Abstract
Composites are a class of materials that give the desired individual tribological and mechanical characteristics. In composite materials, more than two materials are combined to provide a unique combination of properties. This article describes the tribological and mechanical properties of Al6061 reinforced with Al2O3, found experimentally. This article describes the preparation of Al6061 composites with 5 % Al2O3 (size 50 microns) by stir casting process. The hardness of Al6061 with and without amplification was found out with the help of Rockwell hardness tester for 10 seconds at a load of 100 kg. It was found that the hardness of Al2O3 reinforced Al6061 increases compared to unreinforced Al6061. The characteristics related to wear of Al6061 and the new composite material Al6061+Al2O3 were studied. The “pin on disk” method was used with the variation of load varying from 5N-200N and a speed range of 200-1500. An analysis of the sensitivity of key parameters such as load and speed is also described. The results show that the newly developed composite material has a lesser specific rate of wear.
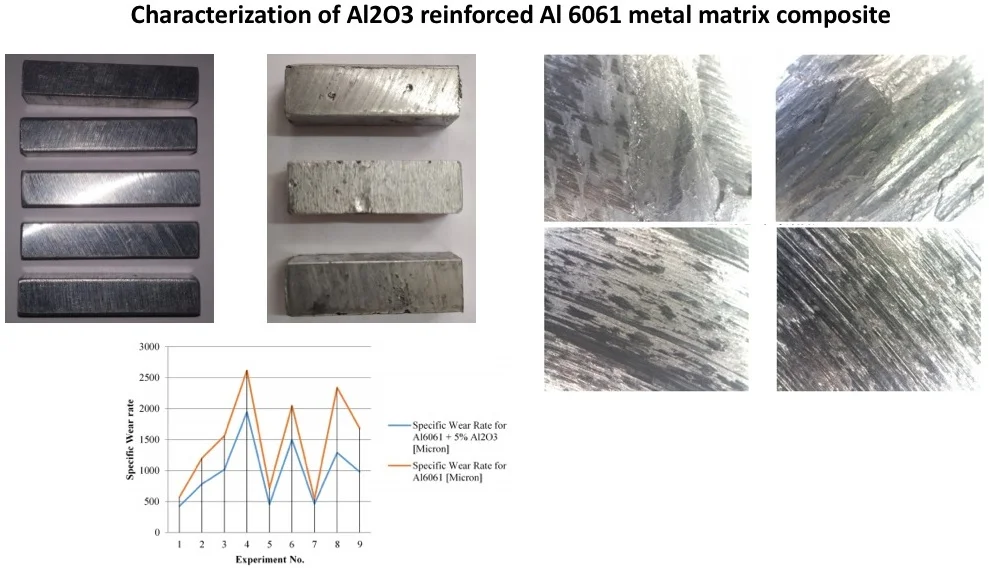
Highlights
- Composite of Al2O3 reinforced Al 6061
- Manufactured with Stir Casting
- Tribological Behavior has been studied
- Hardness Characterisation has been performed
1. Introduction
Engineering and technology development continue to drive the development of engineering materials for a variety of applications such as transportation, aerospace, and military technology. For such applications the development is always needed of lightweight, increased-strength materials with enhances properties of mechanical domain. This is actually accomplished by developing new classes of materials to encounter the complex challenges and properties required for applications in the engineering domain.
Composites are a category of materials that can give the desired individual properties in accordance with mechanical domain. This composite material combines three or more materials to provide a unique combination of properties. For composites, most of the work is devoted to polymer matrix composites, because metal matrix composites (MMC) have processing issues, due to which much of the work is not solved with MMC. Metal Matrix Composites (MMCs) are made from matrices as basic light metals such as magnesium, aluminium and titanium and are reinforced with a variety of ceramic fibres [1-3].
Various manufacturing approaches are castoff to process metal matrix composites, which are mixing/stir casting, powder metallurgy, deposition, infiltration, and diffusion bonding. Choosing appropriate manufacturing methods to cast metal matrix composites will have a significant impact on material properties. The manufacturing method and its process parameters will affect the distribution of reinforcement. That is, the mechanical properties of the material are affected by uniformity, wettability, hardness distribution, density distribution etc. [4].
Stir casting technology is a common technology for manufacturing MMC. In this method, an impeller or stirrer typically made of graphite is used to mix the liquid metal continuously, and then intermittent reinforcing materials are introduced into the matrix. During the operation, the noble gas is injected into the container to avoid chemical reactions. Then pour the mixture into the desired shape [4, 5]. “There are many factors that need wide attention within the manufacture of a material with a metal matrix by casting with mixing, including: (a) the problem in achieving a regular distribution of reinforcing material, (b) wettability between the 2 main materials; (c) the body of the solid metal matrix composite; (d) chemical process between the reinforcing material and also the matrix alloy” [5]. However, the above problems can be solved by effectively managing parameters listed as mixing speed, mixing time, depth of mixing, and feed rate. Adding 1 % magnesium to the foam will reduce the wettability. Inert conditions can be used to reduce the possibility of chemical reactions between components [6-8].
MMC can be made of a variety of strengthening materials, such as titanium dioxide (TiO2), silicon carbide (SiC), boron carbide (B4C), boron nitride (B4N) and alumina (Al2O3). The size of reinforcing material varies from 10 to 100 microns. The impact of the reinforcing material improves the physical, mechanical and tribological properties of the substrate. Increased mass percentage increases productivity [9, 10].
Abrasion refers to the gradual removal of particles from a solid surface as two hard materials rub in contradiction of one other. Wear cannot be as a characteristic of the material, but its subjected to on the environment it is exposed to [11]. Distance, Speed and load are the main parameters for testing wear [12].
The mixing of Aluminium Oxide into Aluminium alloy 6061 metal matrix found that with the growth in the % of reinforcement, the tensile strength and the UTS increase while the percentage of elongation was decreased. “Also, the hardness increased with the increase in the reinforcement content. The optical micrographs show fairly uniform distribution of Al2O3 in the Al6061 MMC” [12]. Compared to Al6061 alloys [13, 14], the weight loss of composites is also low. Compared to the old stir casting method, the use of ultrasonic assisted casting technology can give better enhancement in the mechanical, physical and tribological properties of the manufactured composite material [15]. Low cycle fatigue tests showed no evidence of isotropic hardening or softening [16]. The microstructure and mechanical properties of the copper-coated Al2O3-reinforced Al6061 composite both show fairly uniform distribution and improved mechanical properties [17].
The dry gliding wear test of SiC and Al2O3 reinforced hybrid aluminium 6061 metal matrix composites shows that increasing the volume percentage of the reinforced material can reduce wear. Use statistical regression analysis and analysis of variance to establish empirical relationships to evaluate wear [18]. By the use of model which is newly developed, we analysed the wear resistance of the face surface hardness. “The volume fraction of the reinforcement material will seriously affect other factors such as low relative surface load, low speed and high hardness. The failure is caused by the abrasive wear mechanism” [19].
The wear resistance of Al 6061 is much lower because it is a soft (easily ductile) material. The purpose of this project is to obtain a material with higher wear resistance and lower weight. Therefore, in order to improve the wear resistance, we must add ceramic reinforcing materials to the Al6061 alloy. It is found that the wear features of Al 6061 alloy can be improved by adding a reinforcing agent (Al2O3). However, in 5 % by weight of the reinforcing agent, Al2O3, not much work has been done. The wear characteristics of Al2O3 strengthened by Al 6061 alloy under high RPM and high load are also the same. This paper focusses main on finding the Wear and Hardness of Al2O3 reinforced (5 wt. %) at High load and high RPM.
2. Experimental procedure and methodology
2.1. Material selection
Aluminium 6061 alloy was used as the base matrix for this study, and aluminium oxide with a size of 50 microns (5 % by weight) was used as the reinforcing material. 1 % by weight of magnesium (Mg) and 1 % flux to improve the wettability of the matrix reinforcement material. Table 1 shows the elements included in Al6061 alloy.
Table 1Composition of alloy Al 6061
Cu | Mn | Ti | Fe | Mg | Si | Zn | Cr | Other elements | Al |
0.20 | 0.18 | 0.07 | 0.45 | 1.05 | 0.62 | 0.03 | 0.09 | 0.2 | Remainder |
2.2. Composite manufacturing
The manufacture of standard quality composite materials is accountable for the correct selection of operating parameters, such as the melting point of the reinforcing material, the stirring speed and the preheating temperature. To prepare the compound, follow these steps.
Fig. 1Setup of Stir casting process
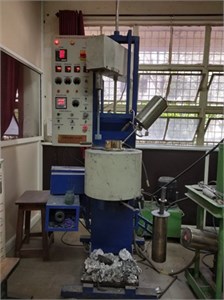
A resistance induction furnace was used to heat around 1 kg of alloy Al6061 to a molten state in a crucible of graphite. Melting point is 750 °C. The stirrer is comprising of two blades covered with a non-stick boron nitride paste. The alloy after melting completely, a stainless-steel stirrer is placed in the alloy which is in molten form, after that the stirring process begins. The boron nitride non-stick coating is used to avoid melted metal from adhering to the part inside of the crucible. The whole mixing unit, at speed of 500 rpm was switched on for half an hour. The entanglement depth of the stirrer is sustained at about 2/3 of the total depth of the molten metal. Under stirring, 5 % by weight of the preheated strengthening particles Al2O3 was added to vortex created by stirring. Prior to this, preheat the strengthening particles to 250 °C for 1 hour. After the particles are added to the melt, the alloy is poured into a preheated permanent steel mould (300 °C) and then chilled to normal room temperature. Then remove the preform from the mould. As a result, an Al6061-Al2O3 composite material having a reinforcement material of 5 % by weight was obtained, and a wear test piece was processed from the composite material. Table 1 lists the nominal composition of Al6061.
2.3. Test specimen preparation
After manufacturing the composite material, a water jet processing was used to produce wear test samples. The dimensions are 15 mm×15 mm×50 mm. Then milling process was used to the pin to form a precise size of 10 mm×10 mm×50 mm.
2.4. Hardness test
The hardness value of alloy Al 6061 and composite materials is measured using the Rockwell Hardness test Machine. A spherical indenter is used to apply a load of 100 kg to the polished sample for 10 seconds. In order to avoid the influence of the separation of the steel bar in the matrix, each sample is tested 10 times. The average hardness value is listed in the table below. Then use the hardness conversion table to convert the hardness value to Brinell hardness.
2.5. Wear test
Under environmental conditions the dry-slip wear tests on pins and disk devices are performed. Use a high-carbon and high-chromium steel disc with a hardness of 658HB, a diameter of 165 mm, and a thickness of 8mm. Using the response surface method, we designed 9 trials with two variable values: load and rotation. The load range is 5 to 200 N, and the speed range is 200 to 1500 rpm. Before performing the abrasion test, clean the surface and disc samples with an acetone solution. The calculation of specific wear rate can be done as follows.
1) wear coefficient, or specific wear rate (also sometimes called wear factor) = (wear rate)/ (normal force) (m3 / N−1m−1).
2) wear resistance = 1/ (wear amount) (m−1, kg−1, m−3).
3) wear amount = mass loss (kg) or linear dimensional change (m) or volume loss (m3).
4) wear rate= (wear amount)/ (sliding distance or time) (kg/m, m/m, kg/s, m3/m, m/s, m3/s).
Table 2DoE for wear test
Experiment No. | RPM | Load (N) |
1 | 346 | 46 |
2 | 346 | 173 |
3 | 1053 | 46 |
4 | 1053 | 173 |
5 | 700 | 20 |
6 | 700 | 200 |
7 | 200 | 110 |
8 | 1200 | 110 |
9 | 700 | 110 |
Fig. 2Al6061 pins
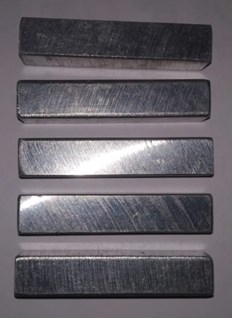
Fig. 3Al6061+Al2O3 pins
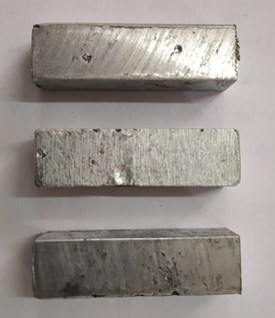
3. Results and discussions
The properties related to mechanical, of processed composites are highly dependent on the mass fraction of hardened particles added to the alloy base material. The reinforced particles change the performance of the material from toughness to brittleness. As shown in Fig. 4, it can be seen that the hardness of Al2O3 reinforced MMC is better than Al6061. Note that adding a reinforcing agent will significantly increase the hardness value. The higher hardness value clearly shows that the presence of particles in the matrix improves the overall hardness of the composite material.
Fig. 4Hardness values of Al 6061 v/s Al6061+Al2O3
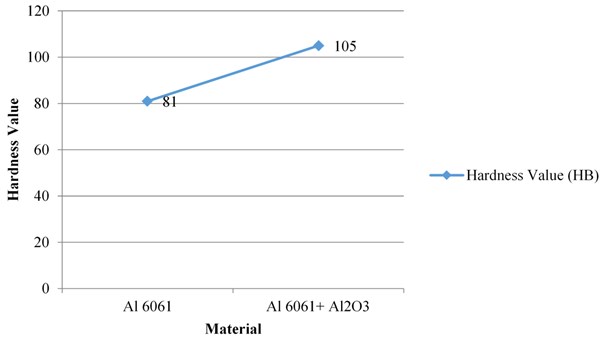
Wear due to adhesion was observed in the case of aluminium alloy 6061 because it is ductile, while wear was observed in the case of MMC containing alumina. RPM and Load are the two most vital factors of wear.
Table 3Results for wear
Expt No. | Specific wear rate for Al6061 [Micron] | Specific wear rate for Al6061 + 5 % Al2O3 [Micron] |
01 | 567.75 | 423.3 |
02 | 1199.28 | 783.17 |
03 | 1559.99 | 1016.49 |
04 | 2618.17 | 1944.29 |
05 | 719.4 | 453.8 |
06 | 2047.9 | 1497.15 |
07 | 539.79 | 461.27 |
08 | 2340.06 | 1289.7 |
09 | 1681.9 | 978.83 |
Fig. 5Specific wear rate of Al6061 v/s Al6061+Al2O3
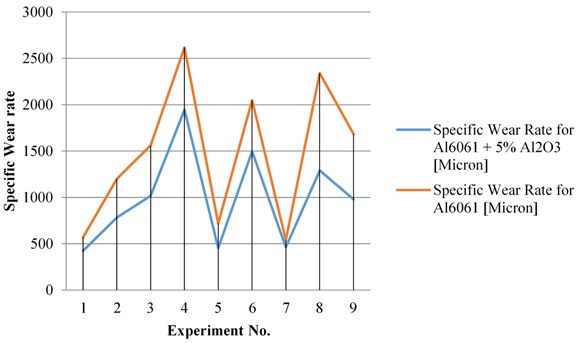
Compared with composite alloy samples, the wear of non-reinforced alloys increases sharply with the applied load. Figs. 6 and 7 show the analysis of Al6061. It can be seen from Fig. 6 that at a constant speed, there is increase in wear as the load surges. Similarly, the higher the speed, the higher the wear rate under the same load. Under constant load, the wear rate surges with the increase in the speed per minute, and as the load increases, an increase in the wear rate is observed at the same speed, as shown in Fig. 7. Al6061 is observed in Figs. 8 and 9.
Fig. 6Wear v/s load by RPM at constant value for Al6061 alloy
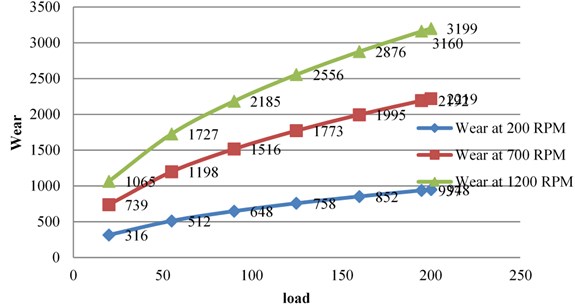
Fig. 7Wear v/s RPM by constant Load for Al6061 alloy
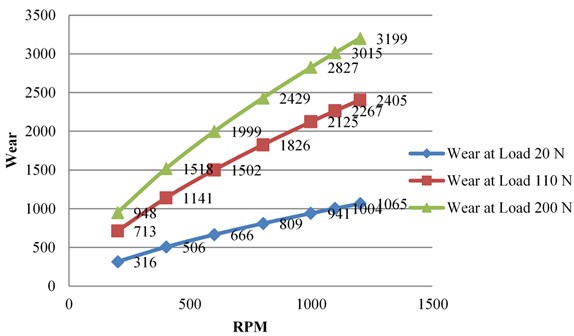
Fig. 8Wear v/s load by same RPM for Al6061+Al2O3
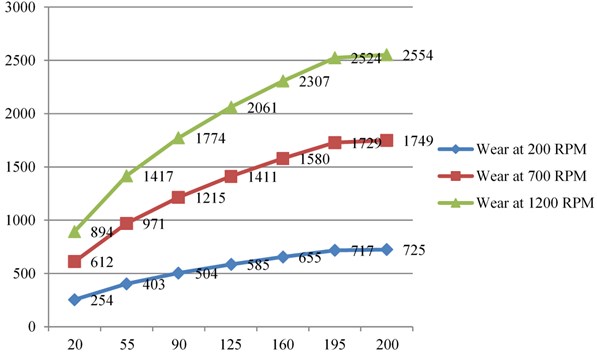
As shown in Fig. 10, the wear rate at 700 rpm is compared. It has been observed that Al6061 has a higher wear rate than Al2O3. As the load increases, the wear rate also increases. Fig. 11 shows the comparison of the wear rate of the two materials under a constant load of 110 N. As you can see, as the number of revolutions increases, the wear rate of both materials will increase. However, the wear rate of Al6061 alloy is higher than that of reinforced composites.
Fig. 9Wear v/s RPM by load value constant for Al6061+Al2O3

Fig. 10Wear v/s load at 700 RPM
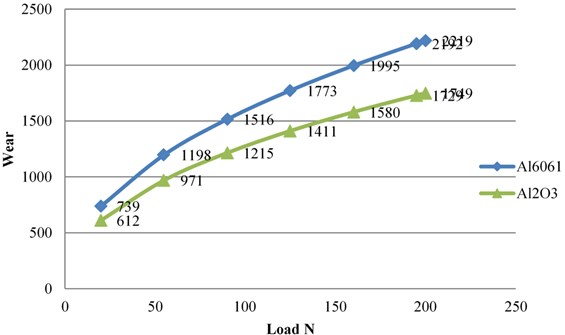
Fig. 11Wear v/s RPM at 110 N load
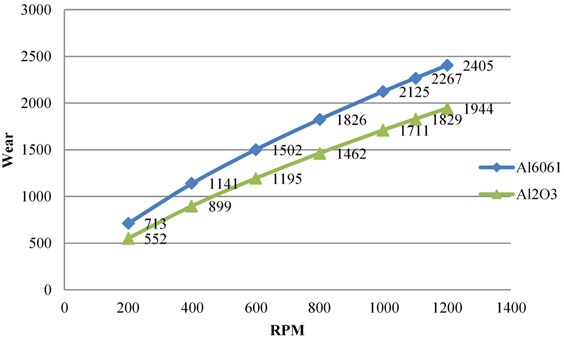
The image of the wear marks is shown below. You will see that there is bond in the Al6061 alloy. When the test material wears, the inherently ductile Al6061 alloy tends to stick to the disc. Al2O3 reinforced MMC is not sticky.
Fig. 12Track of Al6061
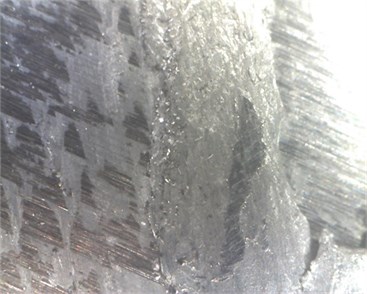
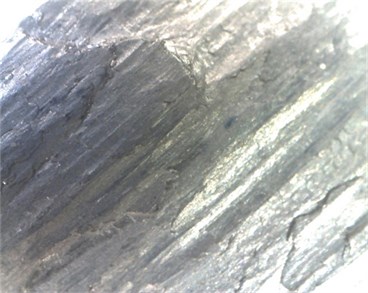
Fig. 13Track of Al6061+SiC
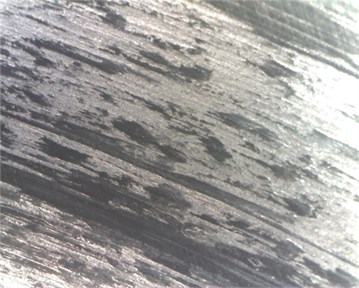
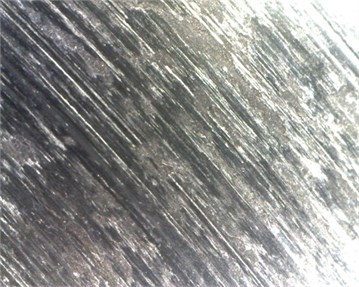
4. Conclusions
Compared to Al6061, the newly developed Al6061 and 5 % Al2O3 composites have better wear characteristics. The value of hardness measured in Rockwell number of the new composite material is also significantly improved. The knowledge base is expanding due to the greater influence of the speed and load depending on the rate of wear. At consistent load condition, wear rises with increasing speed. Correspondingly, when speed is constant as the load rises, there is an increase in wear at speeds when they are at constant value, as there is increase in load, more wear is detected than Al6061-Al2O3 in the case of Al6061. Under constant load with increasing speed it was also found that the wear in the case of Al6061 exceeds the wear of Al6061-Al2O3. Therefore, it is concluded that the reinforced composite with an Al2O3 metal matrix MMC has better properties than the non-reinforced Al6061 alloy.
References
-
R. Bauri and D. Yadav, “Introduction to metal matrix composites,” Metal Matrix Composites by Friction Stir Processing, pp. 1–16, 2018, https://doi.org/10.1016/b978-0-12-813729-1.00001-2
-
D. D. L. Chung, “Metal-matrix composites,” Carbon Composites, pp. 532–562, 2017, https://doi.org/10.1016/b978-0-12-804459-9.00009-9
-
M. Haghshenas, “Metal-matrix composites,” Reference Module in Materials Science and Materials Engineering, 2016, https://doi.org/10.1016/b978-0-12-803581-8.03950-3
-
N. Panwar and A. Chauhan, “Fabrication methods of particulate reinforced Aluminium metal matrix composite-A review,” Materials Today: Proceedings, Vol. 5, No. 2, pp. 5933–5939, 2018, https://doi.org/10.1016/j.matpr.2017.12.194
-
Ulhas K. Annigeri, “Method of stir casting of aluminum metal matrix composites: a review,” Materials Today: Proceedings, Vol. 4, No. 2, pp. 1140–1146, 2017.
-
M. K. Sahu and R. K. Sahu, “Fabrication of aluminum matrix composites by stir casting technique and stirring process parameters optimization,” Advanced Casting Technologies, May 2018, https://doi.org/10.5772/intechopen.73485
-
B. Chandra Kandpal, J. Kumar, and H. Singh, “Manufacturing and technological challenges in Stir casting of metal matrix composites – a review,” Materials Today: Proceedings, Vol. 5, No. 1, pp. 5–10, 2018, https://doi.org/10.1016/j.matpr.2017.11.046
-
J. Hashim, L. Looney, and M. S. Hashmi, “Metal matrix composites: production by the stir casting method,” Journal of Materials Processing Technology, Vol. 92–93, pp. 1–7, Aug. 1999, https://doi.org/10.1016/s0924-0136(99)00118-1
-
Yashpal, Sumankant, C. S. Jawalkar, A. S. Verma, and N. M. Suri, “Fabrication of aluminium metal matrix composites with particulate reinforcement: a review,” Materials Today: Proceedings, Vol. 4, No. 2, pp. 2927–2936, 2017, https://doi.org/10.1016/j.matpr.2017.02.174
-
H. Kala, K. K. S. Mer, and S. Kumar, “A review on mechanical and tribological behaviors of stir cast aluminum matrix composites,” Procedia Materials Science, Vol. 6, pp. 1951–1960, 2014, https://doi.org/10.1016/j.mspro.2014.07.229
-
A. T. Alpas, S. Bhattacharya, and I. M. Hutchings, “4.5 wear of particulate metal matrix composites,” Comprehensive Composite Materials II, pp. 137–172, 2018, https://doi.org/10.1016/b978-0-12-803581-8.09965-3
-
K. Vijaya Bhaskar, S. Sundarrajan, B. Subba Rao, and K. Ravindra, “Effect of reinforcement and wear parameters on dry sliding wear of aluminum composites - A review,” Materials Today: Proceedings, Vol. 5, No. 2, pp. 5891–5900, 2018, https://doi.org/10.1016/j.matpr.2017.12.188
-
B. C. Kandpal, J. kumar, and H. Singh, “Fabrication and characterisation of Al2O3/aluminium alloy 6061 composites fabricated by Stir casting,” Materials Today: Proceedings, Vol. 4, No. 2, pp. 2783–2792, 2017, https://doi.org/10.1016/j.matpr.2017.02.157
-
V. Bharath, M. Nagaral, V. Auradi, and S. A. Kori, “Preparation of 6061Al-Al 2 O 3 MMC’s by stir casting and evaluation of mechanical and wear properties,” Procedia Materials Science, Vol. 6, pp. 1658–1667, 2014, https://doi.org/10.1016/j.mspro.2014.07.151
-
D. K. Koli, G. Agnihotri, and R. Purohit, “Influence of ultrasonic assisted stir casting on mechanical properties of Al6061-nano Al2O3 Composites,” Materials Today: Proceedings, Vol. 2, No. 4–5, pp. 3017–3026, 2015, https://doi.org/10.1016/j.matpr.2015.07.286
-
L. Ceschini, G. Minak, and A. Morri, “Tensile and fatigue properties of the AA6061/20vol% Al2O3p and AA7005/10vol% Al2O3p composites,” Composites Science and Technology, Vol. 66, No. 2, pp. 333–342, Feb. 2006, https://doi.org/10.1016/j.compscitech.2005.04.044
-
B. R. Mithun, M. Nagaral, V. Auradi, and V. Bharath, “Microstructure and mechanical properties of cu-coated Al2O3 particulate reinforced 6061 Al metal matrix composite,” Materials Today: Proceedings, Vol. 4, No. 10, pp. 11015–11022, 2017, https://doi.org/10.1016/j.matpr.2017.08.060
-
K. Umanath, S. T. Selvamani, K. Palanikumar, and R. Sabarikreeshwaran, “Dry sliding wear behaviour of AA6061-T6 reinforced SiC and Al2O3 particulate hybrid composites,” Procedia Engineering, Vol. 97, pp. 694–702, 2014, https://doi.org/10.1016/j.proeng.2014.12.299
-
K. Umanath, K. Palanikumar, and S. T. Selvamani, “Analysis of dry sliding wear behaviour of Al6061/SiC/Al2O3 hybrid metal matrix composites,” Composites Part B: Engineering, Vol. 53, pp. 159–168, Oct. 2013, https://doi.org/10.1016/j.compositesb.2013.04.051