Abstract
The paper discusses the issues related to facing stone production of hard-rock granite rocks. It describes the rational methods for producing dimension stones and designs of thermal tools to destruct rocks in processing and production of dimension stones. The designs of thermal tools characterized by increased output performance has been developed as a work tool for power-operated unit of stone-cutting machines.
1. Introduction
Let us consider the second technique in more detail. Thermal technique introduced into production on surface treatment and penetration of slotted workings in the granite massif has significantly increased the work efficiency [1]. There was a possible additional exposure of monolith prepared for breaking. With the application of thermal penetration of slotted workings in the massif, a monolith should be broken when it is exposed on the four planes [2, 3]. A monolith prepared for breaking should be connected with massif by one vertical and horizontal plane [4]. Moreover, the horizontal plane is selected in the place where there is a natural horizontal crack [5, 6]. Such a process layout for breaking has contributed to the stone integrity preservation. Yield of blocks has increased for up to 25-40 %. However, the technology basis is an availability of the natural horizontal cracks [7]. The main tools for penetration of slotted workings in the granite massifs are hand gasoline-air torches. Such torches enable penetration of slotted workings only in the vertical direction [8-10]. The depth of workings is generally 1.5-3 meters, although there are examples on penetration of workings to a depth of five meters and more. It is difficult to implement penetration by the hand torches, since they become hard to manage. In accordance with the terms of reference of the scientific project under the RoK MES grant, a laboratory model of the new machine design - thermal stone cutting unit was designed and manufactured in 2015. The technical requirements include the requirements of design simplicity, maintainability and operating safety, which will ensure a high operating performance of the new machine design. According to the terms of reference, the thermal stone cutting unit consists of thermal cutter, connection pipes, compressor, fuel and air supply system, as well as transport and supply system. Load bearing characteristics of the unit, including those providing the granite cutting speed of at least 50 mm/min have been justified. Transport and supply system includes the following requirements for workspace dimensions: horizontal traverse length of at least 4.000 mm and maximum 20.000 mm; vertical traverse length of at least 6.000 mm, cutter rotation in the vertical plane of at least 180°. Electromechanical drive that ensures the specific traverse speeds with step control is required for installation. Cutter weight should not exceed 20 kg. We have developed the improved and modernized designs of thermodynamic tools as an actuating device (TRV-60, TRV12М). They are equipped with thermodynamic nozzles, which enable increasing the energy parameters of torches. Industrial tests of these tools were conducted. The following specifications were obtained: air flow – 5 m3/min, fuel flow (gasoline / diesel oil) – 15 L/hour, nozzle diameter – 13 mm, nozzle head diameter – 20 (22) mm. The test results have determined the torch flame as equal to 25 cm and three-dimensional machining efficiency as equal to 4000 cm3/min. In addition, the alternative designs of BVR80 thermal cutters (see Figure 1) and its prototype TR60 have been developed.
2. Materials and methods
Development of facing stone deposits has a number of specific features that allow allocating such type of quarries to a special group of mining enterprises. As noted in [1, 2], these features are as follows:
requirement to preserve the key quality indicators of stone in the process of its quarrying (i.e. strength, block size and decorative properties);
application of special techniques to separate the stone blocks from the face, their loading, transportation and lifting from the quarry;
application of special development system options and deposit opening techniques.
The first feature determines the operating characteristics of dimensional stone quarries. It imposes conditions both on the tools and organization of quarrying operations. Everything is based on the stone integrity preservation. As the quarry operation practice indicates, even when the cracks and micro-orientation of minerals are correctly used, yield of large blocks from the rock mass rarely exceeds 25-30 % in principle, and the remaining rock mass is a common stone, small blocks, etc.
Knowledge of the massif structure anisotropicity, which should be considered when selecting the development techniques and directions, has a great importance in the process of work organization in the quarry. The massif structure anisotropicity is noted in granites [2], which simplifies the stone split in the certain directions. Facing stone is generally quarried by using two techniques:
1) Stone block spelling by using the wedges. Such technique consists in the fact that the holes are drilled along the spelling line, and then the steel wedges are driven into them. A strong mechanical shock is made on these wedges. Such technique is quite laborious and time consuming [3].
2) Thermal stone cutting with fiery jet. Such technique differs with high speed, relatively low cost and high work quality.
Fig. 1BVR80 thermal cutter: 1 – distribution head, 2 – combustion chamber, 3 – nozzle, 4 – gas-dynamic nozzle, 5 –lengthening pipe, 6 – combustion chamber back cover, 7 – air swirled, 8 – jet
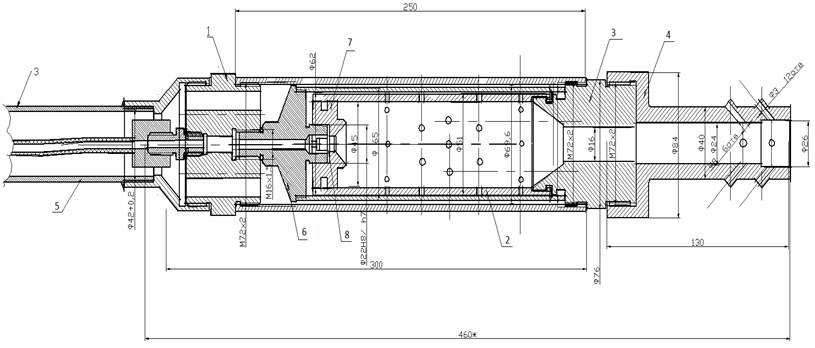
Shape and location of nozzles, combustion chamber length, value of slots for air movement in the process of cooling and others have been changed in the schemes proposed. The most difficult in solving the issue of a mechanized cutting is to obtain a stable working of slots in the areas of granite massif with the inclusion of mafic minerals and other surrounding rocks. Heterogeneity of composition along the cutting line leads to irregular speed of slot workings in depth. When cutting with hand thermal tools, the circumstance does not complicate slot penetration, as in this case, the irregular traverse speed of tool is easily set.
It is quite difficult to set the irregular traverse of actuating device for the stone-cutting machine and provide for an automatic speed control system depending on the thermal breaking of rocks on the face. Attempts of such solutions were taken in the process of development of the jet-drilling rigs, where the issue was decided regarding a thermo drill feed speed control depending on the rate of face advance, i.e. the issue of maintenance of an optimal distance from the torch nozzle exit to the face. Feed speed control systems that are reliable and easy to use have not been found.
When developing the stone-cutting machines, the feed speed of actuating device should be taken as regular. The value of actuating device traverse speed and gas jet attack angle should be selected so as to reduce the heterogeneity impact in composition of rocks along the cutting line to a depth of slot working, at the same time, by compromising on working efficiency. Such situation when it is necessary to select manual regulation of actuating device (torch) feed speed on more complicated areas should be provided for.
In addition to solution of the task on ensuring a stable working of slots, a number of process tasks should be solved when developing the stone-cutting machines. For the most part, such tasks are common when developing the machines of both vertical and horizontal penetration of slots. Task on a rectangular contour slot working at the gas jet attack angles of less than 90 degrees should be solved here. The Kharkov Aviation Institute has determined that cutting is the most effective at the gas jet attack angles of 30-60 degrees. They use idle stroke in the machine designs developed and perform cutting by traversing the torches only in one direction from the ledge to massif. Such circumstance leads to the fact that the slot working is made as raised. Blinding slot wall looks as inclined; inclination angle is a function of the gas jet attack angle. In such a case, the working stroke length of the torch changes in the process of cutting that makes it difficult to organize an automatic machine operation.
We have developed an experimental stone-cutting unit for penetration of the vertical slotted workings. It consists of a trolley where all the actuating device traverse drives of the machine are mounted. The trolley moves on the rail track along the cutting line. A bracket is mounted on the trolley with the carriage rack, where a rod with thermal cutter is fixed on the hinged bearings. Thermal cutter rotary drive is mounted on the same carriage, refer to Fig. 2. So, the thermal cutter may traverse jointly with trolley along the cutting line, by turning around.
The thermal cutter traverse speed along the cutting line is adjusted within 0.25-1.5 cm/sec. The reverse rotation speed is set as constant and equal to 20 rot/min. The rotation angle is adjustable within 90-150 degrees. Thermal cutter drops in depth after each stroke on the value of working. Driving motion is different in each direction. BVR-80 thermal cutter is installed as an actuating device of the stone-cutting machine (Table 1).
Table 1BVR-80 Thermal Cutter Specifications, fuel component flows
Air | m3/min | 18-20 |
Petrol | kg/h | 35-40 |
Torch Diameter | mm | 60 |
Torch Traverse Motion. Torch motion speed is regulated with variator, which changes the rotation speed of drive roller. Electrical circuit of control over the traverse motion of thermal tool provides for an automatic reverse and a timed shutdown after each stroke, which makes it possible to obtain a vertical wall at the end of slot. Reverse and shutdown at the end of stroke is performed by using the limit switches. Electrical circuit provides for shutdown and activation of the carriage feed with thermal tool by using a push-button control board.
The use of gasoline-air torches as actuating devices of the mechanized thermal equipment is restrained by a comparatively low power at the increase of which, their overall dimensions rapidly rises, as well as by the small dimensions of torch flame (0.1,..., 0.15 m) when using the scheme of processing with torch flame throughout its length – “band source”. According to this processing scheme, the gas torch jet is directed parallel to the work surface and embedded into the rock by 0.3,..., 0.5 torch nozzle diameter. Contact patch with the rock of such a jet, compared to the contact patch of kerosene-oxygen torches is less by 2 times and more; therefore, processing performance is significantly lower.
Fig. 2Structural machine layout with thermodynamic actuating device
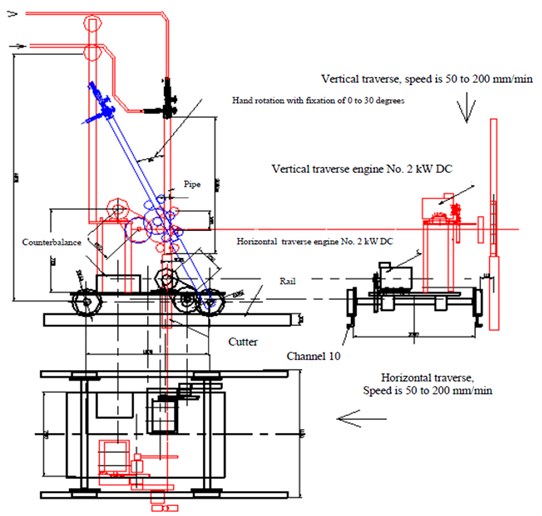
However, due to simplicity of gasoline-air torch operation and organization of their supply with fuel components, the use of gasoline-air torches as actuating devices of the mechanized units is relevant. Increase in the power of gasoline-air torches with no significant development of their overall dimensions and increase in the dimensions of torch flame, commensurable with the dimensions of the work surfaces of stone items (border stone, steps, etc.) is possible due to intensification of combustion processes.
One of the techniques for combustion intensification of available jets outside the nozzle exit is a post-combustion of incomplete-combustion products of fuel-rich mixture by atmospheric air ejection. When using heavy fuel mixtures in the torches, the torch ignition technique should be improved.
We have developed a new design of thermodynamic tool as the actuating device. The scheme of such thermodynamic tool is shown in Fig. 3. It is proposed to use two nozzle heads in this scheme that allows maintaining the nozzle temperature as not exceeding those permissible. It increases the useful life of the latter [11].
We have developed a design of device for vertical feed of thermal cutter, enabling to enhance the cut quality and efficiency of the stone cutting process, by increasing the rigidity of pipe with thermal cutter at a large cutting depth and reducing the weight load of pipe with thermal cutter on a roller feed [12].
Application of the device proposed will increase the rigidity of pipe with thermal cutter when performing a stone massif cutting, especially at a significant length of the pipe advance downwards. Currently, the pipe advance depth reaches 6 m or more. The high pipe rigidity prevents thermal cutter from oscillation due to the gas jet action that allows making smooth and homogeneous stone cutting profile. It improves the quality of a stone massif cutting process.
In addition, the cable tension force reduces the impact of pipe/cutter weight force on the feed rolls that allows significantly reducing the pipe slippage in the rolls when lifting the pipe and cutter upwards, especially in case of the rapid lifting. The specifications obtained are shown in Table 2.
Fig. 3Thermal cutter for stone cutting with two nozzles: 1 – thermal cutter, 2 – combustion chamber, 3 – distribution head, 4 – jet body, 5 – air swirled, 6 – fuel nozzle, 7 – nozzle body, 8 – changeable nozzle, 9, 10, 11, 12, 13, 14 – nozzle rotary and change mechanism
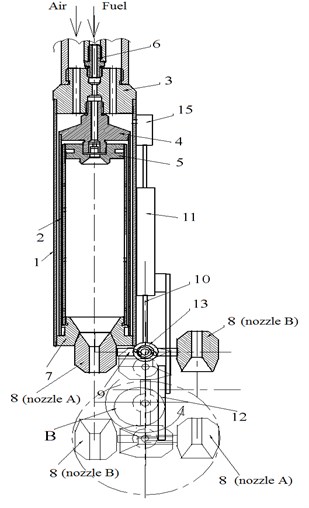
Table 2Basic specifications of the motorized machine for cutting slotted workings in the rock mass
Name | Value |
Cutting Width, at least, mm | 80 |
Cutting Length, at least, mm | 20.000 |
Cutting Depth, at least, mm | 6.000 |
Fuel Type | Diesel |
Flow, maximum, L/hour | 50 |
Oxidizer | Air |
Thermal Cutter, Length, mm | 4.000-7.000 |
Weight, maximum, kg | 25 |
Granite Cutting Speed, at least, mm/min | 50 |
The experiments have shown that the slot width is more than 7 cm that is larger than the outer size of thermal cutter.
Fig. 5Formation of slotted working by using BVR60 thermal cutter torch with gas-dynamic nozzle
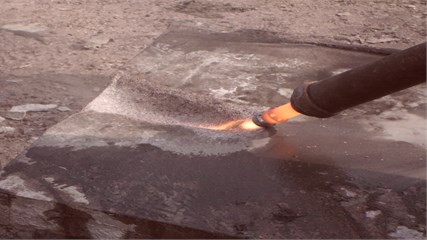
3. Conclusions
The machine developed and equipped with а powerful thermodynamic actuating device will allow making the slotted workings, if a uniform machine running is ensured in both horizontal and vertical directions.
References
-
Sinelnikov O. B. Natural Facing Stone Quarrying. RAAS Publisher, 2005, p. 244-249.
-
Bakka I. T., Ilchenko. I. V. Facing Stone. Geological, Industrial and Technological Assessment of Deposits. Depths, 1992, p. 290-302.
-
Levkovskiy G. L. А.S. USSR No. 1789687. Technique for Natural Stone Block Quarrying. Vol. 3, 1993.
-
Voluyev I. V., Sychev Yu. I., Tkach V. R. Waste-Free Technology for Natural Stone Quarrying and Dressing. Depths, 1994, p. 180-192.
-
Grigorovich M. B. Deposits of Minerals for Building Materials Industry. Depths, 1987, p. 144-149.
-
Orlov A. M. Natural Stone Quarrying and Dressing. Stroyizdat, 1977, p. 349-357.
-
Kosolapov A. I. Facing Stone Quarrying Technology. Krasnoyarsk KrSU Publisher, 1990, p. 192-210.
-
Dmitriyev A. P., Goncharov S. A. Thermal and Combined Destruction of Rocks. Depths, 1978, p. 304-311.
-
Sherstyuk B. F. Drillability of Rocks and Ores in Kazakhstan by Firing Technique. Extended Abstract of Cand. Sc. Dissertation, Novosibirsk, 1964, p. 18-27.
-
Goldayev I. P., Fursov A. P. Engineering evaluation technique for air-burning torches of thermal tools. News of Higher Educational Institutions. Mining Journal, Vol. 4, 1972, p. 76-81.
-
Povetkin V. V., Askarov Ye. S., Povetkin A. V., Shukhanova Zh. K. The RoK Innovation Patent No. 29758. Thermal Cutter for Stone Cutting with Two Nozzles, Vol. 4, 2015, p. 85-95.
-
Povetkin V. V., Askarov Ye. S., Povetkin A. V., Kerimzhanova M. F. The RoK Innovation Patent No. 30458. Device for Vertical Feed of Pipe with Thermal Cutter for Stone Cutting, Vol. 10, 2015, p. 35-46.
About this article
The authors declare that there is no conflict of interests regarding the publication of this paper.