Abstract
The laser welding efficiency of stainless steel is high, but the welding quality is still insufficient. In order to improve the welding performance of stainless steel, a controllable ultrasonic laser welding system was designed in the paper. Through numerical simulation and experimental test, the influences of ultrasonic vibration on the mechanical properties of weld were obtained. For the simulation study, the sound vibration coupling scheme was applied to the welding model. The closed environment model was established, and the characteristic frequency and sound pressure distribution of ultrasonic were simulated and analyzed by COMSOL software. In the aspect of performance test, through the real-time monitoring of the welding system, the effect of ultrasonic on the molten pool area, molten pool flow rate and metal vapor pressure is obtained. Under different ultrasonic excitation frequencies, the changes of weld microstructure, wear morphology, hardness and oxidation were studied. The results show that ultrasonic vibration can significantly improve the wear resistance, hardness and corrosion resistance of stainless steel welds. The ultrasonic energy efficiency at the second-order characteristic frequency is higher, the flow rate in the molten pool is low, and the joint quality is better.
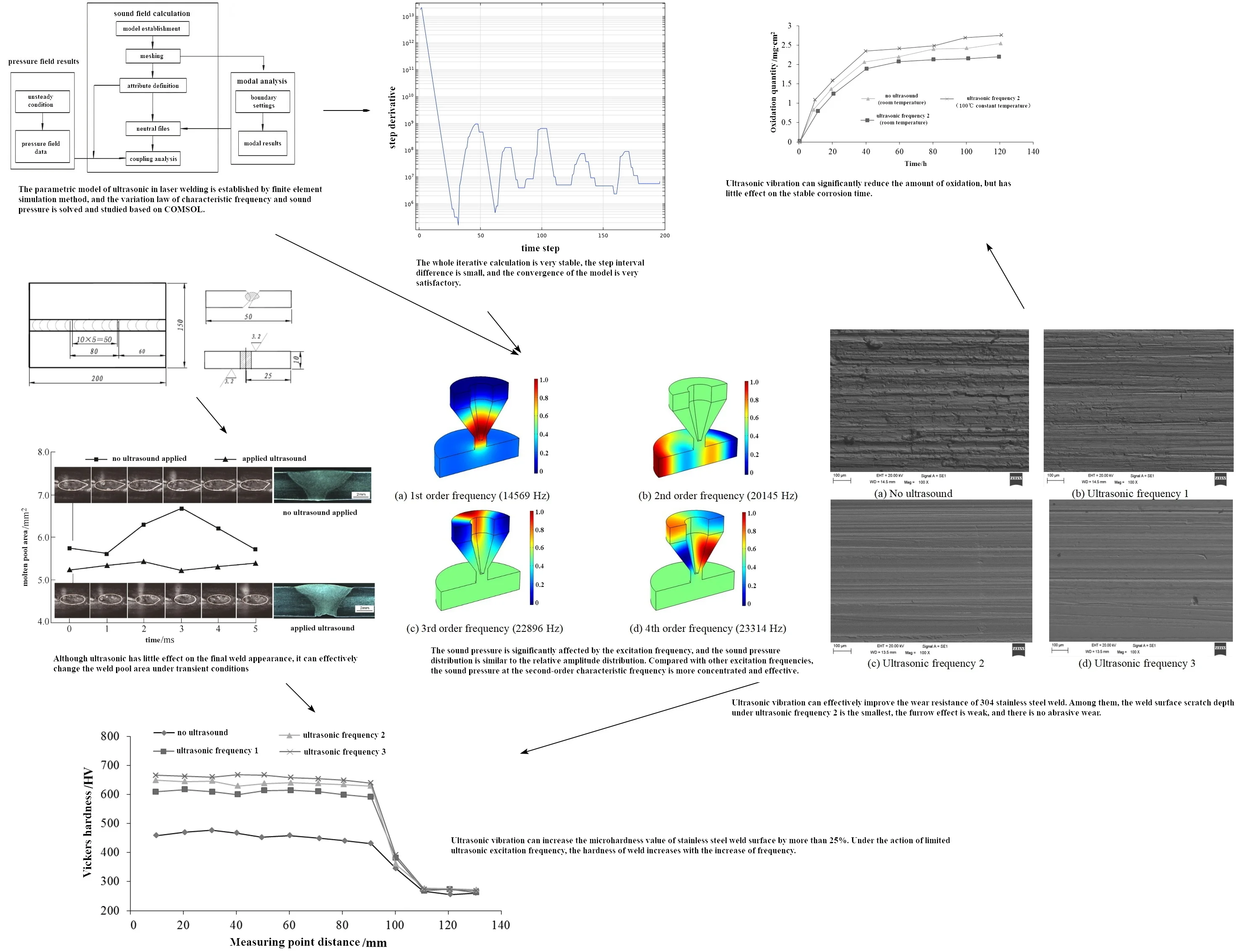
Highlights
- In order to improve the welding performance of stainless steel, a controllable ultrasonic laser welding system was designed.
- The closed environment model was established, and the characteristic frequency and sound pressure distribution of ultrasonic were simulated and analyzed by COMSOL software.
- Through the real-time monitoring of the welding system, the effect of ultrasonic on the molten pool area, molten pool flow rate and metal vapor pressure is obtained.
1. Introduction
Laser welding is a new welding technology, which has the characteristics of fast weld pool forming [1], large welding depth and small thermal deformation. It does not need special environmental conditions, so the industrialization application rate is high. However, in the laser welding process of stainless steel 304, due to the concentrated and large energy of laser heat source and large flow rate of molten pool, it is easy to produce plasma cloud composition when the base metal is heated and melted [2], which makes more small pores and depressions on the weld surface, which not only affects the laser focusing, but also reduces the joint strength. In addition, laser welding will also lead to some problems, such as insufficient hardness of stainless steel weld and relatively poor wear resistance. At present, the application and research of ultrasonic in laser welding are relatively few, mainly focusing on the evaluation of weld quality and mechanical properties. Chen [3] used the single factor test method to study the influence of ultrasonic on weld deformation, and established the best ultrasonic power with the deformation as the optimization goal. Koyanagi [4] studied the effect of ultrasonic vibration base on finite element analyses and the ultrasonic welding of CFRPs were performed by using a two-dimensional model. Goram [5] investigated the performance optimization of ultrasonic welding composite using a poly methyl meth acrylate (PMMA) coupling interlayer. Kalyan [6] studied the welding of carbon fiber reinforced thermoplastic and 6061 aluminum alloy by ultrasonic welding process. According to the principle of ultrasonic laser welding, ultrasonic vibration mainly improves the weld performance by affecting the state of molten pool. In view of the above problems, the combination of numerical simulation and experimental test is proposed to study the dynamic characteristics of sound field and its influence on the mechanical properties of weld, which provides an important basis for the optimization of laser welding process of stainless steel.
2. Vibration simulation of ultrasonic sound field
2.1. Model establishment
The propagation rate of ultrasonic wave is greatly affected by temperature [7], and it can still maintain a stable wavelength in a closed environment. Therefore, the parametric model of ultrasonic in laser welding is established by finite element simulation method, and the variation law of characteristic frequency [8, 9] and sound pressure is solved and studied based on COMSOL. Due to the remarkable reflection of ultrasonic wave, the simulation and calculation are carried out in the way of sound vibration coupling. Its process and principle are shown in Fig. 1. Considering that the ultrasonic vibration can significantly affect the sound pressure, the scheme has high calculation accuracy.
Fig. 1Flow chart of coupling simulation
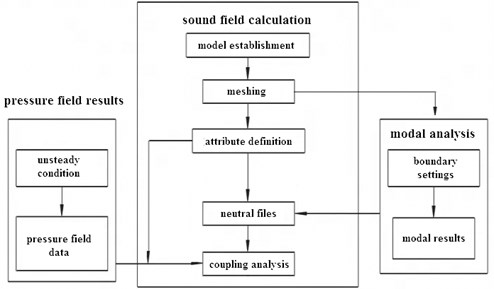
According to the physical properties of ultrasonic, under the condition of specific ultrasonic frequency, when the wavelength meets a certain size relationship with the propagation space, the standing wave mode [10] will appear. At this time, the characteristic frequency can be calculated accurately. Combined with the characteristics of 304 stainless steel laser welding process, the sound field simulation model is established, as shown in Fig. 2, including strong sound field area, sub strong sound field area and weak sound field area. In ICEM software, the model is meshed, the numerical calculation in the boundary layer is considered, and the perfect matching layer and absorption layer in the grid are distinguished to avoid the sound wave on the boundary being reflected and reduce the error interference. For the mesh generation of perfect matching layer, set the calculation width as 0.5-1 times of the wavelength, and define its equal fraction in the radial direction as 50. For the absorption layer, the minimum cell size is 0.12 mm according to the structural size of the laser beam emitting end, and the final meshing result is shown in Fig. 3.
Fig. 2Composition of ultrasonic sound field model
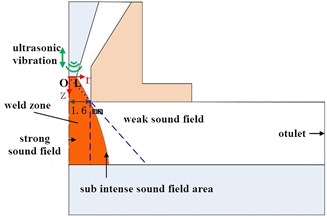
Fig. 3Meshing results
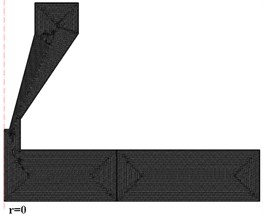
The analysis type of transient model is the display calculation based on convective wave equation, and the core algorithm is discontinuous Galerkin algorithm [11]. The algorithm has low requirements for grid distortion, and only two element grids are needed for calculation in a single wavelength. However, because laser welding is a typical high-temperature environment, it is difficult to achieve convergence under large temperature difference distribution. Therefore, in the preliminary calculation, it is necessary to verify the mesh density of the perfect matching layer. The characteristic frequency distribution of ultrasonic is essentially the instantaneous state of sound field, and the actual amplitude cannot be obtained. Only by determining the actual impedance law of ultrasonic, can the specific amplitude be solved. Different from the time domain analysis, the frequency domain analysis of ultrasonic field is the distribution law of stable sound field, which reflects the final response result, and the amplitude is the relative amplitude. In the calculation of frequency domain characteristics, the governing equation of sound pressure is:
where pt is the total sound pressure field, ρ0 is density field, qd is the dipole source vector, c is ultrasonic velocity, ω is ultrasonic emission frequency, and Qm is the monopole source.
Sound velocity is one of the most typical characteristics of ultrasonic finite element model, and its boundary condition in the model is defined as:
where n is the direction vector under the condition of constant background velocity and density, c0 is the instantaneous ultrasonic velocity vector, f is the characteristic frequency and Av is the amplitude.
The convergence diagram in the simulation process is shown in Fig. 4. It can be seen that the whole iterative calculation is very stable, the step interval difference is small, and the convergence of the model is very satisfactory.
Fig. 4Convergence diagram in simulation process
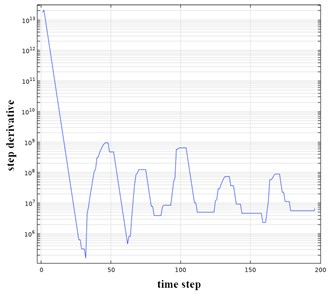
2.2. Characteristic frequency analysis
In COMSOL, the sound field state at different characteristic frequencies can be solved based on Helmholtz equation, and the relative amplitude can be normalized. According to the emission range of ultrasonic excitation frequency, the results of extracting the first four steps are shown in Fig. 5. It can be seen that at the first-order characteristic frequency, the maximum relative amplitude is close to the laser emission center, and the ultrasonic propagation is obviously restrained under the influence of the structure of the laser head. The standing wave energy generated by the second-order sound field is less, and the sound field separation in the weld area is large. Although the weld area is close to the sound source, the relative amplitude is small, and the traveling wave plays a leading role. The distribution of the third-order sound field is similar to that of the fourth-order sound field, which is dominated by the standing wave, and there is relatively large amplitude at the tip. It can be seen that when the ultrasonic wave works at the second-order characteristic frequency, it can achieve better weld excitation effect.
Fig. 5Relative amplitude distribution at different characteristic frequencies
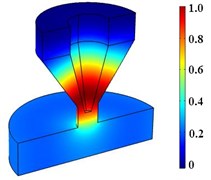
a) 1st order frequency (14569 Hz)
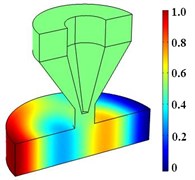
b) 2nd order frequency (20145 Hz)
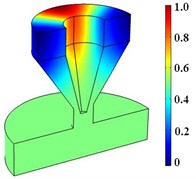
c) 3rd order frequency (22896 Hz)

d) 4th order frequency (23314 Hz)
2.3. Sound pressure distribution law
Because the ultrasonic emission model is a semi closed structure, the ultrasonic will be output after multiple reflections and superposition in the transmitting cavity of the horn. At this time, the output ultrasonic sound pressure will be distributed in a complex state, which has an important impact on the weld pool. Through the simulation analysis, the cloud diagram of sound pressure distribution under the first four characteristic frequencies can be obtained, as shown in Fig. 6.
Fig. 6Sound pressure distribution at different characteristic frequencies
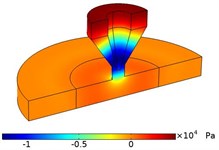
a) 1st order frequency (14569 Hz)
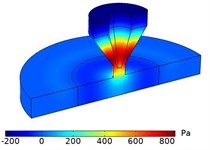
b) 2nd order frequency (20145 Hz)
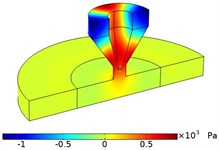
c) 3rd order frequency (22896 Hz)
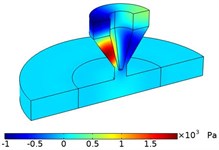
d) 4th order frequency (23314 Hz)
It can be seen that since the sound pressure at the outlet of the ultrasonic transmitting cavity is determined by the initial pressure, reflection pressure and reverberation pressure, the closer to the central axis, the greater the value of sound pressure. The sound pressure is significantly affected by the excitation frequency, and the sound pressure distribution is similar to the relative amplitude distribution. Compared with other excitation frequencies, the sound pressure at the second-order characteristic frequency is more concentrated and effective.
3. Analysis of ultrasonic laser welding process
3.1. Welding system design
In order to accurately test the dynamic characteristics of laser welding pool, the welding system is designed properly and innovatively in the paper, including laser welding system, data acquisition system and ultrasonic control system, as shown in Fig. 7. Through the adjustment of ultrasonic vibration parameters, the comparative results of flow response of 304 stainless steel pool can be obtained. The data acquisition system can realize the transmission of signals and instructions based on PCI data card, and feed back to the laser welding system with the application of LINKS - 11S01 linker to realize precise control of welding current, flow rate of shielding gas (Argon), and trajectory of laser welding gun. The working parameters of ultrasonic power supply and transducer can be effectively adjusted by ultrasonic control system, so as to realize the control of ultrasonic vibration frequency and amplitude. The ultrasonic excitation power supply with the maximum frequency of 500 kW is used for the ultrasonic excitation system. Through the ultrasonic laser welding system, the image acquisition of weld pool under different ultrasonic vibration frequencies [12], the real-time monitoring of weld pool flow rate, metal vapor pressure and other data can be tested simultaneously, which provides an important basis for the application efficiency of ultrasonic vibration in laser welding.
Fig. 7Composition of ultrasonic vibration laser welding system
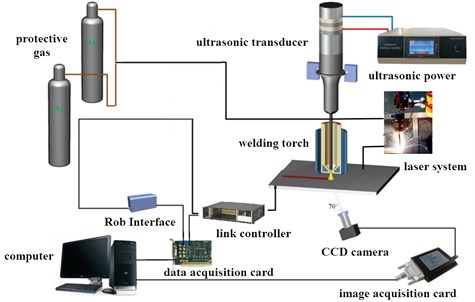
3.2. Process parameter design
In order to improve the balance of energy and shielding gas flow, the inclination angle of laser welding gun is set to 10°, the included angle between welding wire and base metal is set to 15°, and the direction of argon flow rate is set to 45°. The motion control of the welding gun is realized based on the stepping motor, and except for the welding gun, other auxiliary mechanisms remain stationary in the working face. According to the welding procedure qualification standard, the base metal of stainless steel is processed into standard welding samples, as shown in Fig. 8. At the same time, the main parameters of its laser welding process are set as shown in Table 1.
3.3. Welding effect of ultrasonic vibration
According to the sound field simulation results of ultrasonic laser welding, the second-order characteristic frequency is more conducive to the improvement of energy efficiency. In order to better study the welding effect, the ultrasonic frequency is set to 20145 Hz.
Fig. 8Weld sample processing scheme
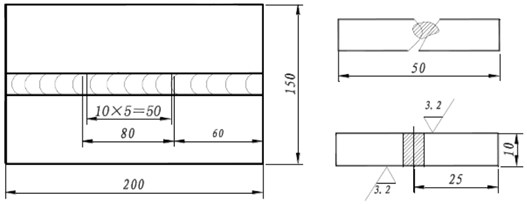
Table 1Process parameter setting
Parameter type | Numerical value | Error range |
Laser power / W | 1500 | 5.0 % |
Focal length / mm | 189 | 2.0 % |
Spot diameter / mm | 2.5 | 2.0 % |
Welding gun speed / mm·min-1 | 900 | 2.5 % |
Welding wire speed / mm·min-1 | 1000 | 1.0 % |
Protective gas flow / L·min-1 | 20 | 3.5 % |
Through the image monitoring of 304 stainless steel weld during the welding process, the transient weld pool area is obtained, as shown in Fig. 9. It can be seen that although ultrasonic has little effect on the final weld appearance, it can effectively change the weld pool area under transient conditions [13]. The maximum weld pool area of conventional laser welding is 6.68 mm2, and the fluctuation range is 18.3 %. Under the influence of ultrasonic vibration, the maximum molten pool area is reduced to 5.38 mm2 and the fluctuation range is reduced to 3.9 %. It can be seen that ultrasonic vibration can effectively improve the stability of molten state of stainless steel weld pool, is conducive to full solidification and crystallization, and effectively reduce the probability of small pores and depressions.
Fig. 9Variation law of transient molten pool area
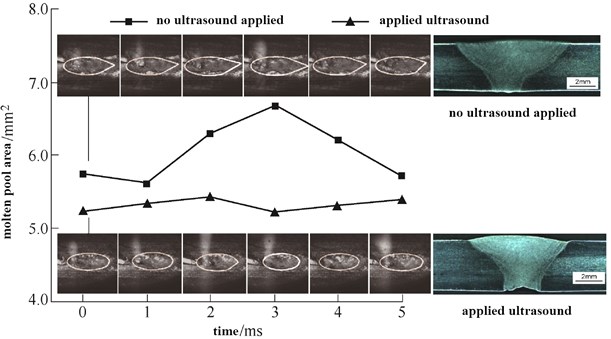
At different positions away from the center of the weld, the distribution laws of molten pool flow rate and metal vapor pressure at 1 s can be measured, as shown in Fig. 10 and Fig. 11 respectively. It can be seen that the flow velocity of 304 stainless steel weld pool in the weld center decreases significantly after ultrasonic wave is applied. When it exceeds ± 2 mm from the weld center, the ultrasonic wave has little effect on the flow velocity of the molten pool. The distribution of steam pressure is opposite to the flow velocity of molten pool. When it is far away from the weld center, ultrasonic vibration will significantly increase the steam pressure. With the decrease of the distance from the weld center, the effect of ultrasonic on metal vapor pressure is no longer obvious. It can be seen that ultrasonic vibration can enhance the curing effect of the center of the molten pool and improve the thermal stability of the central weld away from the heat source.
Fig. 10Distribution of maximum flow velocity
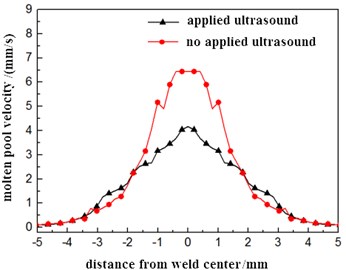
Fig. 11Distribution of metal vapor pressure
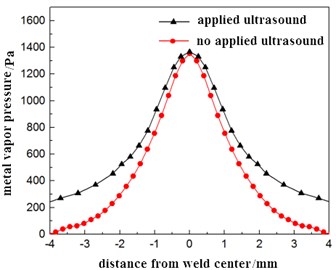
4. Effect of ultrasonic frequency on weld properties
4.1. Metallographic structure analysis
In order to study the effect of ultrasonic frequency on the mechanical properties of weld, laser weld samples of stainless steel were prepared at the first-order (ultrasonic frequency 1), second-order (ultrasonic frequency 2) and third-order (ultrasonic frequency 3) characteristic frequencies respectively. The metallographic structure of the weld sample is shown in Fig. 12.
Fig. 12Metallographic structure of weld under different ultrasonic frequencies
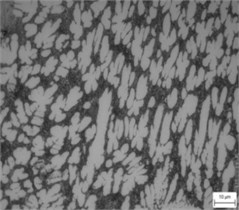
a) No ultrasound
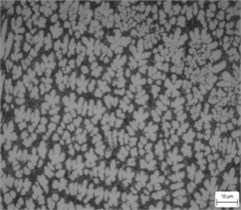
b) Ultrasonic frequency 1

c) Ultrasonic frequency 2
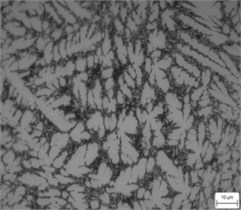
d) Ultrasonic frequency 3
It can be seen that ultrasonic has a significant effect on the microstructure morphology. The grain size under ultrasonic frequency 1 and ultrasonic frequency 2 is smaller than that without ultrasonic vibration. The grain size under ultrasonic frequency 3 is relatively coarse, and ferrite is evenly distributed around pearlite in the form of blade. The grain shape under the condition of ultrasonic frequency 2 is more similar to that without ultrasonic vibration. However, due to the small flow rate of the molten pool and the high pressure of the surrounding metal vapor, the possibility of splashing in the molten pool is greatly reduced, so the uniformity of the weld thickness direction is effectively improved.
In order to study the effect of ultrasonic on the wear resistance of 304 stainless steel weld, constant speed friction test was carried out on weld samples under different ultrasonic frequencies. The normal load of the friction pair is defined as a constant value of 150 N, and the relative angular velocity of the pin disc is set as 6 rad/s under the condition of dry friction. Finally, the wear morphology is obtained, as shown in Fig. 13. It can be seen that ultrasonic vibration can effectively improve the wear resistance of 304 stainless steel weld. Among them, the weld surface scratch depth under ultrasonic frequency 2 is the smallest, the furrow effect is weak, and there is no abrasive wear.
Fig. 13Metallographic structure of weld under different ultrasonic frequencies
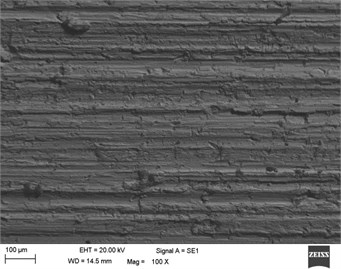
a) No ultrasound
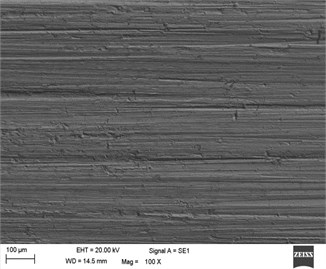
b) Ultrasonic frequency 1
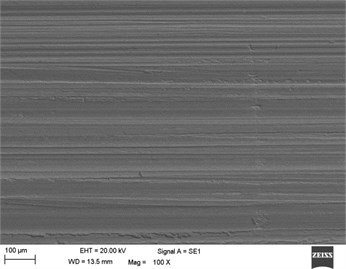
c) Ultrasonic frequency 2
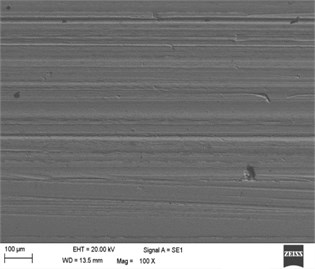
d) Ultrasonic frequency 3
4.2. Microhardness and corrosion resistance analysis
Hardness is one of the important indexes to measure the comprehensive mechanical properties of weld. Through the HVS-5Z microhardness tester, the hardness distribution under different ultrasonic frequencies can be obtained, as shown in Fig. 14. It can be seen that ultrasonic vibration can increase the microhardness value of stainless steel weld surface by more than 25 %. Under the action of limited ultrasonic excitation frequency, the hardness of weld increases with the increase of frequency. Generally, the increase of hardness will improve the strength and wear resistance of materials, and the probability of insufficient toughness will also increase. Therefore, the compromise value is preferred in engineering to meet good comprehensive properties.
According to these test results, it can be known that the second-order characteristic frequency of ultrasonic can effectively improve the mechanical properties of 304 stainless steel weld. In order to verify its influence on corrosion resistance, the three weld samples were placed in the acidic environment with constant temperature of room temperature and 100 ℃ respectively, and the change law of oxidation amount was tested, as shown in Fig. 15. It can be seen that ultrasonic vibration can significantly reduce the amount of oxidation, but has little effect on the stable corrosion time. After 40 hours, the oxidation amount of the weld under different test environments reached a stable state, which shows that the corrosion resistance of the weld is more affected by the physical properties of the material itself.
Fig. 14Microhardness distribution under different ultrasonic frequencies
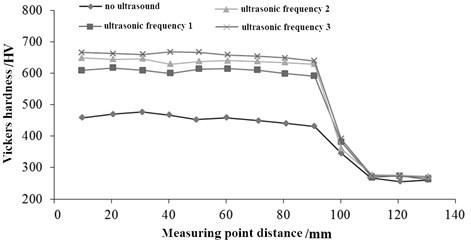
Fig. 15Variation law of weld oxidation
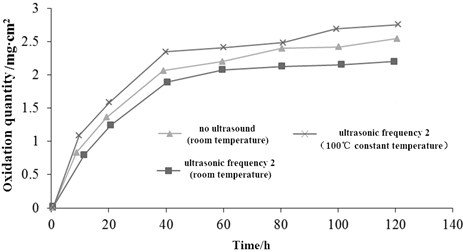
5. Conclusions
In various engineering fields, the mechanical properties and corrosion resistance of stainless steel are good, but its welding process is relatively poor, and the conventional welding scheme is difficult to obtain the ideal effect. Therefore, it is proposed to increase the influence of ultrasonic vibration. In order to improve the reliability of sound field calculation results, considering the influence of mode on ultrasonic pressure field, the acoustic vibration coupling method is innovatively proposed for finite element analysis. In addition, a multi-functional image detection experimental platform is designed and built. Combined with metallographic analysis, the improvement effect of ultrasonic on weld performance can be effectively verified. The research shows that ultrasonic vibration can significantly improve the transient characteristics of stainless steel laser welding pool, reduce the flow rate of weld pool in the center of the weld, increase the surrounding metal vapor pressure, and improve the balance and stability of the weld. Compared with laser welding without ultrasonic, the probability of weld pool splash, small pores and depression is greatly reduced. In this welding system, the second-order excitation frequency of ultrasonic (20145 Hz) can achieve higher energy efficiency in the weld area. Under the influence of ultrasonic vibration at this frequency, the wear resistance, surface hardness and corrosion resistance of the weld are significantly improved. With the development of automation technology, there are more and more efficient welding assembly line production modes. It is a necessary requirement for engineering manufacturing industry to obtain higher production quality in the shortest time. Through the research of this paper, it can be seen that improving the welding quality from the aspect of ultrasonic vibration can significantly improve the economic benefits of products.
References
-
C. An, Y. M. Zhang, and J. S. Zhang, “Experimental study on density and pore defects of CO-Cr alloy formed by selective laser melting,” (in Chinese), Applied Laser, Vol. 38, No. 5, pp. 730–737, 2018.
-
S. H. Zhang and W. X. Yang, “Detection and analysis of plasma in laser deep penetration welding,” (in Chinese), Applied Laser, Vol. 37, No. 6, pp. 847–851, 2021.
-
G. Y. Chen, D. Y. Jiang, and B. Wang, “Study on deformation control of 6061 aluminum alloy ultrasonic assisted laser welding,” (in Chinese), Laser Technology, Vol. 45, No. 5, pp. 541–547, 2021.
-
J. Koyanagi, M. Takamura, K. Wakayama, K. Uehara, and S. Takeda, “Numerical simulation of ultrasonic welding for CFRP using energy director,” Advanced Composite Materials, Vol. 31, No. 4, pp. 428–441, Jul. 2022, https://doi.org/10.1080/09243046.2022.2031376
-
G. Gohel, C. Z. Soh, K. F. Leong, P. Gerard, and S. K. Bhudolia, “Effect of PMMA coupling layer in enhancing the ultrasonic weld strength of novel room temperature curable acrylic thermoplastic to epoxy based composites,” Polymers, Vol. 14, No. 9, p. 1862, May 2022, https://doi.org/10.3390/polym14091862
-
R. Kalyan Kumar and M. Omkumar, “Investigation of ultrasonic welding of carbon fiber reinforced thermoplastic to an aluminum alloy using a interfacial coating,” Materials and Manufacturing Processes, Vol. 36, No. 11, pp. 1323–1331, Aug. 2021, https://doi.org/10.1080/10426914.2021.1905839
-
X. H. Shao, Z. C. Lu, and Z. Wang, “Temperature compensation algorithm for flow metering based on least square surface fitting,” (in Chinese), Chinese Journal of Sensors and Actuators, Vol. 29, No. 6, pp. 897–902, 2016.
-
P. C. Jena, D. R. Parhi, and G. Pohit, “Dynamic investigation of FRP cracked beam using neural network technique,” Journal of Vibration Engineering and Technologies, Vol. 7, No. 6, pp. 647–661, Dec. 2019, https://doi.org/10.1007/s42417-019-00158-5
-
L. Zhou and M. Song, “Stability of cracked functionally graded graphene-reinforced beams under magnetic field,” Journal of Scientific Research and Reports, Vol. 28, No. 4, pp. 14–24, Apr. 2022, https://doi.org/10.9734/jsrr/2022/v28i430511
-
J. Y. Li and Q. Ye, “Discussion and Analysis on measurement method of ultrasonic propagation velocity,” (in Chinese), Physical Experiment of College, Vol. 34, No. 3, pp. 55–58, 2021.
-
H. Zhou, B. Zhang, and Q. B. Feng, “Numerical study on ultrasonic defect detection excited by annular light source,” (in Chinese), Laser Technology, Vol. 45, No. 2, pp. 168–173, 2021.
-
W. G. Chen, “Research on vision laser metal plate welding system and its application,” (in Chinese), Applied Laser, Vol. 40, No. 4, pp. 672–676, 2020.
-
P. Charan Jena, “Identification of crack in SiC composite polymer beam using vibration signature,” Materials Today: Proceedings, Vol. 5, No. 9, pp. 19693–19702, 2018, https://doi.org/10.1016/j.matpr.2018.06.331
About this article
The paper is supported by National Nature Science Foundation of China (61873136) and scientific research project named Research on Moving Workpiece Recognition and Robot Grasping Intelligent Control Based on Binocular Stereo Vision (2020KJ03).
The datasets generated during and/or analyzed during the current study are available from the corresponding author on reasonable request.
The authors declare that they have no conflict of interest.