Abstract
The article discusses history of technical diagnostics and repair organization in industry in Russia. The history of formation of the principles of repair, which were further formed into a system of preventive and planned repairs, is considered. At one of the stages of industrial development and the formation of repair organization systems, it became necessary to develop technical diagnostics of machines and equipment that can be carried out on working equipment. The main reasons and key points at various stages of the formation of technical diagnostics and repair organization are considered.
1. Introduction
It is hard to say now, when technical diagnostics of machines and equipment was born, since any kind of mechanism sooner or later fails and requires repair, therefore development proceeded systematically. The first stage of industrial revolution happened in the 60s of the 18th century, when distribution of new working machines in English textile industry was began. Perhaps, this moment of history is the starting point for development of technical diagnostics and repair of machines.
Around the same time more complex equipment such as steam-engines was created. Polzunov I. I. designed the “fire-working machine” in April 1763 and the “machine” was made in 1765. James Watt patented a new type of steam engine in 1769, further in 1784 he created “double-acting steam engine”, which was placed at factory in 1785 for the first time. However, diagnostics and repair of first engines was performed spontaneously, and, in fact, maintenance was carried out by the same people who worked on it.
2. Stages of development of technical diagnostics
The industrial revolution enabled the introduction of new machines and equipment in various areas. Steam fleet in the Crimean War 1853-1856 played an important role in the development of technical diagnostics.
This war is notable for the collision of sailing and steam ships, which showed the advantage of steam engines. During war, operational state of key units (steam engine, steering system, pointing device) was urgently needed. Just then “engine crew” were created to ensuring the operation of machinery and equipment of ships (Fig. 1). At the same time, the need for the specialists become clear.
The organized system of inspections and actions become the basis of technical diagnostics. In particular, key equipment had been expected every shift, day, week and month. The repair system was created: emergency repair, maintenance, and overhaul.
The beginning of 20th century characterized by intensive progress of technic in various industries, development and implementation of various equipment and machines [1]. It created a need for the development for methods of repair and technical diagnostics of machines.
In the 20s, the repair business began to play a significant role in new machine development. Principles of preventive and planned repair were being created and introduced everywhere. Repair shops and workshops were begun to organized in the late 1920s and early 1930s. The use of equipment began to systematize specifically the record of standing and working equipment. Then the firs elements of future preventive and planned repair system appeared, for instance sequencing repairs with information of key units’ life time. The condition of the equipment was assessed based on periodic inspections, and the timing, types, and scope of repairs were planned.
Fig. 1“Aurora” cruiser’s mechanical engineers and engine crew
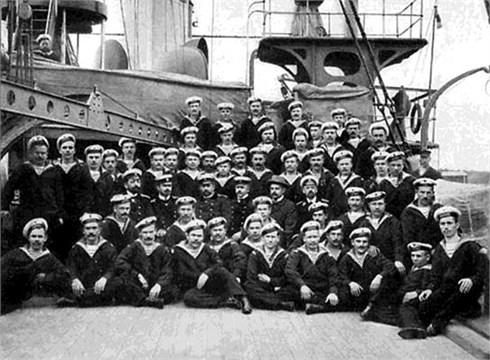
The first publication on the organization of repairs was the work of Popov A. G. in 1927 [2], theme was further developed in the form of work “Rationalization of the repair business at the factory” [3]. In the development of Popov’s A. G. labor, Spiridonov V. V. was engaged in the rationalization of the repair of factory equipment. He published a brochure [4], and later in 1932 published the work in which the term “planned preventive maintenance” first appears [5] (Fig. 2).
In the works of Popov A. G. and the works of Spiridonov V. V. the organization of repairs was carried out through the prism of determining the life of equipment elements, the manufacture of spare parts and timely replacement. By the established deadlines for the repair, it was planned to manufacture the necessary parts. This strategy is called the post-inspection repair system. The disadvantage of such a system was the lack of clear standards and the difficulty of planning repairs and preparing spare parts for a long period.
It should be noted that at that time, other methods for assessing the technical condition, in addition to visual, began to be used. Namely, there was a bearing temperature control and an acoustic control method, which was consisted in noise control with a stethoscope.
In the mid-1930s, the System of standard repairs (or the System of forced repairs) was organized. It was based on the withdrawal of equipment for repair at the scheduled time, regardless of the state during which the forced replacement of certain parts was carried out. At the same time, the terms of forced replacement of parts were established on the basis of an estimate of the service life of parts obtained on the basis of a study of their wear.
In 1934 Y. S. Borisov and G. P. Zhukov developed a system of scheduled preventive periodic repairs [6], called the “System of periodic repairs” (and further developed in the work “The system of periodic repairs of equipment of machine-building enterprises” [7]). According to this system, various types of repair were sequentially repeated and form a repair cycle. Scheduled repairs were carried out periodically after a given number of hours. And within the cycle formed by periodic scheduled repairs, each piece of equipment was subjected to scheduled checks, called inspections. During the checks, minor defects were eliminated, adjustments and cleaning were performed, and a list of components and parts that should have been prepared for replacement during the next scheduled repair was determined.
Fig. 2One of the first works in the field of preventive maintenance [5]
![One of the first works in the field of preventive maintenance [5]](https://static-01.extrica.com/articles/22706/22706-img2.jpg)
Fig. 3The Unified System of Scheduled Preventive Maintenance of Equipment, which was mandatory for all enterprises
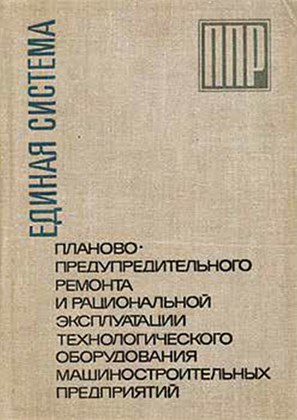
In 1941-1945 the structure of repair cycles was complicated and their duration increased, namely, additional scheduled current and medium repairs were introduced, and, accordingly, the period between major repairs was increased. For equipment which long-term repairs were unacceptable, planned repairs were carried out at different times per node.
In 1945-1948, the preventive scheduled repair system was widely recognized and was introduced by various machine-building ministries and industrial enterprises. In 1955, the Unified System of Scheduled Preventive Maintenance of Equipment, which was mandatory for all enterprises of the country, began to operate. The system provided for the transition from the normative piecework system of remuneration of repair workers to a time-based bonus system with indicators: plan implementation, reduction of equipment downtime, absence of accidents through the fault of repair workers (Fig. 3). In subsequent years, until 1987, a moderate gradual improvement of individual elements of this system occurred.
In these years, the industry has developed with great strides and more and more complex and responsible equipment has been developed and introduced. The preventive scheduled repair system used at that time was already showing its disadvantages. In particular, the repair of expensive and important equipment became more and more difficult. Replacing expensive, but still workable elements of machines became less and less economically rational. It became logical to extend the assigned service life according to the current technical condition. But this approach required both a deeper assessment of the technical condition, and a more operational one. It was necessary to develop methods that would be informative, including without stopping the operation of the equipment, and allow assessing the condition of the equipment and the need for repair. This led to the creation of technical diagnostics.
In the development of technical diagnostics, it is worth noting the contribution of the Soviet scientist and engineer P. P. Parkhomenko (Fig. 4). In 1955, he was admitted to the laboratory of the remote control IAT of the USSR Academy of Sciences, where he studied the structural theory of relay devices, the theory of finite-state machines, problems of analysis and synthesis of circuits. He formulated the subject of research, the basic concepts and tasks of technical diagnostics, determined its place and connection with the theory of control and control, with the theory of reliability and forecasting. In 1964, at the IAT of the USSR Academy of Sciences, on the initiative of Parkhomenko P. P. and under his leadership a new laboratory of logical machines was formed, where he became the initiator and author of the first developments in our country of universal equipment for automated control of complex products in the conditions of their production and operation. The equipment was used in industry. The developments attracted attention and intensified the solution of control automation problems in various areas of the economics [8]. In 1969 Parkhomenko P. P. published one of the first widely known works on technical diagnostics[9].
Fig. 4Parkhomenko Pavel Pavlovich, who made a great contribution to the development of technical diagnostics and the first alarm control systems in the country
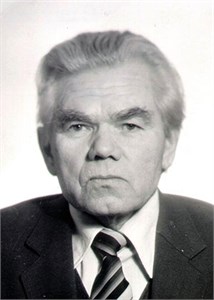
In 1964, the Research Institute of Introscopy was established with the aim of developing the theoretical foundations and creating methods and tools for intravision in opaque bodies and media. Klyuev V. V. made a great contribution to the development of the institute. (Fig. 5), who established a scientific school for non-destructive testing and technical diagnostics, and gradually the institute became a leading enterprise in these fields. One of his first well-known works is “Instruments for non-destructive testing of materials and products” [10], published in 1976 (Fig. 6). We note that the institute exists to this day in the person of RIIN “SPEKTR”, and is the leading enterprise in the country in the field of non-destructive testing and technical diagnostics.
It is also important to note the major scientific work “Non-Destructive Testing” in 8 volumes under the general editorship of Klyuev V. V. [11], which combines information about various types of control.
Fig. 5Klyuev Vladimir Vladimirovich, who had a significant impact on the development of non-destructive testing and technical diagnostics in the country
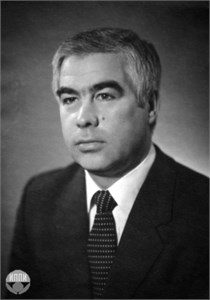
In the 1970s, diagnostic approaches based on “hardware (or physical) redundancy” methods were formed, which use additional sets of sensors, actuators, computers and software to measure and/or control individual variables. In the distribution of this method in 1976, the books “Technical Diagnostics of Digital Devices” [12] (Fig. 7) and “Fundamentals of Technical Diagnostics. Book 1 - models of objects, methods and algorithms of diagnosis” [13], which have become widely known among specialists.
Fig. 6Significant work in the field of non-destructive testing, published in 1976
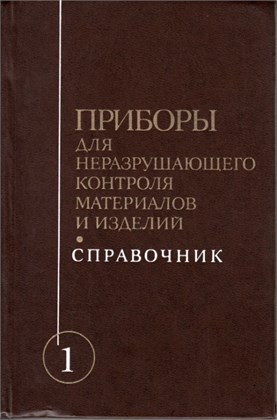
Fig. 7“Technical diagnostics of digital devices” (1976), which described the principles of hardware redundancy in technical diagnostics
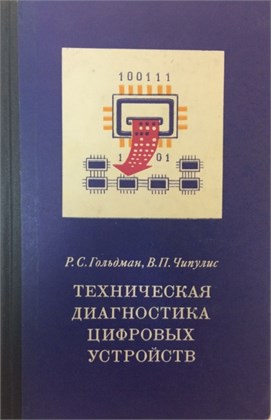
Until the mid-1980s, to assess the technical condition of machines and equipment during its operation (namely, without stopping and development), only the visual method and the acoustic method (namely, the “auditory” method using various types of phonendoscopes) remained common. The visual method is obviously too limited for assessing the condition of the equipment, and the mentioned acoustic method was highly dependent on the experience and practical skills of the specialist conducting the diagnostics [14]. At the same time, measuring instruments that exceeded the hearing capabilities of a person began to appear in the early 70s. However, at that time they were expensive and difficult to implement.
In 1973, the state standard GOST 18353-73 “Non-destructive testing. Classification of types and methods” [15], which fixed the following types of testing: acoustic testing (ultrasonic method), magnetic testing (magnetic particle flaw detection), testing by penetrating substances, radio wave testing, radiation testing (X-ray method), optical testing, thermal testing, electric control, electromagnetic (eddy current) control, hardness testing. It is a very strange fact, but in this regulatory document, vibration diagnostics, which later became widespread, is not specifically highlighted. This will only be corrected in the 2015 reissue [16].
In the 1980s, vibration diagnostics began to develop. Although it is worth noting that the vibration control algorithm for the overall level of the absolute value of the root mean square value of the vibration velocity amplitude was developed back in 1954 [17].
Vibration diagnostics began to develop simultaneously in two directions. The first is the development of means to measure the vibration parameters, including the development of vibration sensors. The second direction is the development of signal processing methods, evaluation of measurement results, identification of defects, determination of the degree of their danger and residual resource.
In the 1990s, microprocessor technology began to develop rapidly, greatly influenced the possibilities of technical diagnostics. First of all, it affected vibration diagnostics, since it made signal processing and spectral transformation much easier from a technical point of view.
It is noteworthy that the first versions of the automatic vibration diagnostic system were developed as early as 1991 [18], although at that time and to this day, portable vibration diagnostic systems are mainly used.
In the 90s, there was a significant decline in the organization of repairs and the development of technical diagnostics. For example, all-Union and sectoral repair organizations were disbanded for the centralized repair of specialized equipment. The development and improvement of the system of planned preventive maintenance of equipment has stopped or slowed down, which previously provided industrial enterprises with a methodological and regulatory framework. The system of centralized supply of enterprises with equipment, spare parts, repair, tooling and repair materials also collapsed. Due to the negative economic situation, technical diagnostics at many enterprises have receded into the background. Thus, in some areas of technical diagnostics and organization of repairs in industry, development was thrown back by almost 70-80 years.
The repair organization system and technical diagnostics have been preserved in large enterprises and in responsible industries, such as oil and gas, petrochemical, energy, etc.
3. Conclusions
Analyzing the most important stages of the organization of repairs and technical diagnostics, and evaluating the current problems and demands of the industry, it is possible to predict what they will become in the near future.
The decline in the economy in the 90s, and in particular in the field of technical diagnostics, undoubtedly had a negative impact on the industry. On the other hand, the lack of diagnostics at existing sites allows us to have the potential to introduce modern principles of technical diagnostics at a new level. In the context of the development of digitalization, big-data, cheaper electronic components, the Internet of things, the development of neural networks, it is predicted that in the near future there will be significant automation and optimization of equipment operation. And the introduction of new methods and principles of technical diagnostics can happen quickly and efficiently.
References
-
Sukharkov Igor Nikolaevich, “Formation of a competitive technical service for ensuring the performance of mining and transport equipment: dissertation,” (in Russian), Technical Sciences, 2018.
-
Popov A. G., “Accounting and renewal of spare parts of factory equipment through mechanical repair shops,” (in Russian), System and Organization, Vol. 8-9, pp. 5–15, 1927.
-
Popov A. G., Rationalization of the Repair Business at the Plant. (in Russian), GNTI, 1931.
-
Spiridonov V. V., Rationalization of Factory Equipment Repair. (in Russian), 1931.
-
Spiridonov V., “For preventive maintenance,” (in Russian) in Rationalization Sector of the Club of the Russian National Economy named after Dzerzhinsky, NKTP, 1932.
-
Borisov Yu. S. and Zhukov G. P., “Technique for planning repairs of factory equipment by the method of reduction to conventional units of repair complexity,” (in Russian), Organization of Production, Vol. 9, pp. 16–21, 1934.
-
Borisov Yu. S. and Zhukov G. P., The System of Periodic Repairs of Equipment of Machine-Building Enterprises. (in Russian), Oborongiz, 1939.
-
Covid-19 Spares No One. The scientist of the Russian academy of sciences and veteran of the great patriotic War P. P. Parkhomenko, “Scientific Russia,” (in Russian), 2020.
-
Parkhomenko P. P., About Technical Diagnostics. (in Russian), Znanie, 1969.
-
A. S. Borovikov et al., Instruments for Non-Destructive Testing of Materials and Products: a Reference Book in 2 Books. (in Russian), Russia, Moscow: Mashinostroenie, 1976.
-
V. V. Klyuev, “Non-destructive testing,” (in Russian), 2006.
-
R. S. Goldman and V. P. Chipulis, Technical Diagnostics of Digital Devices. (in Russian), Russia, Moscow: Energia, 1976.
-
Parkhomenko P. P., Fundamentals of Technical Diagnostics. (in Russian), Russia, Moscow: Energia, 1976.
-
Shchedrin V. I. and Tatter V. Yu, “Analysis of the development of vibration diagnostics systems and trends in their development,” (in Russian), Omsk Scientific Bulletin, Vol. 10, 2000.
-
GOST 18353-73 Non-destructive testing. Classification of types and methods (in Russian).
-
GOST R 56542-2015 Non-destructive testing. Classification of types and methods (in Russian).
-
Sokolova A. G., Balitsky F. Ya., Ivanova M. A., and Lobanov M. A., “Practical application of the method of multidimensional discriminant analysis of hull vibration of machine equipment for the early detection of hidden defects in gas turbine engines,” (in Russian), Bulletin of Scientific and Technical Development, Vol. 7, p. 14, 2014.
-
Rosenblatt F., The Problem of Introducing Self-Learning Information Systems to Assess the Quality of Manufacturing and Functioning of Machines and Equipment. (in Russian), Russia: St. Petersburg, 2004.
About this article
The reported study was funded by the Russian Science Foundation according to the research project No. 22-29-00970, https://rscf.ru/project/22-29-00970/.