Abstract
The Shear Thickening Fluid (STF) is a non- Newtonian fluid which comes under dilatant material, STF undergoes phase transition from a low to high viscosity when shear stress is applied on it. In this paper modelling and simulation tools are used to study the STF fluid interaction when subjected to applied shear stress. The Eulerian description used for the fluid flow and the model considered the Lagrangian description of the rigid particles. The numerical analysis inspects important guideline such as acceleration of the flow, particle dispersion and the base of Non-Newtonian fluid. The fluid particles interrelation of STF showed that the shape, arrangement, volume concentration, and size of the particles had a vital effect on the behavior of STF. By adding sand particles in non-Newtonian fluids and applying high shear strain rates showed improvement in the shear thickening effects.
1. Introduction
As the world is changing rapidly in many aspects and so humans. If we see the past, then maximum battles were due to land and water. So, for that, we need civil, military structures and updated systems which overcome the impact due to things which were used during the encounter. There are so many energy absorbing materials which have been considered in order to overcome the impact or shock loading. Shear thickening fluid (Polypropylene Glycol 400 and sand) [1] is a portable solution that when sheared increases its viscosity so the more stress applied to it the more resistance it gives to that.
Shear thickening fluid (STF) could possibly be used to fortify the resistance of army garment and body armor against ballistic thread [2] and puncture [3]. Zip lock bags of STF on soldier and it would be nice and flexible when he is walking around but then if a projectile come and hit on STF armor it would turn hard and reflect he projectile. In the past, experimental analysis was a common research approach in studying STF but now availability of advanced software and machines makes it logical to do modelling and study numerically to further understand the physics and mechanisms of STF [4].
In Lagrangian, a fluid particle is being followed at each point the fluid properties are then determine as the fluid particle move about. But in Eulerian approach a frame is fixed at a particular point in space during a fluid flow and noting that characteristics of the particles as they pass through the frame [5]. Stokesian dynamics methods [6], Dissipative particles dynamics [7] and the Lagrange multiplier fictitious domain method are other computer models which are now used to study fluid characteristics. This study depicts us the shear thickening effect when we use both Eulerian and Lagrangian models [8]. By using these models, the study shows us the effects of various factors that are linked with rigid body particles on shear thickening. Such factors comprise of particle size, shape, volume friction, distributions, and many more the next section offers a brief analysis of Shear Thickening Fluid (STF), which is then classified by using the description of different things like numerical modeling and analysis. Thereafter, the numerical results and discussion are presented followed by results obtained after the computational studies.
2. Review of STF
A fluid in which the shear stress is directly proportional to the rate of shear strain is known as Newtonian fluid:
where – shear stress, – viscosity of a fluid, and – strain rate.
Fig. 1 shows on the -axis the shear stress and plotted against the -axis which is rate of shear strain or the velocity gradient. As the straight line goes through a zero is a Newtonian fluid that follows the Eq. (1). Also, there are many type of fluid that do not behave like Newtonian fluid and the study of these kind of fluid is called rheology such fluid comes under non-Newtonian fluid.
According to the power-law model viscosity and shear strain rate can be expressed in the mathematical expression of for non-Newtonian fluids:
where – flow behavior index, – flow consistency index.
The mathematical expression of the apparent viscosity in term of shear strain rate can be written as:
For a Newtonian fluid type, the (flow consistency index) is equivalent to fluid viscosity, and the flow of behavior index , is one. For the STF is greater than 1. Fig. 2 shows the relation where a Newtonian Fluid relationship is summarized. STF is the example of dilatant material which comes under non-Newtonian fluid. The dilatant material like sand, ethanol, mercury can be dispersed in carrier fluid e.g. water or Polypropylene Glycol (PPG400) [9].
Fig. 1Shear stress Vs shear strain rate
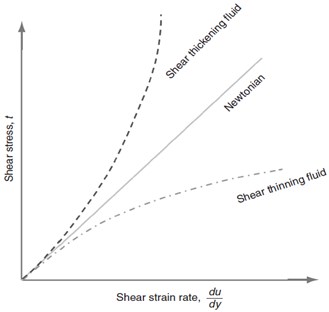
Fig. 2Relation between flow consistency index (Pa sn) and shear stress (Pa)
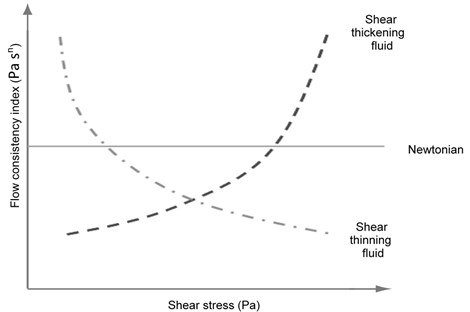
3. Numerical modeling and analysis
3.1. Modeling of STF
Eulerian approach is mostly used to model the STF in two phase or multi-phase. The Lagrangian approach at the particle-level was used to examine the characteristics of the STF in this study, based on contact with a Eulerian carrier fluid. In this study individual particle was focused for numerical analysis. ANSYS CFX Rigid Body Solver was used for the geometry modelling, meshing, setup, solution and results. Also, ANSYS CFX was used to optimize each rigid body movement when it subjected to shear loading condition.
Fig. 3Geometry of shear thickening fluid model
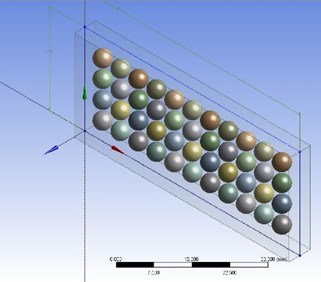
Fig. 4Meshing of silica and fluid domain in STF model
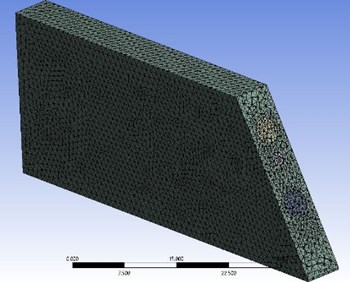
3.2. Mesh
As we concentrated on a 2-D geometry 3-D model had to be defined with cell thickness of 1 mm in the -direction. A hexahedral mesh was used for meshing the model Number of nodes are 31, 451 and elements are 1,57,734 are the basic mesh information for ANSYS CFX as shown in Fig. 4.
3.3. Transient modeling
Transient modeling is required to study the behavior of the silica particles at every time step when dispersed fluid and solid interface are subjected to shear loading. The total time was selected 2 second for simulation and the time step size was taken as 0.2 second. The time interval for output was selected based upon the dimension of the particles having control volume of 60 mm×25 mm and diameter size of 2 mm, with applied flow velocity of 2 m/s. K-Epsilon model was chosen for turbulence modeling and turbulence wall function was scalable.
3.4. Materials
In this study water was chosen as the carrier fluid. Water having viscosity of 0.0091 Poise and the density of silica is 2.196 g/cm3. SiO2 particles were located in between the fluid flow [10]. The diameter of each spherical SiO2 particle was selected 2mm and all the particles was placed at same distance from each other.
3.5. Boundary conditions
In the set-up part we defined the boundary conditions. The rectangular box was considered as the fluid domain and spherical ball was considered as sand particles. Spherical balls are placed inside the carrier fluid. Upper wall of the fluid domain was considered as inlet and bottom wall was considered as no slip wall. Right and left wall was defined as transitional periodicity interface. Front and back wall was considered as boundary of the fluid domain. In the analysis command we chosen the 2 second times for transient simulation at 0.2 s time step. Also, The Rigid Body Solver was used for silica particle interaction with carrier fluid.
Fig. 5Boundary condition and finite element meshing
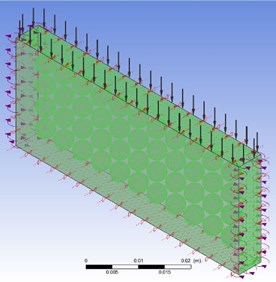
3.6. Multiphase modeling
The two general components of the Shear Thickening Fluid (STF) are the base fluid which is water and the granular particle phase which is silica particles. To simulate the two phases particles, the interaction among the two phases has to be defined before the process starts. Multiphase flows are generally classified as either segregated or dispersed. In segregated flows, each phase flow through the domain is separated by macroscopic interfaces and in dispersed flows, at least one of the phases is a rigid body particle.
3.7. Rigid body modeling of particles
The motion of the rigid body is dictated by the fluid forces and external forces. Rigid body solver was used for rotation and giving a particular shape to the silica particles. Here we used a function denotes the particle location in space at a particular time, . The function is the velocity. This velocity was given at a particular time ():
For rigid bodies like silica particles, there would also be a requirement to define as the rotation of the body. Thus, and makes up the three-dimensional variable of the rigid body [12]. If we think that the rotation has to be fixed, then the only momentum which is lift is translation. To check the imitation of a solution along with the motion of a rigid body, all the forces that are acting on a rigid body silica particle would also be necessary, and it can be defined as . For a rigid body particle having a mass m, the change of over time would be given by:
4. Results and discussion
All the calculation was done by using velocity magnitude 2 m/s. Inlet face of the fluid domain was subjected to shear velocity of 2 m/s. The acceleration was calculated 0.195 m/s2 under this velocity with respect to time. Parameter like viscosity, shear strain rate, pressure gradient, velocity distribution and mass flow were calculated in this study. Viscosity of STF increase with respect to shear strain rate. As the shear strain rate increase viscosity of STF initially decreases and after certain point it raises. This characteristic makes the STF future Body armor material. Pressure gradient decreases along direction as the velocity increases. Momentum boundary flow on fluid domain also increases with respect to time.
Fig. 6Shear strain rate and viscosity distribution for flow velocity of 2 m/s
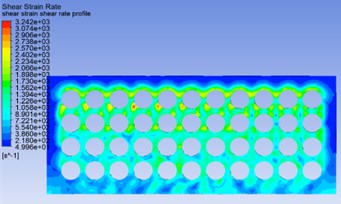
a)
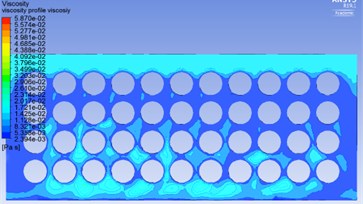
b)
Fig. 7Pressure gradient distribution and velocity profile distribution at 2 m/s
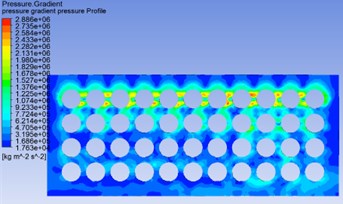
a)
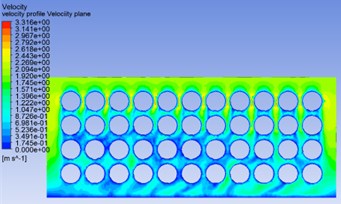
b)
Fig. 8Velocity profile along Y-direction
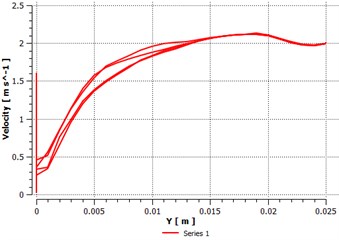
Fig. 9Viscosity vs. shear strain rate
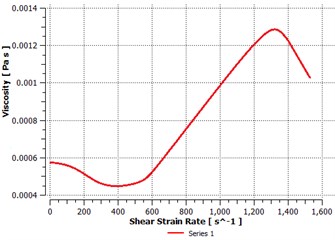
Fig. 10Momentum of fluid flow vs. time
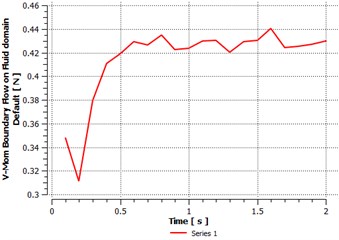
Fig. 11Pressure distribution along Y direction
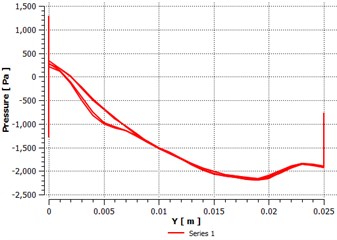
5. Conclusions
The numerical simulation analysis was led by modeling the separated sand particles and base fluid interaction. The important particle parameter was studied by using the Lagrangian and Eulerian approach, that could influence the execution of STF. By applying higher acceleration and velocity to the STF domain higher shear thickening effects could be achieved, Also higher concentration of sand particles in base fluid effect the viscosity of the STF. This numerical simulation proposed that sand particles could further improve the viscosity of STF. Improve viscosity leads to the improve shear thickening result of dilatant fluids, although a further study is required for the non-linear response at lower shear strain rates. Favorable outcome in the simulation of the shear thickening effect would motivate for more upgraded and enhanced Shear thickening fluid design.
References
-
Nesterenko V. F. Shock (Blast) Mitigation by ‘Soft’ Condensed Matter. Granular Material-Based Technologies, Vol. 759, 2003.
-
Lee Y. S., Wetzel E. D., Wagner N. J. The ballistic impact characteristics of Kevlar woven fabrics impregnated with a colloidal shear thickening fluid. Journal of Materials Science, Vol. 38, 2003, p. 2825-2833.
-
Decker M. J., Halbach C. J., Wetzel E. D., Nam C. H., Wagner N. J., Wetzel E. D. Stab resistance of shear thickening fluid (STF)-treated fabrics. Composite Science and Technology, Vol. 67, 2007, p. 565-578.
-
Petkova S., Hossain A., Naser J., Palombo E. CFD modeling of blood flow in portal vein hypertension with and without thrombosis. Third International Conference on CFD in the Minerals and Process Industries CSIRO, Melborne, Australia, 2003.
-
Ein-Mozaffari F., Upreti S. R. Investigation of mixing in shear thinning fluids using computational fluid dynamics. Computational Fluid Dynamics, 2010, p. 77-102.
-
Foss D. R., Brady J. F. Structure, diffusion and rheology of Brownian suspensions by Stokesian dynamics simulation. Journal of Fluid Mechanics, Vol. 407, 2000, p. 167-200.
-
Boek E. S., Coveney P. V., Lekkerkerker H. N. W., Van der Schoot P. Simulating the rheology of dense colloidal suspensions using dissipative particle dynamics. Physical Review E, Vol. 55, Issue 3, 1997, p. 3124-3133.
-
Hamaker H. C. The London-Van der Waals attraction between spherical particles. Physica, Vol. 4, Issue 10, 1937, p. 1058-1072.
-
Xu Y.-L., Gong X.-L., Peng C., Sun Y.-Q., Jiang W.-Q., Zhang Z. Shear thickening fluids based on additives with different concentrations and molecular chain lengths. Chinese Journal of Chemical Physics, Vol. 23, Issue 3, 2010, p. 342.
-
Lee B.-W., Kim I.-J., Kim C.-G. The influence of the particle size of silica on the ballistic performance of fabrics impregnated with silica colloidal suspension. Journal of Composite Materials, Vol. 43, Issue 23, 2009, p. 2679-2698.
-
Baraff D. Rigid Body Simulation. Course Notes, Siggraph, 2001.