Abstract
The dynamic property of typical tri-cyclic servo system is related with the parameters of electric machine, but there has been no research for the relations. In this paper, the dynamic property evaluation function of tri-cyclic servo system was built based on the integral squared time-weighted errors. The transfer function model of tri-cyclic servo system was built, and the control parameters of the model were tuned with the genetic algorithm. Moreover, on the basis of data acquisition by optimization Latin square design, the evaluation model of dynamic property was built based on a BP network. The result of the verification experiments showed that the evaluation model was able to evaluate the dynamic property of typical tri-cyclic servo system with different technical parameters, and it could be used to provide a reference for the chosen electric machine.
1. Introduction
The tri-cyclic servo system was widely used in the industrial production, and its dynamic properties such as tracking error, response velocity decided whether the production task could be completed or not. The typical tri-cyclic servo system is composed of an electric machine, transmission mechanism, actuating mechanism, testing sensors, controllers and others [1]. The dynamic property of tri-cyclic servo system was related to the parameters of all parts. Therefore, the relations between parameters of each part and the entire tri-cyclic servo system must be studied to make sure satisfactory dynamic property could be achieved.
The studies of the mentioned relations have been concentrated on two aspects at present. The first aspect was building a mathematical model based on parameters identification for the controlled object, and then using some novel control methods or tune methods for setting control parameters to optimize the dynamic property for a tri-cyclic servo system [2, 3]. The second one was analyzing and preventing from the degradation of dynamic property generated from the stiffness, friction and other factors of transmission element by the methods of test experiments or simulation. Although the dynamic property of tri-cyclic servo system is also determined by the parameters of electric machine, there were few studies on this aspect [4]. It was so because in the traditional design method of servo system, the parameters of electric machine were determined by the principle of low cost and high efficiency according to the condition of power supply, the efficiency of the transmission element and others which had not taken the dynamic property into consideration. Once the parameters of electric machine were chosen, it cannot be changed. Therefore, the studies were meaningless unless the dynamic property had been taken into consideration at the determination of electric machine parameters in the design process of the servo system.
In this paper, we believed that the dynamic property of servo system should be taken into consideration in the design process and be built on an evaluation model to display the relations between the electric machine parameters and the dynamic property. In Section 2, an object function of evaluating the dynamic property for servo system was built based on integral squared time-weighted errors (ISTE). In Section 3, the simulation model of transfer function for tri-cyclic servo system was built and the control parameters of this model were to be tuned according to the genetic algorithm (GA). And then, on the basis of data acquisition by the simulation model and optimization Latin square design, the evaluation model of dynamic property was built based on a BP network in Section 4.
2. Dynamic property evaluation object function
The tri-cyclic servo system is used for implementing an accurate displacement or angle following, and the following process should also be fast and steady. At present, the object evaluation function of dynamic property for the tri-cyclic system can be described by time domain indexes, frequency domain indexes or integral performance indexes. The integral performance indexes are the comprehensive performance indexes which are close to reflect the dynamic property of tri-cyclic system more than the other two [5, 6]. And it includes the integral square error (ISE), ISTE, integrated absolute error (IAE), integrated time absolute error (ITAE) and others. ISE emphasize on preventing the big error of the transient process with the behavior of fast response and easy to generate an oscillation, IAE emphasize on preventing from a small error with the disadvantage of non-sensitivity to the system parameters variation, the ITAE is effective on the control of oscillation generating but fail in preventing from a big dynamic error, while the ISTE is good at controlling the big error in a relative short time as compared to others [7]. Therefore, in this paper, a dynamic property evaluation object function was built based on ISTE:
where J is the evaluation values of the dynamic property, and it is better when it is smaller, ω is the penalty factor for the system overshoot and can be defined as a great number, o is the overshoot, T is the minimum requirement time for the servo system reaching to the stable point, n is an integer bigger than 2, and it could be used to coordinate the system requirement of steady state error and settling time, and if the integer n is bigger, the requirement of steady state error for the system is higher.
3. Simulation model of transfer function
The relation between the electric parameters and the dynamic property should be studied in the condition of that the control parameters of the servo system have been tuned. Therefore, in this section, by studying the construction of the servo system, its simulation model for transfer function was built, and on the basis of GA, the control parameters of the servo system have been optimal and fast tuned.
3.1. Simulation model building
The tri-cyclic servo system consists of a current loop, velocity loop and position loop which were built based on the open loop transfer model of the electric machine [8]. And in the position loop, a proportional (P) controller is always used, while in the current loop and the velocity loop, it is a proportional-integral (PI) controller. Moreover, in the physical system, a low-pass filter that can be expressed by first order inertial link is used in the current loop to restrain the disturbance to the servo system. The low-pass filter in the current loop will cause the problem of control delay, the same first order inertial link shall be used before the current loop to make the feedback signal and the given signal transmission at the same time. Analogously, a feedback low-pass filter and pre-filter are also used in the velocity loop. Therefore, took the most frequently used permanent magnet synchronous electric machine (which the open loop transfer model was shown in Fig. 1) as an example, where, Lq is the winding inductance, R is the winding resistance, Ke is the back-EMF coefficient, Kr is the moment coefficient, J is the rotational inertia of electric machine, TL is the torque of load, B is the viscous friction coefficient, ωr is the angular velocity of the rotor. The simulation model tri-cyclic servo system can be built which was shown in Fig. 2.
Fig. 1Open loop transfer model of permanent magnet synchronous electric machine
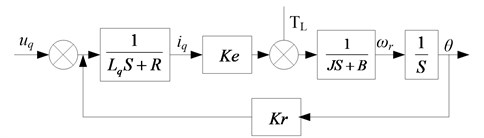
Fig. 2Simulation model tri-cyclic servo system
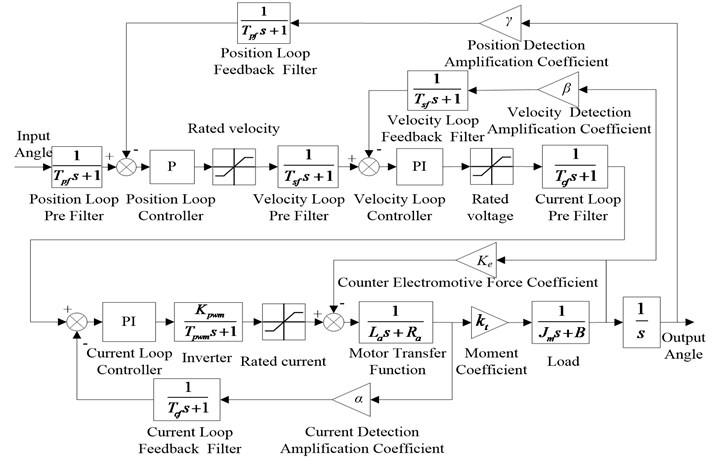
3.2. Tuning of control parameters
According to the simulation model shown in Fig. 2, there were 5 control parameters to be tuned. The GA had been proved better in tuning control parameters than the traditional method [9], and in this paper, it was used to tune the control parameters for the tri-cyclic servo system. The tuning step was:
(1) Computed the objective function value.
According to the dynamic property evaluation function mentioned in Section 2, the objective function value was defined as:
(2) Encoded for gene.
The tuning of control parameters consists in finding a solution for the optimization of a continuous function, and a gene encoded with the binary system was complicated with low accuracy as compared to the one encoded with a real number. Therefore, the one encoded with a real number was used in this paper.
(3) Selection operation.
In the selection operation, a higher survival probability was made for the individual that had a bigger F computed with Eq. (2). Hypothesis fi was the objective function values of individual i and Σfiwas the accumulated total values of the objective function of all the individuals, the duplication ability of individual i was fi/Σfi.
(4) Crossover and mutation operation.
Basic arithmetic crossover and mutation operation were used in this paper. And a high mutation constant was selected in the mutation operation to reflect the global search ability of the genetic algorithm. Moreover, the best individual is not used in both the crossover and the mutation operations to ensure the global convergence of GA.
(5) Convergence analysis.
In the traditional convergence analysis, the optimal searching result or the number of generations was used to determine whether convergence conditions are satisfied or not. However, in this paper, the optimal objective function value for the simulation model could not be certified in advance. Therefore, GA searching ended with the number of generations reach to the set numbers.
According to the tuning step for control parameters, a tri-cyclic servo system with its parameter indexes shown in Table 1 was tuned.
Table 1Parameter indexes of tri-cyclic system
Parameter | V (r/min) | C (A) | U (V) | Ra (Ω) | La (H) | Jm (kg×m2) | B | Ke |
Values | 3000 | 7.5 | 220 | 0.59 | 0.00169 | 0.00167 | 0.01 | 0.0838 |
Parameter | Tpf | Tsf | β | γ | Tcf | Kpcm | Tpcm | Kr |
Values | 0.0001 | 0.001 | 1 | 1 | 0.0001 | 0.1 | 0.001 | 0.8 |
The value of the evaluation function (J) was 1308 while n was 3 and ω was 100 after tune, and the dynamic following property was shown in Fig. 3.
Fig. 3Dynamic following property of tuned tri-cyclic servo system
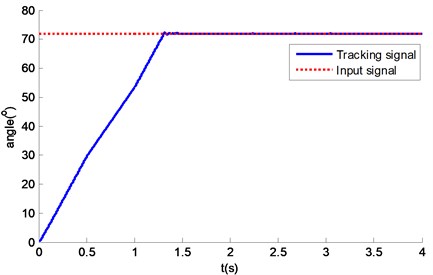
4. Dynamic property evaluation for Tri-Cyclic servo system
4.1. Experiment design for data acquisition
The accuracy of the evaluation model for the dynamic property based on BP network was decided by the data acquisition method. The orthogonality principle was utilized in the mathematical statistics, and the representative data, which displayed the relations between the electric parameters, were chosen, and the dynamic property could guarantee the accuracy of the evaluation model. The simulation data distribute in the data space uniformly and it is orthogonal with each other by using the optimization Latin square design method [10]. For the parameters V, C, Ra, La, β and Tsf shown in Table 2, they were obvious relevant with the dynamic property, the evaluation model for the relationships between these 6 parameters and the dynamic property was studied. The number of sample data groups used for building the evaluation model was set as 50. Therefore, according to the optimization Latin square design method, the dynamic property based on the simulation model and tuning steps was computed, the 50 groups sample data was shown in Table 2 while n was 5 and ω was 100.
Table 250 groups sample data
Group | V (r/min) | C (A) | Ra (Ω) | La (H) | β | Tsf | J |
1 | 2957 | 5.76 | 3.622 | 0.0576 | 8 | 0.000125 | 5315 |
2 | 3263 | 7.22 | 1.51 | 0.0535 | 2 | 0.000112 | 3692 |
… | … | … | … | … | … | … | 5150 |
50 | 3275 | 5.57 | 4.541 | 0.0758 | 5 | 0.0000613 | 3796 |
4.2. Evaluation model building based on BP network
As a widely used network, a 3-layers BP network is able to approximate all the continuous functions in any accuracy [11]. And it was used in this paper to build the evaluation model. In the BP network training process, the number of input neurons was 6 as per the parameters V, C, Ra, La, β and Tsf shown in Table 3, while the output neuron was J also shown in Table 3. The number of hidden layer neurons was set as 10 according to the empirical formula:
where, y was the number of hidden layer neurons, m was the number of input neurons, n was the number of the output neurons, a was an integer which was varied from 0 to 10.
By comparing the result of substantive BP training experiments, the transfer function between input layer and hidden layer was chosen to be sigmoid, and between hidden layer and output layer it was a purelin function. The training function was training, and the learning rate was set as 0.01, the training error was 10-5. 45 groups of sample data were used to train, and after training with 52986 times, the error reached to 9.9928×10-6. The error varied with training process was shown in Fig. 4.
Fig. 4Error varied with BP network training process
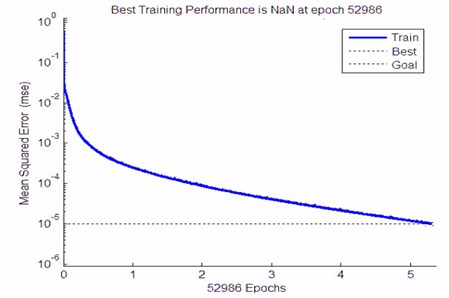
According to the result of BP network training, the evaluation model was built as:
where, Jpwas the evaluation value of the dynamic property, Pij and bj were the weight and threshold between input layer and hidden layer, Qj and k were the weight and threshold between hidden layer and output layer, Xi was the values of input parameters.
There were 5 groups of sample data that had not been used in the BP network training. They were used to verify the evaluation model. As shown in Fig. 5, the error between the evaluation values and the actual result of these 5 groups sample data was low, and it proved the evaluation model could be used to study the relations between the electric parameters and dynamic property of a tri-cyclic servo system.
Fig. 5Comparison of evaluation values and actual result
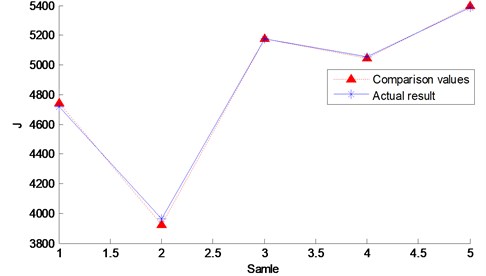
5. Conclusions
For evaluating the dynamic property of a typical tri-cyclic servo system with different technical parameters of electric machine, the evaluation object function was built based on ITSE. And by studying the construction of a tri-cyclic servo system, a simulation model of transfer function of tri-cyclic servo system was built. The control parameters of the simulation model had been optimal and fast-tuned on the basis of GA. Moreover, based on BP network, the evaluation model used to study the relations between the electric parameters and the dynamic property of tri-cyclic servo system was built and verified, which meant the evaluation model could be used to provide a reference for the chosen electric machine.
References
-
Yi Linzhi, Li Ming, Liu Xiang Research of three-loop control method of PV grid-connected inverter. Chinese Control and Design Conference, 2010, p. 4281-4285.
-
Bechouche Ali, Seddiki Hamid, Abdeslam Djaffar Ould Adaptive ac filter parameters identification for voltage-oriented control of three-phase voltage-source rectifiers. International Journal of Modeling, Identification and Control, Vol. 24, Issue 4, 2015, p. 319-331.
-
Czarskia Tomasz, Pozniaka Krysztof T., Romaniuk Ryszard S. Cavity parameters identification for TESLA control system development. Nuclear Instruments and Methods in Physics Research A, Vol. 548, 2005, p. 283-297.
-
Baek J. H., Kwak Y. K., Kim S. H. On the frequency bandwidth change of servo system with a gear reducer due to backlash and motor input voltage. Archive of Applied Mechanics, Vol. 73, Issue 5, 2003, p. 367-376.
-
Dorf Richard C., Bishop Robert M. Modern Control System. Seventh Edition. Addison-Wesley, Reading, Massachusetts, 1995.
-
Nise Norman S. Control System Engineering. Second Edition. Benjamin-Cummings, Redwood City, California, 1995.
-
Wang Enhua, Zhang Hongguang, Fan Boyuan Parametric robust stability analysis of a PID controller for variable nozzle turbocharger. 3rd International Conference on Computational Intelligence and Industrial Application, 2010, p. 183-186.
-
Liu Chao, Liu Jia, Wu Jian-hua A relay shaping method for servo mechanical system identification. International Conference on Intelligent Robotics and Applications, 2013, p. 353-364.
-
Zhang Jinhua, Zhuang Jian, Du Haifeng Self-organizing genetic algorithm based tuning of PID controllers. Information Sciences, Vol. 179, 2009, p. 1007-1018.
-
Liu Xiaolu, Chen Yingwu, Jing Xianrong Optimized Latin hypercube sampling method and its application. Journal of National University of Defense Technology, Vol. 33, Issue 5, 2011, p. 73-77.
-
Wang Hao-yu, Meng Xiang-de, Ji Xiao-juan Evolutionary learning algorithm and improvements for BP neural network. Energy Procedia, Vol. 13, 2011, p. 3594-3598.