Abstract
According to the factors that influence flexible material processing (FMP), the deformation compensation modeling method based on T-S fuzzy neural network is proposed. This method combines T-S fuzzy reasoning with a fuzzy neural network. Firstly, fuzzy clustering is introduced to extract fuzzy membership functions and the fitness of fuzzy rules of T-S fuzzy neural network antecedent from the past processing data. Secondly, with the steepest descent method, back-propagation iteration is used to calculate the connection weights of the network. The processing of experiments shows that T-S fuzzy neural network modeling is superior to typical T-S model. The angle error and the straightness error processed by NTS-FNN is 40.4 %, 28.8 % lower than those of STS-FNN. The minimum processing time processed by NTS-FNN is lower by 46.1 % than that of STS-FNN.
1. Introduction
The flexible material processing (FMP) refers to the process that takes various complex graphical processing on a flexible material (combined by multi-layer soft material), and an uneven three-dimensional pattern strayed on the surface of a flexible material [1, 2].
FMP deformation can be caused by multiple factors. Generally, several relevant variables will be regulated in order to reduce processing errors. Essentially, the compensation control of FMP deformation is a multi-input and a multi-output process. At present, the intelligent modeling of FMP is mainly based on the method of regression analysis, fuzzy reasoning and neural network [3, 4]. The method of Neural Network PLSR (NNPLSR) [5]; Kernel PLSR (KPLSR), which is suitable for real-time process modeling, is studied in [6-7]. Regarding the methods of modeling artificial intelligence, in 1993, a Japanese scholar Yasukawa proposed a simplified T-S fuzzy model. Its parameter of conclusion is expressed by a single value, which greatly simplifies the identification process [8]. In 1996, another Japanese scholar Sugeno proposed a T-S fuzzy model of a continuous recognition algorithm, the model parameter adjustment is achieved by the least squares method of weighted round robin [9]. In 2002, S. G. Cao from Australia proposed a fuzzy dynamic model, which consisted of multiple linear equations that smoothly connected global models through fuzzy membership functions. The accuracy of approximation can be arbitrary to any continuous nonlinear functions, which are defined on the compact set [10]. In 2011, Uros Zuperl from Slovenia studied the neural network model cutting force prediction of 3D spherical milling process [11].
Through the analysis of the literature above, it can be concluded that fuzzy, neural network modeling method has a strong non-linear expression. It is suitable for dynamic and complex uncertainty process modeling. A primitive angle, the interpolation rate, the processing direction angle and the flexible parts clamping way influence FMP deformation. Furthermore, some problems exist in the actual machining process, which requires deformation compensation prediction in real-time.
This paper proposes the FMP deformation compensation modeling, which effectively combines T-S fuzzy reasoning and a fuzzy neural network. It also introduces fuzzy clustering in order to achieve antecedent network model identification [12]. Based on fuzzy clustering, it adaptively adjusts the input space clustering center, the radius and the number of clusters, completes the input space fuzzy classification, determines the membership function and the rule fitness of data points, and improves the model training speed and approximation accuracy.
2. FMP deformation compensation modeling based on T-S fuzzy neural network
As the consequent network structure of a typical T-S model is relatively simple, if a new hidden layer is added to the consequent network, it will contribute to improve the universal approximation capacity of the model. Fig. 1 shows a new T-S fuzzy neural network extended model diagram of the standard T-S model. An antecedent network and a consequent network construct the new T-S fuzzy neural network model. The antecedent network is used to match the premise of T-S fuzzy rules. Meanwhile the consequent network generates the fuzzy rules. Then, the non-linear relationship modeling between the compensation output S={s1,s2,…,sr} and the deformation factors X={x1,x2,…,xn} is established through weighted calculations of antecedent and consequent networks.
Fig. 1Construction of T-S fuzzy neural network model after extension
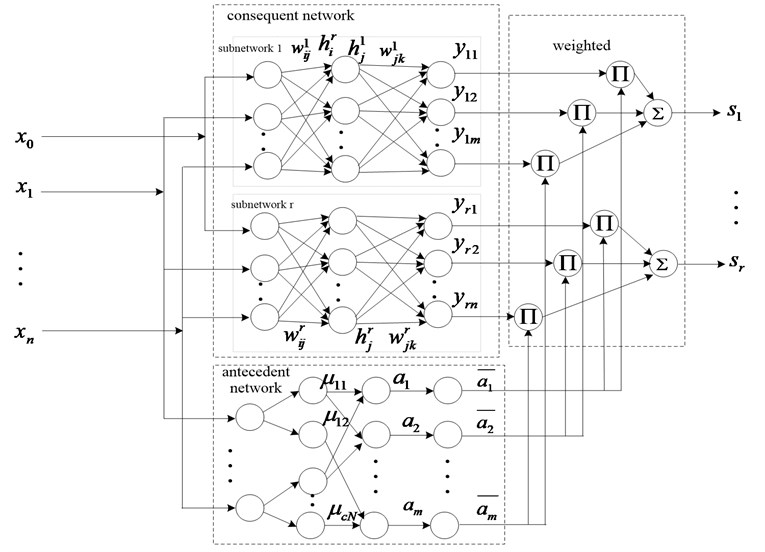
2.1. FMP deformation compensation model constructed by T-S fuzzy neural network
In Fig. 1, the T-S fuzzy neural network structure of FMP deformation compensation includes the function of a structuring membership, the rules of fitness of an antecedent network, and the calculations of the weight parameter of a consequent network [4].
2.1.1. Constructed antecedent network through clustering division of input data
The purpose of the division of FMP input data (FMP deformation influence factors) is to divide the input data fuzzy level, and to identify the coordinates of the center of each clustering and the width of each division district. Introducing the front part of the antecedent of T-S fuzzy neural network extracts input membership functions and the fitness of the fuzzy rules. Fuzzy clustering of the input data is mainly for working out the fuzzy partition matrix and clustering centers. Fuzzy clustering distance measurements are shown by Mahalanobis distance by calculating the minimum objective function (Eq. (1)) of c groups of fuzzy clustering division. This is done in order to obtain the data point xk’s clustering centers and the fuzzy partition matrix:
In Eq. (1): X={x1,x2,...,xn} is the n-dimensional input data set. U=[uik] is the fuzzy partition of X(uk) is a k-th sample that about i-th class membership degree), and ∑ci=1uik=1, k=1, 2,…, N. D2ikMi is the square inner product from the mid-point of n-dimensional data space xk to clustering center vi (Eq. (2)):
In Eq. (2), Mi=det(Fi)1nF-1i, where Fi is a positive definite symmetric matrix:
In Eq. (1), the minimum objective function is the basis for input data fuzzy clustering. Meanwhile, ∑ci=1uik=1, k=1, 2,…, N. Eq. (1) use Lagrange multiplier method to get the objective function and constrains. Then, introduced Lagrange multiplier λ:
The requirement for getting the extreme of ˉL(X;U,V,λ) is:
Therefore, if the values of data set X, the categories number of clustering c, and the fuzzy weighting exponent β are known, the data partitioning, the optimal fuzzy classification matrix and the cluster center all can be calculated by Eq. (5) [13].
Suppose the fuzzy partition matrix of input data is U=[uik] after the fuzzy clustering division, the fuzzy category of c set is Gi (1≤i≤c), then categories’ center of Gi,viq, and the corresponding variance σ2iq can be:
If the input data space division requires a high fuzzy clustering, in each Gi category data qk is very close to the category component of vi,n+1 (i=1,2,...,c) of the clustering center Vi=[vi,1,vi,2,...,vi,n+1]T (variance is σ2iq≈0), the clustering center corresponds to Gi, then the category value qk, which is the shortest distance from the categories’ center viq can be used as the decision function D(Gi):
Corresponding, relative to Gi membership function of xk is presented in Eq. (8), where i=1,2,...,c, j=1,2,...,n, |viq-v'iq| is the width of the corresponding input data division region. v'iq is the value of the cluster center, which is closest to the center of the i-th cluster. γ reflects the coefficient of the membership reduction speed when the input sample is away from the cluster center:
The physical meaning of the membership function Zji(xkj) can be described as a measuring of a similar relationship between the input sample xk and the fuzzy category Gi’s prototype. If xk is away from the prototype, Zji(xkj) is closer to 0. If xk is closer to prototype, Zji(xkj) moves near 1 [4].
For each fuzzy category Gi and its decision category, Ri reflects one of the decision rules (Ri: if xk∈Gi, then d(xk)=D(Gi), i=1,2,...,c). If the multidimensional fuzzy set Gi is projected to the whole input data space, then the decision rule R'i is as follows:
Respectively, the rule fitness of xk, relative to the rules of R'i, is expressed by Eq. (10):
Eqs. (8) and (10) are the calculation formula of the membership function and rule fitness when constructing the T-S fuzzy neural network model. Therefore the constructing of T-S fuzzy neural network model follows the below steps: 1) The execution of the fuzzy clustering algorithm in input data space to get category Gi (1≤i≤c); 2) The category center viq, corresponding to the variance σ2iq of all fuzzy categories is calculated (by using Eq. (6)); 3) By using the quality indicators parameter ξ, an excellent divided fuzzy category is selected; 4) The fuzzy category decision function D(Gi) after a filter is calculated (by using Eq. (7)); 5) The membership Zji(xkj) of sample data xk with respect to the fuzzy category Gi is calculated; 6) Fuzzy rule sets are generated according to Eq. (9); rule fitness υi are computed according to Eq. (10).
ξ is introduced as the parameter of the quality standard. Firstly, it assigns one small value to c, calculating all variance of fuzzy division categories. If σ2iq>ξ, c=c+1, then the fuzzy partition is redone and looped until the condition σ2iq≤ξ is met. Only then the corresponding fuzzy categories are accepted to construct a membership of a fuzzy neural network model.
2.1.2. Calculation of consequent network parameters wrij, wrjk
The value of the consequent network parameters wrij and wrjk are calculated based on the steepest descent learning algorithm. Supposed, Sr=[s1,s2,…,sr]T,S'r=[s'1,s'2,…,s'r]T represent the actual and the expected outputs of the consequent neural network. Then, the network output minimum variance of error cost function is Emse=12∑pr=1(s'r-sr)2.
Moreover, supposed ΔEmse=∂Emse∂w, W represents the connection weights between nodes, u∈(0,1) is learning rate, neurons coefficient iterative function each layer of consequent neural network is W(t+1)=W(t)-uΔEmse, and calculated by the error back-propagation algorithm, the calculation formulas of wrjk and wrij are:
3. Processing test experiments
Real measure data of FMP is taken to test the performance of the new deformation compensation model T-S fuzzy neural network (below called NTS-FNN), which was discussed above. The analysis and the calculation is carried out with Intel i5 processor, 2.4 GHz frequency, 2 GB RAM, Microsoft Windows 7 Professional operating system, and MATLAB R2008 software platform.
3.1. Modeling of FMP deformation compensation
The primitive angle x1 (°); the feed depth x2 (mm); primitive types (circle or line) x3 (circle: 1, line: 2); the processing step Lstep (mm) x4 as the deformation influence factors (which are the input parameters of NTS-FNN) are taken, and s1, s2 are taken ass the feed compensation parameters of the X, Y direction (which are the output of NTS-FNN) in order to construct NTS-FNN model. This mainly includes: 1) Construction of the antecedent network membership function Zji(xkj), the fuzzy rule fitness υi; 2) Calculation of w1jk,w1ij,w2jk, w2ij of consequent network parameter.
Fig. 2Experiment platform of quilting CNC
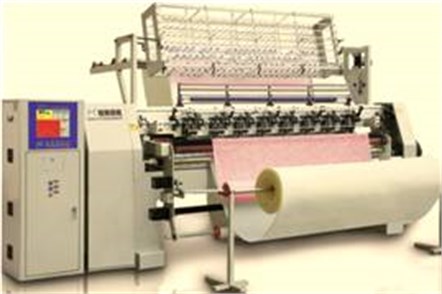
Choose five pieces of flexible parts, which length and width is 200 mm×120 mm and the material is polyurethane foam (the modulus of elasticity E=0.3652 MPa, Poisson’s ratio μ=0.25). Flexible parts have different thickness. The track machining experiment was conducted on the quilting CNC platform (Fig. 2), and the track angle machining error was controlled within ±2.0 %. 265 samples were gained (flexible parts’ thickness (mm) is 5, 15, 20, 25, 35, the machining track is parallelogram, cure angle is 15°, 30°, 45°, 60°) as test data of NST-FNN.
Assigned β=2, ε=0.00001, maximum iteration number tmax=400, c=2, ξ=1.3. According to Eq. (8), assigned γ=2, membership function Zji(xkj) and the fuzzy rule fitness υi of x1-x4 are gained. Furthermore, the number of nodes of each layer of the antecedent network is determined: from 1 to 4 is 4, 40, 10, 10. Finally, according to the Hecht-Nielsen method, it is confirmed that each layer neurons nodes of antecedent network is 4-40-10-10, consequent network is 5-11-10-2.
233 samples are chosen from the original 265 samples to train consequent network. 32 samples are left for the accuracy test, at the learning efficiency initial value u=0.4, the minimum expected error emin=0.001. The training step is 600, the gain consequent network parameter is w2ij:
Furthermore,w1ij, w1jk, w2jk is calculated.
3.2. Processing experiments
The processing track angle error fα, the straightness error fl, and the primitive minimum processing time tp are chosen as the machining performance test indicators. Moreover, performance indicators are compared to the standard-based fuzzy neural network prediction model STS-FNN [4].
Fig. 3Processing track geometry
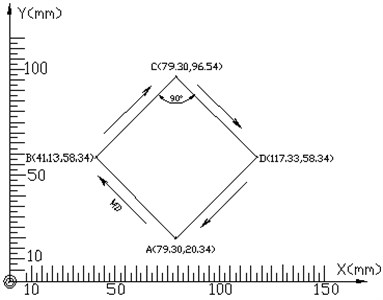
The pattern in Fig. 3 is used as the processing track, polyurethane sponge is used as a flexible material (the modulus of elasticity E=0.3652 MPa, Poisson’s ratio is 0.25), length, width and height of the flexible material is 150 mm×100 mm×15 mm. The processing experiment is without precompensation (NC), the feedback compensation control based on STS-FNN or NTS-FNN is conducted separately.
1) Process of errors fα, fl
Under the control of STS-FNN and NTS-FNN respectively, 14 groups processing samples are received. After data treatment, 3 groups of samples are removed (those with the starting points and end points not closed). Finally, 11 groups samples are selected to respectively measure the processing track angle errors and the straightness errors.
Fig. 4 shows a comparative graph of processing errors of the processing track angle error fα, the straightness error fl (that without precompensation (NC), and with compensation by STS-FNN, NTS-FNN). Processing track angle error: fa-NC, fa-STSFNN, fa-NTSFNN; straightness error: fl-NC, fl-STSFNN, fl-NTSFNN.
Fig. 4Comparative graph of processing errors
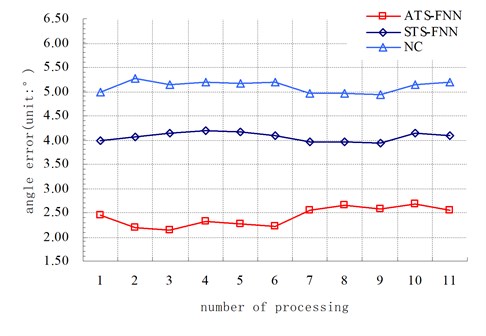
a)fa-NC, fa-STSFNN, fa-NTSFNN
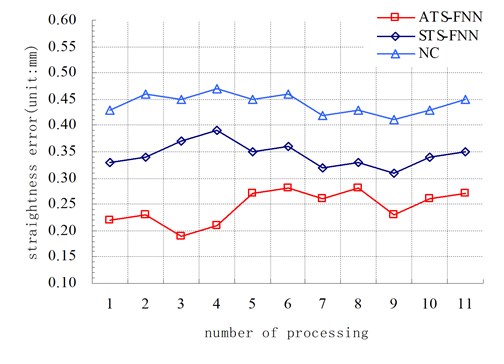
b)fl-NC, fl-STSFNN, fl-NTSFNN
Furthermore, more calculations are made: the processing track angle error of the average without precompensation (NC), compensation by STS-FNN, NTS-FNN are: f'a-NC=5.09°, f'a-STSFNN=4.06°,f'a-NTSFNN=2.42°; average straightness errors are: f'l-NC=0.44 mm, f'l-STSFNN=0.34 mm, f'l-ATSFNN=0.25 mm.
2) Primitive minimum processing time tp
From the testing results shown in Fig. 5, the time-consuming of completing track processing is as below.
The average primitive minimum processing time of process without pre-compensation (NC) tp-NC=2.86 s; with feedback compensation control based on STS-FNN tp-STSFNN=5.66 s; based on NTS-FNN tp-ATS-FNN=3.05 s.
From the processing experiment results, we can conclude that the processing track on the flexible material of thickness is 15 mm, f'a-NTSFNN is 40.4 %, 52.55 % smaller than f'a-STSFNN, f'a-NC; f'l-NTSFNN decreased 28.8 %, 44.45 % relative to f'l-STSFNN, f'l-NC; tp-NTSFNN decreased 46.1 % relative to tp-STSFNN, and increased by 6.65 % more than tp-NC.
Fig. 5Comparative graph of primitive minimum processing time
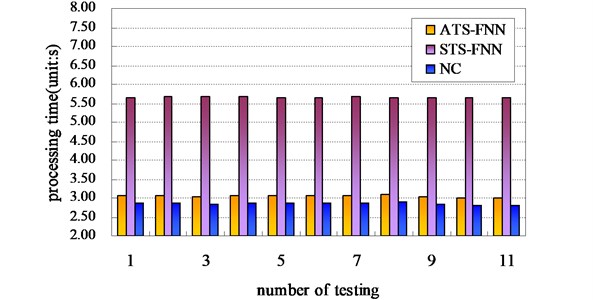
4. Conclusion
1) In the T-S fuzzy neural network modeling process, pre-optimized input spaces (by using the fuzzy clustering method) ensure an antecedent network membership function, simplify the fuzzy rule number, help save fuzzy reasoning time, and improve model training speed. The testing result shows that the primitive minimum processing time processed by NTS-FNN is lower by 46.1 % than that processed by STS-FNN.
2) FMP deformation compensation modeling method includes the advantage of fuzzy clustering and T-S fuzzy neural network method. Compensated by NTS-FNN, an angle error, the straightness error is 40.4 %, which is 28.8 % lower than these of STS-FNN.
3) The consequent network and the antecedent network are relatively independent. Therefore they can easily realize embedded parallel computing. This is conducive to the application of the model in the prediction of the actual FMP compensation.
References
-
Yaohua Deng, Sicheng Chen, Bingjing Li, Jiayuan Chen, Liming Wu Study and testing of processing trajectory measurement method of flexible workpiece. Mathematical Problems in Engineering, Vol. 2013, 2013.
-
Yaohua Deng, Bingjing Li, Sicheng Chen, Jiyuan Chen Deformation forecast of flexible material process by spline finite element method and application. International Journal on Smart Sensing and Intelligent Systems, Vol. 6, Issue 1, 2013, p. 333-351.
-
Sun Zengqi, Xu Hongbin Fuzzy-neural network based on T-S model. Journal of Tsinghua University, Vol. 37, Issue 3, 1997, p. 76-80.
-
Deng Yaohua Liu Guixiong ATS-FNN-based modeling and simulation for compensation prediction of fwp machining deformation. Journal of South China University of Technology, Natural Science Edition, Vol. 40, Issue 3, 2012, p. 146-151.
-
J. M. Karthikeya Udayagiri V. R.,Taleb Moazzeni, et al. Detection algorithms for the Nano Nose. 19th International Conference on Systems Engineering, 2008, p. 399-404.
-
Kyungpil Kim, Jong-Min Lee, In-Beum Lee A novel multivariate regression approach based on kernel partial least squares with orthogonal signal correction. Chemometrics and Intelligent Laboratory System, Vol. 79, 2005, p. 22-30.
-
Bai Yifeng, Xiao Jian, Yu Long Kernel partial least-squares regression. International Joint Conference on Neural Networks, 2006, p. 1231-1238.
-
Sugeno M., Yasukawa T. A fuzzy logic based approach to qualitative modeling. IEEE Trans on Fuzzy Systems, Vol. 1, Issue 1, 1993, p. 7-31.
-
Dan A. Ralescu, Michio Sugeno Fuzzy integral representation. Fuzzy Sets and Systems, Vol. 84, 1996, p. 127-133.
-
Feng G., Cao S. G., Rees N. W. Stable adaptive control of fuzzy dynamic systems. Fuzzy Sets and Systems, Vol. 131, 2002, p. 217-224.
-
Zuperl U. F. Cus neural control strategy of constant cutting force system in end milling. Robotics and Computer Integrated Manufacturing, Vol. 27, Issue 3, 2011, p. 485-493.
-
Francisco de A. T. de Carvalho, Camilo P. Tenório Fuzzy K-means clustering algorithms for inter valued data based on adaptive quadratic distances. Fuzzy Sets and Systems, Vol. 161, Issue 23, 2010, p. 2978-2999.
-
Zhang Dong-B., Wang Yao-Nan, Huang Hui-Xian Fuzzy rough model based rough neural network modeling. Acta Automatica Sinica, Vol. 34, Issue 8, 2008, p. 1016-1023.
About this article
This work is partially supported by National Natural Science Foundation of China (No. 51205069), Natural Science Foundation of Guangdong Province China (No. S2013010013288) and Combination project of Industry-university research of Foshan Shunde of Guangdong Province China (No. 2013CXY02). Thank you for all your help.