Abstract
An optimization based on sequential quadratic programming (SQP) algorithm to increase the thermal insulation and sound transmission loss of honeycomb panel in thermal environments is presented. First, heat transfer analysis is performed to reveal the steady-state thermal performance of hexagonal aluminum honeycomb sandwich panel, by using the semi-empirical Swann and Pittman formula. Next, the influences of temperature on acoustic performance of honeycomb panel based on statistical energy analysis method (SEA) is performed. Results show that increasing the thickness of the honeycomb core can improve the acoustic performance and heat insulation behavior.
1. Introduction
The metal honeycomb sandwich panel is made up of upper and lower skin and intermediate honeycomb core, which is an important part of the metallic thermal protection system (MTPS) because of its relatively high rigidity, low structure density and certain thermal insulation performance [1]. In addition to the thermal protection structure, it is also widely used in other spacecraft bearing structure and the basic structure of large accessories, such as the sun wing of the substrate, aircraft engine parts [2]. When the aircraft is flying at high speed, the outer surface of the metal honeycomb panel will withstand a large aerodynamic thermal load and pneumatic noise, so its acoustic performance and heat insulation performance should meet certain requirements.
Vibro-acoustic studies of sandwich panels have been carried out with wave impedance analysis [3, 4] or statistical energy analysis [5, 6] in high frequency, but few of these studies considered thermal effects. Therefore, it is necessary to consider the thermal effect when studying acoustic performance of honeycomb panels.
This article is organized as follows: In Section 2, the numerical study is performed to reveal the influences of the cell size on the steady-state thermal performance of aluminum honeycomb sandwich panel, by using the semi-empirical Swann and Pittman formula. In Section 3, acoustic behavior of honeycomb panels is studied by considering the effect of temperature variation. In Section 4, the multi-optimization with the objective that simultaneously minimizing the sound transmission and the structural thermal transmission with constraint of area mass density is carried out here.
2. Heat transfer analysis
The heat transfer inside the honeycomb sandwich panel is very complex, which is the coupling process of solid, gas heat conduction, radiant heat transfer in the honeycomb cavity and natural convective heat transfer, scholars have proposed a variety of calculation models for the equivalent calculation of the heat transfer performance of the sandwich structure. Among them, the semi-empirical formula model proposed by Swann and Pittman [7] has been used as a standard model to calculate the equivalent thermal conductivity of the honeycomb structure, which has greatly facilitated the calculation of the heat transfer performance of the sandwich panel.
2.1. Heat transfer calculation method
In this paper, Swann and Pittman’s semi-empirical formula is used to analyze the thermal performance of aluminum honeycomb sandwich panels. Swann and Pittman ignore the temperature gradient of the skin and treat the heat transfer in the thickness direction of the sandwich panel as a one-dimensional linear problem. The equivalent thermal conductivity of honeycomb sandwich considering solid, gas heat conduction and radiant heat transfer is expressed as:
where kf and kg represent thermal conductivity of core and air, ∆A/A is the ratio of cell wall fraction to total cell area of the cross-sectional area of the honeycomb sandwich cell, krradiation equivalent thermal conductivity, the expression is:
where λ is the ratio of the core height to the straight hexagonal circumscribed circle diameter, ε and σ are surface panel emissivity and Stefan-Boltzmann constant, T1 and T2 are the temperature of the upper and lower panels. The equivalent thermal conductivity is related to the temperature of the upper and lower panels, therefore, the temperature of the lower panel can be calculated by repeated iterations.
2.2. Heat insulation numerical calculation
The size of the aluminum alloy honeycomb panels studied is as follows: the thickness of the upper and lower panels is 1 mm, the height of the honeycomb core is 20 mm, the wall thickness of the honeycomb core is 0.1 mm, and the length of the honeycomb unit is 5 mm. The emissivity of the honeycomb upper and lower plates is 0.25. The thermal physical properties of aluminum alloy are shown in Table 1. When the upper panel is subjected to a temperature of 300 ℃, the size effect of thermal insulation can be shown in Figs. 1-4.
Table 1The thermal physical property parameter of aluminum alloy
Temperature / ℃ | 25 | 100 | 200 | 300 |
Specific heat / J/(kg·K) | 720 | 840 | 924 | 966 |
Thermal conductivity / W/(m·K) | 147 | 151 | 160 | 168 |
Fig. 1The relationship between temperature difference and honeycomb wall thickness
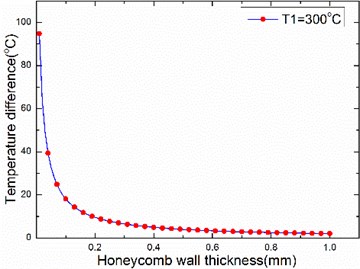
Fig. 2The relationship between temperature difference and length of honeycomb side
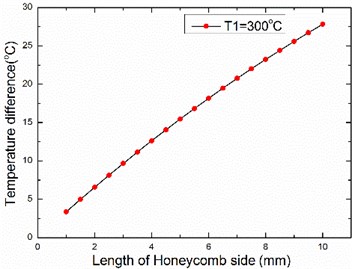
Fig. 3The relationship between temperature
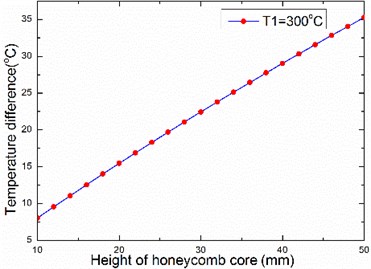
Fig. 4The relationship between temperature difference and thickness of panel
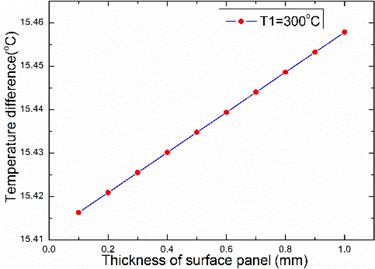
The thermal conductivity of air is much smaller than the thermal conductivity of aluminum alloy, the larger the volume ratio of the aluminum alloy structure in the honeycomb core layer, the better the heat transfer. Therefore, the larger the honeycomb wall thickness, the smaller the temperature difference; the temperature difference increases with the honeycomb side length, panel thickness and honeycomb core thickness, as illustrated in Figs. 2-4.
3. Acoustic performance
Statistical energy analysis (SEA) is a modeling procedure which uses energy flow relationships for the theoretical estimation of the vibration response levels of structures in resonant motion.
3.1. SEA theory
The modal density of structures depends on their boundary conditions and the governing equations of motion. For simply supported panels, the modal density is associated with the constant frequency loci of the wavenumber; then:
where Ap is the surface of panel.
For honeycomb sandwich panels with stiff cores, the anti-symmetric motion is dominant in the frequency under consideration. The sixth-order governing equation for free motion of sandwich structures presented by Mead and Markus [8] can be written as:
with:
where Ej is the Young’s modulus of the face sheet j; Gc the out-of-plane shear modulus of the core; tj and h are the thickness of the face sheet j and the core, and μ the mass area density of sandwich panel.
A transmission model is considered to consist of three coupled systems as source room, panel and receiving room, with the subscripts are expressed as 1, 2 and 3. Hence, the transmission loss can be expressed as [6]:
with:
where Vj is T(K) the volume of source room and receiving room, ηj and nj are the internal loss factor and modal density. ηradis the coupling loss factor due to radiation damping, Rrad is the radiation resistance of a baffled simply supported single-layer panel given by [9]. The internal loss factor of the sound field was determined from the reverberation time T3, the modal density can be obtained from Eqs. (1-2).
3.2. Effect of temperature on acoustic performance
When only considering the effect of temperature on the physical parameters, a typical temperature-dependent material properties P can be expressed as follows [10]:
where Hi is the coefficients of temperature T(K), which are particular to each specific material. Elastic modulus E of aluminum alloy are taken as temperature dependent. The temperature-dependent coefficients are listed in Table 2.
Table 2The thermal coefficient of elastic modulus E of aluminum alloy
H-1(K) | H0(K) | H1(K) | H2(K) | H3(K) |
0 | 204.2 | –4.585E-3 | 1.050E-5 | –8.338E-9 |
Fig. 5The relationship between temperature and modal density of honeycomb sandwich panel
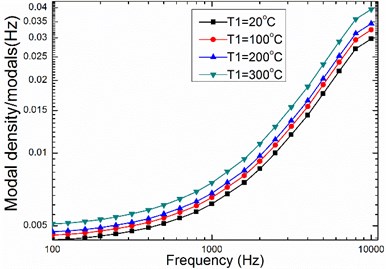
Fig. 6The relationship between temperature and sound transmission loss of honeycomb sandwich panel
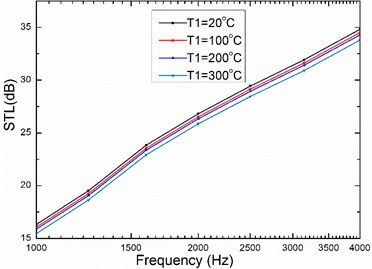
The dimensions of the panels are 0.84 m×0.42 m. T3 and η2 are set as 1.4 s and 0.03. Because the thickness of the upper and lower panels is very small, the temperature of upper and lower panels can be considered homogeneous. The temperature of honeycomb is assumed to be intermediate temperature of the core approximately. Modal density increases with temperature shown in Fig. 5, and increasing the temperature causes the sound transmission loss to decrease as illustrated in Fig. 6, the main reason is that the increase of temperature leads to the decrease of elastic modulus.
4. Optimization analysis
In this part, a multi-objective optimization model of honeycomb sandwich is proposed, with the objective of maximizing the sound transmission loss and thermal insulation. The thickness of the upper and lower panels, height of honeycomb core, the wall thickness of the honeycomb core and the length of the honeycomb unit are chosen as the decision variable.
4.1. Objective function
The acoustical function is determined from a weighted average of the field-incidence transmission coefficients:
in which the weighting function is chosen to correspond to a weighting for seven frequencies in the range of 1000-4000 Hz [11]. Finally, the weighted sound transmission loss average was calculated from:
thermal insulation object function was set as:
In this paper, the constraint is the area mass density:
where ρf and ρc are the density of face panel and core. Therefore, Multi-objective optimization problem can be written:
s.t.{μ≤μmax,0.1mm≤tf≤1mm,10mm≤tc≤50mm0.01mm≤t≤1mm,1mm≤l≤10mm,,
where w1 and w2 denote the weight of objective function, satisfied with w1+w2=1. ATL0 and ∆T0 were single objective optimization result of ATL and ∆T. μmax=4 kg/m2 is used in the following numerical calculation.
4.2. Optimization
The SQP algorithm is an efficient method to solve the nonlinear programming problem. The basic idea is to construct a simple approximation optimization problem by using the information about the nonlinear programming problem. The current iteration point is corrected by solving it, with a series of linear programming or quadratic programming to successively approximate the original nonlinear programming problem.
ATL0=20.4951 dB and ∆T0=157.6101 °C are obtained by SQP, with constraint of area mass density. When w1 and w2 are set as 0.5, the iterative process of the multi-objective function value is shown in Fig. 7. The optimization results are achieved when the height of honeycomb core reaches a maximum, the relationship between ATL and ∆T is displayed in Fig. 8.
Fig. 7The iterative process of the multi-objective function value
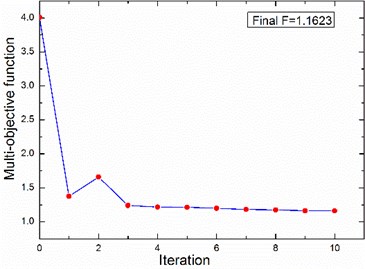
Fig. 8The relationship between ATL and ∆T
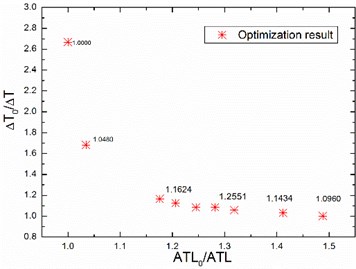
5. Conclusions
Aluminum alloy honeycomb insulation performance is related to size, the main factor is related to the proportion of aluminum material to the core. The increase of temperature leads to the decrease of elastic modulus and the increase of modal density, eventually leading to reduced sound transmission loss. Increasing the core thickness helps to improve the thermal insulation and sound insulation of the honeycomb panel at the same time. The optimized result has an important guidance value for engineering applications.
References
-
Caogen Y., Hongjun L., Zhonghua J., et al. A study on metallic thermal protection system panel for reusable launch vehicle. Acta Astronautica, Vol. 63, Issue 1, 2008, p. 280-284.
-
Shang G. Q., Zhu Z. S., Chang H., et al. Development of ultra-high strength titanium alloy. Chinese Journal of Rare Metals, Vol. 35, Issue 1, 2011, p. 286-291.
-
Kurtze G., Watters B. G. New wall design for high transmission loss or high damping. The Journal of the Acoustical Society of America, Vol. 31, Issue 6, 1959, p. 739-748.
-
Dym C. L., Lang M. A. Transmission of sound through sandwich panels. The Journal of the Acoustical Society of America, Vol. 56, Issue 5, 1974, p. 1523-1532.
-
Wang T., Li S., Rajaram S, et al. Predicting the sound transmission loss of sandwich panels by statistical energy analysis approach. Journal of Vibration and Acoustics, Vol. 132, Issue 1, 2010, p. 256-280.
-
Zhou R., Crocker M. J. Sound transmission loss of foam-filled honeycomb sandwich panels using statistical energy analysis and theoretical and measured dynamic properties. Journal of Sound and Vibration, Vol. 329, Issue 6, 2010, p. 673-686.
-
Swann R. T., Pittman C. M. Analysis of Effective Thermal Conductivities of Honeycomb-Core and Corrugated-Core Sandwich Panels. National Aeronautics and Space Administration, 1961.
-
Mead D. J., Markus S. The forced vibration of a three-layer, damped sandwich beam with arbitrary boundary conditions. Journal of Sound and Vibration, Vol. 10, Issue 2, 1969, p. 163-175.
-
Crocker M. J., Price A. J. Sound transmission using statistical energy analysis. Journal of Sound and Vibration, Vol. 9, Issue 3, 1969, p. 469-486.
-
Touloukian Y. S. Thermophysical Properties of High Temperature Solid Materials. Macmillan, New York, 1967.
-
Makris S. E., Dym C. L., Smith J. M. G. Transmission loss optimization in acoustic sandwich panels. The Journal of the Acoustical Society of America, Vol. 79, Issue 6, 1986, p. 1833-1843.