Abstract
This paper describes the design process of a new asphalt slab track able to reduce vibrations induced by railway vehicles. In a first stage, the optimal dosage of the asphalt mixture including plastic waste is determined and the cross section designed. Then, a real stretch of asphalt slab track is built in an operating tram line in which real acceleration data sets are collected. These records will be used to calibrate and validate a 3D FEM model to assess the performance of the designed solution in different scenarios from the point of view of vibrations.
1. Introduction
In the last decades, the search of solutions that allow reducing the impact generated by the railway vibrations has increased in parallel to the development of new lines and the renewal of the existing ones. The incorporation of new materials to the traditional ballasted and concrete slab tracks has encouraged the reduction of the railway induced vibrations affection on people and buildings located in the track surroundings.
Asphalt mixtures highlight within the materials incorporated to the design of railway solutions due to their interesting structural properties and to their vibrations abatement capacity. In this context, the most extended use of asphalt mixtures is as subballast layer in the track infrastructure which has been already implemented with excellent results in high speed lines in Spain, Italy and Japan [1]. Moreover, Xei and Rose [2] performed a numerical experiment that revealed that, in poor terrains, an asphalt layer under the ballast minimizes the deflections, accelerations and stresses in the subgrade induced by the passing trains. Di Mino et al. [3] also considered asphalt layers in analytic models for the vibration prediction, demonstrating the good performance by comparing the results obtained with others from conventional ballasted tracks.
In order to prompt the vibration mitigation power provided by these bituminous layers, Zheng et al. [4] incorporated rubber dust to the mixture. The laboratory tests demonstrated that the rubber increases both the stiffness and the damping ratio of the mixture, improving simultaneously the structural and dynamic behavior of the infrastructure. This effect was evidenced in the high speed line Torino-Milan by D’Andrea et al. [5], where it was observed a vibration decrease in the range 50-100 Hz while for lower frequencies the attenuation power was not so pronounced. Moghaddam et al. [6] incorporated recycled plastomers to the asphalt mixture, demonstrating an improvement of the SMA mixture properties. Additionally, Hassani et al. [7] proved a reduction of the aggregates content in the mixture minimizing thus the environmental impact related to its massive use.
In this context, the development of a new slab track system addressed to the vibration reduction in tram networks environment was posed. This track is composed of a slab exclusively made of an asphalt mixture which includes recycled plastics in the formulation. This paper studies the design and the dynamic behavior of this new asphalt slab track. Firstly, the optimum dosage of the mixture is determined and the dimensions of the cross section are calculated. Secondly, the dynamic performance of the track against vibrations induced by a passing vehicle is assessed. To accomplish this second part, a three dimensional Finite Elements model is created and then calibrated and validated with acceleration records from a real track, which is constructed according to the requirements established in the previous stage. In order to confirm the versatility of this new solution, the track is tested in different scenarios in which the surface layer of the track is varied to assess the consequences of that on the dynamic behavior.
Since the last part analyzes the vibration response of the new asphalt slab track using a three dimensional finite elements model, it should be mentioned the previous work developed by Kourioussis et al. [8] in which the accelerations near the Brussels tram track were calculated using a integrated numerical model. In this case, the interaction vehicle-track was represented by a multi-body model; the track was modeled using the FEM and the soil as a combination of finite and infinite elements. Another interesting example of the FEM applied to acceleration prediction in concrete slab tracks can be found in Fang et al. [9], who compared the dynamic behavior of different slab tracks.
2. Determination of the optimal mixture
The election of the optimal dosage of the asphalt mixture that constitutes the new track must consider three fundamental aspects: it has to provide enough vibration mitigation capacity; satisfy the durability and strength requirements and be economically viable.
2.1. Vibration mitigation capacity
Considering a viscoelastic behavior, the complex stiffness modulus E* of the asphalt mixtures can be defined as the sum of the real modulus E' which has into account the elastic component and the imaginary modulus E'' representing the viscous part:
The quotient of the imaginary and the real component is known as the loss factor η and is equal to the tangent of the phase angle Φ:
The vibration attenuation capacity of a material is given by its damping ratio ξ, which is calculated as the loss factor divided by two:
The relation between the phase angle and the damping ratio was studied by Billigri et al. [10] in the abatement of the noise produced in the tire-pavement contact. Since the objective in this case is also to achieve an asphalt mixture with a high damping ratio, different dosages of the mixtures, in which the content and the properties of the aggregates, filler, binder and plastics are varied, are developed determining the phase angle in each case according to the standard UNE-EN 12697 [11] for the determination of the fatigue strength of hot mix asphalts. For this test, the temperature, the excitation frequency and the microdeformations of the specimens must be defined.
The temperature selected was 20°C according to the climate conditions in the experimental stretch location. The excitation frequency was 5 Hz, approximately equal to that of the bogie passage induced frequency of a tram vehicle at low speeds. Finally, five different microdeformation values selected on the basis of the expected values for the infrastructure layers of a tram tack were tested.
Results in Fig. 1 show that the higher values were obtained for the specimens containing a 0.5 % of plastic waste for both asphalt concrete (S20) and stone mastic asphalt (SMA16). Moreover, the phase angle obtained for SMA mixtures was globally higher than these obtained for the S20.
Fig. 1Phase angle values for the different mixtures tested
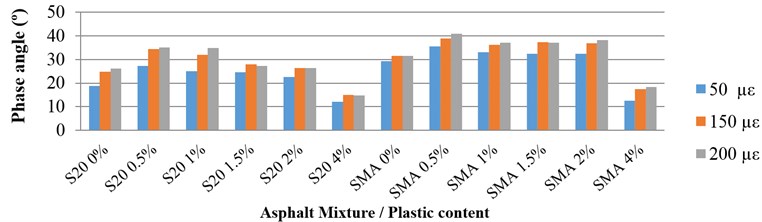
2.2. Mechanical properties of the mixtures
Besides providing high damping ratio, the bituminous mixture of the new asphalt slab track must fulfill several requirements to ensure the structural stability and durability. These requirements are specified in the PG-3 document of the Spanish Ministry of Development [12] for road works and have been adequately adapted to the needs of the current project.
Within the tests performed to the asphalt mixtures, it should be cited the Marshall stability and flow, fatigue strength and density tests. All the test procedures have been developed in agreement to the standards UNE-EN 12697 [11] for hot mix asphalts.
In Fig. 2, the values obtained for the Young’s modulus are displayed. This parameter is crucial for the design since a high value may cause a reduction in the thickness of the layers, achieving in that manner material cost savings and obtaining the same strength against the loads produced by the vehicles.
Fig. 2Young’s modulus for the different mixtures tested
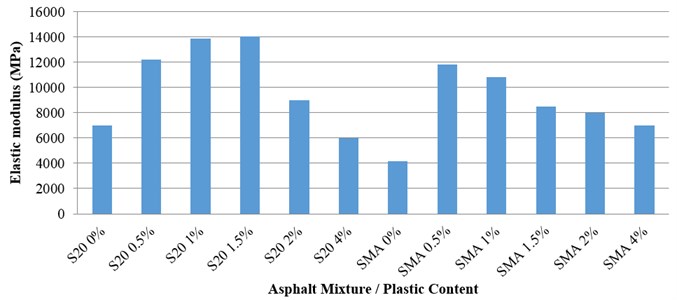
There does not exist a great difference between the mixtures that obtained the best damping results; the Young’s modulus of the mixture S20-0.5 % is 12200 MPa while this parameter in the case of the SMA16-0.5 % reaches 11800 MPa.
The results of the Marshall stability and flow test, average relative density and voids volume in the mixture are presented in Fig. 3. Although there are differences among the results for the different mixtures tested, in all the cases the minimum specifications of the standards are satisfied: the void volume in the mixture is over 4 % and the Marshall stability higher than 15 kN.
Fig. 3Results for the Marshall stability and flow, average relative density and voids volume test
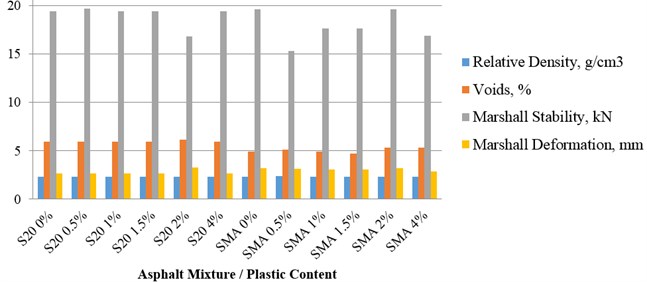
2.3. Economic appraisal
The economic criteria used for the appraisal of the different asphalt mixtures have only considered the fabrication costs. It is supposed that the rest of the costs (i.e. transportation, compaction, etc.) are similar in all the cases as any of the mixtures requires specific methods different from the conventional ones.
Fig. 4Fabrication cost of the different asphalt mixtures
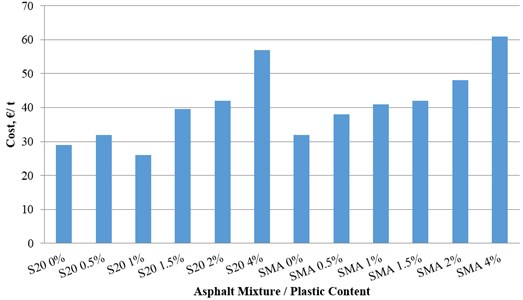
In Fig. 4, it can be seen how the cost per ton increases with the percentage of plastic in the mixture. In addition, for the same plastic content, the SMA16 mixtures are slightly more expensive than the S20 as a consequence of the higher binder content of the first ones.
In order to ensure that the asphalt mixture chosen is the optimal solution, apart from the logical assessment that has been done in this section the PRESS multicriteria decision making method was performed [13]. Up to six variables were considered in the process with the relative weights shown in Table 1.
Table 1Variables and weights considered in the PRESS method
Variable | Weight |
Viscous behavior | 0.3 |
Structural behavior | 0.2 |
Marshall stability | 0.1 |
Marshall deformation | 0.1 |
Void ratio | 0.05 |
Economic cost | 0.25 |
As deduced from Table 1, the higher weight has been assigned to the viscous behavior of the mixture. This property is represented by the phase angle and it has been considered of great importance since it determines the vibration mitigation power of the asphalt mixture. The next attribute in importance is the economic cost; the new track final solution will not be just an experimental result but it must be implemented in real tracks and therefore it must be economically viable. Finally, there are considered the structural behavior represented by the Young’s modulus and the stability, flow and voids results obtained from the Marshall tests.
The multicriteria decision making method revealed that the mixture SMA16-0.5 % is the optimal solution according to the vibration attenuation, structural strength and economic cost.
3. Design of the asphaltic slab track
Once the most suitable asphalt mixture has been determined, the next step is to design of the cross section of the track, calculating the optimal thicknesses of the different layers that guarantee the good performance of the infrastructure over its life span and minimize the construction costs.
3.1. Design criteria
The calculation of the thicknesses of the asphalt mixture layers in the track structure is performed according to fatigue requirements. In Fig. 5, a representative cross section of the track is presented. It can be seen two different layers of SMA16-0.5 % (surface and intermediate); the gradded aggregate that supports the intermediate layer and the sandy natural ground.
Fig. 5Cross section of the new asphalt slab track
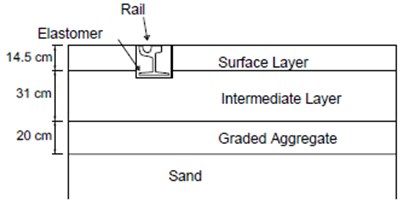
Table 2Mechanical properties of the track elements
E (MPa) | ν | ρ (kg/m3) | |
Rail | 210000 | 0.30 | 7830 |
Elastomer | 26.67 | 0.48 | 900 |
Asphalt mixture | 11500 | 0.33 | 2400 |
Graded aggregate | 170.92 | 0.30 | 1700 |
Sand | 50* | 0.30 | 2000 |
The mechanical properties of the different materials in the track are summarized in Table 2. The Young’s modulus of the sand is marked with an asterisk because it is a priori unknown. It has been assigned a low value in order to ensure that the calculated dimensions of the asphalt mixture are larger than the minimums required in reality. It is a secure method to guarantee the adequate structural behavior of the track against the stresses induced by the vehicles.
Constructing a finite elements model in which the thicknesses of the bituminous layers are variable, the strains produced in the different materials can be calculated. These strains are caused by the passage of the operating trains. The following strains must be checked in the studied track:
• Maximum horizontal tensile strain in the bottom fiber of the intermediate asphalt layer εhSMA.
• Maximum vertical compressive strain in the upper fiber of the graded aggregate layer εvGA.
• Maximum vertical compressive strain in the upper fiber of the natural ground εvSoil.
The fatigue equations for each of these materials have been calculated during the lab tests. These equations link the strain ε produced in each load cycle N with the number of cycles that can be produced without collapsing the material and are presented in the following equations for the mixture SMA16-0.5 % Eq. (4); the graded aggregate Eq. (5) and the sand Eq. (6):
From the information previously presented, the design process is as follows: given an asphalt mixture thickness, the different strains in the defined checkpoints are calculated using a finite elements model. These obtained strains are introduced into the fatigue equations, checking that the number of load cycles Ni is higher than the critic number of cycles Ncrit estimated for a life span of 50 years and a potential traffic level for each one of the materials. The minimum thickness of the SMA16-0.5 % mixture that satisfies this requirement is chosen as the optimal design. In this case, the optimal thickness resulted of 45.5 cm divided into the surface layer (14.5 cm) and the intermediate layer (31 cm) as depicted in Fig. 5. These results have been calculated considering that the vehicles operating in this case are Vossloh 4100 and Bombardier Flexity Outlook.
The design iterative process is outlined in Fig. 6.
Fig. 6Diagram of the asphalt layer thickness optimization process
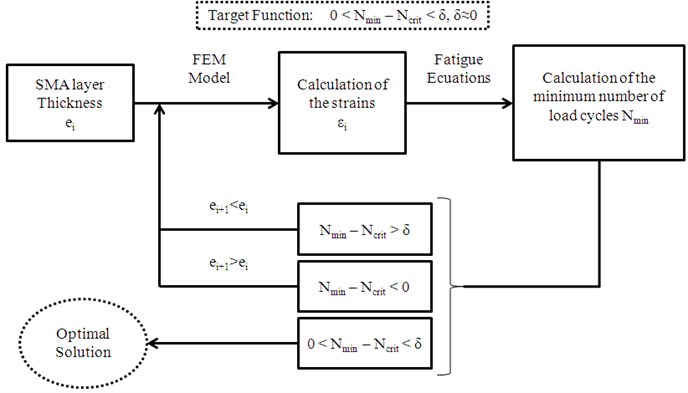
3.2. Construction of the stretch of track
After determining the dosage of the mixture and the optimal dimensions of the cross section, a stretch of the new asphalt slab track is constructed in a real operating line. The line chosen was finally in the Alicante (Spain) TRAM network, and the specific location is near the Poble Espanyol station.
Fig. 7a) Compaction of the graded aggregates and b) rail alignment previous to the elastomer pouring
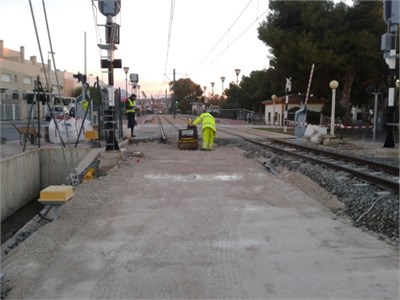
a)
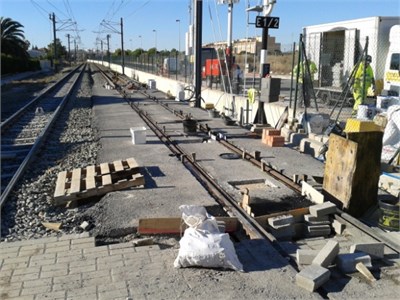
b)
It is a straight stretch at the end of the station, where a 20 m stretch of the former ballasted track was replaced by the new slab track. To do so, the rail, sleepers and ballast layer were completely removed, as well as the rest of granular layers until the distance from the rail head was –65.5 cm, matching the top of the sand stratum in Fig. 5. Then, the 20 cm layer of graded aggregate was placed and compacted, applying a tack coat on the surface to improve the adherence between the aggregates and the asphalt mixture.
The intermediate layer was compacted in two stages because of its high thickness while the surface layer was directly compacted after the placement. The channel that contains the rail was excavated using a trencher machine.
Once the rail channel was completed, the rail was placed using topographic equipments ensuring the longitudinal and transversal alignment and the tops were welded to the existing track. The elastomer used to fill the rail channel was the system Edilon Corkelast®, in which, the elastomeric material is poured in liquid state providing a total coating of the rail. The construction process of the new stretch of track is shown in Fig. 7.
4. Dynamic behavior of the stretch of track
The acceleration results that allow the assessment of the vibration mitigation power of the new asphalt slab track are presented in this section. For this purpose, real accelerations induced by a passing train are measured on the real stretch. These acceleration data sets allow creating a three dimensional finite elements model with the same dimensions that the model described in Section 3 for the design of the optimal cross section. A data acquisition campaign was done using the three axial accelerometers Sequoia Fast Tracer® shown in Fig. 8 and placed at a distance of 0.2 and 0.7 m measured from the outer side of the rail. After the dynamic model is calibrated and validated, the acceleration results can be calculated in any point of the domain.
Fig. 8Stretch of asphaltic track and accelerometers
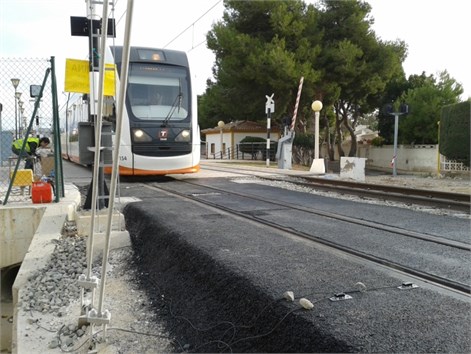
4.1. Finite elements model
Previous to the calculation of the dynamic response of the slab track, it is necessary to assemble the finite elements model. The cross section depicted in Fig. 5 has been schematically represented, assigning to the different materials in the track the mechanical properties in Table 2.
The dimensions of the model have been chosen so as to study accelerations in the range 2-50 Hz [14]. The symmetric half of the model is represented in Fig. 9 as appears in the software ANSYS Multiphysics/LS-DYNA V.14.
Since in any case it is considered a flawless track, the main mechanism of vibration generation is the 50 kN quasi-static load. This load is induced by the passage of a vehicle Vossloh 4100 which operated on the track stretch during the data acquisition campaign.
4.2. Calibration
As explained in Section 3, the Young’s modulus of the sand in Table 2 has been supposed to design safely the track but the real value of this parameter may differ from 50 MPa. Moreover, the global Rayleigh damping coefficient β which represents the contribution of the stiffness matrix to the vibration damping of the system is an unknown input.
Fig. 9Representation of the symmetric half of the stretch of track in the model
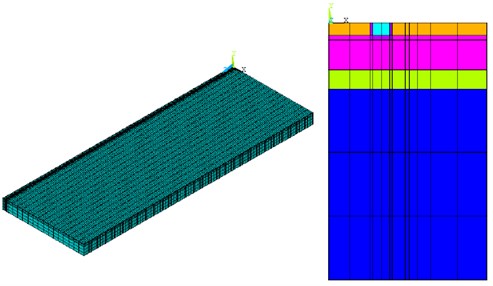
With the aim of determining the approximate value of these two inputs, a calibration process is performed. The calibration of a model can be done on the basis of results from experimental modal analyses as in the case of Ribeiro et al. [15] or from real acceleration registers as in this case.
The procedure followed is an iterative method in which pairs of values for the Young’s modulus of the sand and the global Rayleigh damping coefficient β are proposed. Then, the different vibration responses are obtained from the finite element model. These solutions are compared with the real acceleration data sets and the combination that yields the closer results to the real registers will be chosen as the correct. The overlapping of the real and the calculated accelerations is shown in Fig. 10, calculated with a combination of Esand=144 MPa and β= 0.001 in the point located at 0.2 m from the outer side of the rail.
Fig. 10Calibration. Real (black) and calculated (gray) accelerations
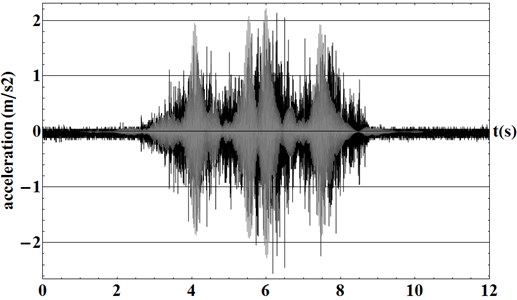
4.3. Validation
The real and the calculated responses must be compared in a different point from that used in the calibration in order to validate the model. This point is located at a distance of 0.7 m from the outer side of the rail since real acceleration data sets are available at this point.
The magnitude of the peaks calculated with the model and the time distribution match the records registered by the accelerometer. In addition, the tail times are mostly overlapped in both cases, giving an a idea about the time elapsed between the beginning of the excitation perception and the moment in which the wheel that produces it passes through the section in which the accelerometer is placed producing the peak. These validation criteria based on morphological aspects have been also employed by Costa et al. [16], comparing vibration velocities calculated and measured on a sleeper.
A numerical model able to reproduce accurately the dynamic behavior of the studied track is available. From this model, the dynamic response of the track in different scenarios can be calculated in the next subsection.
Fig. 11Validation. Real (black) and calculated (gray) accelerations
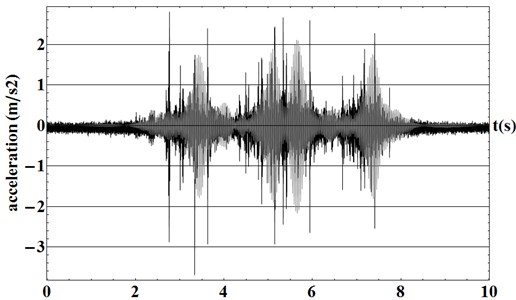
4.4. Dynamic behavior of the new asphalt slab track with different surface layers
One of the advantages of the new track is that the surface layer can be made of different materials without affecting the vibration attenuation power of the whole track. In this manner, a better environmental integration can be achieved in the different locations of the track. It is possible because the most part of the excitation induced by the train is in vertical direction and reaches the infrastructure through the rail foot that lies directly on the intermediate layer as depicted in Fig. 5. Consequently, the influence of the materials located over the rail foot plane is not significant on the overall mitigation power of the track.
To prove that, the SMA16-0.5 % surface layer will be replaced in the previously developed model by other materials which are often used in tram tracks: concrete, cobblestones and a conventional asphalt mixture. The mechanical properties of these materials are shown in Table 3.
Table 3Mechanical properties of the track elements
E (MPa) | ν | ρ (kg/m3) | |
Concrete | 22500 | 0.25 | 2400 |
Cobblestones | 3000 | 0.3 | 2300 |
Conventional asphalt mixture | 1500 | 0.3 | 2400 |
The surface layer is represented in the FEM model in Fig. 12 in orange color. The mechanical properties of the elements of this layer will be modified according to Table 3 to represent the different materials in the surface layer and subsequently analyze the dynamic behavior.
The graphs in Fig. 13 (Appendix 1) show how the absolute values of the acceleration decrease and the accelerogram shape blurs as the measuring point moves away from the excitation source. While at the points located at 0.7 m from the rail the effect of each train bogie is manifest, in the farther points the peaks become flat resulting in compact accelerograms with lower values as observed by Galvín and Domínguez [17] in high speed lines. In this manner, the damping capacity of the different materials that the waves traverse is evidenced.
On the other hand, responses slightly differ at 0.7 m from the outer side of the rail for the different materials but are almost identical in the point located at 5 m from the rail. It is because at the nearby points the accelerations have been obtained on the different materials of the surface layer. Their different mechanical properties produce such variations on the vibration responses obtained at these points. However, at a distance of 5 m from the rail the surface material is the same in the three cases and therefore, the results calculated at these points very similar.
Fig. 12Detail of the surface layer elements in orange
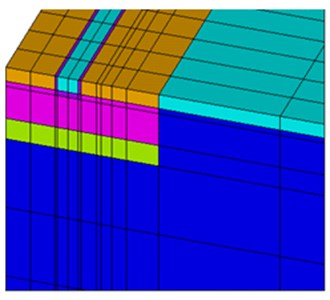
The similar responses obtained for different materials of the surface layer ensure the integration capacity of the new asphalt slab track in the different urban environments. Thus, it is an effective, environmental friendly and versatile solution as the new asphalt mixture with plastic waste presents an excellent behavior against vibrations induced by railway vehicles and can be also adapted to different scenarios varying the materials of the surface layer.
5. Conclusions
The aim of this research was obtaining a new solution able to attenuate the vibrations produced by a train in service in a tram track. Thus, the optimal dosage of an asphalt mixture containing plastic waste and providing high vibration attenuation power has been calculated. Moreover, the design process of the different layers of the track has been presented on the basis of the fatigue equations. In any case, the ground properties at the track location must be updated to achieve the optimal design.
After the design stage, an experimental stretch has been built within an operating line and real accelerations induced by a train passage have been recorded. Using these registers, a three dimensional finite elements model has been calibrated and validated to represent accurately the dynamic behavior of the asphalt slab track designed. Furthermore, these registers can be used to establish future comparisons between the performance of this track and other typologies (i.e. ballasted and concrete slab tracks).
With the 3D FEM model, calibrated and validated, the dynamic behavior of tracks with different surface layers has been simulated, finding that outside the track structure the vibration responses are identical. This result ensures the universality of the asphalt slab track since it can be adapted to the different urban environments merely modifying the surface layer.
References
-
Teixeira P., Ferreira P., López Pita A., Casas C., Bachiller A. The use of bituminous subballast on future high-speed lines in Spain: structural design and economical impact. International Journal of Railway, Vol. 2, Issue 1, 2009, p. 1-7.
-
Xei X., Rose J. Numerical investigation of vibration reduction of ballast track with asphalt trackbed over soft subgrade. Journal of Vibration and Control, Vol. 14, Issue 12, 2008, p. 1885-1902.
-
Di Mino G., Di Liberto M., Maggiore C., Notto S. A dynamic model of ballasted rail track with bituminous sub-ballast layer. Procedia – Social and Behavioral Sciences, Vol. 53, 2012, p. 366-378.
-
Zeng X., Rose J., Rice J. Stiffness and ratio of rubber-modified asphalt mixes: potential vibration attenuation for high-speed asphalt trackbeds. Journal of Vibration and Control, Vol. 7, 2001, p. 527-537.
-
D’Andrea A., Loprencipe G., Xhixha E. Vibration induced by rail traffic: evaluation of atenuation properties in a bituminous sub-ballast layer. 5th International Congress-Sustainability of Road Infrastructures, Rome, Elsevier, 2012, p. 245-255.
-
Moghadamm T. B., Karim M., Soltani M. Utilization of waste plastic bottles in asphalt mixture. Journal of Engineering Science and Technology, Vol. 8, Issue 3, 2013, p. 264-271.
-
Hassani A., Ganjidoust H., Maghanaki A. A. Use of plastic waste (poly-ethylene terephthalate) in asphalt concrete mixtures as aggregate replacement. Waste Management and Research, Vol. 23, 2005, p. 322-327.
-
Kouroussis G., Verlinden O., Conti C. On the interest of integrating vehicle dynamics for the ground propagation of vibrations: the case of urban railway traffic. International Journal of Vehicle Mechanics and Mobility, Vol. 48, Issue 12, 2010, p. 1553-1571.
-
Fang M., Qiu Y., Rose J. G., West R. C., Ai C. Comparative analysis on dynamic behavior of two HMA railway substructures. Journal of Modern Transportation, Vol. 19, Issue 1, 2011, p. 26-34.
-
Billigri K., Kaloush K., Uzan J. Evaluation of asphalt mixtures viscoelastic properties using phase angle relationships. International Journal of Pavement Engineering, Vol. 11, Issue 2, 2009, p. 143-152.
-
UNE-EN 12697 Standard. Test Methods for Hot Mix Asphalt. AENOR – Spanish Association for Standardization and Certification, 2008.
-
PG-3. Technical Specifications for Road and Bridge Works. Spanish Ministry of Development, 2008.
-
Aragonés P. Decision making methods in projects. Course notes. Polytechnic University of Valencia, Spain, 2010, (in Spanish).
-
Kourioussis G., Verlinden O., Conti C. A two-step time simulation of ground vibrations induced by the railway traffic. Journal of Mechanical Engineering Science, Vol. 226, Issue 2, 2012, p 454-472.
-
Riberio D., Calçada R., Delgado R., Brehm M., Zabel V. Finite-element model calibration of a railway vehicle based on experimental modal parameters. Vehicle System Dynamics, Vol. 51, Issue 6, 2013, p. 821-856.
-
Costa P. A., Calçada R., Cardoso A. Influence of train dynamic modelling strategy on the prediction of track-ground vibrations induced by railway traffic. Journal of Rail and Rapid Transit, Vol. 226, Issue 4, 2012, p. 434-450.
-
Galvín P., Domínguez J. Experimental and numerical analyses of vibrations induced by high-speed trins on the Córdoba-Málaga line. Soil Dynamics and Earthquake Engineering, Vol. 29, 2009, p. 641-657.
About this article
This project has been granted by the CDTI (Center for the Industrial Technological Development) of the Spanish Ministry of Economy and Competitiveness. The implication of EIGE (Infrastructure Authority of the Regional Government of Valencia) in the project and the constant support of FGV (Railways of the Valencia Region) in the real stretch implementation should be acknowledged.