Abstract
Roller bearing is one of the widely used elements in a rotary machine. The vibration signal of roller bearing reveals the characteristics and feature of roller bearing faults. Extraction feature from vibration signal and discrimination fault condition are indirect means to ensure the safety operation of machine. This paper addresses a novel roller bearing faults discrimination method with harmonic wavelet package and OAO-RVM (One Against One-Relevance Vector Machine). First, decompose vibration signal with harmonic wavelet package and compute the vector energy from wavelet coefficients. The feature vector is prepared after the vector energy has been standardized. Second, the multi-classification model is established with the simplified OAO-RVM for the purpose of identifying good bearing, bearing with inner race fault, bearing with out race fault and bearing with roller fault. Finally, capture the vibration signal from the roller bearing stand of electric engineering lab to illustrate the proposed method. The feature extraction method with harmonic wavelet package is compared with conventional wavelet package. The accuracy and efficiency of three fault discrimination methods are compared. Experiment results show that the proposed feature extraction method is more effective than conventional method. Compared with ORA (One Against Rest)-RVM and DT (Decision Tree)-RVM, the simplified ORO (One Against One)-RVM model is the best fault discrimination method for its accuracy and efficiency.
1. Introduction
Vibration signals are widely used in condition monitoring of a rotating machine. Comparing the signals of a machine in normal and faulty conditions, discriminating faults is possible. Because of the non-stationary characteristics of roller vibration, many researchers study time-frequency technology in order to extract feature from vibration signals. For Hilbert-Huang transform possesses the performance of adaptive time-frequency domain analysis, Empirical Mode Decomposition (EMD) is used to process roller vibration signals to extract faulty feature [1]. Wavelet transform also possesses good performance for time-frequency domain analysis. Morphological wavelet is used to extract energy feature from roller vibration signals [4]. Compared with wavelet transform, harmonic wavelet transform possesses better filter performance when decompose signals into interested time-frequency domain. Meanwhile, the signals after transformation possesses the same resolution as the original signals, which overcome the limitation of Mallat algorithm in wavelet transform [2]. For harmonic wavelet analysis is effective to extract the singular components in the non-stationary signals, the time-frequency profile of harmonic wavelet is performed to analyze the signals of gear fault [3]. However, with the increase of harmonic wavelet decomposition level, analysis band will gradually tend to lower frequency or higher frequency without arbitrarily selected band. Harmonic wavelet package overcomes the preceding limitation for it adaptively subdivides the whole band of roller bearing vibration signals to extract interested frequency. Therefore, harmonic wavelet package is used to decompose roller bearing signals into different frequency domain and compute energy to form the feature vector [4, 5].
After the feature vector is available, a multiple classifier is necessary to discriminate the fault of roller bearing. When only a smaller number of samples are available, Support Vector Machine (SVM) possesses better nonlinear mapping performance. Based on decision tree architecture, a multiple SVMs classifier is proposed to diagnose roller bearing faults [5]. Relevance Vector Machine (RVM) converts nonlinear mapping in low-dimensional space into linear mapping in high-dimensional space just the same as SVM. Yet, its training process is within Bays architecture and it removes the irrelevant points with Automation Relevance Decision (ARD) principle premising a priori parameters to achieve sparse model [6, 7]. RVM overcomes such limitations of SVM as error parameters determination, model sparse and kernel function satisfying Mercer condition. It possesses similar or better accuracy for regression prediction, classification and identification compared with SVM.
This paper proposes a novel roller bearing faults discrimination method with harmonic wavelet package and OAO-RVM. After feature extraction with harmonic wavelet package, classification model with OAO-RVM architecture discriminates good bearing, bearing with inner race fault, bearing with outer race fault and bearing with roller fault.
2. Feature extraction with harmonic wavelet package
From the spectrum of wavelet package, Newland proposes harmonic wavelet that is a novel wavelet formation approach [8]. Harmonic wavelet is a kind of complex spectrum wavelet with box-shape. Its expression in frequency domain is:
where , determine the wavelet transform level just the same as from in the binary wavelet. Since harmonic wavelet is a complex wavelet with real part and imaginary part, it possesses good performances of locking phase and filter. The interested frequencies are reserved while other frequencies are shielded after transformation [9]. However, harmonic wavelet analysis can not choose interested frequency arbitrarily without infinite subdivision performance. Anyway, adaptive and infinite subdivision may be implemented based on the idea of binary wavelet package. Suppose interested frequency band is , in which is the high frequency and:
Conventional feature extraction method with harmonic wavelet package is to standardize the testing signal for the purpose of eliminating the effects from different variables as described in Eq. (2):
where the function computes the sum of and indicates the standard deviation of . However, conventional standardization method is not appropriate for vibration signal, whose sum may approach zero because of the contradiction between positive signal and negative signal. So, this paper first computes the sum of square of wavelet coefficients in each frequency domain. Then, compute the square root of the sum. After the square root has been standardized, the feature vector is prepared. The process of feature extraction method with harmonic wavelet package is described in detail as below.
1) Decompose vibration signals into multiple scales with harmonic wavelet package to achieve coefficients of each scale.
2) Compute the energy from wavelet coefficients in each scale with Eq. (4):
where indicates the number of frequency bands after harmonic wavelet decomposition and indicates the number of wavelet coefficients in each band.
3) Standardize the energy of wavelet coefficients with Eq. (5):
where function is to compute the average energy of each band and indicates the standard deviation of the energy of each band.
4) The standard fault feature is described as Eq. (6):
3. Faults discrimination method with OAO-RVM
Relevance Vector Machine (RVM) is proposed by Tipping M. E. based on Sparse Bayesian learning theory, which ensures sparse performance by assigning eigenvector with zero mean Gaussian prior distribution after introducing ultra-parameter [6, 7]. Meanwhile, estimate ultra-parameter with the maximizing edge likelihood function and automatically adjust rule coefficients in the process of ultra-parameter estimation [10]. Four bearing states are consider in this paper, including good bearing, bearing with inner race fault, bearing with roller fault and bearing with out race fault. Based on the idea of multi-classification SVM, this paper proposes a classification model with OAO-RVM to discriminate the roller bearing condition.
Just as the model with SVM in literature [12], this paper proposes One-Against-One model with RVM. Suppose the classification number is , the principle of One-Against-One (OAO) is to establish two-classifications to discriminate one sample and the other sample between two samples. Therefore, every two-classification is trained by the corresponding samples without repetition training compared with the Decision Tree model and One-Against-Rest (OAR) model. In the process of testing, each sample is discriminated by two-classifications. If it belongs to the th class, the voting number of the th class pluses 1. Until every two-classification finishes voting, the maximal voting number indicates the corresponding class. The OAO model is shown in Fig. 1.
Fig. 1Faults discrimination model with OAO-RVM
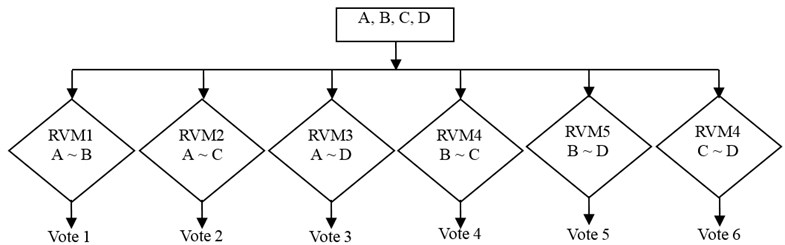
Based on the voting result, testing sample can be determined which class it belonging to. Yet, the RVM classification number will increase significantly when more classes considered. To simplify the architecture of OAO model, this paper incorporates OAO and OAR to propose an advanced OAO model which is shown in Fig. 2.
Where only four two-classifications left compared with the preceding OAO-RVM mode. With OAR-RVM mode, the first two-classification discriminates the good bearing. Then, three two-classifications vote to determine bearing state based on the OAO-RVM mode.
Fig. 2Faults discrimination model with simplified OAO-RVM
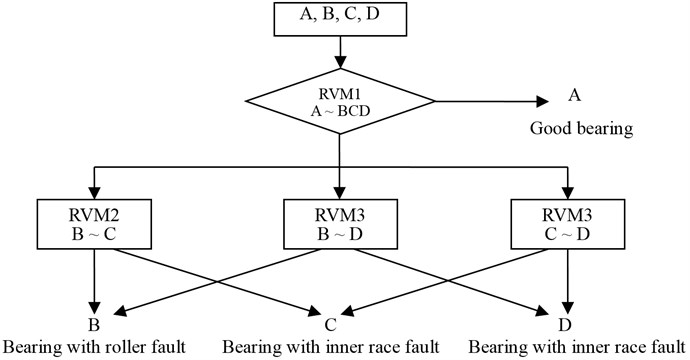
4. Experimental result
To verify the effectiveness of the roller bearing fault discrimination method proposed in this paper, the test data is acquired from electrical engineering lab of rolling bearing fault simulation in Case Western Reserve University [13]. The test stand is shown in Fig. 3.
Fig. 3Test stand of roller bearing
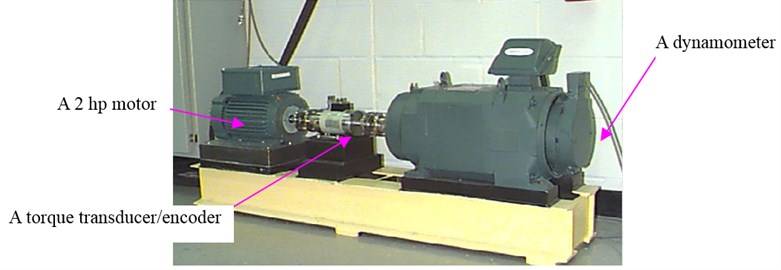
This paper considers the SKF bearings with fault diameters of 7 mils, 14 mils, 21 mils while sampling rate is 12,000 per second. For one bearing state, this paper collects 1024×100 groups. Then extract feature vector with three layer decomposition with harmonic wavelet package. So, 8×100 vectors are prepared. Together, 8×400 vectors are prepared after each bearing feature has been extracted. Among them, the former 8×50 vectors of each bearing state are used to train the proposed models and the latter 8×50 vectors of each bearing state are used to test the proposed models. Four vectors are shown in Fig. 4 corresponding four roller bearing sates.
This paper considers four working load including 0 hp, 1 hp, 2 hp and 3 hp. To compare the performance of feature extraction, the contrasts between harmonic wavelet package and wavelet package are shown in the following tables, in which wavelet package is used to achieve 8×100 vectors after three layer decomposition with the wavelet function db10. And the accuracy and time-consuming are compared among OAO-RVM model, DT-RVM model and OAR-RVM model. Comparison results are shown in Table 1 when fault diameters are 7 mils.
In the following table, WP indicates feature extraction with wavelet package and HP indicates feature extraction with harmonic wavelet package.
Fig. 4Energy distribution after feature extraction
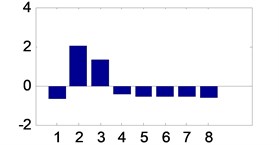
a) Vector from good bearing
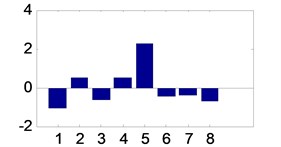
b) Vector from bearing with roller fault
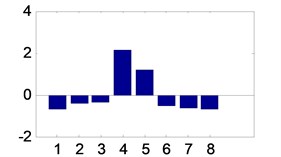
c) Vector from bearing with inner race fault
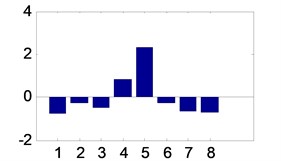
d) Vector from bearing with outer race fault
Table 1Comparison results when fault diameter is 7 mils
Work load (HP) | Rotation speed (RPM) | Signals | Sample rate (K) | OAO-RVM Accuracy Time-consuming (S) | DT-RVM Accuracy Time-consuming (S) | OAR-RVM Accuracy Time-consuming (S) |
0 | 1797 | X097_DE_time X105_DE_time X118_DE_time X130_DE_time | 12K | HP 100 % 0.26 WP 99 % 0.33 | HP 100 % 0.27 WP 100 % 0.32 | HP 99.5 % 0.32 WP 99.5 % 0.37 |
1 | 1772 | X098_DE_time X106_DE_time X119_DE_time X131_DE_time | 12K | HP 100 % 0.33 WP 99.5 % 0.37 | HP 100 % 0.32 WP 100 % 0.31 | HP 100 % 0.32 WP 98 % 0.37 |
2 | 1750 | X099_DE_time X107_DE_time X120_DE_time X132_DE_time | 12K | HP 100 % 0.27 WP 100 % 0.27 | HP 100 % 0.26 WP 99 % 0.29 | HP 100 % 0.33 WP 97 % 0.34 |
3 | 1730 | X100_DE_time X108_DE_time X121_DE_time X133_DE_time | 12K | HP 100 % 0.27 WP 100 % 0.26 | HP 100 % 0.27 WP 100 % 0.26 | HP 100 % 0.40 WP 100 % 0.26 |
5. Conclusions
This paper incorporates harmonic wavelet package and RVM to propose the novel roller bearing fault discrimination method. Harmonic wavelet package possesses better feature extraction performance due to its box-shape frequency analysis. By the contrasts of two feature extraction methods, the discrimination accuracy with Harmonic wavelet package is always larger than or equals conventional wavelet package. The novel discrimination method with simplified OAO-RVM is proposed in this paper. Compared with DT-RVM and OAR-RVM, it possesses good discrimination accuracy and computation efficiency. So, the proposed discrimination method is effective in the process of roller bearing fault identifying.
References
-
Dejie Yu, Junsheng Cheng, Yu Yang Application of EMD method and Hilbert spectrum to the fault diagnosis of roller bearings. Mechanical Systems and Signal Processing, Vol. 19, Issue 2, 2005, p. 259-270.
-
Xing Han, Jingqi Xiong, Rui Sun, et al. Research on the roller bearing fault diagnosis based on morphological wavelet and LSSVM Algorithm. Proceeding of International Conference on Quality, Reliability, Risk, Maintenance, and Safety Engineering, China, 2013, p. 1888-1892.
-
Wang Zhigang, Li Yourong, Li Fang Fault diagnosis method based on harmonic wavelet analysis. Journal of Vibration and Shock, Vol. 25, Issue 2, 2006, p. 125-128.
-
Zhao Yuan-Xi, Xu Yong-Gang, Gao Li-Xin, et al. Fault pattern recognition technique for roller bearing acoustic emission based on harmonic wavelet packet and BP neural network. Journal of Vibration and Shock, Vol. 29, Issue 10, 2010, p. 162-165.
-
Yu Jintao, Ding Mingli, Meng Fangang, et al. Acoustic emission source identification based on harmonic wavelet packet and support vector machine. Journal of Southeast University, Vol. 27, Issue 3, 2011, p. 300-304.
-
Tipping M. E. Sparse bayesian learning an the relevance vector machine. Journal of Machine Learning Research, Vol. 1, Issue 3, 2001, p. 211-244.
-
Tipping M. E., Faul A. C. Fast marginal likelihood maximi-sa-tion for sparse bayesian models. Proceedings of the 9th International Workshop on Artificial Intelligence and Statistics, 2003, p. 3-6.
-
Newland D. E. Harmonic wavelet analysis. Proceedings of the Royal Society A, Vol. 443, 1993, p. 203-225.
-
Newland D. E. Wavelet analysis of vibration, part 1: Theory. Journal of Vibration and Acoustics, Vol. 116, 1994, p. 409-416.
-
Li Shunming, Li Xianglian Modern Analysis Techniques and Application of Vibration Signals. National Defense Industry Press, Beijing, 2008.
-
Mackay J. C. The evidence framework applied to classification networks. Neural Computation, Vol. 4, Issue 5, 1992, p. 720-736.
-
Knerr S., Personnaz L., Dreyfus G. Single-layer learning revisited: A stepwise procedure for building and training a neural network. In Neurocomputing: Algorithms, Architectures and Applications. New York: Springer-Verlag, 1990.
-
The Case Western Reserve University Bearing Data Center Website. Bearing data center seeded fault test data, http://csegroups.cas e.edu/bearingdatacenter/pages/download-data-file.