Abstract
This paper proposes a method for online structural health evaluation, and analyzes the correlation between online monitoring data and structural health status. On the basis of this analysis, the structural health can be evaluated by using the deviation of the current status from the initially designed status. The health degree index, representation and measurement models are also defined for structural health evaluation in this work. A numerical case study is conducted to validate the related concept and health evaluation model using a beam under pressure loads. The results indicate that the proposed method can effectively represent the structural health status.
1. Introduction
The lifetime of a mechanical product is defined as the total time span from the beginning of the usage to the final failure due to the function loss. The failure of a structure is mostly depended on the material properties, manufacture process and the working environments. Therefore, even for the products of exactly the same type, the lifetimes could be very different due to the discrepancies in the above-mentioned factors.
Currently, the strength design of structures is developing from the conventional determined method based on factor of safety to the probabilistic approach based on the reliability to extend the service time. The statistics indicates that about 95 % of the mechanical structure failures are caused by the fatigue cracks under alternating loads [1]. The fatigue failure is extremely dangerous because the whole structure could be break down without any symptom when the critical crack length is reached. Therefore, it is very important to determine the lifetime and the maintenance period to keep the safety of structures with the consideration of uncertain factors.
Most of the maintenance strategies of aircrafts are based on the U.S. Military Standard “Aircraft Structural Integrity Program (ASIP)” [2]. The Individual Aircraft Tracking (IAT) program is specifically defined for the life management of the aircrafts. In the IAT program, the residual lift is estimated using the concept of damage tolerance based on the monitoring of crack extension. The residual life is determined or evaluated using the equivalent flight hours (EFH) based on the given load spectrum.
However, the sequence of loads, the current status of the aircraft can significantly influence the residual life, and thus the EFH cannot accurately evaluate the residual life of the aircraft. Except for the external uncertainties of the loads and working environments, the internal status mostly determined by the material properties and manufacture process also plays a crucial role of the service time. The internal and external uncertainties lead to the different performance deteriorations of the structure, and thus very different life even for the same type designed for the same mission. Therefore, the conventional strategies for the usage and maintenance of aircrafts or the other structures based on the life determined by the standard and usage load spectrum can be inaccurate, and could cause huge economic loss by either overly using the damaged structures or early retiring the health ones [1].
Different from the currently developing condition-based maintenance, an online structure health management strategy is proposed in this paper. In this method, the life estimation and management is replaced by the evaluation of current status of the structure, which is determined by the deviation from initial healthy status. The service status of the structure is reflected or monitored by adding proper sensors providing online data which show the capability to adapt the working environment and to accomplish the mission. By the online status monitoring for individual structure, the structural failure could be predicted more accurately, and the service time could also be managed more properly.
Instead of focus on the failure mechanism, the proposed method directly builds up the relation between the monitoring data and structural health status, and can minimize the incorrect diagnosis and the decision-making display. This is inspired by the concept of “big data”, i.e., we focus on “what” instead of “why”.
There are four more sections in this paper. The definition of structural health based on status monitor is introduced in Section 2. The method for quantitative evaluation of the structural health degree is given in Section 3 using the one-dimensional evaluation model [3]. In Section 4, the performance deterioration of a simple beam example under static and dynamic loads is given as the numerical example to show the feasibility and effectiveness of the proposed method. Some conclusions are drawn in the last section.
2. Beam health
2.1. The concept and characteristics of product health
The concept of health came from the medical research, and the most straightforward expression should be “illness-free”. With the development of health management in medical fields, the concept of health has been extended to the other fields, and various methods and models are proposed to evaluate the health status of the engineering products [4-8]. Based on the previous research [9-11] and considering the features of modern products such as multi-function, applicability to changing environments, complex architecture, etc., the health of an engineering product should include the following aspects:
• The health of a product means it can work in a good condition without failure;
• The health of a product can be evaluated;
• Reliability, durability and self-healing ability are the basis of product health;
• The usage, maintenance and storage environments are the main effects to influence the product health;
• The proper usage and maintenance are important measures to keep and restore the product health;
• The ability to accomplish assigned mission is the criterion of product health.
According to the above comments, the product health is a status indicated by a set of monitoring parameters, and it can reflect the capability of the product to consistently accomplish the assigned mission under given working environments. A complete health-related parameter system shown as Eq. (1) needs to be constructed to manage the usage of product based on the health status:
where, denotes the multi-dimensional vector space of health, denotes the th factor of the characteristic parameter set for the product health, and is the whole multi-dimensional parameter space which indicates the product health.
2.2. Expression of beam health
Usually, there is a reasonable range for each design parameter of the beam. During the service period, the criterion for beam health would vary with the change of the task and working conditions. It is reasonable to assume that the health status deteriorate or degrade with the increase of service time if no intervention is applied to the beam. The deterioration can be represented by the decrease of ability to fulfill the task, the durability, and the adaptability to working environment. The performance deterioration does not mean failure, but indicates that the beam is easier to fail. When the monitored status parameters deviate from the designed ones and the beam cannot completely accomplish the defined tasks, it can be regarded that the performance deterioration occurs.
There are many running parameters during the service period of the beam, but some of them are either not closely related to health status, or not reachable for the measurement. Therefore, the characteristic monitoring parameters must be carefully chosen to improve the accuracy of health degree evaluation of the beam. For relatively simple beam, the strain/stress, deformation, and vibration/noise are usually used as the characteristic parameters. In this paper, the static and dynamic stresses are chosen as the characteristic parameters for the health status:
where denotes the multi-dimensional vector space of the health status, and and denote the dynamic and static stresses at time , respectively.
3. Evaluation of beam health
3.1. Definition of health degree
Mathematically, metric is defined as the distance between elements in a set. The multi-dimensional vector space is the set which defines the mathematical descriptions of parameter spaces for the structural health status. A specific health status is defined by the combinations of characteristic parameters, and can be regarded as a subset of . From the metric space aspect, the health status (or the standard status) is also a subset of , and the health degree can be defined by evaluating the distance between and . The health degree expresses the deviation of the current status from the initially designed or healthy status, and can serve as an index to reflect the ability to fulfill the designed tasks.
The health evaluation can be divided into element-level evaluation and system-level evaluation according to complexity of the structure architecture. The flowchart of health evaluation is shown in Fig. 1.
Fig. 1Flowchart of health evaluation
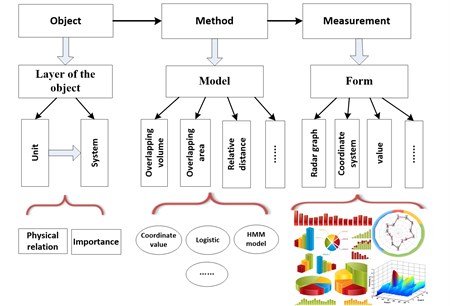
3.2. Evaluation of beam health degree
According to the definition of health degree, there are two types the structure health degree, namely the threshold value type and the probabilistic comparison type, depending on whether the parameter scatters are considered. In practice, the structure health degree is usually calculated using the relative distance, the overlap area or overlap volume in the metric space. Since the structure health is essentially a multi-layer, multi-element and multi-dimensional problem, the methods for health degree evaluation can also be divided into three groups: the one-dimensional methods, the three-dimensional methods [12], and the multi-layer methods [6, 13]. For the simple structures like beam, the one-dimensional evaluation method is enough.
In the one-dimensional method, all the monitored characteristic parameters are projected into the one-dimensional vector space using proper statistical methods or physical models, and construct the vector space of structure health status. The structure health degree of a beam can be evaluated via the distance between a given status and the standard or designed healthy status as:
where denotes the stress status of the healthy beam, and is the metric function.
According to Eq. (3), the evolution of structure health status can be described via the deviation value . However, as an absolute index, is only a real number which cannot provide the current health status of the structure when no reference value is provided. Therefore, we need to convert to a normalized value [0, 1] to explicitly evaluate the structure health status. Here we define as the health degree of the structure, and it can be calculated as:
where is a mapping function [0, 1].
As shown in Fig. 2, when the reference status is given, the smaller the deviation , the healthier the structure. The health degree approach to 0 with the increase of .
In this paper, the mapping function is defined as:
where and are the tunable scale parameters to obtain the actual health degree deterioration curve.
Fig. 2Health degradation based on known health reference
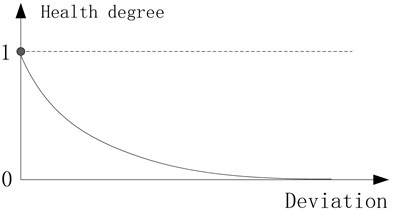
Fig. 3Finite element model of the example beam
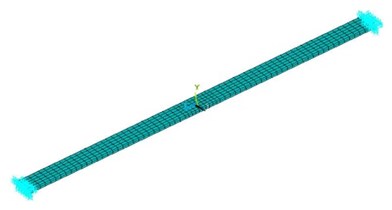
4. Numerical example
In this section, we use a simple beam example to show the concept of structure health. The beam is fixed at both ends as shown in Fig. 3, and the dimensions and material properties are listed in Table 1. The uniformly distributed pressure loads as shown in Eq. (5) are applied on the top surface of the beam:
where and denote the amplitudes of the static and dynamic loads, respectively. Here, we set the static pressure to 5.0E4 Pa, and the dynamic pressure to 5.0E3 Pa. In this example, the performance deterioration is simulated by adding cracks at the middle to reduce the effective area of the beam, as shown in Fig. 4. It should be noted that instead of using actual cracks, we use two slots on both sides to reduce the effective width of the beam.
Fig. 4Simulation of performance deterioration of the beam
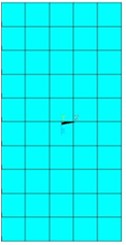
a) 0, 0
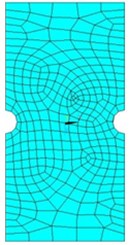
b) 0, 5 mm
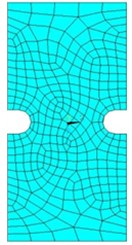
c) 5 mm, 5 mm
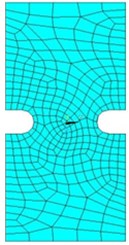
d) 7 mm, 5 mm
The first order frequency of the healthy beam is 69.8 Hz. In order to keep the structural safety, there must be certain difference between the excitation and the natural frequencies. Here, we use two excitation frequencies, 60 Hz and 65 Hz, to calculate the harmonic or dynamic responses of the beam. The vertical displacements and the maximum equivalent stresses at the middle of the beams with different health conditions are listed in Table 2.
Table 1Dimensions and material properties of the example beam
Elastic module | Poisson’s ratio | Length | Width | Height |
210 GPa | 0.3 | 1 m | 0.05 m | 0.01 m |
Table 2Displacement and stress results of beams with different health conditions.
Healthy | 0, 5 mm | 5 mm, 5 mm | 7 mm, 5 mm | |||||
stress | displacement | stress | displacement | stress | displacement | stress | displacement | |
Static | 82.6 | 4.4 | 219 | 4.75 | 290 | 4.84 | 330 | 4.90 |
60 Hz | 16.8 | 0.85 | 54.5 | 1.12 | 75.4 | 1.20 | 89.3 | 1.26 |
65 Hz | 50.4 | 2.54 | 229 | 4.68 | 354 | 5.58 | 466 | 6.52 |
Table 3Deviation and health degree of the beam.
Healthy | 0, 5 mm | 5 mm, 5 mm | 7 mm, 5 mm | |||||
Static | 0 | 1 | 136.4 | 0.81319 | 207.4 | 0.726653192 | 247.4 | 0.674002055 |
60 Hz | 0 | 1 | 174.1 | 0.737108 | 266 | 0.597899128 | 319.9 | 0.520943699 |
65 Hz | 0 | 1 | 315 | 0.527741 | 511 | 0.295709479 | 633 | 0.176332899 |
The existence of cracks reduces the stiffness of the beam, and thus the excitation frequencies get closer to the first order natural frequency. Therefore, the dynamic responses increase significantly. The deviation and health degree of the beam are listed in Table 3. Here we set the value of tunable scale parameters and to 150 and 250, respectively. We can observe that the deviation increased over time, and the health degree of beam decreased over it.
5. Conclusions and discussions
In this paper, we proposed a new kind of prognostic method about the decline of beam health in the context of monitoring data. This approach utilized the real time data collected by PHM system, to achieve the instantaneity of recognition. It improved the off-line and failure-based maintenance applied to the damaged beam, and made the evaluation result to the beam much more accurate. The stress increased with crack propagation in this example, and it indicated the deterioration of beam health. Meanwhile, the validity of the hypothesis that took dynamic/static stress as parameters of beam health has been proved.
It should be noted that the given loads spectrum and crack propagation are not consistent with the actual condition, and it is confined to only use stress to represent and calculate the health degree of the beam in this paper. In future work, we can use the actual loads spectrum and law of crack propagation to validate the theory, and select other parameters, to evaluate precisely.
References
-
Sun M. Fatigue life analysis and research for typical structure part. Journal Harbin University, Science and Technology, Vol. 12, Issue 1, 2007, p. 118-121.
-
Lu H., Guan Y. Adjustment of maintenance plan based on the individual aircraft life management. Journal of Shenyang Aerospace University, Vol. 30, Issue 3, 2013, p. 78-81.
-
Pires A., Chang N.-B., Martinho G. An AHP-based fuzzy interval TOPSIS assessment for sustainable expansion of the solid waste management system in Setúbal Peninsula, Portugal. Resources, Conservation and Recycling, Vol. 56, Issue 1, 2011, p. 7-21.
-
Smeulers J. P. M, Zeelen R. A generic PHM methodology applied to aircraft subsystems. Aerospace Conference Proceedings, 2002, p. 3153-3159.
-
Mishra S., Pecht M. Remaining life prediction of electronic products using life consumption monitoring approach. European Microelectronics Packaging and Interconnection Symposium, 2002, p. 136-142.
-
Li X. J., Bin G. F., Dhillon B. S. Model to evaluate the state of mechanical equipment based on health value. Mechanism and Machine Theory, Vol. 46, 2011, p. 305-311.
-
Liao L., Lee J. A novel method for machine performance degradation assessment based on fixed cycle features test. Journal of Sound and Vibration, Vol. 326, 2009, p. 894-908.
-
Sun Y., Liu Y. The completeness of the metric space and its special properties. Journal of Southwest University for Nationalities, Natural Science Edition, Vol. 38, Issue 2, 2012, p. 211-213.
-
Dai J., Zhang P., Li X., etc. Research on health assessment of integrated vehicle health management. Journal of Astronautics, Vol. 30, Issue 4, 2009, p. 1711-1721.
-
Wang Y., Liao M. Study on grading of health condition of aerospace propulsion system. Journal of Aerospace Power, Vol. 23, Issue 5, 2008, p. 939-945.
-
Liang B., Liu W., Yang X. Transformer condition assessment and residual life prediction. Advances of Power System and Hydroelectric Engineering, Vol. 11, 2010, p. 37-43.
-
Huo L. Research on representation and measurement method for product health. Beihang University, 2013.
-
Wang J., Fan K., Wang W. Integration of fuzzy AHP and FPP with TOPSIS methodology for aeroengine health assessment. Expert Systems with Applications, Vol. 37, 2010, p. 8516-8526.