Abstract
Timing gear systems of motorcycle engines are equipped with chain tensioners, which are subject to premature damage in certain engine models. Early detection of such damage is essential, as it may protect the user from unexpected engine failure while the motorcycle is running. This paper presents the results of research whose purpose was to use the measurements and analyses of vibration signals for the diagnosing of damage to the hydraulic tensioner in the timing gear system. Stand tests were conducted of the motorcycle engine in which new, used or damaged tensioners were installed. The research results allow to conclude that a change in the technical condition of the tensioner caused by wear contributes to an increased level of engine vibrations and that it is possible to detect damage to the timing gear system tensioner by means of measurement, processing and analysis of vibration signals.
1. Introduction
Newer and newer research methods using, among others, vibration signal measurement and analysis are being currently developed to diagnose the technical condition of different means of transport [1-9]. Using these methods allows for disassembly-free and often contactless determination of the technical condition. These methods enable performing the measurements during regular operation, as well as detecting damage at early stage of its development [3, 7]. Currently, a tendency may be observed for implementing vibroacoustic signals measurement and processing methods in the diagnostics of new objects [1, 10-16].
Motorcycle combustion engines are drive units that are expected to operate safely and without failure. Ensuring their operational reliability is also essential for the cyclist’s comfort and safety, as the driver is in the immediate vicinity of the drive unit during movement. The motorcycle user intensly feels any change in the technical condition of the engine, for the vibration generated by the engine are transmitted directly to the other elements of the motorcycle. Such a change also contributes to an increase of noisiness of the motorcycle.
The motorcycle engine elements which in certain models are subject to premature damage are tensioners in the timing gear system. Their damage is caused by the loss of tightness, which leads to a temporary drop of the required oil pressure in the tensioner. This causes a loss of smoothness of the timing chain operation leading, in consequence, to an increase of the motorcycle’s vibration and noisiness, as well as reduction of its power. In critical situations, such a damage may lead to breakage of the cam chain.
The development of methods of early and contactless detection of damage to the cam chain tensioner is also vital for another reason: it may protect the motorcycle user from unexpected blocking of the engine while the motorcycle is running.
This paper presents the initial results of research whose purpose was to assess the possibility of diagnosing the damage of hydraulic tensioner in the timing gear system of the motorcycle combustion engine.
2. Stand tests
The research object was a Honda CBR 600 F2 motorcycle in a good technical condition, equipped with a combustion engine marked as PC 25 (Fig. 1). With a cam chain driven engine, the motorcycle was also equipped with two camshafts in the head (Fig. 2). The element of the system that is exposed to damage is the hydraulic chain tensioner (Fig. 3), which shows a tendency for a momentary decrease of the required pressure. During the tests the engine was equipped with a new, used or damaged tensioner.
Fig. 1Location of the cam tensioner installation
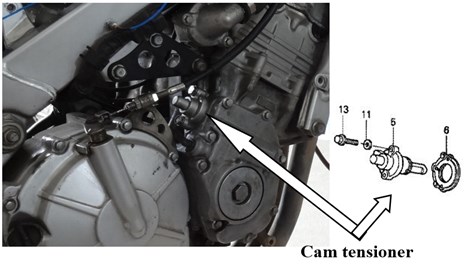
Fig. 2Simplified schematic diagram of the timing gear system
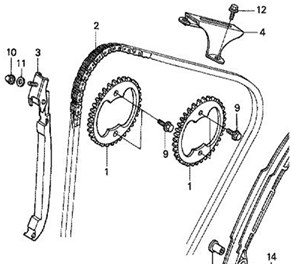
Fig. 3View of the tensioner with a washer
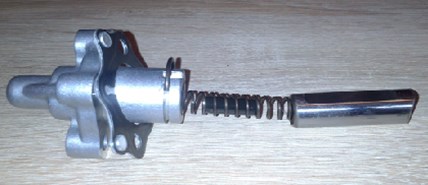
The measurement system used in the tests consisted of: an Ometron laser vibrometer, 3 accelerometers (Fig. 4), a National Instrument Data Acquisition Card NI 4472 and a computer with the LabView 8.6 software. Signals were recorded at a frequency of 20 kHz. Matlab-Simulink Signal Processing software was used for processing. The measurements were taken at an idle speed of ca. 1400 rpm and at a speed of ca. 2500 rpm.
Fig. 4Distribution of measurement points: 1 – accelerometer no. 1, 2 – accelerometer no. 2, 3 – accelerometer no. 3, 4 – point of contactless measurement with a laser vibrometer
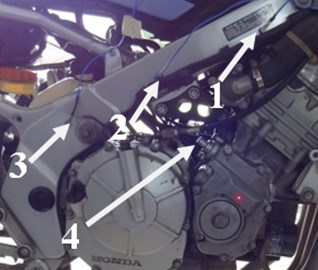
Examples of the research and analysis results are presented later in this paper.
3. Examples of research results and their analysis
Experimental results indicate that a change in technical condition of the tensioner contributes to a change in the vibration level, however, its dynamics depends on the rotational speed of the engine. The most significant change in the level of engine vibration caused by damage of the tensioner occurs at a rotational speed of ca. 2,500 rpm. Fig. 5 presents the calculated RMS values of the acceleration or velocity of the recorded vibration signals at the aforementioned rotational speed of the engine.
Fig. 5RMS changes of the recorded vibration acceleration and velocity signals at the engine’s rotational speed of 2,500 rpm
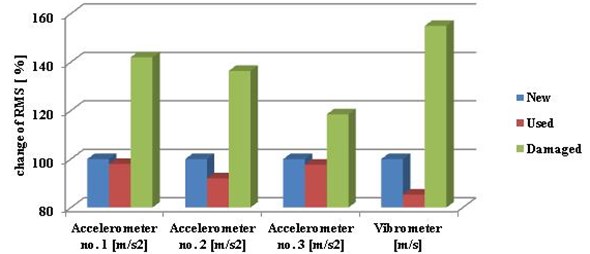
Analyses of the recorded vibration signals allowed for the observation of local maxima in time signals, in the frequency range if their resonance. A significant increase in the vibration amplitude occurs then.
In assessing the application of early damage detection for the tensioner in the timing gear system of the motorcycle engine, a local change of the vibration amplitude was determined in frequency bands by calculating the time-scale frequency distributions by means of a continuous wavelet transform. Fig. 6 presents sample calculation results for an engine equipped with a new or a damaged tensioner.
Fig. 6Time-scale frequency distribution of the vibration acceleration signal recorded with accelerometer no. 1 at a speed of 2,500 rpm: a) new tensioner, b) damaged tensioner
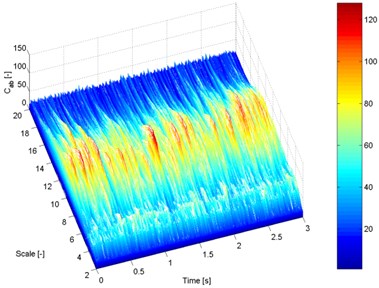
a)
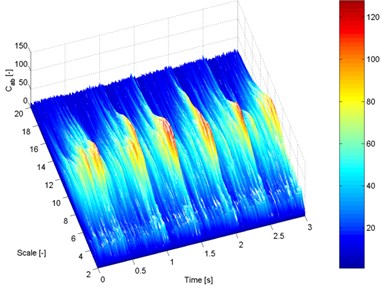
b)
4. Conclusions
The experimental research described in this paper makes it possible to conclude that application of vibration measurements and processing their results enable diagnosing damage to the hydraulic cam chain tensioner in the motorcycle engine. In this case, the use of systems having the capacity to measure and analyse vibration signals to monitor the motorcycle engine may enhance the operational reliability and safety of the motorcycle.
References
-
Haniszewski T., Gaska D. Overhead traveling crane vibration research using experimental wireless measuring system. Transport Problems, Vol. 8, Issue 1, 2013, p. 57-66.
-
Shatnawi Y., Al-Khassaweneh M. Fault diagnosis in internal combustion engines using extension neural network. IEEE Transactions on Industrial Electronics, Vol. 61, Issue 3, 2014, p. 1434-1443.
-
Urbanek J., Barszcz T., Zimroz R., Antoni J. Application of averaged instantaneous power spectrum for diagnostics of machinery operating under non-stationary operational conditions. Journal of the International Measurement Confederation, Vol. 45, Issue 7, 2012, p. 1782-1791.
-
Czech P., Wojnar G., Burdzik R., Konieczny Ł., Warczek J. Application of the discrete wavelet transform and probabilistic neural networks in IC engine fault diagnostics. Journal of Vibroengineering, Vol. 16, Issue 4, 2014, p. 1619-1639.
-
Barczewski R., Jakubek B. Problems of in-situ vibroacoustic testing of low-vibroactive devices. Vibrations in Physical Systems, Vol. 25, 2012, p. 59-64.
-
Figlus T., Liščák Š., Wilk A., Łazarz B. Condition monitoring of engine timing system by using wavelet packet decomposition of a acoustic signal. Journal of Mechanical Science and Technology, Vol. 28, Issue 5, 2014, p. 1663-1671.
-
Dabrowski Z., Zawisza M. Investigations of the vibroacoustic signals sensitivity to mechanical defects not recognised by the OBD system in diesel engines. Solid State Phenomena, 2011, p. 194-199.
-
Droździel P., Krzywonos L. The estimation of the reliability of the first daily diesel engine start-up during its operation in the vehicle. Maintenance and Reliability, Vol. 41, Issue 1, 2009, p. 4-10.
-
Dziurdź J. Application of correlation and coherence functions in diagnostic systems. Diffusion and Defect Data Pt.B: Solid State Phenomena, Vol. 96, 2013, p. 3-12.
-
Figlus T., Wilk A., Krajzel K. The influence of drive parameters and technical condition on the vibroactivity of devices with single-cylinder internal combustion engines. Transport Problems, Vol. 8, Issue 1, 2013, p. 79-85.
-
Albarbar A., Ball A., Starr A. On acoustic measurement based internal combustion engines condition monitoring. Insight: Non-Destructive Testing and Condition Monitoring, Vol. 50, Issue 1, 2008, p. 30-34.
-
Młyńczak J. Using databases in switch point mechanism diagnostics. Communications in Computer and Information Science, 2010, p. 152-159.
-
Hamacek Š., Bartłomiejczyk M., Hrbáč R., Mišák S., Stýskala V. Energy recovery effectiveness in trolleybus transport. Electric Power Systems Research, Vol. 112, 2014, p. 1-11.
-
Gajdzik B., Wieszała R. Measurements of the communication noise level on the internal roads of the manufacturing metallurgical enterprise. Metalurgija, Vol. 51, Issue 3, 2012, p. 369-372.
-
Ragulskis M., Maskeliunas R. Measurement of transverse vibrations of piezoelectric ceramics by atomic force microscopy. Experimental Techniques, Vol. 30, Issue 2, 2006, p. 37-41.
-
Figlus T., Wilk A. Comparison of the sound pressure measurement and the speed measurement of the gearbox vibrating surface. Transport Problems, Vol. 7, Issue 1, 2012, p. 37-42.