Abstract
The present article shows the results of the theoretical and empirical research of the study of the impact made by acoustical oscillations on the working process of a gas-impulsive moulding device with the purpose of increasing the quality of the casting blocks’ seal and decreasing the roughness of the surface of a casting block. It has been shown that acoustical oscillations intensify the working process of the gas-impulsive moulding device. With the increase of frequency and power of oscillations the hardness of a casting block first sharply rises, but then gradually decreases. It has been found out that oscillations may help to adjust the precision of a casting block due to high sensitivity of a gas-impulsive process to the frequency of oscillations. The use of acoustical oscillations broadens technological opportunities of the moulding device.
1. Topicality of the research
Precision, i.e. the degree of conformity with the initially set sample, is the most significant indicator of the quality of machine engineering production, on which many field-performance data of a detail depend. Labour costs and self-cost of a ready product are determined by the precision of its details, which, in its turn depends on the precision of the block.
The main criterion in the selection of a casting block is the maximum approximation of configuration and dimensions of a block to the dimensions of a ready detail.
In casting blocks it is necessary to remove gate runners to ensure geometrical precision. The greatest problems are experienced by castings from intractable materials. The process of sawing off gate runners leads to very high wear of the cutting instrument. All methods of mechanical removal of gating systems are based on two principles:
- purely mechanical separation of metal: cutting off by hacksaw blades, cutting on bench-circular machine tools, cutting on band saw machine tools, cutting down on squeezers;
- melting the metal of a cut product in a place of the cut under the influence of friction along the fast-moving instrument.
The second principle is a perspective one at present. One of the solutions of this problem is application of new technology, in particular a technology of thermofrictional cutting with localisation of the thermal field at the expense of impulse refrigeration [1-4].
The main type of blocks in machine engineering is a casting block. It is overall accepted that high-precision casting blocks can be obtained only by means of precision casting. However, the majority of such means can be restricted in terms of dimensions, mass or casting composition, demands specialized equipment or application of specific materials. At the same time, casting into single sand mould remains significant. Application of high-strength mixes, enriched sands, specific additives and dynamic impacts on the compressed casted mould enabled significant improvement of the casting quality. For example, while traditional materials and technologies result in rough surface of the casting Rz 320…160 and higher, the application of new bonding materials provided the increase of this indicator up to Rz 80 [5].
One of the main factors contributing to the improvement of the quality of a casting block is the hardness of the working surface of a casted mould. Hardness of a mould is determined firstly by the degree of seal of sand mix, which depends on the type of casting. Machine casting, undoubtedly, is preferred to the manual one, but any casting device has limitations in terms of dimensions and mass of the produced mould. The more casting is, the bigger size of the mould is, the more complicated the mechanization and automation of its production is. Seal of big moulds faces big difficulty. So far, the combination of vibration and pressing has been one of the main types of their seal. There have been many constructions of casting machines made that offered various combinations of vibration and pressing. Each dimension-type is characterized by a definite set of parametres considering the seal of casting blocks of a certain size (in a more rare case – several sizes for casting, selected by the enterprise-customer as the typical ones).
Large-sized and massive casting blocks which can be received only by moulding in single sand moulds, are specific to small-batch and individual manufacture. The sizes of boxes and mass of shapes can differ essentially from each other. In addition, conditions of modern manufacture are such that the casting site (department) has no long-term program, and is forced to constantly pass over to new ways of casting depending on changing requirements of the market. All of it demands variation of working parametres of the forming device largely depending on certain conditions. But the given requirement is almost impracticable as it is possible to change a regime of vibration of the forming device only in the restricted breaking points, or it is not possible at all. Therefore, the scientific researches aimed at expanding working regimes of formation using the optimal modes of seal of the sand mix, thus raising quality of the received preform, are actual.
2. Statement of the research problem and physical essence of the process
As it is known, efficiency of vibration impact on the obturated environment depends on the intensity of oscillations which is proportional to magnitude of speedup of oscillations Af2 where A – amplitude, f – frequency.
Energy absorption of vibration oscillations by the sand mix can be calculated by the known equation [6]:
where α – a damping factor of oscillations in the mix, m-1; z1, z2 – distances from a source of oscillations, m, and z1<z2; A1, A2 – amplitude of oscillations on the distance from a source of oscillations z1, z2 accordingly, m.
From Eq. (1) it follows that the amplitude of oscillations is quickly diminished with the increase of distance from a source. Consequently, seal of casting moulds of various height at the same regime of vibrational impact is ineffective, which influences precision and roughness of a surface of received casting blocks. On the other hand, it is necessary to consider the fact of dependence of a damping factor α on viscosity of the environment. In more viscous damp sand mix (if compared to dry sand), vibration oscillations damp down more intensively. Thus, vibration with pressing can be recommended for seal of dry sand and plated sandy mixtures [7].
The damp sand mix is more expedient to be moulded by the impulsive impact of gas pressure [8-10]. The impulse of pressure is created at the expense of sharp expansion of the compressed air [11] (air-impulsive moulding) or explosion of an ignitable gas mixture [12, 13] (gas-impulsive, moulding). Thus the need for vibrators disappears, the construction of the forming device becomes simpler, manageability of the process increases.
Тhe essence of the pulse compression is as follows. In the working chamber of the mold with a mixture of hundredths of a second increase the pressure [14-17]. The mixture acquires a momentum of movement. Due to the kinetic energy of motion is sealed. In this gas-impulse impact more effectively than the air pulse. The peak value of the pressure in both cases approximately the same (about 0.4-0.5 MPa). The rise time of the combustion gas pressure is less. As result, the momentum turns more powerful.
Let us describe the mechanism of the gas-impulsive moulding. Its basis is the combustion of mixture of air with limiting hydrocarbon. Combustion is a difficult physicochemical process. It consists of series of infinitesimal chemical reaction of the oxidising-restoration accompanied by a complex of physical phenomena, such as mass carry and heat transmission. Combustion of gaseous limiting hydrocarbons occurs in two stages and is accompanied by the chain gear of self-acceleration leading to explosion.
At the first stage the gas is ignited – there is a break of interatomic links and the dissociation of molecules of gas from formation of free radicals, which are active particles. These particles react with other components of the mixture, a flame occurs. At the same time, not only oxidizing products, but also new active particles, appear. The flame front moves in the ignitable environment toward new portions of gas, and each of these particles enters the reaction again, the chain reaction occurs, the second stage of combustion is explicated, and a considerable quantity of heat is generated [18]. Heat generation in the confined space, e.g. the working chamber of the moulding machine, leads to the rise of temperature and pressure of gas.
Combustion can be laminar and turbulent. In the second case the process goes faster. Mean square velocity u of turbulent pulsations is proportional to the product of turbulence intensity ε and the velocity of a gas flow υ:
For one period of pulsations the flame front is on average deflected forward and back on magnitude √ˉZ2 [18]:
where t1 – a time interval for which the front of the flame moving along the air-gas mixture takes root into new masses of gas:
where l – turbulence scale, m; sH – normal velocity of spreading of the flame, m/s.
It is obvious that managing the working process of the gas-impulsive moulding device is possible by making the impact either on the initial stage – the more active particles initially emerge, the more intensive ignition is; or on the final one, i.e. on the development of a chain reaction and the degree of flame turbulization.
Proceeding from manufacture realities, it is advisable to have such a regulating factor that would not be rigidly connected with the construction of the forming device, would be entered in an existing technological schedule with the least expenditures and would have complex impact in the certain directions.
In all variety of physical phenomena only oscillations, acoustical and hypersonic, meet such a rigid set of requirements. It is known that oscillations of corresponding frequency and intensity loosen and even break off chemical bonds, activating atoms and molecules, and counteract recombinations of radicals. Acoustical oscillations of a gas log, interacting with the process of spreading of a flame front, force the front to fluctuate. In the big ports (the working chamber and the deflector of the gas-impulsive head) the initially uniform movement of the flame front starts to accelerate due to turbulence reinforcement. The flow of gas mass thus can reach the sound velocity and have the same effect, as a detonation wave [19].
Acoustical wave is a mechanical phenomenon. The energy, radiated by a source of sound, is transferred by acoustical waves, forming an acoustical field. It is characterized by [20]: 1) maximum υmax and effective υϵϕ oscillating velocity; 2) intensity, or sound intensity I; 3) tightness of energy E; 4) acoustical pressure.
Acoustical pressure is imposed on existing pressure of the gas environment, but as it makes only insignificant part of the atmospheric one, it cannot be used for sand mix seal. Thus, the acoustical field demands not powered but controlling impact on the combustion process.
At the stage of ignition acoustical oscillations should intensify the process of emergence of active particles. The minimum sound intensity, which is necessary for a break of interatomic link in the molecules of ignitable substance, is determined from the equation of energy of Eσ of a dissociation of molecules of acoustical energy Ea entered into the unit of volume of the working chamber:
Tightness of acoustical energy in a volume unit depends on the force of sound. And, as the acoustical wave runs on gas with the sound velocity, the energy entered into the environment during one period of oscillations, will be distributed on the length passed by the wave. Hence, the entered energy will be as follows:
where c – sound velocity in the environment where there is an acoustical wave, m/s; ρ – tightness of environment, kg/m3.
From here taking into account dependence Eq. (5) we receive a value of minimum-necessary sound intensity Imin:
Frequency f of acoustical oscillations is determined by a wavelength λ:
To make the impact more efficient, a resonance of frequencies is necessary: frequency of acoustical oscillations should coincide with frequency of turbulent pulsations. Taking this circumstance into consideration, we have:
whence necessary frequency of acoustical oscillations should be equal:
At an output Eqs. (10) ratio (2) and (4) were considered. Dependence (10) links together constructive-technological parametres of the machine (velocity of an air-gas flow υ depends on the number of ventilator revolutions [12], but turbulence intensity ε is determined by the construction and the sizes of the working chamber and the deflector of the air-gas flow), the type of the applied gas mixture (determining normal velocity of a flame sH) and the acoustical effect affixed from the outside. At its application determining the time t1 or, accordingly, turbulence scale l is the most problematic. At the given stage it can be made only empirically.
3. Experimental researches
The scheme of the experimental stand is given in Fig. 1. Its main body is the working chamber 1 in which a turbulizer of a gas flow is placed – a deflector 2 with a ventilator 3. The gas dispensing system 4 ensures stochiometric composition of a gas mixture in the working chamber. The device of ignition 6 initiates the combustion response. Generator 5 radiates acoustical oscillations of the set frequency.
Fig. 1The scheme of the experimental gas-impulsive stand: 1 – working chamber; 2 – deflector; 3 – ventilator; 4 – gas dispensing system; 5 – acoustical generator; 6 – ignition device, 7 – technological capacity; 8 – sample piece of the casting block
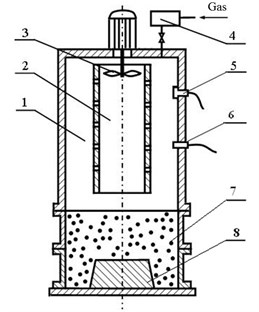
The tests were carried out in the conditions of the casting workshop of the joint-stock company “Teplopribor” (the city of Karaganda, Kazakhstan). The appearance of the experimental stand is presented in Fig. 2. The industrial equipment (casting-box 5, filling frame 4, sample pieces) completely corresponded to the one applied in operating manufacture. Sandy-argillaceous mixture was used as a moulding material, which with its composition and properties corresponds to the working conditions. The composition and properties of the moulding material and a combustible gas (blau gas) did not vary. That was only frequency of acoustical oscillations that varied. The acoustic transducer fed from 220 V, power consumption of 300 watts. The range of emitted frequencies – from 5 to 25 kHz.
On a receiving table of the stand the technological container was fixed; it was filled with moulding material and hermetically drawn in to the working chamber 2. A portion of gas from a dispensing system was sent to the working chamber A. The ventilator was powered up, and the mixture volume in the chamber was mixed up during 5-6 sec. Then the generator of oscillations 1 and the device of ignition 3 were turned on. Right after an impulsive impact on the moulding material the generator was disconnected, the technological container was detached from the chamber and removed from the machine table. By means of ball hardness gauge 071 UZLO hardness of a casting mould in a clearance between sample pieces and the centre of the mould was measured. Each experiment repeated 3 times. The results of measurings were statistically processed. The results of the carried out researches were reflected in the graphs of change of mould hardness (Fig. 3 and Fig. 4).
Fig. 3 presents the graph of influence of frequency and sound intensity on hardness in the centre of the casting mould. With increase in frequency of acoustical oscillations (f) hardness of the mould quickly grows in the beginning, and then is smoothly reduced, but it anyway exceeds a reference value. The hypothesis that acoustical oscillations intensify the process of gas-impulsive moulding proves to be true. Application of acoustical oscillations in gas-impulsive moulding contributes to the increase of precision of a casting block and reduction of roughness of its surface.
For big casting molds the maximum hardness of a form is observed around the frequencies corresponding 9±0.5 kHz. The essential growth of hardness – from 80±2 units to 88±2 units – in a relatively narrow frequency range (5,…, 10 kHz) testifies to high sensitivity of a working process of the gas-impulsive device as a whole and combustion process in particular to presence of acoustical oscillations. Hardness reduction at great values of frequencies testifies to undesirability of surplus energy in a closed-loop system of the working chamber. An explanation of the given paradoxical result, in our opinion, is the following. Considering that hardness of the mould is anyway above the initial, we believe that the first stage of combustion proceeds successfully. Consequently, not fully developed in the chain reaction of combustion, it interferes too large frequency oscillations.
Hence, combustion chain reaction is not explicated to the full, it is disturbed by too strong oscillations. Most probably, they promote deactivation of active particles. But this conclusion needs further consideration.
Fig. 2Appearance of the experimental stand: 1 – acoustical generator; 2 – working chamber; 3 – ignition device, 4 – filling framework; 5 – casting-box; 6 – measuring station
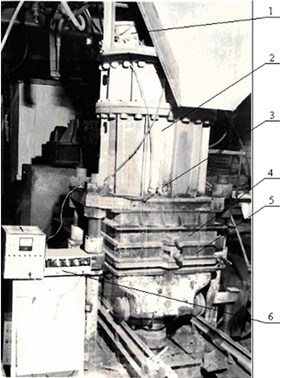
Fig. 3Effect of frequency and intensity of acoustic vibrations on the hardness of the center of the mold: 1 – a great form; 2 – smaller form
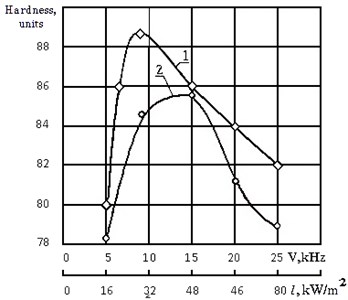
Fig. 4Influence of frequency and intensity of acoustic vibrations on the hardness of the gap between models: 1 – a great form; 2 – smaller form
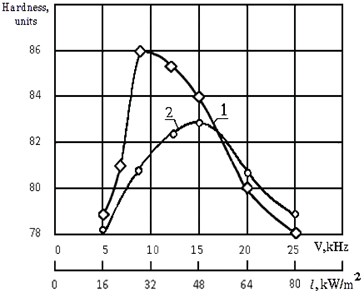
For forms, smaller by the size, the maximum of hardness is displaced towards big frequencies and more indistinct and numerical value of hardness is less. It is explained, in our opinion, by manifestation of a large-scale factor. First, giving to smaller volume of mix of necessary kinetic energy of consolidation (see below in the text) requires more powerful impulse. Secondly, the external friction of mix about walls of a molding and model in smaller volume is shown more strongly owing to the wedging action of grains of sand at their consolidation. For these reasons process is less sensitive to impact of fluctuations. Nevertheless, as appears from the schedule, process and in this case gives in to regulation.
Regulating the quality of seal by means of acoustical oscillations is possible both in a range of pre-maximum (to 9±0.5 kHz for great forms), and post-maximum frequencies. The first variant demands more precise adjustment and, accordingly, more qualified personnel, while in the second variant the requirement are less rigid. In our opinion, for real industrial conditions the second variant is more preferable.
Fig. 4 presents the graph of influence of acoustical oscillations on hardness in a clearance between sample pieces. Explanations to drawing 2 prove to be true in the large. Comparing drawings, we see uniformity of seal on the whole surface of the casting mould. The scatter of values in the centre of the mould and in a clearance between a wall of a casting-box and a sample piece is within 2,…, 4 units. It also contributes to the increase of dimensional precision of casting blocks.
Seal occurs owing to the interaction of infinitesimal strata of the moulding material. At the impact of an impulse the strata start to move, but the lowermost stratum lying on a sample piece, is fixed. It serves as an obstacle for a following stratum which moves and stops it. Accordingly, all overlying infinitesimal strata, still continuing the movement, start to be slowed down by the underlying ones and stop. The uppermost stratum is the first to begin movement and the last to finish it. At braking the sum of all overlying strata presses on the underlying ones, thereby – transmitting a part of the impulse to them and obturating them even more. Simultaneously cohesive links between particles are intensively recovered at the expense of tighter laying down of particles in the mould. The more the initial height and mass of a log of moulding material are, the higher the degree of seal at identical impact is.
In the tests a 120 mm high industrial casting-box was applied. The height of a filling frame equaled to the height of the casting-box (Fig. 4). Therefore the conditions for the gas-impulsive moulding were not favorable. Nevertheless, good results (see Figs. 2 and 3) have been obtained. It is obvious that higher casting-boxes will be obturated better. Regulating the combustion process by frequency of acoustical oscillations, it is possible to mould casting-boxes of different height and mass on the same moulding device without its essential readjustment – changing a stroke of a hold-down tool of a workmount to the gas-impulsive head is enough. Thus, application of oscillations broadens technological possibilities.
4. Conclusions
1. Acoustical oscillations intensify a working process of the gas-impulsive moulding device for manufacturing of casting blocks.
2. With the increase in frequency and force of acoustical oscillations hardness of a casting mould sharply rises in the beginning, then it smoothly falls, but anyway it exceeds a reference value. Thus, application of acoustical oscillations contributes to the increase of precision of a casting block. For experimental conditions the maximum value of hardness (88±2 units) ranged within frequencies of acoustical oscillations 9±0,5 kHz.
3. By means of acoustical oscillations it is possible to regulate precision of a casting block owing to high sensitivity of the gas-impulsive process to the frequency of oscillations. Process adjusting can be made in two frequency ranges: raising and lowering. In a raising frequency range the process is more sensitive to the effect of oscillations, than in the lowering one.
4. At using acoustical oscillations uniformity of seal of moulding material and precision of a received casting block rises.
5. Application of acoustical oscillations broadens technological possibilities of the moulding device, gives the chance to obturate casting moulds that are different in size and mass on the same device without its essential readjustment.
References
-
Innovative Patent No. 22998 RK on Invention 15.10.2010. Bulletin, Vol. 10, Patent No. 2738 UZ. Special Bulletin, Vol. 3, 1995, p. 33-34.
-
Patent No. 2738 UZ. Special Bulletin, Vol. 3, 1995, p. 33-34.
-
Patent No. 2957 UZ. Special Bulletin, Vol. 4, 1995, p. 39-40.
-
Report on the Issue of Innovative Patent for the Invention of the Republic of Kazakhstan. Decision Number 12-3/5594 from 09.12.2011.
-
Toropov Y. A. Allowances, Tolerances and Smooth Cylindrical Connections. Allowances and Tolerances of Castings and Forgings: Handbook. Profession, St. Petersburg, 2004. p. 598.
-
Aksenov P. N. Foundry Equipment. Mechanical Engineering, Moscow, 1977, p. 510.
-
Doroshenko V. S. Gas-dynamic sealing of dry molding compounds. Casting and Metallurgy, Vol. 2, Issue 70, 2013, p. 15-21.
-
Kuzembaev S. B. Working Processes for Molding Machines and Their Computer Simulations: Monograph. SANAT-Printing, Karaganda, 2004, p. 142.
-
Patent 640 437 Sw. Declared 14.11.79, No. 10150/79, Published 01/13/84.
-
Patent 648 498 Sw. Declared 6.11.80, No. 8235/80, Published 03/29/85.
-
Blankenhorn G. Аir impact molding machine. Men and foundry. 1983, p. 35-36, (in French).
-
Boenisch D. Investigation of casting mold by gas pressure. Part 1. Foundry, Vol. 69, Issue 21, 1982, p. 593-598, (in German).
-
Boenisch D. Investigation of casting mold by gas pressure. Part 1. Foundry, Vol. 69, Issue 23, 1982, p. 664-669, (in German).
-
Alfred J. Development of perspective lines forming gas pressure. Foundry, Vol. 67, Issue 20, 1980, p. 662-663, (in German).
-
Allewelt N. Using Jmpast Molding for short feries Production. Foundry Trade Journal, Issue 159, 1985, p. 409-416.
-
Boenisch D., Daume K. Testing of molding materials; molding machines, molding sand to optimize the air impact. Foundry, Issue 10, 1984, p. 381-393, (in German).
-
Jorn Alfred. News Gas pressing densification process associated with clay molding material. Foundry, Vol. 67, Issue 20, 1980, p. 603-610, (in German).
-
Lewis B., Pease R. N., TaylorH. S. Burning Processes. Physics-math. Literature red., Moscow, 1961, p. 542.
-
Novitsky B. G. The Use of Acoustic Oscillations in Chemical-Technological Processes. Chemistry, Moscow, 1983, p. 192.
-
Kuchling H. Handbook of basic physics course. Publishing House Leipzig, 1980, (in German).