings, allows plants to benefit from the sun and increase the ambient temperature.
Solar energy and the panels: In the region taken as an example to the study, the annual average solar radiation is 1303 kWh/m2 year and the average annual sunshine duration is 2623 hours. This value corresponds to a daily power of 3,6 kWh/m2 and approximately 7,2 hours of sunshine per day, a total of 110 days.
Solar panel power requirement: With 2 solar panels, a total of 720 watts is produced per hour. In the digital greenhouse, the motor requires 2 hp = 1471 w/h. The rest of the system consumes 800 watts of energy. At night, when the solar panels go out of the system, irrigation and the remaining system requirements can be met with a 200 ah/6v accumulator. Since the operation time of the motor at once is 25 minutes, energy is provided to the system with a small number of solar panels. Production increases with prolonged sun exposure.
Well Filter: Reverse osmosis system was used in the model created in the study. Reverse osmosis is a water treatment technology that can physically separate drinking water from heavy metals and other pollutants without chemical treatment. In the process, large particles insoluble in water are filtered through the residue filter. Then, the harmful organic chemicals in the water are absorbed by the active carbon filter. Heavy metals and microorganisms in the water are separated by a reverse osmosis membrane filter. Finally, the disinfection process ensures that the water is disinfected.
Ventilation: Balancing the proportional humidity in the greenhouse can be achieved by ventilation. Excess humidity in the greenhouse may cause some disease factors in the plants, as well as prevent the plants from transpiration. Since the plant that stops sweating cannot get water and nutrients from the soil, the production of the plants also stops. While ventilating, there should be no air flow, fresh air should not hit the plant directly, water should not pass through the aerator and the amount of air should be sufficient. There are two types of ventilation, namely natural and mechanical ventilation. In this study, the spontaneous airflow (Natural Ventilation) method was used. With this method, energy-saving will be ensured that, as well as the decrease in heat loss and shading and the products, are not affected by the wind force.
Seasonal conditions also change weather events. With a more stable airflow, it is necessary to prevent the air from going directly on the plant. The humidity required by the tomato plant in the system should be between 70-80 % and the temperature should be between 26-27'C. If the humidity increases, the ventilation works in the system. Otherwise, when the humidity decreases, the humidity of the environment can be increased by spraying water from the pipes to increase the ambient humidity.
Fig. 3End suction centrifugal pump and its location
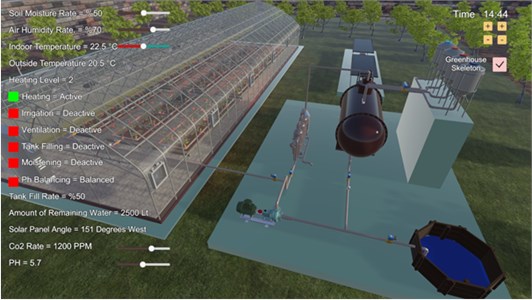
Water Pump: In the study, an end suction centrifugal pump was used, taking into account the variables such as energy requirement, well depth, and flow rate in our system. The pump can provide continuous liquid flow with its mechanism and the flow rate control can be provided by motor control systems. Structurally, it is affordable, robust, and simple. It can reach high revs. The pump was preferred for the 15 meters height, 150 L/min (9 m³/h) flow rate, and 2 atm pressure that was needed. A total of 90 drippers of 2 L/min are used in the system. At this rate, a 180 L/min flow rate is required for irrigation. In order to meet this ratio, a 2 HP engine was used. The motor used in the digital greenhouse is a motor that can provide a flow rate of 3-18 m3/h. A flow rate of 18 m3/h (300 L/min) is a sufficient flow rate for this operation. When the engine is operated with 60 % power, a sufficient flow rate is obtained for irrigation. When the engine is running at full power, the water tank can be fully refilled in about half the time it takes to irrigate.
Well height and wellhead pressure are also important factors in engine selection. In the system that was designed, the head was accepted as 0 and the height of the well was accepted as 10 meters, so a 2 HP engine can provide sufficient flow for the system.
Fig. 4Variation of flow capacity depending on the head
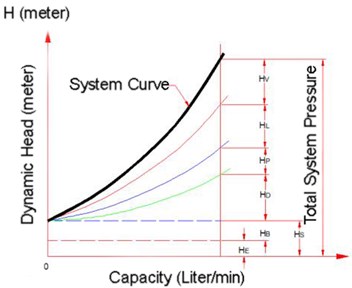
Irrigation System: In greenhouse systems, there may be decreases in yield and quality of products due to insufficient irrigation or wrong irrigation methods. For this reason, irrigation is one of the most important issues for greenhouse cultivation. In terms of quality and efficiency in greenhouse cultivation, irrigation should be done frequently and with less water. For this reason, drip irrigation systems are used.
The drip irrigation method is the application of irrigation to the root of the plant with a small amount of water at a time and in short time intervals, without creating water stress on the plant grown in case of insufficient soil moisture. Positioning of the drippers is important. Irrigation of the soil unevenly can result in under-watering some plants and lower yields. Drippers are used to deliver water to plant roots and there are many types. By using constant flow drippers in the system, more consistent irrigation is provided by obtaining a constant flow rate (Fig. 5), where , – dripper flow, – coefficient of dripper flow path cross-section area, – operating pressure, – coefficient depending on dripper flow regime
Fig. 5Flow/pressure ratio of fixed flow and normal drippers
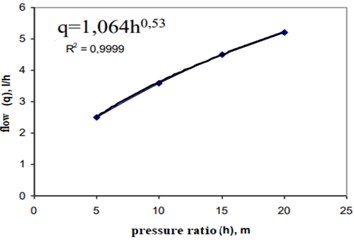
a)
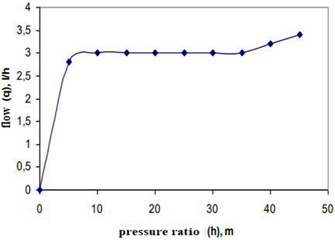
b)
The drippers used in the system are drippers with flow rates of 2 L/min and operating at 2 atm pressure. There are 6 planting rows and 15 plants in each row in the system, and there are 90 drippers in total, one for each plant. With the irrigation intervals defined on the system, for example, daily 25-minute irrigation for tomatoes creates a water requirement of 4500 liters. With the water level sensor found in the water tank, how much water is missing from the tank is calculated during this period. The water used in the system for tomatoes is equal to approximately 10 % of the water tank. If the water in the tank falls below 10 %, the automation system automatically switches to the tank filling process and raises the tank above 90 %. The daily 25 minute irrigation required for tomatoes is programmed to be done between 12:00 and 12:25 every day. If there is not enough water in the tank until 1 hour before the irrigation time, the system moves the irrigation time forward 1 hour and fills the tank during this time. If the soil moisture content falls below what it should be after irrigation, an extra 5 minutes of irrigation is performed, apart from the planned irrigation.
Fig. 6a) Irrigation and b) heating system within the simulation
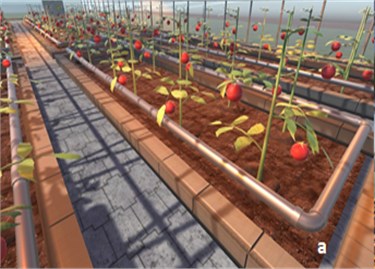
a)
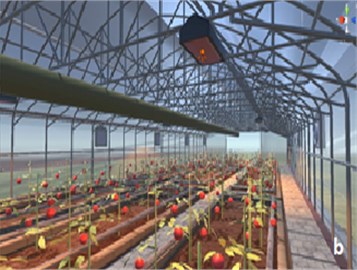
b)
Heating Systems: An electrically powered and solar-effective heater was used in the developed digital greenhouse. This heater emits a sun-like ultraviolet light to aid the photosynthesis process of plants. This heater works in 5 stages. The heaters placed above each plant pool in the hanging position look directly at the plants and balance the different climatic conditions that may occur inside the greenhouses.
The system automation works as follows: Optimum temperature values are defined for the plants entered in the system information base. In the system exemplified on the tomato plant, the required temperature value for the tomato plant to grow is 27 ℃. By measuring the internal temperature of the greenhouse with the temperature sensor, the difference between the required temperature value for the tomato is calculated. If the greenhouse is warmer than it should be, the heating system is disabled and the cooling system operates. If the greenhouse is 2-5 ℃ colder, the heater will operate on level 1, if 5-7.5 ℃, on level 2, if 7.5-10 ℃, on level 3, if 10-15 ℃, on level 4, and finally on level 5 if it is 15 ℃ colder. In this way, more energy will not be spent than necessary and energy savings will be achieved. The optimum temperature values that should be in the cultivation of plants are different for day and night. One of the biggest reasons for this is the dynamic position of the sun. For this reason, in order to create this natural environment in the greenhouse, the heating system of the system is programmed for 15 ℃ at night. The system still works in the same logic and starts the heating process when it is below 15 ℃.
PH Balancing: The PH balance of the water directly affects the quality and life of the plant. Although the optimum pH ratio varies from plant to plant, it is in the range of 5-8 on average. Two tanks, Acidic and Basic, were used for this process. If the PH value rises above 8, malic acid is transferred from the acidic tank to the water tank. The transfer is made with solenoid valves and nozzles. As seen in Fig. 7, the transfer is made from Red (acidic) and Blue (basic) tanks.
Fertilizer-Pesticide tanks: Spraying and fertilizing are done with the blue and brown tanks shown in Fig. 7. In these tanks, fertilizers and pesticides are in liquid solution forms, so they can be mixed with water easily and homogeneously. Release to the water tank is again provided by nozzles and solenoid valves. Malic Acid is used to acidify the water, and Potassium Hydroxide solution is used to make it basic.
Fig. 7PH and fertilizer-pesticide tanks
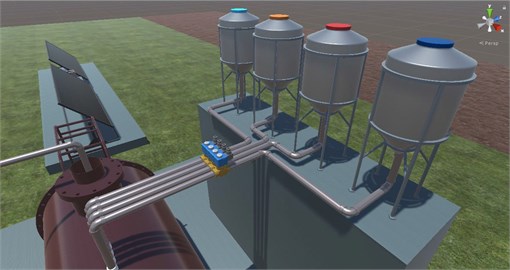
4. Conclusions
Although automation has become widespread in many areas of the world, automation systems are not widely used in greenhouse systems especially in Turkey. In this study, it is aimed to make greenhouse cultivation more qualified, efficient and sustainable with the potential of automation systems in this field. In this study, a greenhouse automation system that can produce better quality and healthy products has been put forward with the objectives such as making the system fully automatic, minimizing the workload and the human error rate, predicting how the system will behave under different conditions with system simulation.
References
-
D. L. Critten and B. J. Bailey, “A review of greenhouse engineering developments during the 1990s,” Agricultural and Forest Meteorology, Vol. 112, No. 1, pp. 1–22, Jul. 2002, https://doi.org/10.1016/s0168-1923(02)00057-6
-
L. Zhou, C. J. Tucker, R. K. Kaufmann, D. Slayback, N. V. Shabanov, and R. B. Myneni, “Variations in northern vegetation activity inferred from satellite data of vegetation index during 1981 to 1999,” Journal of Geophysical Research: Atmospheres, Vol. 106, No. D17, pp. 20069–20083, Sep. 2001, https://doi.org/10.1029/2000jd000115
-
I. Seginer and I. Zlochin, “Night-time greenhouse humidity control with a cooled wetness sensor,” Agricultural and Forest Meteorology, Vol. 85, No. 3-4, pp. 269–277, Jul. 1997, https://doi.org/10.1016/s0168-1923(96)02387-8
-
U. Çebi, B. Aydin, S. Özer, and O. Öztürk, “Effect of irrigation waters in different salinity levels on crop yield and energy use in greenhouse tomato production in turkey: a case study in Kırklareli province,” Horticultural Studies, pp. 123–133, Oct. 2020, https://doi.org/10.16882/hortis.810011
-
Ertek A., Şensoy S., Yıldız M., and Kabay T., “Determination of the most suitable irrigation dose and interval for eggplant plant in greenhouse conditions by using open water surface evaporation,” Kahramanmaras Sutcu Imam University Journal of Engineering Sciences, Vol. 5, pp. 57–67, 2002.
-
R. Tawegoum, R. Teixeira, and G. Chassériaux, “Simulation of humidity control and greenhouse temperature tracking in a growth chamber using a passive air conditioning unit,” Control Engineering Practice, Vol. 14, No. 8, pp. 853–861, Aug. 2006, https://doi.org/10.1016/j.conengprac.2004.09.012
-
U. Kanburoğlu Çebi, S. Özer, S. Altintaş, E. Yurtseven, and O. Öztürk, “Farklı Sulama Suyu Kalitesi ve Su Düzeylerinin Serada Yetiştirilen Domates Bitkisinin Verim ve Su Kullanım Etkinliği Üzerine Etkisi,” Harran Tarım ve Gıda Bilimleri Dergisi, Vol. 22, No. 1, pp. 33–46, Mar. 2018, https://doi.org/10.29050/harranziraat.299023
-
Baytorun A. N., Akyüz A., Çaylı A., Üstün, and S., “Investigation of TR63 region climate conditions in terms of greenhouse,” Mustafa Kemal University Journal of Agricultural Sciences, Vol. 24, pp. 91–100, 2019.
-
D. Jain, “Modeling the performance of greenhouse with packed bed thermal storage on crop drying application,” Journal of Food Engineering, Vol. 71, No. 2, pp. 170–178, Nov. 2005, https://doi.org/10.1016/j.jfoodeng.2004.10.031
-
B. Von Elsner et al., “Review of structural and functional characteristics of greenhouses in European union countries, part II: typical designs,” Journal of Agricultural Engineering Research, Vol. 75, No. 2, pp. 111–126, Feb. 2000, https://doi.org/10.1006/jaer.1999.0512
-
Adem Yilmaz and Hikmet Doğan, “Sera İçi Hava Şartlarının Otomasyon Sistemi İle Üretim Kalitesinin Artırılması ile İlgili Bir Çalışma,” Batman Üniversitesi Yaşam Bilimleri Dergisi, Vol. 6, No. 2/2, pp. 145–159, Dec. 2016.
-
T. Rath, “Einsatz wissensbasierter Systeme zur Modellierung und Darstellung von gartenbautechnischem Fachwissen am Beispiel des hybriden Expertensystems HORTEX,” Ph.D. Thesis, Hannover: Institut für Technik in Gartenbau und Landwirtschaft, 1992.
-
K. Daka, A. Gül, and S. Engindeniz, “Production and marketing of tomatoes oriented to export in greenhouses in Muğla.,” Journal of Ege University Faculty of Agriculture, Vol. 49, No. 2, pp. 175–185, 2012.
-
J. Cuartero and R. Fernández-Muñoz, “Tomato and salinity,” Scientia Horticulturae, Vol. 78, No. 1-4, pp. 83–125, Nov. 1998, https://doi.org/10.1016/s0304-4238(98)00191-5